Understanding Pelletizing Machinery: A Complete Guide
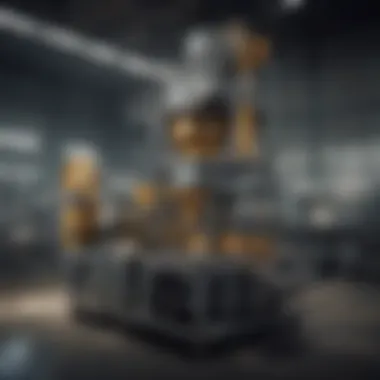
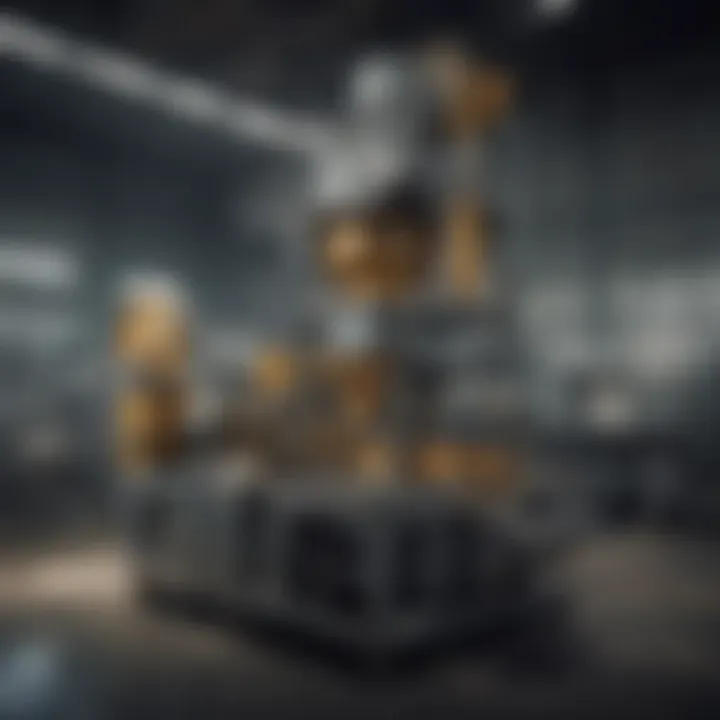
Intro
Pelletizing machinery plays a crucial role in a variety of industries, facilitating the efficient processing of materials. As industries evolve, the demand for optimized, effective machinery grows. Understanding the intricacies of pelletizers can significantly impact production processes for manufacturers, researchers, and industry professionals alike.
In this article, we will explore the various applications of pelletizing machinery, the different types and technologies available, and the importance of selection and maintenance practices. The goal is to provide a comprehensive guide that enhances the reader's knowledge in this domain.
Intro to Pelletizing Machinery
Pelletizing machinery plays a vital role in transforming raw materials into higher-value, easily handled products. This process is not just about making pellets; it is about enhancing material usability across various industries. As industries evolve, the demand for efficient processing and material handling has increased remarkably. Hence, understanding the nuances of pelletizing machinery becomes essential for efficiency and productivity.
Definition and Purpose
Pelletizing machinery refers to equipment designed to convert materials, often in powdered form, into dense, compact pellets. The primary purpose of these machines is to improve the material's physical propertiesβsuch as flow ability, storage stability, and ease of transportation. Pellets are generally uniform in size and can significantly reduce waste.
Industries ranging from agriculture to plastics utilize pelletizing for different reasons:
- Enhanced processing: Materials can be easier to handle when in pellet form.
- Quality control: Uniform pellets promote consistency in manufacturing.
- Cost-effectiveness: Smaller pellets require less energy in transport and storage.
Historical Background
The concept of pelletizing dates back several decades, evolving from simple agricultural processes. Initially, the emphasis was on creating animal feed pellets to ensure better nutritional delivery. Over the years, advancements in technology have transformed this approach. The introduction of various pelletizing machines improved efficiency and consistency, leading to the development of specialized equipment tailored to specific materials.
The growth of industrial applications in the 20th century led to innovations in pelletizing technology. As industries such as biomass, plastics, and minerals gained prominence, so did the need for advanced pelletizing systems. Machine designs have similarly adapted over time, incorporating features like better mixing mechanisms and enhanced quality control processes.
