Understanding ISO Robot Safety Standards: A Detailed Guide
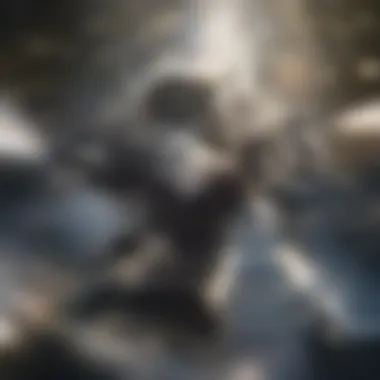
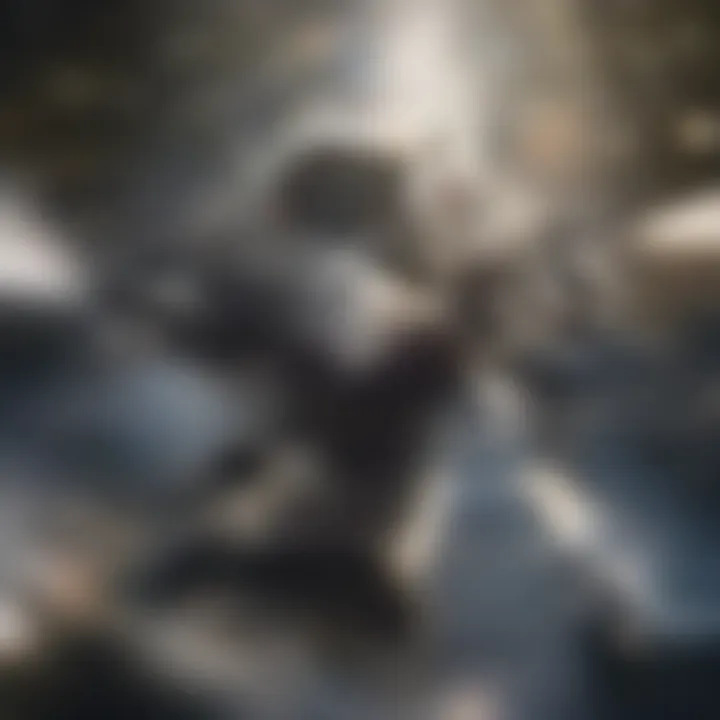
Intro
In recent years, the integration of robotic systems into various sectors has transformed operations, enhanced productivity, and raised the stakes for workplace safety. As robots evolve in complexity and functionality, the demand for standardized safety measures becomes crucial. Here, the International Organization for Standardization (ISO) plays a vital role.
The ISO has developed specific safety standards aimed at ensuring that robots and automated equipment are safe for use in diverse environments. Understanding these standards is essential for students, researchers, educators, and professionals who are involved in the robotics field. These standards not only guide manufacturers in designing safe robots but also protect operators from potential hazards.
Research Context
Background Information
ISO 10218 and ISO/TS 15066 are two fundamental standards that outline the safety measures associated with industrial robots. ISO 10218 focuses on the safety requirements for robots themselves, while ISO/TS 15066 addresses collaborative robots, which work alongside humans. The history of these standards reveals a growing awareness and need for safety in automation, driven by increased robot deployment across industries. This evolution reflects a shift from traditional safety measures to more dynamic, integrated approaches to human-robot interaction.
Importance of the Study
Compliance with ISO standards is not merely a regulatory requirement; it is a commitment to the safety and well-being of all personnel involved. Industries that implement these standards often experience improved operational reliability and reduced incidents. Understanding these standards empowers various stakeholders, including operators and manufacturers, to actively participate in risk assessments and safety improvements, ultimately fostering a culture of safety.
"Safety standards are critical; they are the foundation upon which the safe operation of robotic systems is built."
Employing these standards has substantial implications. It ensures that organizations not only adhere to legal obligations but also enhance their credibility in the market. As such, this article aims to delve deeper into the nuances of ISO robot safety standards, offering comprehensive insights into their structure, implications, and best practices for implementation.
Intro to ISO Robot Safety Standards
The rise of automation and robotics in various industries necessitates a framework that ensures the safety of both operators and machines. ISO robot safety standards are central to establishing such a framework. These standards provide guidelines that help organizations to identify risks and implement measures to mitigate them.
Robots are increasingly integrated into manufacturing, healthcare, and service industries, among others. This integration introduces potential hazards, making safety a priority. The importance of ISO standards in robotic safety cannot be overstated. They serve as a benchmark for designing safe machines and for training operators effectively. Compliance with these standards is not just about adhering to regulations; it is about fostering a culture of safety that benefits everyone.
