Milling Foam: Techniques and Innovations in Manufacturing
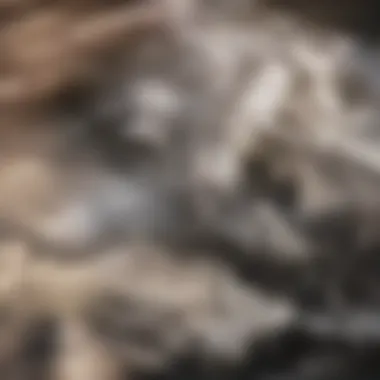
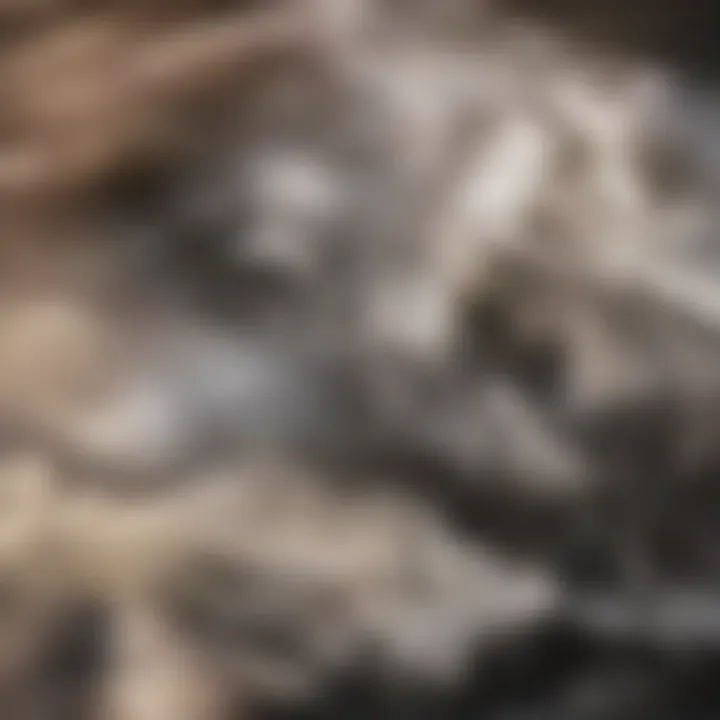
Intro
Milling foam is a process that has gained importance in various manufacturing sectors. The precision and versatility of this technique cater to different applications across industries such as automotive, aerospace, and architecture. This article focuses on the nuanced aspects of foam milling, exploring the techniques utilized, the types of foams involved, and the innovative applications resulting from this manufacturing method.
Understanding the principles behind foam milling allows for greater insights into its efficiency and effectiveness in producing high-quality components. From basic operations to advanced technologies, the topic is rich with potential for enhancement in product design and development.
Research Context
Background Information
The milling of foam involves removing material from a larger foam block or sheet to achieve desired shapes and sizes. Common types of foam processed include polyurethane, polystyrene, and polyethylene, each with characteristics suited for specific applications. As industries evolve, the demand for customized solutions has spurred innovations in foam milling techniques.
Importance of the Study
Investigating foam milling is essential for multiple reasons. It drives innovation in product development, significantly contributes to design flexibility, and reduces material waste. Enhancing our understanding of foam milling techniques will allow industries to adopt more efficient processes that can lead to cost savings and improved product outcomes.
Discussion
Interpretation of Results
The advancements in milling technology have shown impressive results, particularly in terms of accuracy and speed. Modern equipment enables precise cuts that minimize waste, thereby increasing overall efficiency. Comparison of traditional milling methods with contemporary technologies reveals a shift toward automation, which improves consistency and reduces human error in production.
Comparison with Previous Research
Research in the field of foam milling has expanded significantly over recent years. Earlier studies focused primarily on the mechanical properties of foams and their response to milling. However, recent research has placed greater emphasis on optimizing milling conditions, examining factors such as feed rate, cutting speed, and tool selection. This evolution signifies a deeper understanding of how these parameters can be manipulated to enhance performance.
"Milling foam processes are critical in defining the quality and effectiveness of produced components, influencing both performance and material sustainability."
Through an in-depth analysis of techniques, machinery, and material types, it becomes evident that the future of foam milling is bright. Industries harnessing these innovations are likely to see expansive growth in their capabilities and product offerings.