Types of Pelletizing Machinery
The classification of pelletizing machinery plays a crucial role in defining how materials are processed into pellets. Different types of pelletizers serve various industrial needs, and understanding these types is essential for making informed decisions in the realm of manufacturing and material processing. Factors such as efficiency, application, and operational cost greatly depend on the specific type of machinery utilized. By choosing the appropriate pelletizing technology, industries can enhance productivity, reduce waste, and ensure that the end products meet the necessary quality standards.
Ring Die Pelletizers
Ring die pelletizers are the backbone of large-scale pellet production. These machines are characterized by a cylindrical die that rotates around a central shaft, as the feedstock is pressed through the holes in the die to form pellets. This type of pelletizer is particularly valuable for producing uniform pellets with consistent density and size, leading to reduced variation in final products.
One of the primary advantages of ring die pelletizers is their high throughput capacity. They can efficiently produce large volumes of pellets, making them ideal for industries such as animal feed, biomass, and biofuels. Additionally, they tend to be more energy-efficient compared to other types, due to their design and operational mechanics.
However, potential users must also consider the initial investment cost and maintenance requirements associated with ring die pelletizers. While they offer numerous benefits, proper maintenance is crucial for prolonged operation and optimal performance.
Flat Die Pelletizers
Flat die pelletizers are another integral part of pelletizing machinery. In contrast to their ring die counterparts, flat die pelletizers use a flat die where the material is compressed between the die and rollers, converting it into pellets. This design allows for flexibility in producing smaller batches of various materials, catering to both industrial and small-scale needs.
This type of pelletizer is particularly beneficial for applications such as organic fertilizers and specialized feed mixtures since it can produce a wide range of pellet sizes. Furthermore, they have lower initial costs, making them accessible for smaller businesses or startups.
Despite these advantages, flat die pelletizers can have limitations in terms of production capacity and efficiency when compared to ring die designs. Users should weigh their specific requirements against the operational output offered by flat die systems. In environments where high volume is essential, flat die pelletizers may not be the best choice.
Screw Press Pelletizers
Screw press pelletizers represent a more modern approach in the realm of pelletizing technology. Utilizing a screw mechanism, these machines press material through a die, resulting in pellet formation. Screw press pelletizers are particularly effective for materials that are challenging to handle with traditional methods, such as certain plastics and organic materials.
One notable advantage of this type of pelletizer is its ability to handle diverse feedstock without significant adjustments. This adaptability makes screw press pelletizers highly sought after for recycling and waste management industries, where varied materials are common.
However, their operational complexity may require more technical expertise and careful calibration to ensure optimal output. Users of screw press pelletizers should be mindful of these factors, as mismanagement could lead to inefficiencies.
In summary, the type of pelletizing machinery selected can significantly impact operational efficiency, product quality, and overall manufacturing processes. Each type, whether ring die, flat die, or screw press, has its strengths and weaknesses, necessitating thorough evaluation.
Principles of Operation
The principles of operation of pelletizing machinery are crucial to understanding how these machines function efficiently in converting raw materials into valuable pellets. Each step in the process contributes to the final product's quality and consistency, which are vital in various applications. Pelletizing machinery utilizes specific mechanisms and processes that, when understood, can highlight areas for optimization and innovation.
Feed Mechanism
The feed mechanism is the first critical component in the pelletizing process. It ensures a steady and controlled flow of raw materials into the machine. This aspect is important for several reasons:
- Uniform Distribution: A well-functioning feed mechanism guarantees that materials enter the pelletizer uniformly. This uniformity is essential for achieving consistent pellet size and density.
- Material Types: Different materials may require unique handling characteristics. For instance, products like biomass and plastics have different flow properties. An effective feed mechanism can adapt to these variations.
Various types of feed systems are used. Some use gravity, while others employ screw feeders. Choosing the right type often depends on the material properties and the specific pelletizing setup.
Pellet Formation Process
The pellet formation process involves transforming the feed material into pellets under heat and pressure. The significance of this step cannot be overemphasized:
- Die Types: The choice between ring die or flat die systems impacts the pellet's quality and characteristics. Ring die systems often provide better efficiency and throughput for larger production scales.
- Pressure and Temperature Control: Controlling the pressure and temperature during this stage is vital. Too much heat can alter material properties, leading to weaker pellets, while insufficient pressure can result in non-uniform pellets.