ISO standards, such as ISO 10218 and ISO/TS 15066, focus on various aspects of robotic applications. These include design requirements, operational safety measures, and maintenance protocols. By adhering to these standards, manufacturers help ensure that their robots are both efficient and safe for human interaction.
The adoption of ISO safety standards also has implications beyond safety. For manufacturers, compliance can lead to increased marketability and trust among clients. For employees, it can mean safer working conditions and reduced risk of injury. Thus, understanding these standards is vital for anyone involved in the robotics field.
"Adhering to ISO standards is not merely a regulatory requirement; it is a commitment to excellence in safety practices that has far-reaching implications for all stakeholders."
In exploring the nuances of ISO robot safety standards, this article will not only outline key regulations but also discuss their historical context, relevance, and impact on current practices in various sectors. Understanding these standards will equip professionals with the essential knowledge required to navigate the complexities of robot safety effectively.
Historical Context of Robotic Safety Standards
Understanding the historical context of robotic safety standards is crucial for grasping their present importance. As the use of robotics has expanded across various industries, the need for safety protocols has become more pressing. Initially, robots were introduced in manufacturing to enhance efficiency and reduce labor-intensive tasks. However, with the rise in automation, incidents involving robotic equipment raised concerns about workplace safety.
In the early stages of robotics, there were no formal guidelines to govern the safe operation of these machines. This ambiguity often resulted in accidents that could have been avoided. Recognizing this gap, stakeholders began to advocate for the establishment of safety standards. The evolution of robotic safety standards was driven by the necessity to protect workers from potential hazards associated with robotic operations. They provided a structured approach to ensuring safety during the operation, maintenance, and programming of robotic devices.
The introduction of ISO standards in the late 20th century marked a pivotal moment. The International Organization for Standardization aimed to develop uniform safety practices that could be adopted globally. ISO 10218, for instance, was one of the first standards addressing safety in industrial robots, focusing on risk reduction and the implementation of safeguards. The establishment of this and other standards gradually contributed to a culture of safety that prioritized human well-being alongside productivity.
Throughout the 2000s, as robots became more sophisticated and began to share workspace with humans, the relevance of safety standards transitioned to account for these changes. ISO/TS 15066 was introduced to address the unique challenges posed by collaborative robots, signifying a more nuanced understanding of robot-human interaction. This progression not only reflects technological advancements but also highlights the growing recognition of safety as an ethical responsibility in technological development.
"The evolution of robotic safety standards exemplifies how industries can adapt to technological changes while prioritizing human safety."
The historical context also includes legal frameworks that have emerged in tandem with standards. Governments and regulatory bodies recognized the necessity for compliance with safety protocols to mitigate liability and ensure worker safety. Thus, organizations began to align their operations with ISO standards to fulfill these requirements.
Overview of ISO Standards
ISO standards play a crucial role in the robotics industry by providing guidelines and benchmarks for safety and efficiency. These standards are established by the International Organization for Standardization (ISO), which is an independent, non-governmental international organization. Their purpose is to enable organizations to ensure high-quality performance and safety of their products, services, and systems. In the context of robotics, compliance with these standards not only enhances operational effectiveness but also fosters trust among users and stakeholders in robotic technology.
When we delve into the specifics, we see that ISO standards help in:
- Defining Safety Protocols: They outline safety measures that need to be integrated into robotic designs, ensuring that machines operate effectively without posing risks to humans or other machines.
- Establishing Best Practices: They set the foundation for best practices in the industry, guiding manufacturers on how to build safe robots while promoting innovation.
- Enhancing Industry Consistency: Standards create a uniform approach to safety across the industry, ensuring that all players adhere to the same level of quality and responsibility.
Definition and Purpose of ISO
The International Organization for Standardization (ISO) was founded in 1947 and is based in Geneva, Switzerland. It aims to develop international standards that can be adopted universally across different sectors. For robotics, ISO provides frameworks that define safety and operational parameters. These standards guide manufacturers and operators in ensuring that their robotic systems are not only effective but also compliant with safety regulations. Standards such as ISO 10218 and ISO/TS 15066 are pivotal as they directly address safety in robotic applications.
Relevance of Standards in Robotics
In an era where robots are increasingly entering work environments alongside humans, the relevance of ISO standards cannot be overstated. They are essential for:
- Reducing Risks: By complying with these standards, organizations can identify and mitigate potential hazards before they lead to accidents.
- Facilitating Collaboration: As collaborative robots become more common, ISO standards help delineate the responsibilities of both robots and humans in shared workspaces.
- Supporting Compliance: Many jurisdictions require adherence to specific ISO standards as part of their legal framework, making compliance not just a best practice but a legal necessity in many cases.
