3D Printing Circuit Boards: Innovations and Uses
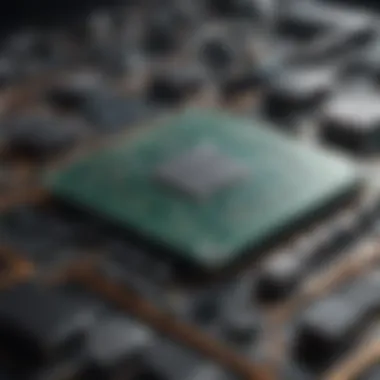
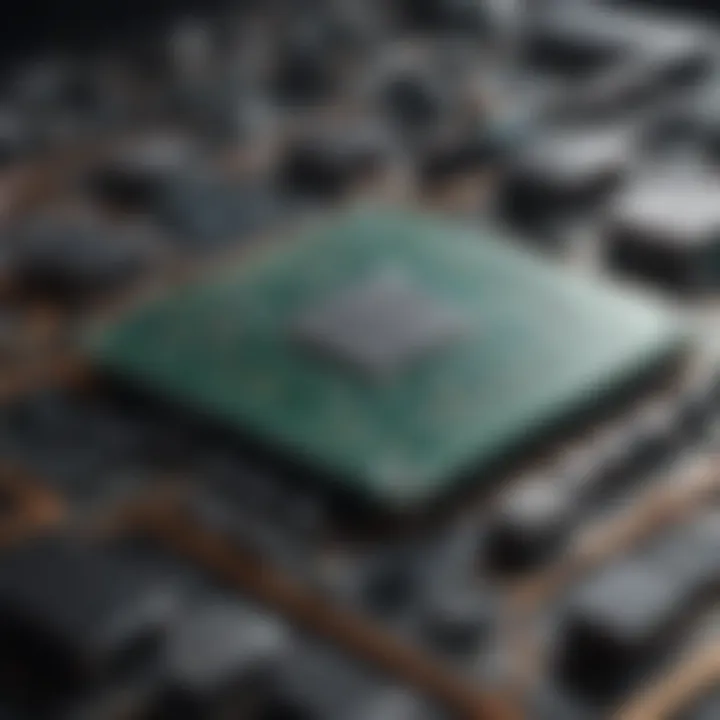
Research Context
Background Information
The field of electronics is in a state of flux, and a key player in this shift is 3D printing technology. Traditionally, the production of circuit boards has relied on subtractive manufacturing processes, which can be both time-consuming and resource-intensive. This has led to a growing interest in alternative methods, primarily 3D printing, which allows for the creation of complex circuit designs directly from digital models. Using various materials, including conductive inks and pastes, manufacturers can layer components and create intricate pathways that were once only a figment of imagination.
Importance of the Study
The significance of this study lies in its potential to revolutionize the electronics landscape. As industries across the boardβbe it healthcare, communications, or automotiveβstrive for faster prototyping and the customization of electronic devices, understanding the implications of 3D printing circuit boards becomes crucial. This exploration not only assesses current methodologies but also evaluates the innovation that pushes boundaries and could make the production process more sustainable. Amidst concerns about waste and resource depletion, this technology holds a promise for minimizing environmental impact while maximizing functional efficiency.
Discussion
Interpretation of Results
3D printing technology is often seen as a beacon of hope for the electronics industry, but it is essential to interpret what the data reveals. Studies suggest that 3D-printed circuit boards can significantly reduce production time and costs. For example, instead of a lengthy process that might involve sourcing materials and assembling components, a designer can input a digital blueprint and have a physical circuit board ready in a fraction of the usual time. This efficiency can lead to increased innovation and faster time to market.
Comparison with Previous Research
Comparative analysis with past research indicates a notable evolution from conventional methods, which typically utilized rigid substrates like FR-4, towards flexible, more adaptive materials. Previously, electronic designs were limited in their complexity, often requiring multiple components to be soldered together after the circuit board's initial fabrication. In contrast, 3D printing paves the way for integrated designs, allowing for the embedding of components directly into the circuit during the printing process.
Adoption has been gradual, and the skepticism lingering in traditional manufacturing sectors highlights a crucial point. While the advancements are impressive, the challenge lies in scaling these methods and ensuring reliability and performance across various applications. Industry experts argue that a more in-depth understanding of material properties and printing techniques could bridge this gap.
In essence, the evolution in 3D printing technologies signals a paradigm shift within the realms of circuit board manufacturing, paving the way for innovation that was once considered unattainable.
As the technology continues to mature, the interplay between artistry and engineering becomes increasingly pronounced. The deeper implications for professionals in electronics, as well as the academic interest it sparks, can serve as a focus for future studies. Greater emphasis on interdisciplinary collaboration between designers, engineers, and researchers can unveil further insights, ensuring that the full potential of 3D printing in electronic applications is realized.
