Understanding PHE Gaskets: Composition and Benefits
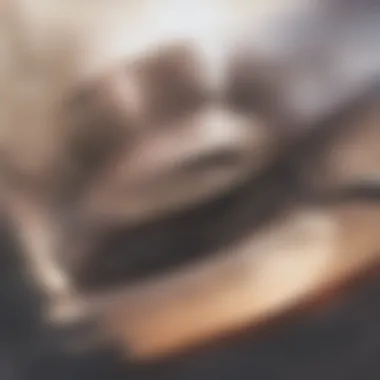
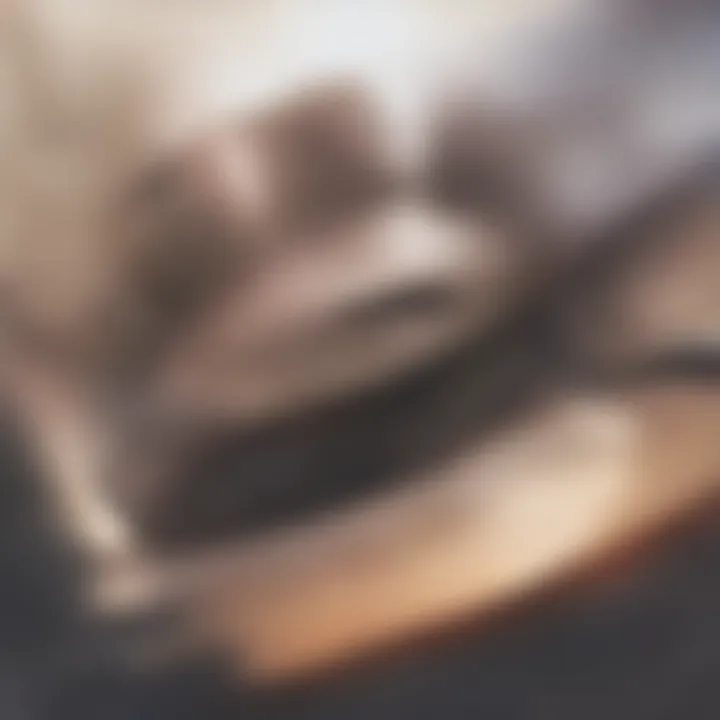
Intro
PHE gaskets are crucial components in various thermodynamic applications. Their role in heat exchangers is significant, impacting efficiency and reliability. This article will delve into the essentials of PHE gaskets, including their materials, types, and advantages in industrial uses. Understanding these gaskets can help professionals make informed decisions about selection, installation, and maintenance.
Research Context
Background Information
The study of PHE gaskets has evolved alongside advancements in thermal engineering. Plate heat exchangers, or PHEs, serve many purposes in industries like food processing, chemical manufacturing, and HVAC systems. These devices use gaskets to seal the gaps between the plates and facilitate heat transfer. The composition of gaskets greatly influences the performance of PHEs.
Importance of the Study
As industries push for increased efficiency and lowered energy consumption, the necessity of reliable PHE gaskets has grown. Both researchers and engineers must understand the materials, types, and innovations of gaskets to optimize their systems. This understanding can enhance heat exchanger performance and, subsequently, overall energy efficiency in complex systems.
Composition of PHE Gaskets
PHE gaskets can be composed of various materials, each with distinct properties. Common materials include:
- EPDM (Ethylene Propylene Diene Monomer)
- Nitrile rubber
- PTFE (Polytetrafluoroethylene)
- Silicone
- Viton
Each material has its advantages, such as chemical resistance, temperature stability, and durability, making it suitable for different applications. It is critical to select the right material based on the operational conditions of the heat exchanger.
Applications of PHE Gaskets
The flexibility of PHE gaskets means they are used in a variety of industries. For example, in the food industry, they must adhere to health standards while providing effective sealing capabilities. In chemical processes, they often resist harsh chemicals and high pressures. Other notable applications include:
- Power generation
- Pharmaceutical processes
- Marine applications
Understanding the specific applications for each gasket type can lead to improved performance and efficiency in systems.