"ISO standards are not mere suggestions; they are the cornerstone of safety and reliability in robotics."
In summary, understanding ISO standards is not only beneficial but necessary for anyone involved in the robotics field. As technology advances, the importance of these standards in creating safe, efficient, and trustworthy robotic systems will only continue to grow.
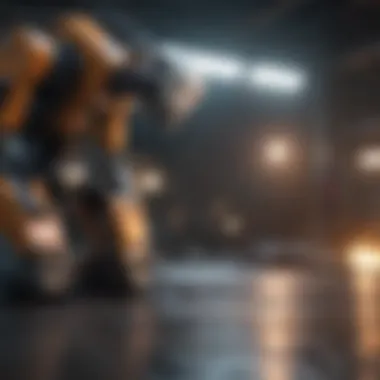
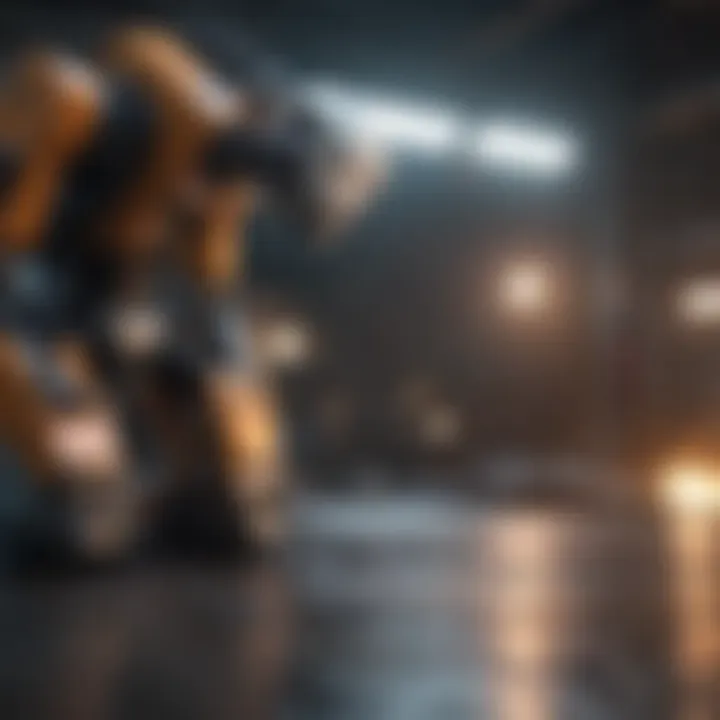
Key ISO Standards Related to Robots
The key ISO standards related to robots serve as foundational guidelines that structure safety protocols and operational procedures in robotic applications. These standards are critical not only for ensuring the safety of human operators but also for enhancing the performance of robotic systems. As robotics continues to evolve, compliance with these standards becomes paramount to mitigate risks associated with industrial environments.
ISO β Robots and Robotic Devices
This standard is divided into two distinct parts, each concentrating on different aspects of robotic technology and its integration into various systems.
Part 1: Robots
Part 1 of ISO 10218 focuses on the design and operational requirements of industrial robots. It highlights the technical specifications necessary to define how robots should function reliably and safely. A key characteristic of this part is its emphasis on operational safety. It outlines the necessary safeguards and methodologies needed to prevent accidents and injuries during the robotβs operation.
The beneficial nature of Part 1 lies in its comprehensive guidelines that assist manufacturers in developing robots that meet rigorous safety standards. Its unique feature includes the integration of risk assessment practices within the design phase, ensuring that safety is built in from the start. This proactive approach significantly reduces the likelihood of safety failures during live operations.
However, a potential disadvantage could be the complexity involved in adhering to these specifications, especially for smaller enterprises with limited resources. Despite this, the standard stands as a vital resource ensuring that industrial robots operate safely and effectively.
Part 2: Safety Requirements
Part 2 delineates the safety requirements that must be met by robotic devices. This section complements Part 1 by providing detailed information on the functionality and design criteria required to ensure safe operation. A prominent characteristic of this part is its focus on identifying potential hazards associated with robotic operations, which is essential for creating a safe work environment.
This aspect makes Part 2 a popular choice for organizations aiming to achieve high safety benchmarks. Its core advantage is the structured methodology it offers for conducting thorough safety assessments. Furthermore, its requirements are adaptable to various robotic applications, making it a versatile tool for manufacturers.
One unique feature of Part 2 is its provision for ongoing compliance checks, which ensures that safety measures are maintained and updated as needed. This characteristic strengthens its applicability in dynamic work environments, though it might demand additional resources for continuous evaluation and oversight.