Prelude to Milling Foam
Milling foam has gained importance in various manufacturing sectors, as it enables the transformation of lightweight materials into precise components. Understanding milling foam means grasping its role in enhancing product development, engineering design, and contributing to various industries. This process facilitates creative innovations while addressing practical requirements.
Definition and Significance
Milling foam refers to the intricate technique of shaping foam materials through milling machinery. This process encompasses various types of foams, including polyurethane and polystyrene. The significance of milling foam lies in its ability to produce tailored shapes and sizes that meet specific design needs. Moreover, it allows for high precision, resulting in components that fit seamlessly into larger systems.
The machining of foam offers distinct advantages. It reduces waste, allows for faster production cycles, and provides adequate versatility across multiple applications. Understanding these benefits is essential for engineers, designers, and manufacturers aiming to optimize their production processes.
Historical Context
Historically, milling was primarily associated with traditional materials like wood and metal. However, the evolution of foam materials in the late 20th century encountered a need for efficient processing methods. With the rise of industries demanding customized foam components, milling techniques adapted to accommodate these new materials.
As the technology progressed, innovative milling machines were developed to handle various foam densities and types. Today, milling foam is a recognized practice that plays a crucial role in sectors such as automotive, aerospace, and consumer products. Understanding this historical context helps professionals appreciate the advancements made, as well as the ongoing innovations within foam milling technology.
Types of Foam Suitable for Milling
The significance of understanding the types of foam suitable for milling cannot be overstated. Different foams possess unique properties that affect their machinability and end applications. Choosing the correct foam can enhance product quality and reduce waste, leading to operational efficiency. Additionally, foam types like polyurethane, polystyrene, and expanded polypropylene each have distinct characteristics that cater to specific industry needs, from automotive to consumer goods.
Polyurethane Foam
Polyurethane foam is widely recognized for its versatility and resilience. It is commonly used in applications requiring cushioning and insulation. This foam type is made by reacting diisocyanates with polyols, resulting in a richly versatile material that can vary in density. One of the primary advantages of polyurethane foam in milling is its ability to retain shape while undergoing considerable mechanical processing.
Its adaptability makes it suitable for products ranging from mattresses to automotive seats. However, working with polyurethane requires precision, as it can generate dust during milling, which may pose inhalation risks and affect the workspace environment. Proper safety precautions and dust control measures should be in place when milling this foam type.
Polystyrene Foam
Polystyrene foam is often used in packaging, insulation, and craft applications. It is lightweight and has good thermal insulating properties. This foam is typically more rigid than polyurethane, offering different advantages in terms of milling. Polystyrene can be easily shaped and cut, making it ideal for intricate designs and custom applications.
Its closed-cell structure helps it maintain shape, but it can also shatter if excessive force is applied during milling. Thus, a well-planned milling strategy is critical to optimizing material yield and achieving desired design specifications.
Companies employ it extensively in the manufacturing of containers, safe packaging for fragile items, and insulation panels. The ease of processing polystyrene makes it a favored choice in many industries, although there are considerations related to environmental impact due to its non-biodegradable nature.
Expanded Polypropylene
Expanded polypropylene foam, often abbreviated as EPP, has started to gain traction in various sectors. It is notable for its excellent impact resistance and low weight. EPP is also chemically resistant and can handle stress without permanent deformation, which makes it a prime candidate for automotive applications where durability is a priority.
The milling process for expanded polypropylene requires careful consideration of cutting speeds and tool selection, as its structure can lead to uneven surfaces if not properly managed. This material is recyclable, thus supporting sustainability goals in manufacturing. Additionally, its foam structure allows for effective cushioning and protection, making it ideal for packaging sensitive equipment.
The Milling Process Explained
The milling process is a pivotal aspect in the manufacturing of foam products. Understanding this process is crucial as it enhances the quality, dimensional accuracy, and overall performance of the final product. Milling serves various industries, from automotive to aerospace, where precision and consistency are paramount. By examining the milling process, one can appreciate its multifaceted nature and its impact on production efficiency.