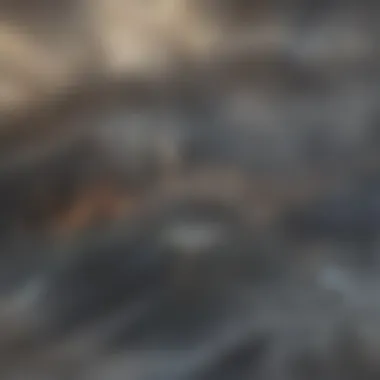
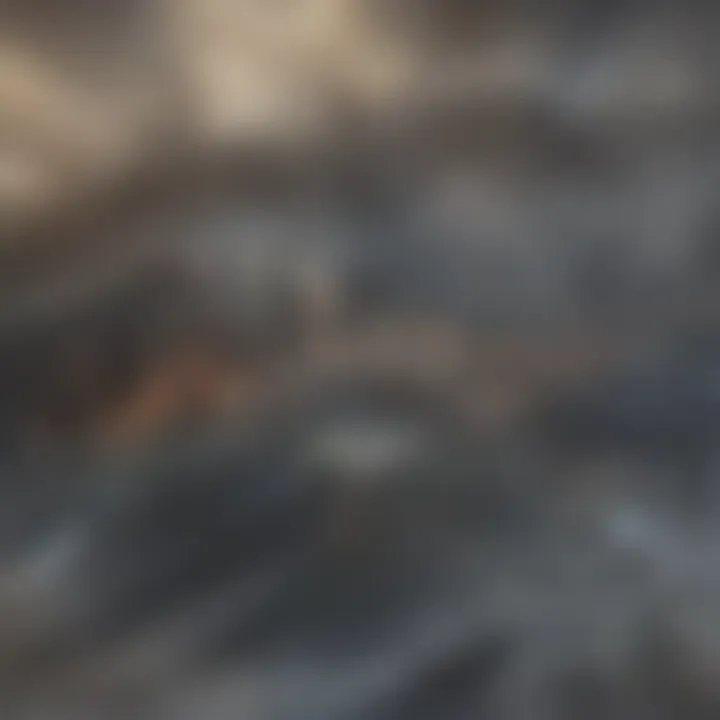
Understanding these details helps manufacturers optimize settings and configurations, reducing waste and enhancing productivity.
Cooling and Drying Processes
Once the pellets are formed, cooling and drying are essential to ensure stability and quality.
- Cooling Mechanisms: Cooling systems help to solidify the recent pellets, retaining their shape and minimizing degradation. There are various cooling techniques, including air cooling and water cooling, which can impact the preservation of nutrients in feed pellets significantly.
- Moisture Control: Proper drying removes excess moisture from the pellets, a factor that directly influences shelf-life and transportability.
A well-optimized pelletizing process significantly impacts both product quality and production efficiency, making it a central concern for manufacturers.
Applications of Pelletizing Machinery
The applications of pelletizing machinery span multiple industries and sectors, underscoring its critical role in both production efficiency and technological advancement. Pelletizing machinery is fundamental in converting raw materials into usable forms, often leading to improved product quality and enhanced operational efficiency. Industries investing in these machines see tangible results, from cost savings to throughput maximization. By detailiung several key sectors utilizing pelletizing technology, one can appreciate not only its versatility but also its transformative impact on material processing and product development.
Industrial Applications
Within industrial settings, pelletizing machinery serves a pivotal function. It streamlines the process of converting bulk materials like wood, plastics, and metals into pellets that are more manageable and easier to transport. Industries such as power generation, where biomass fuels are a focus, leverage this machinery extensively. The densification of biomass makes it more efficient for storage and usage, reducing transportation costs and making energy production more sustainable. The chemical industry also harnesses pelletizing technology to produce fertilizers and other chemical products, enabling precise formulations while optimizing material handling.
Common benefits observed in industrial applications include:
- Enhanced efficiency in material handling: Smaller pellet sizes allow for easier transport and storage.
- Improved uniformity and quality: Machinery ensures that the produced pellets meet specified dimensions and density.
- Waste reduction: Any byproducts generated during the manufacturing process can also be pelletized, thus minimizing waste.