Advantages of Using PHE Gaskets
The advantages of PHE gaskets are plentiful. Some key benefits include:
- Enhanced sealing
- Increased longevity
- Cost-effectiveness
- Energy savings
Using high-quality gaskets leads to lower maintenance costs and increased uptime. It can also contribute to better energy efficiency, which is a central focus in today's industries.
"A well-chosen gasket can significantly enhance system performance and lifecycle."
Selection Considerations
When choosing PHE gaskets, several factors should be evaluated:
- Material compatibility
- Temperature requirements
- Pressure conditions
- Installation and maintenance ease
Considering these aspects ensures the selected gaskets will perform optimally in their intended environments.
Ending
Prelude to PHE Gaskets
PHE gaskets are an integral component of plate heat exchangers, serving a vital role in their efficiency and efficacy. Understanding these gaskets is crucial for various industrial applications. This section will explore key aspects of their definition, function, and importance within heat exchangers. The insights gained here lay the foundation for a deeper comprehension of PHE gaskets' composition and applications.
Definition and Function
PHE gaskets are sealing elements used in plate heat exchangers, designed to prevent the mixing of different fluids. They fill the gaps between the plates, ensuring that the media flows in distinct channels. The correct functioning of these gaskets is paramount as they not only provide a seal but also help to manage the fluid flow within the heat exchanger. A well-designed gasket improves thermal transfer and reduces energy loss, impacting overall system performance positively.
Importance in Heat Exchangers
The significance of PHE gaskets in heat exchangers cannot be overstated. They contribute to the efficiency and reliability of these systems, making them essential in various industries, including chemical processing and HVAC. Factors such as temperature, pressure, and the nature of the fluids being processed affect the choice of gasket materials. Gaskets designed for a specific application minimize leakage and prevent environmental contamination. Furthermore, strong and durable gaskets extend the lifespan of heat exchangers, reducing maintenance costs.
Properly selected and maintained PHE gaskets enhance operational efficiency and safety, minimizing risks associated with leaks.
Composition of PHE Gaskets
The composition of PHE gaskets plays a critical role in their performance and suitability for various applications. Selecting the correct materials and understanding their properties is vital in achieving optimal sealing efficiency and durability. As heat exchangers operate under different conditions, the choice of gasket composition can significantly impact system reliability and operational efficiency.
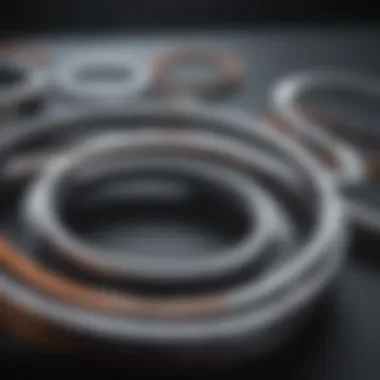
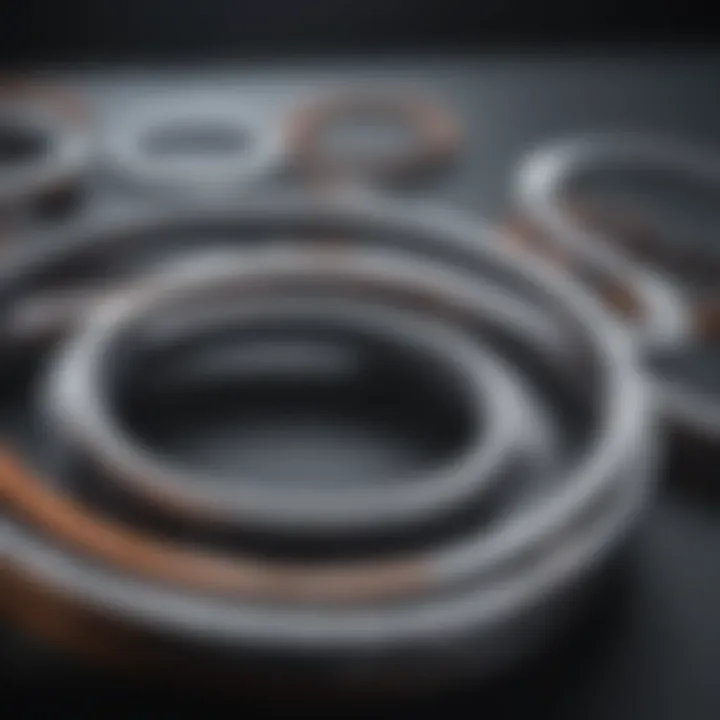
Materials Used
Elastomers
Elastomers are a key component in many PHE gaskets. They provide flexibility and resilience, making them effective at sealing under a wide range of conditions. One of the most notable characteristics of elastomers is their ability to return to their original shape after deforming. This feature is particularly valuable in heat exchanger applications where thermal expansion and contraction occur.