Preparation of Foam Material
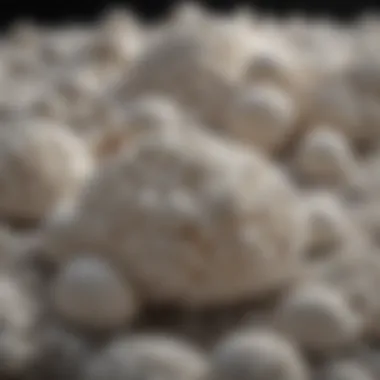
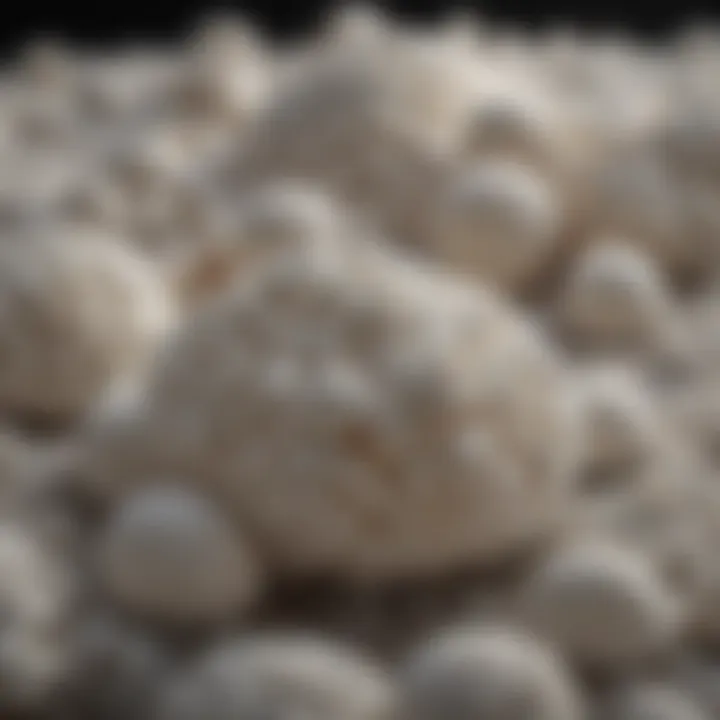
Preparation is the first step in the milling process. The desired quality and characteristics of the final product hinge significantly on how the foam material is prepared. This involves selecting the correct type of foam and ensuring it has uniform density and moisture content.
Before milling, foam is usually cut into manageable sizes to fit the machine. This reduces handling issues and minimizes waste during the milling process. Properly preparing the foam material helps in achieving smoother finishes and deeper cuts.
Milling Techniques Overview
Milling techniques vary, and understanding these differences is essential for selecting the appropriate method for specific applications. The three primary techniques are dry milling, wet milling, and high-pressure milling.
Dry Milling
Dry milling is a widely used technique characterized by the absence of any liquid coolant. One key aspect of dry milling is its efficiency in terms of processing speed. This method is popular because it reduces contamination risk. The unique feature of dry milling is that it generates less heat compared to other methods, helping to maintain the integrity of foam materials.
Advantages:
- Less contamination risk
- Minimal heat generation
- Faster operation due to no coolant processes
Disadvantages:
- Can produce dust which requires careful handling
Wet Milling
Wet milling employs liquid coolant to enhance the milling process. This technique is particularly effective in reducing the friction generated during processing, which helps to extend tool life. The main characteristic of wet milling is its ability to improve surface finishes, making it a beneficial choice for applications where aesthetics and smoothness are prioritized.
Advantages:
- Enhances surface smoothness
- Reduces tooling wear
- Helps in cooling during milling process.
Disadvantages:
- Requires additional cleaning and maintenance
- Potential for contamination from the coolant
High-Pressure Milling
High-pressure milling is another advanced technique that relies on applying increased pressure to cut foam. This method is particularly advantageous for producing intricate designs and achieving high precision in the finished product. Its key characteristic lies in the intense pressure used, which results in clearer cut edges.
Advantages:
- Produces highly detailed cuts
- Reduces overall milling time for complex shapes
- Improved dimensional accuracy
Disadvantages:
- Higher equipment costs
- May introduce more wear and tear on equipment
Understanding these milling techniques allows manufacturers to choose the most suitable method based on their requirements and desired outcomes.
Machinery Used in Foam Milling
The machinery used in foam milling is critical to achieving precise and effective results. Milled foam serves various purposes across several industries, making it essential to understand the equipment that performs this task. The right machinery not only enhances product quality but also influences efficiency, production speed, and overall manufacturing costs. Choice of machinery affects the processing of different foam types and can significantly impact the end products’ characteristics.