ISO/TS β Collaborative Robots
ISO/TS 15066 specifically addresses the requirements for collaborative robots, or cobots, which are designed to work alongside human operators. This standard emphasizes the need for safety measures that account for the unique interactions that occur in collaborative environments. A key aspect of this standard involves defining acceptable limits for robot force and speed to prevent injury during collaborative tasks.
Its relevance is underscored by the rapid rise of collaborative robotics in various sectors, particularly manufacturing. The distinct safety measures provided by ISO/TS 15066 serve as an essential framework to navigate the emerging field of human-robot collaboration. Embracing these standards can lead to improved productivity while ensuring operator safety.
Importance of ISO Compliance
ISO compliance is crucial in the realm of robotics for multiple reasons. Adhering to international standards ensures that robotic systems are built and operated with safety as a priority. This compliance not only protects human workers but also enhances productivity by reducing the risk of accidents and technical failures. Understanding and implementing ISO standards enable organizations to create a safer working environment, thus fostering trust among employees and stakeholders.
Legal and Regulatory Implications
The legal ramifications of non-compliance with ISO standards can be significant. Organizations that fail to adhere to these guidelines may face hefty fines, legal action, or even loss of operational licenses. In various jurisdictions, robotic safety standards are not just recommendations; they are often legally binding. This means that manufacturers and operators must integrate these regulations into their operations to ensure lawful practices and safeguard against potential litigation.
Moreover, the issue of liability emerges when accidents occur. If a robot malfunctions and injures a worker, the absence of compliance documentation can result in severe legal repercussions for the organization. Thus, maintaining ISO compliance not only keeps businesses within legal boundaries but also minimizes operational risks.
Impact on Industry Practices
ISO compliance shapes industry practices in several key areas. For starters, it often leads to the optimization of safety protocols. Businesses that follow ISO standards regularly update their safety practices, ensuring that they are aligned with the latest advancements in technology. This enhances their overall operational efficiency.
Furthermore, adherence to these standards can boost a company's reputation. Clients and collaborators prefer to work with firms that prioritize safety and compliance. A strong commitment to ISO guidelines can thus become a competitive advantage in the robotics industry.
In addition, employee training programs often incorporate ISO standards. This ensures that personnel are well-versed in safety measures and understand the role of robotics in their work environment. Such comprehensive training mitigates risks and prepares employees for potential challenges that may arise.
Risk Assessment in Robotic Applications
Risk assessment in robotic applications serves as a critical component in maintaining safety and efficiency in various industries. As robots become more prevalent in workplaces, understanding the potential hazards is essential. This process involves identifying, analyzing, and managing risks associated with robotics. A well-structured risk assessment ensures that robotics systems operate with reduced dangers to human operators and the surrounding environment.
By systematically examining potential risks, stakeholders can implement effective protocols to mitigate those hazards. It benefits organizations by enhancing safety, reducing liability, and improving overall operational efficiency. The increasing integration of robotics in manufacturing, healthcare, and logistics highlights the necessity for a robust risk assessment framework.
Identifying Hazards
Identifying hazards is the first step in a comprehensive risk assessment. It requires a thorough examination of the robotic systems in use, including their environment, operation, and interaction with human workers. Common hazards include mechanical failure, improper programming, and unsafe operator procedures.
Some typical methods to identify hazards include:
- Workplace Inspections: Regular inspections of robots and surrounding areas help find potential risks before they cause accidents.
- Failure Mode and Effects Analysis (FMEA): This analytical procedure evaluates potential failures in a system, identifying their causes and consequences.
- Hazard and Operability Study (HAZOP): A structured approach that investigates how process conditions can result in hazards, focusing on deviations from intended operation.
Collectively, these strategies enhance the chance of recognizing issues that may compromise safety. Proper documentation of identified hazards allows organizations to take proactive measures against them.
Risk Reduction Strategies
After hazards are identified, implementing risk reduction strategies becomes essential. These strategies can vary widely depending on the nature of the robotic application and specific risks involved. Effective measures include:
- Engineering Controls: Redesigning robots for safety, including adding protective barriers or safety interlocks.
- Administrative Controls: Establishing safety policies and providing training for operators about safe practices while working with robots.
- Personal Protective Equipment (PPE): Utilizing appropriate safety gear for workers in proximity to robotic systems.
The focus is on minimizing risks to acceptable levels while maintaining productivity. This approach often requires collaboration between engineers, safety experts, and operators.