Elastomers, such as Nitrile and EPDM, offer excellent resistance to environmental factors. They are often chosen for their good temperature range and compression set resistance, which contributes to their durability. However, elastomers may have limitations regarding certain chemicals, which can reduce their effectiveness in harsh environments.
PTFE
PTFE, or polytetrafluoroethylene, is another significant material used in PHE gaskets. It is well-known for its exceptional chemical resistance, making it ideal for applications involving aggressive fluids. A key characteristic of PTFE is its non-stick surface, which helps prevent the accumulation of deposits.
This material is beneficial when maintaining purity in food and beverage applications. However, PTFE gaskets can have reduced mechanical strength compared to elastomers. This trade-off must be carefully considered when selecting materials for specific applications, particularly where pressure and stress are concerns.
Metallic Components
Metallic components in gaskets add structural integrity and strength. They are often used alongside elastomers or PTFE to enhance the overall performance of the gasket. These components can support higher pressures and temperatures compared to non-metallic options. The most common metals used include stainless steel and copper due to their strength and corrosion resistance.
One key characteristic of metallic components is their ability to maintain a robust seal during thermal cycling. However, they can be less forgiving than softer materials. Care must be taken during installation to avoid damage to softer gaskets in hybrid designs.
Physical Properties
Thermal Resistance
Thermal resistance is crucial in gasket applications, especially in heat exchangers. This property determines how well a gasket can withstand temperature fluctuations without degradation. Gaskets with high thermal resistance can maintain effective seals even under extreme conditions.
This unique feature helps in improving the reliability and safety of heat exchange systems, reducing the likelihood of leaks. However, itβs important to consider that while some materials excel at thermal resistance, they may not perform well under other stresses, such as chemical exposure.
Chemical Compatibility
Chemical compatibility dictates how well gasket materials stand up to various chemicals. Different industries, such as chemical processing or food production, have unique requirements regarding the fluids they handle. Selecting a gasket with suitable chemical compatibility is essential to prevent degradation and ensure safety in operation.
Some materials, like PTFE, are known for their broad compatibility, making them frequent choices for applications with high chemical exposure. On the other hand, elastomers may be limited by specific chemicals, which could lead to failures if not properly evaluated.
Mechanical Strength
Mechanical strength is an important consideration when assessing the suitability of gasket materials. It involves the ability to withstand physical stress and pressure without failure. Gaskets with high mechanical strength are better equipped for high-pressure environments, making them popular in applications such as oil and gas.
This feature allows for greater flexibility in system design and operation. However, it can also contribute to increased rigidity, which may make installation more challenging. Thus, finding a balance between strength and flexibility is key when choosing suitable materials for PHE gaskets.
Types of PHE Gaskets
Understanding the types of PHE gaskets is key to ensuring optimal performance in heat exchangers. Each type serves a unique role, fulfilling specific needs while enhancing the overall system's effectiveness. Selecting the right type directly impacts sealing efficiency, durability, and cost-effectiveness.