Two main categories of machinery stand out when discussing foam milling: CNC milling machines and traditional vertical and horizontal mills. Each type has its advantages and is suited for particular tasks.
CNC Milling Machines
CNC milling machines represent a significant leap in foam machining technology. The acronym "CNC" stands for Computer Numerically Controlled. This machinery allows for precise control of milling processes through computer programming. The main aspects of CNC milling machines include:
- Precision: The technology offers high precision, making it possible to cut foam to specific dimensions repeatedly without errors.
- Automation: CNC milling machines perform tasks automatically, significantly reducing the time and labor required compared to manual methods.
- Versatility: They can handle various types of foam materials, adapting to different milling techniques as needed.
The programming behind CNC machines facilitates complex designs and shapes, which are ever more important in industries demanding customized foam products, such as automotive or aerospace. The integration of advanced software enhances the operator's ability to modify designs swiftly, allowing for flexibility in production. Furthermore, the consistency in quality provided by CNC machines makes them essential in maintaining standards in manufacturing.
Vertical and Horizontal Mills
Vertical and horizontal mills form the traditional backbone of foam milling processes. Understanding the differences can help choose the right milling solution for specific needs.
- Vertical Mills: In these machines, the cutting tool moves vertically, which is optimal for creating intricate shapes and finishes. This type of milling allows for excellent visibility of the workspace and quick adjustments during operations. They are often preferred for smaller jobs where design intricacy is a priority.
- Horizontal Mills: In contrast, horizontal mills use a cutting tool that operates parallel to the ground. This type allows for higher material removal rates, making it more suitable for larger foam blocks or materials that require substantial cutting. They are also effective in handling heavier workpieces due to their stable designs.
When deciding between vertical and horizontal mills, consider the specific requirements of the foam product being produced. For tasks that require more complexity and detail, vertical milling may be the best choice. Conversely, horizontal milling might be more efficient for larger-scale operations focusing on speed and material efficiency.
"The choice of milling machinery can make or break the production process in foam milling, influencing both quality and cost-efficiency in manufacturing."
Parameters Influencing Milling Efficiency
The efficiency of milling foam significantly depends on several critical parameters. Understanding these elements enhances the quality of the milling process and maximizes productivity. Such parameters include cutting speed, feed rate, and tool selection. The right balance of these factors can lead to improved outcomes, reduced waste, and cost-effectiveness. Many professionals and companies must consider these variables to achieve optimum results in foam milling.
Cutting Speed
Cutting speed refers to the speed at which the cutting tool moves through the foam material. This parameter is crucial as it directly affects the quality of the milled product and the efficiency of the operation. High cutting speeds can lead to faster operations, but they also increase the risk of generating excessive heat. This heat can cause foam to deform, resulting in low-quality output. Therefore, finding an ideal cutting speed is vital.
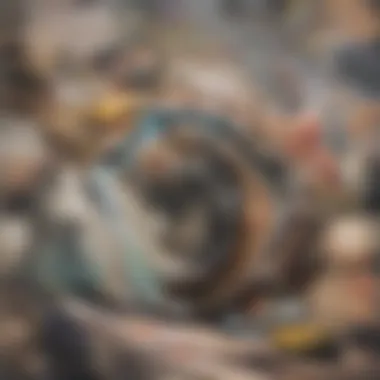
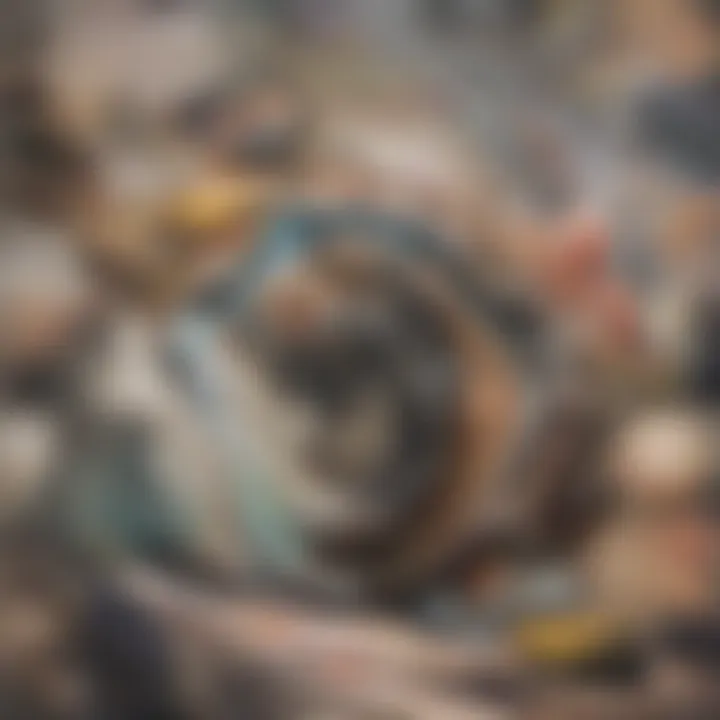
When determining the right cutting speed, manufacturers must account for the specific type of foam being milled. For instance, polyurethane foam may require different speeds compared to polystyrene foam. By adjusting the cutting speed according to foam type, manufacturers can maintain precision while optimizing production time.