Agricultural Applications
In agriculture, pelletizing machinery finds numerous applications that improve both efficiency and product quality. Feed manufacturing is perhaps the most significant use, where various grains, nutrients, and supplements are combined and pelletized to create animal feed. This method not only enhances feed palatability but also ensures better digestion and nutrient absorption. Additionally, pelletized fertilizers allow for precise application, reducing wastage and ensuring that plants receive the necessary nutrients effectively.
Benefits specific to agricultural applications include:
- Optimized nutrient delivery: Pelletized fertilizers can be more efficiently distributed across agricultural lands.
- Enhanced feed intake: Livestock often prefer pelletized feed due to its texture and ease of consumption.
- Sustainability: By efficiently utilizing organic waste in agriculture, pelletizing supports eco-friendly farming practices.
Nutritional Products
The nutritional industry has also adopted pelletizing machinery for producing health supplements and dietary products. This sector demands high-quality processing to ensure that the nutritional value is retained post-manufacturing. Pellets made from various food sources are used in protein supplements, dietary aids, and weight management products. The versatility of pelletizing machinery allows for the incorporation of diverse ingredients while maintaining consistency in size and composition.
Key advantages in nutritional products include:
- Preservation of ingredient quality: Careful handling during pelletizing maintains vitamins and minerals.
- Convenience: Pellets can be easily packaged and consumed in various forms.
- Customization: The ability to adjust formulations aids in meeting specific dietary needs or preferences.
In summary, the applications of pelletizing machinery highlight its critical importance across various sectors. Understanding how these machines function in industrial, agricultural, and nutritional contexts helps stakeholders make informed decisions when it comes to investing in such technology.
Common Materials Processed
Understanding the common materials processed through pelletizing machinery is essential to grasp the full scope of its industrial applications. Each material presents unique challenges and benefits during the pelleting process. By identifying these materials, one can appreciate the diverse capabilities of pelletizers and make informed decisions regarding machinery selection. This contributes to improved efficiency and product quality in various sectors. It is also critical for professionals working in processing industries to stay aware of the characteristics and requirements of these materials.
Biomass
Biomass is a prominent category making use of pelletizing technology. This includes organic materials derived from plants and animals. Biomass pellets are favored for their high energy content and are often utilized as a renewable energy source. The process of converting biomass into pellets enhances its bulk, storage, and transportability, which is advantageous in energy production settings.
Key aspects to consider:
- Feedstock Variety: Raw materials such as wood residues, agricultural leftovers, and energy crops are frequently used.
- Moisture Content: The moisture level in biomass should be controlled effectively, as it influences both the pelleeting efficiency and the resultant pellet quality.
- Additives: Sometimes, binding agents are necessary to improve pellet density and durability.
The biomass sector has observed a surge in interest due to growing environmental concerns, making effective machinery for biomass pelleting an important consideration for businesses.
Plastic and Waste Materials
The pelletization of plastic and waste materials is gaining more traction in recent years. This process allows for recycling and repurposing materials that would otherwise contribute to environmental pollution. Plastic pellets created from recycling waste are instrumental in producing new plastic products, therefore closing the loop in plastic usage.
Important factors include:
- Material Type: Different plastics, such as polyethylene and polypropylene, exhibit distinct properties and require tailored processing methods.
- Contamination: Thorough cleaning procedures are critical to generate high-quality pellets and maintain the integrity of end products.
- Granulation: The initial granulation of waste materials can affect the pelleting efficiency and final product quality.
With the global push towards sustainability, the role of pelletizing machinery in managing plastic waste cannot be overstated. This aligns businesses with eco-friendly practices while also fulfilling material demands.
Mineral and Chemical Substances
Mineral and chemical substances also find processing advantages through pelletizing technology. Various minerals can be pelletized for improved handling and application in diverse industries such as fertilizers, animal feed, and chemical manufacturing.
Considerations for this category include:
- Particle Size: Uniformity in particle size is essential for consistent quality in the pelleting process.
- Chemical Composition: Understanding the chemical properties of minerals allows for better formulation and blends, enhancing the pellets' effectiveness.
- Durability: The physical properties of the pellets must withstand transportation and storage to prevent degradation.
The adoption of pelletizing for minerals is becoming more common, particularly as industries seek to optimize production processes while maintaining quality.