Standard Gaskets
Standard PHE gaskets are designed for typical operating conditions in various applications. They are manufactured to fit common plate patterns, making them widely available and easier to source. These gaskets generally offer reliable sealing capabilities under moderate pressure and temperature ranges. The advantage of using standard gaskets lies in their compatibility with many heat exchangers, which simplifies maintenance and replacement. However, they may lack the specialized properties needed for extreme working conditions.
Custom Gaskets
Custom gaskets are tailored to meet specific requirements of individual applications or systems. They can be produced in various shapes, dimensions, and materials depending on the unique demands of the operation. This customization allows for improved sealing performance in particular scenarios. The significant benefit of custom gaskets is their ability to enhance reliability and maintain efficiency in systems with unusual configurations or challenging operational parameters. While they may involve higher initial costs, their long-term performance can outweigh these expenditures by reducing maintenance frequency and downtime.
Specialized Gaskets
Specialized gaskets are engineered for specific conditions that require exceptional material properties. Within this category, we can identify two notable types:
High-Temperature Gaskets
High-temperature gaskets are crucial in settings where heat resistance is paramount. These gaskets are typically made of advanced materials like silicone or specific elastomers that can withstand extreme temperatures. The key characteristic of high-temperature gaskets is their ability to maintain integrity without deforming or experiencing thermal degradation. This makes them a popular choice for industries such as power generation and chemical processing. One unique feature is their thermal stability, allowing them to perform well in applications involving steam or high-temperature fluids. However, consideration must be given to their cost, as specialized materials can be more expensive than standard options.
Low-Temperature Gaskets
Low-temperature gaskets are designed for environments where temperatures drop significantly. Often made from flexible materials like rubber or certain plastics, these gaskets remain functionally efficient in extreme cold. The crucial feature of low-temperature gaskets is their resilience, ensuring a reliable seal even when the environment poses risks such as brittleness. They are beneficial in applications within the food and beverage industry and cryogenic systems. However, it is essential to validate their suitability against specific requirements since not all low-temperature gaskets provide the same level of performance in varying conditions.
Applications of PHE Gaskets
The applications of PHE gaskets are broad and critical in various sectors. Their role in ensuring reliable sealing in heat exchangers cannot be overstated. Effectively designed gaskets maintain the integrity of systems, preventing leaks and ensuring efficient operation. Industries that rely on this technology benefit significantly from their unique properties and advantages.
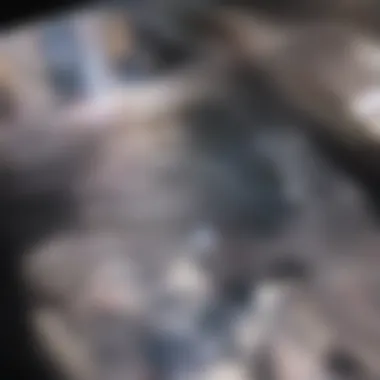
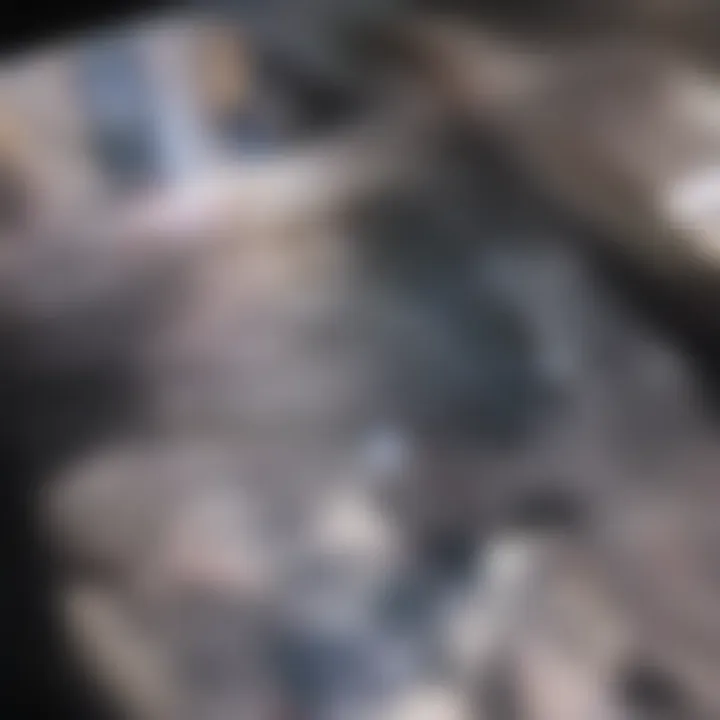
Chemical Processing Industries
PHE gaskets are pivotal in chemical processing industries where fluid dynamics are crucial. They provide effective sealing under high pressure and varying chemical exposures. The chemical resistance offered by materials such as PTFE ensures that aggressive chemicals do not degrade the gasket. Proper seal integrity maintains system efficiency and reduces the risk of contamination and safety hazards.