Feed Rate
Feed rate is another important factor in milling efficiency. It defines how quickly the material is fed into the milling machine. An inappropriate feed rate can compromise the milling process. Too slow a feed rate results in prolonged contact between the tool and foam, leading to overheating. Conversely, a too-fast feed rate may lead to compromised cutting quality and finish.
Setting the correct feed rate involves evaluating the material's properties and the intended application of the milled foam. This consideration is crucial for industries like automotive and aerospace, where quality and precision are paramount. Balancing feed rate with cutting speed ensures that the material is processed optimally, thus enhancing overall performance.
Tool Selection
The choice of tool is fundamental in the foam milling process. Different tools come with varying geometries and materials, each suited for specific milling applications. Selecting the appropriate tool can lead to efficient cutting and high-quality results.
One must consider factors like tool diameter, shape, and material when choosing tools. A tool that is too blunt or inappropriate for the foam type can lead to increased wear and less effective milling. Mastery of tool selection becomes particularly relevant in high-volume production environments.
"Proper cutting speed, optimal feed rate, and suitable tool selection are the three pillars of effective milling efficiency in foam processing."
Applications of Milled Foam
The applications of milled foam are diverse and critical across various industries. Understanding these applications provides valuable insights into the potential benefits and considerations of using milled foam in manufacturing and design. The versatility of milled foam lies in its ability to be shaped, customized, and integrated into a wide array of products and processes. The significance of effectively milling foam cannot be overstated.
Key elements to consider include:
- Cost efficiency: Milled foam can reduce production costs due to its lightweight nature.
- Customization: Foam can be easily shaped to meet specific product design requirements.
- Performance: Proper milling enhances the foam's structural properties, leading to improved end-product resilience.
Each application area demonstrates unique advantages and challenges that industries must navigate when integrating milled foam into their operations.
Automotive Industry
In the automotive sector, milled foam plays a crucial role in enhancing comfort, safety, and sound insulation. Car manufacturers utilize milled foam in various components such as seat cushions, interior panels, and sound-deadening materials. The advantages of using milled foam in automotive applications include its lightweight properties, which contribute to improved fuel efficiency and performance.
Moreover, milled foam can absorb shocks and vibrations, providing a more comfortable ride for passengers. It also allows for easy customization, fitting different vehicle designs and consumer preferences. However, manufacturers must consider factors like durability and burn resistance when selecting foam materials for automotive use.
Aerospace Applications
The aerospace industry demands high performance and reliability from all materials, including foam. Milled foam is used in several components of aircraft, such as interior linings, seat cushions, and thermal insulation. Its lightweight nature is essential for reducing the overall weight of aircraft, contributing to fuel efficiency while ensuring high safety standards.
Furthermore, milled foam can be engineered to provide fire resistance, which is a crucial consideration in aviation. The use of specialized milling techniques allows for precision and uniformity in the components, ensuring they meet strict regulatory and safety standards. Challenges include the need for rigorous testing and validation processes to ensure that the milled foam performs as required under extreme conditions.
Consumer Products
In the realm of consumer products, milled foam is instrumental in producing items ranging from appliances to furniture. Many household goods, like mattresses and cushions, employ milled foam for comfort and support. The ability to customize foam density, firmness, and shape allows manufacturers to cater to the diverse needs of consumers.
Additionally, milled foam is used in electronics packaging, where it provides superior protection for fragile items during shipping. However, the environmental impact of foam production and disposal is a significant consideration for manufacturers producing consumer goods. Engaging in sustainable practices and exploring recycling options can mitigate these concerns and further enhance the appeal of foam in the consumer market.