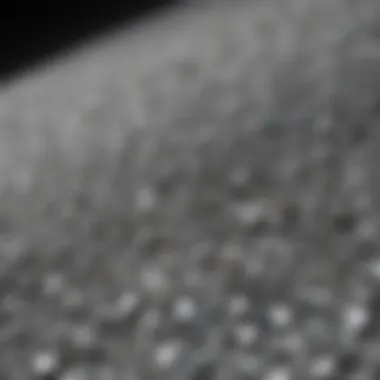
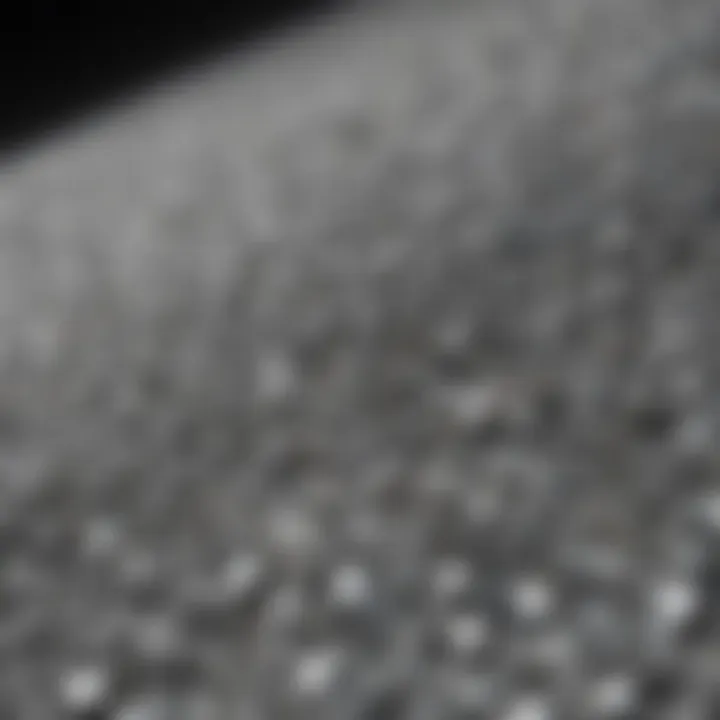
Technological Advancements in Pelletizing Machinery
Technological advancements have fundamentally redefined the landscape of pelletizing machinery. They enhance productivity, increase efficiency, and offer greater flexibility for various applications. In an era where sustainability and efficiency are paramount, these advancements are not merely beneficial; they are critical.
Automation and Control Systems
Automation has emerged as a cornerstone in modern pelletizing systems. Automated machinery simplifies operations and minimizes human intervention, resulting in consistent production quality. These systems utilize sensors and software to monitor various parameters. This includes temperature, pressure, and moisture levels, ensuring that the process runs smoothly with minimal disruption.
Incorporating advanced control systems allows for real-time adjustments. Operators can tweak settings instantaneously based on input data, leading to improved output quality. Additionally, integration with Industry 4.0 technologies enables remote monitoring and predictive maintenance. This reduces downtime and extends the life of the machinery, making it a wise investment for any organization reliant on pelletizing processes.
Energy Efficiency Improvements
Energy efficiency has become a vital consideration in the design of new pelletizing machinery. Manufacturers focus on reducing energy consumption without sacrificing output. Innovative techniques such as variable frequency drives (VFDs) adjust motor speeds based on current demand. This has shown to significantly reduce power usage, particularly during low-activity periods.
Furthermore, some newer models employ regenerative braking systems. These systems recapture energy that would otherwise be lost during operation. Such improvements not only lower operational costs but also contribute to environmentally friendly practices within the industry. Maintaining a focus on energy efficiency may also lead to favorable regulatory outcomes and enhance corporate responsibility within the sector.
Innovations in Material Handling
Effective material handling is essential for pelletizing efficiency. Innovations in this field have streamlined the process from raw material feeding to final product discharge. Automated feeders, for instance, ensure that the right amount of material enters the system at the correct rate. This consistency directly impacts the quality of the final pellets.
Moreover, advancements in conveyor technology allow for smoother transportation of materials. Systems equipped with load sensors can adjust their speed based on real-time data. This optimization minimizes waste and maximizes throughput. Additionally, specialized material handling systems address the unique properties of varied inputs, further enhancing performance.
"Technological advancements are not just enhancements; they are essential for maintaining competitiveness in the pelletizing sector."