Food and Beverage Sector
In the food and beverage sector, hygiene is paramount. Gaskets must meet stringent health standards while ensuring that they do not impart any taste or odor to food products. PHE gaskets made from FDA-approved materials meet these requirements efficiently. Their ease of maintenance and cleaning further enhances their suitability for this industry. Ensuring a safe food supply revolves around the role of reliable sealing solutions like PHE gaskets.
Energy Sector
The energy sector is another area where PHE gaskets play a significant role, as they are indispensable in the oil and gas and nuclear power industries.
Oil and Gas Applications
Oil and gas applications rely on PHE gaskets especially due to their ability to operate efficiently in high-pressure environments. These gaskets exhibit a high degree of resilience against harsh materials, making them an excellent choice for sealing applications in pipelines and refineries. Their key characteristic is the capacity to endure thermal cycling and pressure fluctuations common in these settings. The unique feature of PHE gaskets in this sector includes the ability to maintain integrity against potential leaks. This property is a major advantage, as leaks can have catastrophic consequences not only for energy efficiency but also for safety and environmental concerns.
Nuclear Energy
In the context of nuclear energy, PHE gaskets are integral to maintaining the safety and efficiency of reactor systems. The key characteristic that sets these gaskets apart is their capability to handle extreme temperatures and pressures. This makes them a reliable option for cooling systems and associated heat transfer applications. The unique feature of PHE gaskets in nuclear settings is their role in preventing radiation leaks, thereby ensuring operational safety. Their advantages include not only reliability but also longevity under demanding operating conditions.
HVAC Systems
PHE gaskets are also found in HVAC systems where they are vital for maintaining air and fluid integrity. Effective sealing in these systems prevents energy loss, enhancing overall efficiency. The durability of PHE gaskets ensures long-term performance, reducing the need for frequent replacements. The result is a more sustainable approach to managing heating and cooling systems.
In summary, the applications of PHE gaskets extend across multiple industries, each requiring specific performance characteristics to ensure efficiency and safety. The advantages they offer make them invaluable in todayβs industrial landscape.
Advantages of PHE Gaskets
Understanding the advantages of PHE gaskets is crucial for industries relying on efficient heat exchange systems. These gaskets play a significant role in maintaining performance and ensuring the durability of heat exchangers. Choosing the right gasket can lead to improved operation, lower maintenance costs, and enhanced overall efficiency of the systems they serve. Below are the key advantages.
Sealing Efficiency
PHE gaskets significantly improve sealing efficiency in heat exchanger applications. Their design allows for tight seals, preventing leakage of fluids and gases. This is essential for maintaining process integrity, especially in demanding environments like chemical processing or energy production. Proper sealing minimizes cross-contamination and preserves the quality of the products being processed.
Factoring in different materials and precise designs also enhances the adaptability of these gaskets to various operational conditions. With the appropriate gasket choice, energy losses through leakage can be minimized. This translates to better operational efficiency and helps in achieving desired thermal performance levels.