"Understanding the applications of milled foam offers invaluable insights into its importance across several industries. By focusing on functionality, customization, and innovation, manufacturers can leverage this material effectively to meet modern product demands."
Environmental Considerations
The milling of foam incorporates significant environmental considerations that must be addressed. The focus here is not only on production efficiency but also on minimizing ecological impact. As industries become more aware of sustainability, processes that involve foam must adapt to these expectations. Key elements include recycling strategies, waste reduction, and resource efficiency.
Recycling of Foam Materials
Recycling foam materials presents a viable path for environmentally conscious milling practices. Many types of foam, such as polyurethane and polystyrene, can be recycled, providing an opportunity to repurpose materials that would otherwise contribute to landfill waste. The recycling process generally involves collecting scrap foam, shredding it into small pieces, and then reconstituting it into new products. This mitigates the need for virgin material and reduces overall environmental footprint.
Moreover, recycling can significantly lower costs associated with material sourcing. Companies can obtain recycled materials at a fraction of the price of new ones. This becomes crucial as market demands evolve towards sustainable options, pushing businesses to integrate green practices into their operations. Understanding local recycling capabilities and regulations is essential for optimizing this process.
"The path to sustainable foam milling involves not just innovation in machinery but also a commitment to recycling the materials we use."
Sustainability Practices in Milling
Implementing sustainability practices in milling is key to reducing negative environmental impacts. This includes energy-efficient machinery, optimization of cutting processes, and the use of biodegradable lubricants. By focusing on energy consumption, facilities can adopt CNC milling machines that are designed to operate with lower energy use, thus reducing the carbon emissions associated with foam processing.
Minimizing waste during the milling process is also essential. This can involve strategies such as accurate measurements and advanced cutting technology that reduces excess scrap. Furthermore, organizations can train staff on best practices to ensure they are aware of how their actions impact the environment.
Challenges in Foam Milling
The milling of foam presents unique challenges that must be addressed to ensure efficiency and quality in the final products. These challenges stem primarily from the characteristics of foam materials and the machinery utilized in the milling process. Understanding these challenges is essential for manufacturers aiming to optimize their operations and achieve the desired end product.
Material Variability
Foams differ significantly in density, elasticity, and chemical composition. This material variability can lead to inconsistent milling outcomes. For instance, polyurethane foam behaves differently than polystyrene foam due to its varying hardness and resilience. When milling these materials, operators must adjust parameters such as cutting speed and tool selection accordingly.
In some cases, irregularities within the foam itself can create further complications. Foams often have inhomogeneous structures, which may cause uneven cutting and lead to excessive tool wear. Hence, manufacturers must conduct thorough material testing prior to milling. This requires investing time and resources in understanding the specific properties of the foam being processed.
Moreover, maintaining quality control throughout the milling process can be challenging. Operators may need to implement quality assurance protocols to identify defects and manage inconsistencies as they arise.
Machinery Limitations
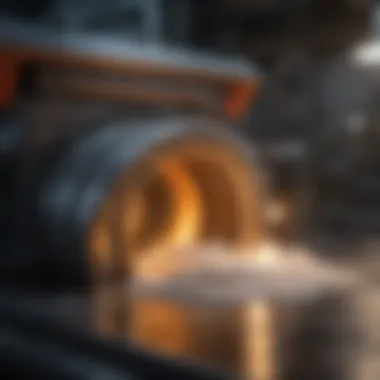
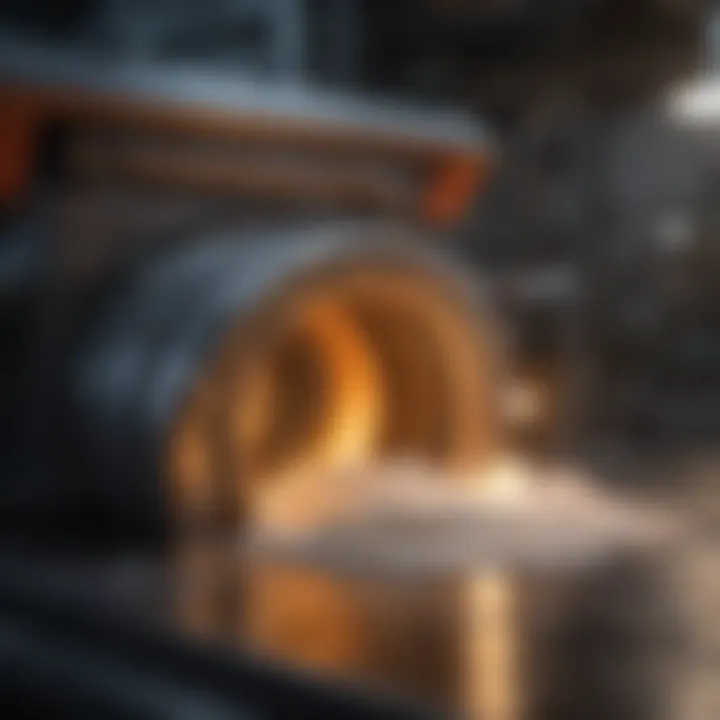
The efficiency of foam milling highly depends on the machinery used. Standard milling machines may not be ideally suited for foam materials. For example, a CNC milling machine designed for hard metals might struggle with softer foams, leading to poor cutting performance and subpar results.