In summary, the continual evolution of technology within pelletizing machinery is paramount. From automation and control systems to energy efficiency and material handling, these advancements drive the industry forward. Organizations must adapt to these changes. A focus on technology not only improves production but positions companies to meet the complex demands of an ever-evolving market.
Factors to Consider When Choosing Pelletizing Machinery
Choosing the right pelletizing machinery is crucial for optimizing production and ensuring efficient processes. This decision impacts not only the quality of the pellets produced but also affects operational costs and throughput. Several key factors need careful consideration to ensure that the selected machinery aligns with production goals and material specifications.
Material Properties
The characteristics of the material to be pelletized play a fundamental role in the choice of machinery. Different materials exhibit varying behaviors under processing conditions. For instance, the moisture content, particle size, and composition affect how easily a material can be pelletized.
- Moisture Content: Higher moisture levels can lead to challenges in pellet formation and might require specific types of pelletizers that can manage such conditions effectively.
- Particle Size: Uniformity in particle size is essential. Inconsistent sizes can lead to uneven pellet quality. Ring die pelletizers might be more suitable for finely ground materials, while flat die pelletizers may work better with coarser feed.
- Composition: Knowing whether the material is organic, plastic, or mineral helps in selecting the right machine equipped to handle those specific properties.
In summary, understanding the properties of the feed material helps ascertain the kind of machinery that can produce the most effective and high-quality pellets.
Production Capacity Requirements
Another significant factor is production capacity. The volumes of production vary considerably based on industry demands and production goals. Each type of pelletizer has its specific capacity limits, which can influence operational efficiency.
- Volume Needs: Businesses must analyze their current and projected production volumes. Underestimating capacity can lead to bottlenecks, causing delays and lost opportunities.
- Scalability: It is vital to assess whether the chosen machinery can be upgraded or expanded to accommodate future growth without requiring a complete overhaul of the system.
- Operational Speed: Faster operating machines can lead to higher production rates but could also require greater investment. Balancing speed with quality is essential for meeting production targets.
Capacity considerations help in selecting machinery that aligns with both immediate needs and long-term operational strategies.
Budget Constraints
Finally, budget constraints play a vital role in selecting pelletizing machinery. Understanding the cost implications associated with different types of machines is necessary for making financially sound decisions.
- Initial Investment: The purchase price of machinery varies widely based on features and capabilities. Businesses must evaluate their budget and whether they can afford high-end models or need to opt for more economical options.
- Operating Costs: Beyond manufacturing costs, considerations should include energy consumption, maintenance expenses, and labor costs that correlate to the use of the machinery.
- Return on Investment: It is important to analyze the potential ROI for the chosen equipment. Machines that may have a higher initial cost might offer better durability and efficiency, thereby lowering long-term costs.
Careful budgeting ensures that companies can invest in durable and efficient machinery without straining their financial resources.
"Choosing the right pelletizing machinery involves a holistic understanding of material properties, production needs, and budget constraints to ensure sustainable and efficient operations."
Maintenance Practices for Pelletizing Machinery
Regular maintenance of pelletizing machinery is essential to ensuring an optimal performance and longevity of the equipment. The proper upkeep not only enhances the efficiency of the machinery but also minimizes the risk of unexpected failures that could lead to significant downtimes and financial losses. Strong maintenance practices foster a reliable production environment that ultimately contributes to better manufacturing outcomes.
Routine Inspection and Cleaning
Routine inspection is arguably the cornerstone of effective maintenance for pelletizing machinery. This practice involves systematically checking various components for signs of wear, damage, or malfunction. Common areas to inspect include the dies, rollers, and feed mechanisms. Bi-weekly or monthly inspections help identify minor issues before they escalate into major problems.
Cleaning is equally important. Pelletizing machines often work with materials that can create residues and clogs. Regular cleaning helps to prevent these issues. The process may include:
- Removing buildup on the dies and rollers to ensure optimal pellet formation.
- Cleaning the feeding system, which can prevent jams and irregular flow of the raw materials.
- Inspecting and cleaning the cooling system to ensure efficient temperature control.
Incorporating a thorough cleaning regime can significantly extend the life of pelletizing machinery, ensuring consistent product quality and reducing maintenance costs in the long run.