Durability and Longevity
Another key advantage of PHE gaskets is their durability and longevity. Made from robust materials like elastomers and PTFE, they can withstand extreme temperatures and pressures. This resilience is necessary for industries that operate under harsh conditions, especially in the energy sector, where equipment is regularly subjected to severe operating environments.
The longevity of these gaskets reduces the frequency of replacements, translating to lower downtime and maintenance costs. Overall, investing in high-quality PHE gaskets ensures that operations remain stable and reliable, leading to long-term benefits for plant efficiency and equipment lifespan.
Cost-Effectiveness
Cost-effectiveness is a significant aspect of PHE gaskets. Although the initial purchase price might vary based on material and design, the long-term savings often outweigh upfront costs. Savings come from reduced energy loss, minimized maintenance, and fewer replacement needs.
Moreover, efficient sealing reduces the risks of operational disruptions caused by leaks, which can lead to costly production halts. By ensuring critical systems operate smoothly, PHE gaskets contribute to an organization's bottom line, making them a wise investment for any facility dependent on heat exchange technology.
"The right gasket choice is vital for operational efficiency and reliability in heat exchangers."
Selection Criteria for PHE Gaskets
Selection criteria for PHE gaskets are vital, as they directly impact the performance and reliability of heat exchanger systems. Choosing the right gasket involves multiple factors, including environmental conditions, operational requirements, and the specific fluids that will be used. Understanding these criteria can ensure optimal sealing, longevity, and functionality.
Environmental Considerations
Environmental factors play a crucial role in gasket selection. These include temperature fluctuations, humidity levels, and exposure to corrosive agents. The suitability of a gasket material must align with the environmental conditions in which it will function.
One important aspect is the resistance of the gasket material to degradation caused by harsh environments. For instance, gaskets used in chemical processing may be subject to various acids and bases, so selecting materials with high chemical resistance is necessary to maintain integrity. Properly addressing environmental considerations prevents premature gasket failure, ensuring efficient system operation over time.
Operational Parameters
Operational parameters are critical when selecting PHE gaskets, as they dictate the gasket's performance under specific working conditions. Two main factors are pressure requirements and temperature factors, each influencing the effectiveness of the gasket.
Pressure Requirements
Pressure requirements refer to the maximum permissible pressure the gasket can withstand without failing. Gaskets must be rated for the specific pressure levels present in heat exchangers. It is also important to understand the pressure fluctuation scenarios that may occur during operation.
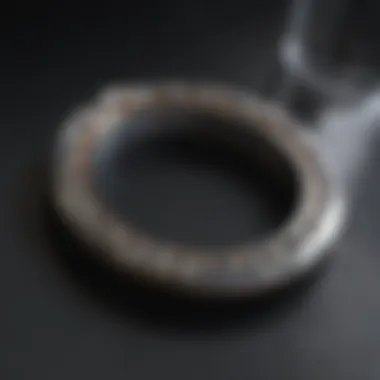
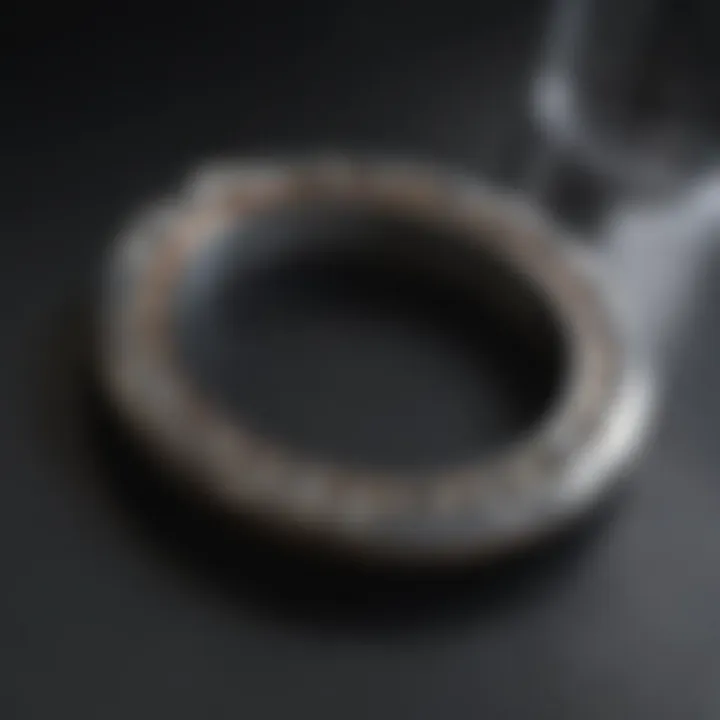
High-pressure environments generally require materials with enhanced mechanical strength. Ductile materials may be a beneficial choice, as they can absorb stress without losing shape. Additionally, proper compression during installation is crucial, as it affects sealing ability and life span.