In addition, cutting tools must be selected based on the specific foam type. The wrong choice of tools can lead to several problems including overheating, rapid tool degradation, and inconsistent surface finishes. Manufacturers face the challenge of finding specialized tools that can effectively handle various foams.
Another consideration is the limits of current technology. While advancements have been made in foam milling methods, some machinery still lacks the precision and adaptability required for complex geometries. Manufacturers looking to mill intricate designs may need to invest in more advanced systems, which can represent a significant cost.
As milling technology develops, businesses must remain vigilant and explore innovations that can mitigate these challenges.
Addressing the limitations of machinery involves continuous research and adaptation to new techniques. Staying attuned to the latest advancements in foam milling technology is crucial for improving processes and outcomes.
Overall, recognizing these challenges in foam milling can aid manufacturers in strategizing solutions and enhancing their operations.
Innovations in Foam Milling Technology
Innovations in foam milling technology play a pivotal role in enhancing efficiency and precision in manufacturing processes. With the continuous evolution of machinery and techniques, industries are improving the quality of products and reducing operational costs. These advancements not only propel productivity forward but also lead to better resource management, thus ensuring environmental sustainability.
One key element of innovation is the development of advanced tools and systems that facilitate precision milling. Efficient milling reduces waste, improves shape retention, and enhances the mechanical properties of milled products. As industries are increasingly focused on efficiency and effectiveness, understanding and adopting these innovations becomes essential.
Innovative technologies help streamline production processes, leading to better quality and reduced waste in foam milling.
Advanced CNC Technology
Advanced CNC (Computer Numerical Control) technology has revolutionized the foam milling landscape. Modern CNC systems offer enhanced capabilities, allowing for complex geometries and intricate designs to be milled with utmost precision. They provide operators with the ability to design and execute detailed patterns and shapes that were previously unattainable with traditional milling methods.
Moreover, these CNC machines come with improved software solutions that facilitate better planning and execution of milling processes. High-speed machining is now possible, significantly reducing production time while maintaining the quality of the finished product.
Key benefits of using advanced CNC technology include:
- Precision: The ability to mill foam materials with high accuracy.
- Flexibility: Capacity to adjust designs and parameters rapidly.
- Reduced downtime: Streamlined operations mean less time isn't wasted on tool changes or machine setup.
As a result, companies adopting advanced CNC technology are achieving competitive advantages in terms of both speed and product quality.
Automation in Milling Processes
Automation in milling processes represents another significant innovation. The incorporation of robotics and automated systems reduces reliance on manual labor, leading to increased consistency in product output. Automation enhances the scalabilty of milling operations, as machines can run for extended periods without interruption, ensuring continuous production.
Implementing automation brings several advantages that positively affect efficiency, including:
- Increased output: More work can be done in less time.
- Consistency: Guarantees that every piece milled meets the same standards.
- Safety: Reduces human exposure to potentially hazardous procedures.
Furthermore, automated processes allow for real-time monitoring of operations. This aspect enables quick adjustments and immediate identification of any issues that arise during milling. By employing automation, industries can ensure a smoother workflow and improved overall productivity.