Lubrication and Part Replacement
Proper lubrication is vital in reducing friction between moving parts. Lubricants minimize wear and tear, and help parts function smoothly. The lubrication schedule may vary based on the specific machinery and usage patterns, but it should generally be performed on a regular basis, often every few weeks or even daily in high-use scenarios.
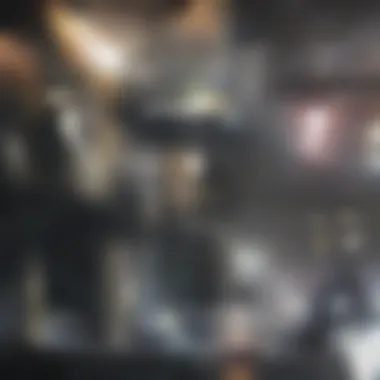

Common areas that require lubrication include:
- Bearings: These are critical to maintaining proper alignment and movement of moving parts.
- Gears: Well-lubricated gears reduce the chances of noisy operation and unwanted heat.
- Roller assemblies: Ensuring these are properly greased helps maintain their smooth operation.
Part replacement becomes necessary when wear is too extensive. Identifying when to replace parts rather than just lubricate them is key. When components become beyond repair, timely replacement prevents disruptions in production.
Troubleshooting Common Issues
Even with routine maintenance, problems may still arise in pelletizing machinery. Troubleshooting common issues is critical to minimize downtime and ensure continuous production. Some frequent problems include:
- Irregular Pellet Sizes: Often caused by inconsistent feed rates or worn-out dies. Adjusting the feed mechanism and monitoring die conditions can solve this issue.
- Overheating: Usually indicates a malfunction in the cooling system or inadequate lubrication. Regular checks can help pinpoint the exact cause.
- Unusual Noises: Grinding or rattling noises can signify a misalignment or part failure. Investigating these sounds promptly will often avoid further damage.
A structured approach to troubleshooting can greatly reduce the time taken to identify and fix problems. Keeping records of issues and their resolutions can also provide invaluable insights for future maintenance activities.
Effective maintenance not only saves costs but also increases productivity in pelletizing operations.
Economic Impact of Pelletizing Machinery
The economic effects of pelletizing machinery are significant in various sectors, including agriculture, environmental management, and manufacturing. These machines play a crucial role in enhancing production efficiency, enabling cost-effective processes, and adjusting to market demands. Their influence extends beyond operational aspects, affecting profitability and sustainability in the industries that employ them.
Contribution to Production Efficiency
Pelletizing machinery inherently boosts production efficiency. By converting raw materials into uniform pellets, they ensure better material handling, storage, and transportation. This uniformity reduces waste and enhances product quality. The efficiency of these machines often results in higher throughput rates.
- Consistent pellet size improves combustion efficiency in biomass applications.
- Enhanced feed flow during production lowers energy consumption.
- Higher output translates into improved industrial sustainability.
"Efficient pelletizing machinery reduces processing times and energy requirements, providing a competitive edge in various industries."
Cost Reduction Strategies
Cost efficiency is critical for operations relying on pelletizing equipment. These strategies can significantly lower production costs:
- Energy Efficiency Improvements: Investing in energy-efficient machines or retrofitting existing models can lead to substantial energy savings. This includes using modern motors or advanced control systems that optimize energy use.
- Material Optimizations: Selecting the appropriate feedstock can enhance output without increasing costs. For example, using lower-cost raw materials that still meet quality standards can minimize expenses while maintaining production levels.
- Preventive Maintenance Practices: Regular maintenance avoids unplanned downtime and costly repairs. By implementing a rigorous preventive maintenance schedule, companies can extend the lifespan of their machinery.
Market Trends and Demand Analysis
Understanding current market trends is essential for manufacturers and suppliers of pelletizing machinery. The demand for pellets, particularly in energy production from biomass, is increasing due to a global push for sustainable practices. Key trends include:
- Growth in Renewable Energy: The rising need for alternative energy sources elevates demand for biomass pellets. As countries promote greener energy solutions, pelletizing machinery becomes a vital component.
- Shift in Consumer Preferences: There is a growing awareness of environmentally friendly products. As consumers choose sustainable options, industries are adapting their processes, leading to higher demand for pelletized products.
- Technological Innovations: Advances in pelletizing technology further support market growth. Enhanced machinery with better efficiency and output capabilities attracts businesses looking to optimize their production processes.