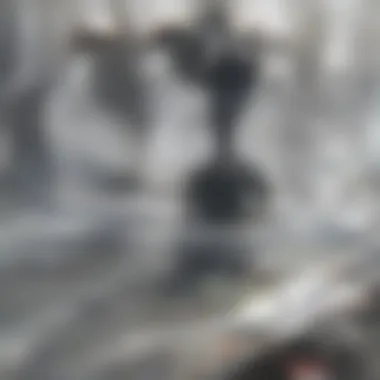
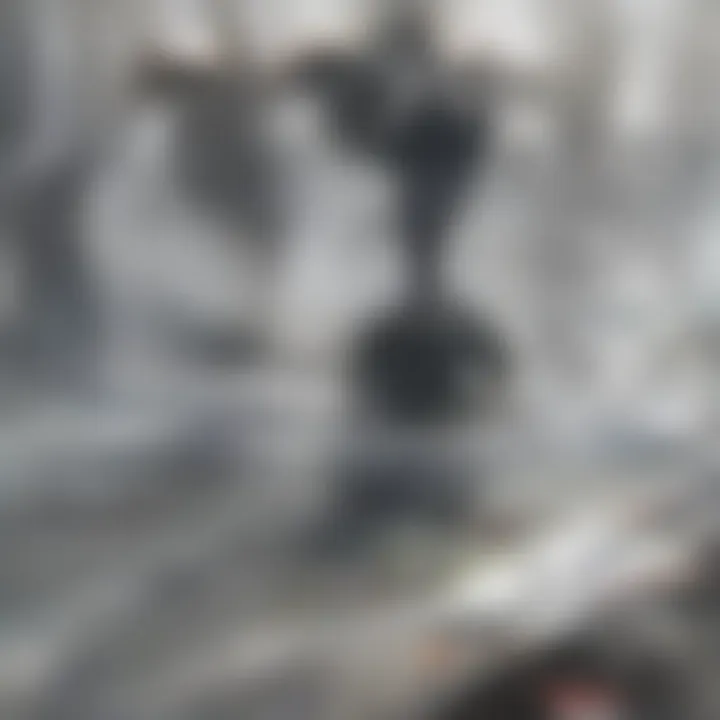
Role of Safety Components
Safety components play a vital role in enhancing the safety of robotic applications. These components are designed to automatically manage and control potential hazards, varying from simple to complex systems. Key safety components include:
- Safety Sensors: Devices such as light curtains and pressure mats can help detect the presence of personnel near robots, stopping operation when necessary.
- Emergency Stop (E-Stop) Buttons: These enable quick shutdown of robotic systems in case of an emergency, providing a critical layer of safety measures.
- Control Systems: Advanced safety control systems ensure that robots operate within designated safety parameters.
Incorporating these safety components is crucial for reducing risks associated with robotics. Not only do they enhance safety, but they also foster compliance with ISO safety standards.
Overall, a comprehensive risk assessment contributes significantly to effective management in robotic applications. By prioritizing safety, organizations create a more secure working environment, facilitating the smooth integration of robotic technologies.
Performance Requirements for Robot Safety
Performance requirements for robot safety are essential in ensuring that robotic systems function safely and effectively in various environments. These requirements outline the safety standards that robots must meet to prevent accidents and ensure the safety of operators and other personnel. This section will delve into the specific elements, benefits, and considerations of performance requirements related to robot safety.
Safety Functionality
Safety functionality refers to the capabilities that robotic systems must possess to operate safely. It encompasses various components, such as emergency stop mechanisms, safety-rated control systems, and fail-safe designs. These features help in minimizing risks associated with robotic operations. For example, a robot equipped with an effective emergency stop feature can quickly halt operations in the event of a malfunction, significantly reducing the risk of injury.
The implementation of safety functionality is not solely about technical compliance. It also plays a critical role in fostering a safety culture within organizations. When operators understand that the robots they work with are designed with comprehensive safety measures, it enhances their confidence in working alongside them. Therefore, investing in robust safety functionality can lead to a more efficient and secure working environment.
Testing and Validation
Testing and validation of robots against performance requirements is a systematic process essential for ensuring compliance with ISO standards. This process involves several steps, including:
- Initial Testing: Conducted during the design phase to identify potential safety issues before the robot is deployed.
- Field Testing: Testing the robot in a controlled environment to simulate real-world conditions and evaluate its performance against the defined safety requirements.
- Regular Maintenance and Re-testing: Continuous evaluation of robot performance and safety measures, ensuring they align with any updates to the ISO standards.
Validation is crucial as it proves that a robotic system performs its intended safety functions effectively. In cases where testing reveals deficiencies, modifications can be made to improve safety. Adhering to rigorous testing and validation processes helps maintain compliance with safety standards and mitigates the risk of accidents.