Temperature Factors
Temperature factors also significantly influence gasket performance. Each gasket material has a specific range of operational temperatures. Operating outside of this range can lead to degradation of the gasket, affecting its sealing properties.
Selecting materials that can withstand high or low temperatures is beneficial for devices dealing with extreme conditions. For instance, silicone gaskets excel in high-temperature applications, while PTFE gaskets can function well in lower temperature situations. Understanding temperature behavior is essential to ensuring the gasket maintains effectiveness under dynamic thermal conditions.
Compatibility with Fluids
Fluid compatibility is a critical criterion for gasket selection. Different fluids can interact with gasket materials in various ways, potentially leading to swelling, dissolving, or other forms of degradation. Therefore, selecting a gasket material that is compatible with the specific fluids being processed is essential.
Materials such as PTFE are known for their broad compatibility with diverse chemicals, making them suitable for numerous applications. Considerations around fluid type, concentration, and temperature are vital when assessing compatibility.
Maintenance of PHE Gaskets
Proper maintenance of PHE gaskets is essential to ensure their performance and longevity in various applications. These components play a critical role in maintaining the integrity of heat exchangers. Regular maintenance can prevent leaks, reduce downtime, and enhance overall system efficiency. In this section, we will examine both inspection procedures and replacement guidelines to provide a comprehensive understanding of gasket maintenance.
Inspection Procedures
Regular inspection of PHE gaskets is crucial for identifying potential wear and tear before it leads to significant issues. Key factors to consider during inspections include:
- Visual Assessment: Inspect gaskets for any visible cracks, tears, or signs of deformation. Look for uneven surfaces that may indicate improper seating.
- Leak Testing: Perform pressure tests and leak detection methods to assess the sealing capability of gaskets. This is especially important in critical applications.
- Surface Checking: Review the contact surfaces for corrosion, buildup of contaminants, or any anomalies that might hinder gasket performance. Consider using specialized tools like gap gauges for precise measurements.
- Temperature Inspections: Monitor the temperature around gaskets to ensure they do not exceed their specified limits. High temperatures can lead to premature failure.
Frequent inspections enhance reliability and reduce the likelihood of unscheduled maintenance, which can be costly.
Replacement Guidelines
Knowing when to replace PHE gaskets is important for maintaining operational efficiency. Factors indicating gasket replacement include:
- Signs of Wear: If gaskets show significant wear, deformation, or damage during inspections, they should be replaced.
- Leakage: Any detectable leaks, especially when they occur regularly, signal that gaskets have lost their sealing capability.
- Material Degradation: Consider the material properties and specifications. Gaskets made of elastomers or PTFE may degrade over time due to environmental exposure.
- Manufacturer Recommendations: Follow guidelines provided by manufacturers regarding service life and replacement intervals to ensure optimal performance.
Proper removal and installation procedures are vital during replacements. Ensure that the surfaces are clean and free from debris. When installing new gaskets, apply appropriate torque to bolts according to specifications to avoid over-compression.
"Regular maintenance and timely replacement of PHE gaskets are key to preventing major failures and ensuring system performance."
By adhering to these maintenance practices, operators can extend the service life of PHE gaskets, thus enhancing operational efficiency and reducing potential losses associated with system downtime.