Research Trends in Pelletizing Technology
Research in pelletizing technology is vital for several reasons. It aids in understanding how equipment and processes can be optimized and further developed to enhance productivity and efficiency. As industries evolve, the demand for high-quality pellets and minimized environmental impact has driven research efforts. This section outlines the current academic focus and expected future directions in this field, emphasizing their importance in advancing pelletizing technologies.
Current Academic Research Focus
Academic research in pelletizing technology often emphasizes improving the efficiency of existing machinery and the development of new methods. Current research areas include:
- Material Behavior Studies: Understanding how different materials respond during the pelletizing process has become a focus. Researchers analyze variables such as particle size, shape, and moisture content, which influence pellet formation and quality.
- Process Optimization: Scholars are investigating methods to optimize parameters like temperature, pressure, and feed rate. Effective optimization can lead to higher production rates and superior pellet characteristics.
- Sustainability Practices: There is growing interest in making pellet production more sustainable. This involves researching renewable feedstocks and minimizing energy consumption during production.
- Digitalization and Automation: The integration of advanced monitoring and control systems in pelletizing processes is also under study. These technologies aim to enhance process reliability and reduce operational costs through automation.
Future Directions and Innovations
As industries continue to evolve, so too must pelletizing technologies. Future research initiatives may include:
- Advanced Materials: Finding innovative materials that can reduce energy usage or improve pellet quality will be critical. Research into nanomaterials and biodegradable options is pertinent here.
- Smart Pelletizing Systems: The trend toward Industry 4.0 suggests that future technologies will involve smart manufacturing systems. These systems will utilize big data and machine learning to predict process outcomes, allowing for real-time adjustments to enhance performance.
- Lifecycle Analysis: Future studies may focus on lifecycle assessments of pelletizing machinery to understand long-term sustainability impacts. This will involve evaluating environmental consequences from production to end-of-life disposal.
"Research in pelletizing technology supports industries in advancing their processes, ensuring product quality, and minimizing environmental impact."
- Integration with Renewable Energy: Future innovations may explore integrating renewable energy sources in pellet production. Abundant and renewable energy can help mitigate conventional energy use, aligning with global sustainability goals.
By focusing on these areas, the future of pelletizing technology can lead to more efficient, sustainable operations across various industries. This research not only enhances productivity but also ensures products meet modern environmental standards.
Culmination
The conclusion is a critical component of any extensive article. It not only serves to encapsulate the main ideas presented throughout but also reinforces the importance of understanding the multifaceted nature of pelletizing machinery. With growing demand in various industries, the efficiency brought by these machines cannot be overstated. The conclusion synthesizes the knowledge shared, allowing readers to reflect on its practical implications.
Key elements such as diverse applications, technology advancements, and maintenance practices offer valuable insights into the utility and significance of pelletizing machinery. This section also emphasizes the economic impact, helping to connect operational dynamics with profitability and sustainability considerations. By concluding the article effectively, readers gain a clearer view of how these machines contribute to operational efficiencies and the overall value chain.
Summary of Key Points
- Diverse Applications: Pelletizing machinery finds relevance in agriculture, waste management, and mineral processing, demonstrating its versatility across sectors.
- Types of Machinery: Different pelletizers, including ring die and flat die designs, cater to unique material needs, ensuring optimal performance.
- Technological Developments: Innovations like automation and energy efficiency improvements play a crucial role in shaping the future of pelletizing technologies.
- Maintenance Practices: Regular maintenance routines significantly extend machinery lifespan and improve productivity.
- Economic Benefits: Integrating pelletizing machinery can lead to substantial cost savings and enhanced production capacities.
Future Implications and Recommendations
As industries evolve, pelletizing machinery will likely undergo further transformations to meet changing demands. Future research should focus on enhancing automation and integrating smart technologies to improve operational efficiencies. Consideration should be given to:
- Sustainability: Future designs must prioritize eco-friendly practices, reducing waste and promoting renewable resources.
- Customization: Machinery must adapt to diverse material specifications to facilitate broader applications.
- Training Programs: Investing in human capital through education about new technologies can ensure that the workforce adapts to advancements in machinery.
- Collaboration: Engaging with academic institutions and industry players can drive innovation through shared knowledge and expertise.
As the landscape of pelletizing technology continues to expand, stakeholders must remain vigilant and proactive in their approach to harnessing its full potential.