"In the world of robotics, safety is so important that it should be integrated into the entire lifecycle of the robot, from design to deployment."
Through thorough testing and validation, stakeholders ensure that performance requirements for robot safety are not just met but continually enhanced. Such practices pave the way for safer, more dependable robotic applications in various industries.
Roles of Operators and Manufacturers
Understanding the roles of operators and manufacturers is crucial within the framework of ISO robot safety standards. These roles not only support compliance but also ensure a safer environment in robotic applications. This section breaks down the responsibilities and obligations associated with each party, emphasizing their contributions to overall safety in robotic systems.
Operator Responsibilities
Operators play a pivotal role in the safety of robotic systems. They are the individuals who interact directly with the machines and their environments. The following elements characterize their responsibilities:
- Training and Certification: Operators must undergo proper training to understand the functionalities and limitations of the robot they are working with. This training ensures they are equipped to handle day-to-day operations safely.
- Monitoring and Maintenance: Continuous monitoring of robotic systems is essential. Operators should perform routine checks and maintenance, following predefined schedules, to ensure equipment remains in optimal working condition.
- Awareness of Hazards: Operators must be aware of potential hazards associated with the robotic systems. This includes understanding mechanical risks and knowing safety protocols to mitigate accidents.
- Reporting Incidents: If an incident occurs, operators are responsible for documenting and reporting it to the appropriate channels within the organization. This helps in fine-tuning safety measures and preventing future occurrences.
The effectiveness of operators significantly influences workplace safety. Their proactive engagement with safety practices cannot be overstated.
Manufacturer Obligations
Manufacturers hold substantial responsibilities when it comes to ISO compliance. Their obligations are designed to create a safe environment for operators and reduce risks associated with robotic devices. Key considerations include:
- Design Safety: Manufacturers are responsible for integrating safety features into the design of robots. This could involve fail-safes, emergency stop buttons, and other mechanisms that enhance user safety.
- Compliance with Standards: Manufacturers should ensure that their robots comply with relevant ISO safety standards, such as ISO 10218 and ISO/TS 15066. This compliance not only meets legal requirements but also guarantees that the robots function safely in their intended environments.
- Providing Documentation: Clear and concise documentation should accompany each robotic system. This documentation usually includes operational manuals, maintenance guides, and safety protocols. Good documentation aids operators in understanding and properly using the equipment.
- Ongoing Support and Updates: Manufacturers have an obligation to provide continuous support after sale. This includes software updates and technical support to address any safety concerns that may arise post-deployment.
"Manufacturers have a crucial role in designing robotic systems that prioritize user safety and meet international standards."
By recognizing these obligations, manufacturers contribute to the broader goal of workplace safety in robotics. Ensuring a collaborative environment between operators and manufacturers fortifies the overall commitment to safety standards.
Challenges in Implementing ISO Standards
Implementing ISO robot safety standards poses significant challenges for organizations across various sectors. These challenges must be acknowledged to develop effective strategies that ensure compliance and safety. Among the key areas of concern are adaptation to new technologies and the costs associated with maintaining compliance. Understanding these challenges is essential for businesses that wish to fully integrate robotics into their operations without compromising safety standards.
Adaptation to New Technologies
The robotics field is evolving at an unprecedented pace. As new technologies emerge, the existing ISO standards must be adapted to accommodate them. This process involves a comprehensive review of the standards and possibly their revision.
Organizations face several hurdles during this adaptation. Firstly, the new technologies can introduce unforeseen risks that current standards do not adequately address. Companies must invest in research and development to identify and evaluate these risks. Furthermore, maintaining consistency with the ISO standards while integrating innovative solutions becomes a balancing act. It requires an active dialogue between developers, industry experts, and standard organizations.
Additionally, the introduction of advanced technologies such as artificial intelligence and machine learning complicates compliance. These technologies not only enhance robot capabilities, but they also increase operational complexities. They demand higher levels of safety and performance specifications. The ability to quickly access updated standards plays a crucial role in facilitating smooth transitions to new technological landscapes.
Cost of Compliance
Compliance with ISO standards often comes with significant financial implications. The cost of implementing these standards can be daunting, especially for small and medium enterprises.