Innovations in Gasket Technologies
The significance of innovations in gasket technologies lies in their ability to enhance efficiency and performance in various industrial applications. These advancements often lead to improved sealing capabilities, longer operational lifespans, and reduced maintenance costs. In an environment where industries continually seek to optimize processes, the development of more effective gasket materials and manufacturing techniques plays a crucial role.
Advanced Materials
The introduction of advanced materials in gasket technologies has transformed how these components function in heat exchangers and other systems. Materials such as graphite, expanded PTFE (ePTFE), and composite blends are now common in high-performance gaskets. Each of these materials offers unique properties which address specific challenges in sealing applications.
- Graphite: This material provides excellent thermal stability and high resistance to a wide range of chemicals. It can withstand extreme temperatures, making it suitable for applications in industries such as oil and gas, where conditions can be harsh.
- Expanded PTFE: ePTFE gaskets excel in chemical resistance and flexibility. They can accommodate the thermal expansion of metals, ensuring a tight seal over time without compromising performance.
- Composite Blends: Combining various materials can yield a gasket that takes advantage of the strengths and mitigates the weaknesses of individual components. This versatility is valuable across different sectors, especially where lower weight and higher resilience are necessary.
These advanced materials also contribute to sustainability. Many manufacturers are now focusing on options that reduce environmental impact. By using biodegradable materials or sourcing from renewable resources, companies aim to meet the increasing demand for environmentally friendly products.
Manufacturing Techniques
Along with advanced materials, the methods used to manufacture gaskets have also evolved. Innovative manufacturing techniques such as 3D printing, precision die cutting, and automated processes enhance the efficiency and accuracy in gasket production.
- 3D Printing: This technology allows for rapid prototyping and production of complex shapes. It reduces waste and allows for customization, catering to specific client needs without lengthy lead times.
- Precision Die Cutting: This method ensures high accuracy in gasket dimensions. It allows manufacturers to produce large quantities of gaskets with consistent quality, which is essential for applications requiring uniformity.
- Automated Processes: Automation in manufacturing not only speeds up production but also reduces the likelihood of human error. This precision is critical in applications where the integrity of the gasket can impact safety and efficiency.
"Advancements in gasket technologies are more than just improvements; they represent a vital shift towards efficiency and sustainability."
Epilogue
Understanding the role of PHE gaskets is vital for anyone involved in industries that utilize heat exchangers. The gaskets are not just simple components; they play a crucial role in ensuring sealing efficiency, durability, and operational reliability in various systems. The article illuminates how these elements contribute to overall effectiveness in applications ranging from chemical processing to HVAC systems.
Future Trends in PHE Gasket Usage
As industries evolve, so do the technologies associated with PHE gaskets. Several trends are emerging that indicate how the landscape of gasket application may shift in the coming years:
- Introduction of Advanced Materials: New materials are being researched and developed that could enhance the performance of gaskets, improving their thermal resistance and chemical compatibility. Materials like expanded PTFE are gaining attention for their usefulness in demanding environments.
- Sustainability Initiatives: There is a growing push toward sustainable practices in manufacturing. Future gaskets might focus on environmentally friendly materials, reducing waste and improving recyclability.
- Smart Gasket Technology: The rise of IoT in industrial applications could lead to the development of smart gaskets. These gaskets could be equipped with sensors to monitor pressure, temperature, and leak detection in real-time, allowing for proactive maintenance.
- Customization and Adaptation: As operations become more specialized, the need for custom gaskets that meet unique operational demands will likely increase. This could extend to low-volume production runs aimed at specific industrial needs.
With these trends, professionals in the field should stay informed about advancements in materials science and technology that could enhance the performance and longevity of PHE gaskets. By keeping an eye on these developments, industries can make informed decisions, ensuring their systems run efficiently and effectively.
"In the face of technological evolution, the importance of rigorous analysis and understanding of PHE gaskets cannot be understated."
In summary, the future of PHE gaskets is poised for growth and innovation, aligning with broader trends in technology and sustainability.