Future Perspectives on Foam Milling
The future of foam milling presents a significant avenue for exploration within the manufacturing landscape. As industries increasingly prioritize efficiency and sustainability, understanding the direction foam milling will take is crucial. Advancements in technology and methodologies promise to redefine processes, making them more adaptable and effective. With the reliance on foam materials in various sectors, including automotive, aerospace, and consumer products, the quest for innovating milling techniques will continue.
There are several specific elements to consider when discussing future perspectives on foam milling:
- Technological Integration: The integration of smart technologies such as IoT and machine learning is expected to enhance operational efficiencies in foam milling. These advancements offer the potential for predictive maintenance, which can minimize machinery downtime and improve production rates.
- Sustainability Initiatives: As sustainability becomes a focal point within manufacturing, innovations will likely prioritize eco-friendliness. This includes not only recycling efforts but also reducing waste and energy consumption associated with milling processes.
- Customization Capabilities: The demand for personalized products is rising. Foam milling must adapt to facilitate custom designs, thus expanding its relevance across industries. This might involve developing equipment capable of more precise cuts and intricate designs.
Market Trends
The market for foam milling is currently influenced by several key trends that project its future trajectory. Some of these trends include:
- Increased Automation: There is a rising trend toward automation that enhances not only efficiency but also reduces human error. Automated milling machines are becoming more commonplace, allowing for consistent output.
- Demand for Lightweight Materials: The aerospace and automotive industries are increasingly focusing on lightweight materials for enhanced fuel efficiency. Milled foam options are gaining attention for their optimal weight-to-strength ratio.
- Evolving Consumer Preferences: Consumers are leaning towards sustainable and innovative products. This shift drives manufacturers to explore the potentials of milled foam in new applications, thereby stimulating market growth.
"The future of foam milling is not just about cutting materials; it encompasses the evolution of tools, techniques, and sustainability initiatives that meet modern demands."
Emerging Research Areas
Research in foam milling is evolving, paving the way for innovations that could transform current practices. Some notable areas of focus include:
- Material Innovations: Ongoing studies into new foam materials could lead to developments that make milling easier and more effective. This could include bio-based foams or composite materials designed specifically for milling.
- Advanced Processing Techniques: Research into new milling techniques, such as ultrasonic milling, could create less waste and improve finishing on foam products. These techniques offer the potential for higher precision in complex designs.
- Integration of AI in Design: The utilization of AI in the design phase could help manufacturers streamline foam milling processes. AI can optimize designs taking into account material properties and milling constraints, reducing both time and cost.
Epilogue
The conclusion of this article serves as an essential synthesis of the various elements explored throughout the discussion on milling foam. It emphasizes the significance of this manufacturing process in both industrial contexts and more specialized applications. By understanding the techniques and advancements associated with foam milling, professionals and researchers can better appreciate its impact on product development and innovation.
In summarizing key points, we recognize that milling foam is not just about simplistically processing materials; it involves intricate methods that contribute to optimizing efficiency and sustainability. Evaluating how different types of foam respond under various milling techniques provides insight into their applications in industries such as automotive and aerospace.
"Foam milling showcases not only the functionality of materials but also the creativity inherent in engineering design."
Moreover, the environmental considerations, alongside the challenges faced, highlight critical areas for improvement. As the demand for sustainable practices increases, understanding these challenges positions researchers and manufacturers to innovate effectively.
Summary of Key Points
- Techniques and Innovations: The advancements in CNC machining and automation techniques drive efficiency in foam milling processes, reflecting the changing landscape of manufacturing.
- Applications and Industries: The versatility of milled foam showcases its utility in diverse sectors, from automotive to consumer goods, broadening its market relevance.
- Environmental Impact: As sustainability becomes more pressing, the recycling of foam and sustainable practices in milling have entered the forefront of industry discussions.
- Challenges to Address: Material variability and the limitations of current machinery are notable barriers that need addressing for better outcomes in foam milling.
Implications for Future Research
Future research in foam milling presents exciting avenues for advancement. There are several areas that warrant deeper exploration:
- Material Science Innovations: Developing new foam materials that optimize milling techniques could yield higher performance in applications.
- Improved Machinery Development: There is a need for machinery that can handle a wider range of foam materials while maintaining precision and efficiency.
- Sustainability Research: Furthering studies into recycling methods and sustainable milling practices can contribute significantly to the industry's environmental goals.
- Technology Integration: Implementing sophisticated software solutions for design and process optimization in milling will likely enhance productivity and product quality.