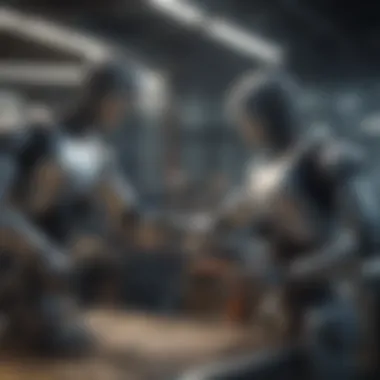
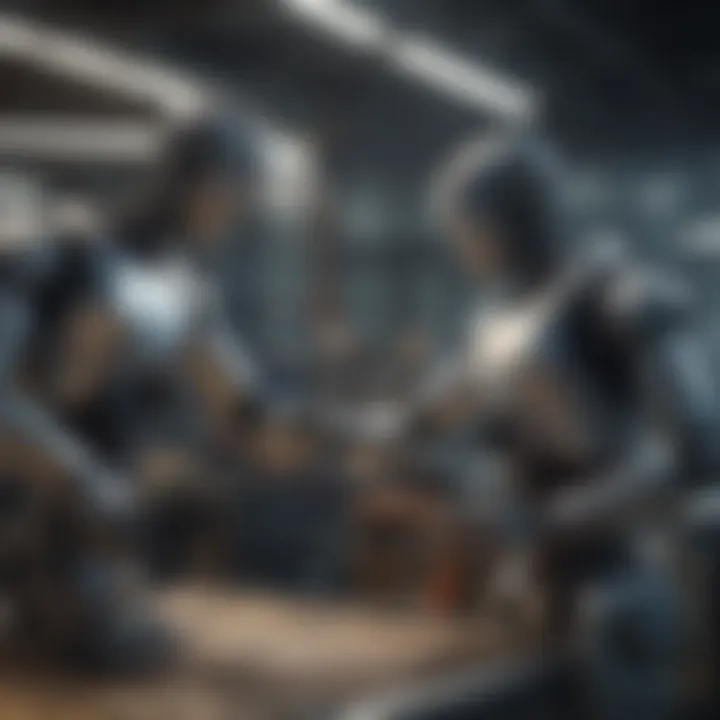
Organizations must allocate funds for various aspects of compliance, including:
- Training personnel to understand and adhere to safety standards.
- Upgrading equipment and systems to meet safety requirements.
- Conducting regular audits to ensure ongoing compliance and identifying potential issues early.
Additionally, bureaucratic hurdles can complicate the compliance process and lead to increased costs. Variances in regional regulations may necessitate different approaches to compliance, which can drain resources and time. Companies must also prepare for the possible economic impact of fines and penalties for non-compliance, which can be significant.
"Investing in compliance is not just a regulatory obligation; it represents a commitment to operational excellence and safety."
Acknowledging the financial burden linked to compliance can enable organizations to plan budgets more effectively. Seeking external guidance and support can also ease the load, particularly for those who may lack in-house expertise. Working together with consultants or industry associations can provide valuable insights into optimizing costs associated with compliance, making it more manageable.
Future of ISO Robot Safety Standards
As technology progresses, the future of ISO robot safety standards becomes an essential aspect of ensuring safety in increasingly complex robotic environments. The ongoing developments in robotics, including automation and artificial intelligence, necessitate a vigilant approach to safety standards. This section will explore the upcoming trends, revisions, and updates that shape the landscape of ISO standards in robotics.
Emerging Trends in Robotics
Recent advancements in robotics have introduced a variety of trends that will influence ISO safety standards moving forward. One significant trend is the rise of collaborative robots, or cobots. These robots are designed to work alongside human operators in shared spaces. As cobots become more prevalent across sectors, their integration into safety standards is vital. Companies like Universal Robots and Rethink Robotics are at the forefront of this movement.
An increased focus on adaptability is also emerging. Robots are no longer restricted to rigid environments; they are being deployed in unpredictable surroundings. This adaptability demands that ISO standards accommodate varying operation conditions. For instance, manufacturers must now consider safety measures when robots perform tasks that involve significant interaction with different tools or environments.
Furthermore, the integration of machine learning into robotics is a noteworthy trend. Robots equipped with advanced algorithms can analyze and learn from their environments, improving their functionality and efficiency. However, this raises new safety concerns that ISO standards must address. If a robot makes autonomous decisions based on learned data, how can its safety be ensured? Thus, safety standards must evolve alongside technological advancements to mitigate potential risks.
Ongoing Revisions and Updates
ISO standards are not static; they require periodic revisions to keep pace with innovative developments and emerging safety challenges. The process of updating these standards is continuous and involves collaboration among industry experts, manufacturers, and regulatory bodies. The goal of these revisions is to enhance the clarity and applicability of safety standards, ensuring they remain relevant in dynamic environments.
Effective revisions include feedback mechanisms for stakeholders to contribute their experiences and insights. This could be from industries that apply robots, as they often face real-world challenges that the standards might not fully address. Engaging these parties strengthens the robustness of safety standards.
Additionally, international collaboration plays a significant role in the updates of ISO standards. With robotics increasingly becoming a global endeavor, aligning safety regulations across different countries is essential. This alignment helps in maintaining consistent safety measures while avoiding conflicts in compliance responsibilities.
"ISO standards must adapt to the dynamic landscape of robotics to ensure safe interactions and operations, keeping human safety at the forefront while fostering innovation."
Case Studies on ISO Compliance
Case studies on ISO compliance offer practical insights into how these standards translate into real-world applications. They are essential in highlighting the impact of ISO robot safety standards on organizational processes and employee safety. By examining specific scenarios, stakeholders gain a clearer understanding of both the challenges and successes that accompany the implementation of these standards.
Moreover, case studies provide valuable information for educating industry players on best practices. Organizations can learn about the consequences of compliance and the potential risks of neglecting these important standards. Ultimately, such a focused approach enhances internal safety protocols and encourages continual improvement.
Industrial Applications
In various sectors, especially manufacturing and logistics, industrial applications have shown significant results through adherence to ISO safety standards. For instance, many automotive manufacturing plants have integrated ISO 10218, enhancing robot safety during assembly processes. This has led to reduced workplace injuries and optimized workflow.
Real-world examples indicate that compliance not only meets legal requirements but also improves overall productivity. Here are some specific elements relating to industrial applications:
- Employee Safety: Studies found reduced accident rates after implementing ISO standards.
- Efficiency Gains: Streamlined operations were observed when robots operated within a safer framework.
- Cost-Effectiveness: Initially costly compliance measures yielded substantial long-term savings through decreased injury claims and operational downtimes.
Collaborative Robots in Practice
The rise of collaborative robots, or cobots, signals a new era in robotic applications. These are designed to work alongside human operators, making ISO/TS 15066 especially relevant. Implementing this standard ensures that cobots can operate safely in shared environments, mitigating risks involved in direct human-robot interactions.
Case studies have revealed various positive outcomes from the deployment of collaborative robots, including:
- Increased Flexibility: Businesses adapted more easily to production changes due to the versatile nature of cobots.
- Enhanced Workforce Morale: Employees reported greater satisfaction when working alongside machines that prioritize safety.
- Easier Integration: Companies successfully integrated cobots into existing lines due to clear safety guidelines.
"Understanding how ISO standards affect the workplace is crucial for innovation and safety in robotics."
By assessing these case studies, organizations can glean important lessons about effective implementation strategies. Compliance with ISO standards and clear documentation creates a framework for future advancements and optimizations in safety technologies.
Ending
The conclusion serves as a critical component in this exploration of ISO robot safety standards. It encapsulates the primary topics addressed throughout the article and underscores the significance of adherence to these standards in various industries. The safety of robotic systems is paramount, given the potential risks associated with their operation. By understanding the importance of these standards, stakeholders can foster safer work environments and improve operational efficiency.
Recap of Key Insights
In this article, several key insights emerged:
- ISO standards define safety norms: The establishment of ISO 10218 and ISO/TS 15066 elucidates the essential safety requirements for robots and collaborative robotic environments. These standards ensure that both robots and their human counterparts can operate safely.
- Compliance matters: Meeting ISO standards is crucial not only from a legal perspective but also for maintaining competitive advantage within the industry. Companies that comply with these standards demonstrate their commitment to safety and quality, thereby enhancing their brand image.
- Risk assessment is a proactive measure: Identifying hazards and implementing risk reduction strategies is an ongoing necessity. The integration of safety components is vital to achieve the required safety functionalities.
- Operator and manufacturer roles: Operators hold significant responsibilities in adhering to safety protocols, while manufacturers play a pivotal role in ensuring their equipment meets established safety standards.
The Path Forward for Robotics Safety
Looking ahead, the journey towards enhanced robotics safety is marked by evolving challenges and opportunities. Several factors play a role:
- Technological advancements: As robotics technology progresses, new safety standards will need adaptation. This will require collaboration among industry stakeholders to address emerging risks.
- Continuous updates and revisions: The dynamic nature of the robotics field necessitates ongoing revisions to existing standards. Stakeholders must stay informed and be prepared to implement changes that enhance safety measures.
- Training and education: Ensuring that operators and manufacturers are well-versed in safety standards will be crucial. Education initiatives can ensure that everyone involved is aware of their responsibilities and the latest safety protocols.
"Effective compliance with ISO robot safety standards not only minimizes risks but fosters innovation in robotic technologies."
In summary, the future of ISO robot safety standards is not just about adhering to regulations but about fostering a culture where safety is embedded in the very fabric of technological advancement.