Prelims to 3D Printing in Electronics
The intersection of 3D printing and electronics is not just a trendy buzzword; it signifies a deep and meaningful shift in how circuit boards are manufactured. Traditional circuit board production often involves lengthy timelines, significant waste, and hefty costs. Enter 3D printing, which promises an efficient, flexible, and innovative alternative. By allowing for layer-by-layer assembly, this technology vastly reduces the barriers to entry for prototyping and small production runs, thus empowering inventors and companies alike to bring ideas to fruition quickly.
The Evolution of Circuit Board Manufacturing
Circuit board manufacturing has taken a neat journey over the decades, evolving from labor-intensive processes to automated systems that boast precision. Initially, making circuit boards was an intricate craft, relying heavily on manual labor and requiring a high level of expertise. The introduction of techniques like subtractive manufacturingβwhere material is removed from a substrateβwas a game changer, but it still faced issues like long lead times and poor adaptability for custom designs.
With advancements in digital technology, particularly during the late 20th century, we witnessed the rise of flexible printed circuits and more sophisticated manufacturing techniques such as surface mount technology (SMT). Here's a brief timeline of the evolution:
- 1970s: Emergence of printed circuits, widely used in consumer electronics.
- 1980s: Introduction of SMT which allows for smaller components and denser boards.
- 1990s: Computer-aided design (CAD) tools streamline circuit board design.
- 2000s: Automation takes over, enhancing production speed and accuracy.
- 2010s and beyond: The dawn of 3D printing ignites new possibilities, especially for bespoke designs and rapid prototyping.
This evolution highlights an essential theme: adaptability. As technologies progressed, manufacturers were compelled to integrate disruptive innovations in response to market demands. The marriage of 3D printing and circuit board manufacturing stands as a significant milestone in this journey, offering many benefits, but it also needs to navigate its own set of challenges.
Defining 3D Printing Technology
When discussing the role of 3D printing in electronics, it's crucial to establish what 3D printing is. In simple terms, 3D printing, or additive manufacturing, is a method of creating objects by layering materials based on digital designs. Unlike traditional manufacturing that often removes material, 3D printing builds up a product layer by layer. This process can use various materials, particularly plastics and metals, which can include conductive inks specifically designed for electronics.
Key Characteristics of 3D Printing Include:
- Layer-by-layer construction: Each layer is precisely created based on the design, resulting in intricate structures.
- Customization: Adjustments can be made easily in the digital design phase, resulting in tailored solutions without the need for new tooling.
- Efficiency: Materials are used more precisely, leading to less waste compared to traditional subtractive methods.
- Accessibility: With desktop 3D printers becoming more common, even smaller organizations can prototype effectively.
"3D printing technology can be a significant enabler of creativity and innovation, especially in fields like electronics where customization and rapid iteration are critical."
To sum it up, the rise of 3D printing in electronics is reshaping how circuit boards are conceived and produced. From enhancing the potential for custom designs to streamlining production times, it opens the door for countless new applications. Understanding this technology's fundamentals sets the stage for exploring further advancements and applications in the field.
Core Technologies in 3D Printing Circuit Boards
The realm of circuit board manufacturing is undergoing a renaissance driven by the integration of core technologies in 3D printing. These innovations not only redefine manufacturing processes but also empower designers and engineers to create highly complex structures that were previously inconceivable. Understanding these technologies is crucial as they dictate the flexibility, scalability, and ultimately the cost-effectiveness of the circuit boards produced.
Additive Manufacturing Techniques
Additive manufacturing techniques encompass various methodologies, where material is added layer by layer to build up the desired circuit board. This approach stands in stark contrast to traditional methods where materials are subtracted from a solid block.
- Screen Printing: One prevalent additive technique is screen printing of conductive inks. It allows for efficient application of metal pastes onto substrates, creating conductive traces that are essential for circuit functionality. The accuracy of this method has improved markedly, enabling high-resolution prints that rival traditional fabrication.
- Direct Ink Writing (DIW): Another noteworthy technique is Direct Ink Writing, where a nozzle extrudes conductive inks in precise patterns. This method opens doors to complex geometries, making it versatile for creating circuitry that conforms to unique shapes, which is particularly beneficial in medical devices or wearable technology.
- Fused Deposition Modeling (FDM): Some manufacturers are even adopting FDM in conjunction with conductive filaments. This combination allows them to print entire boards, integrating both the structural and electrical components in one go, which heralds a significant shift in the assembly process.
Ultimately, additive manufacturing techniques democratize circuit design by allowing customization and rapid prototyping. For engineers pressed for time, the ability to iterate designs rapidly is a game-changer, providing the agility needed to keep up with fast-evolving tech demands.
Subtractive vs. Additive Processes
When discussing the core technologies in 3D printing circuit boards, one cannot ignore the contrast between subtractive and additive processes. Each has its own advantages and limitations, and understanding these helps in selecting the right method according to specific project requirements.
Additive Processes:
- As mentioned before, additive methods build up layers, which not only minimizes waste but also allows intricate designs that traditional methods simply cannot achieve.
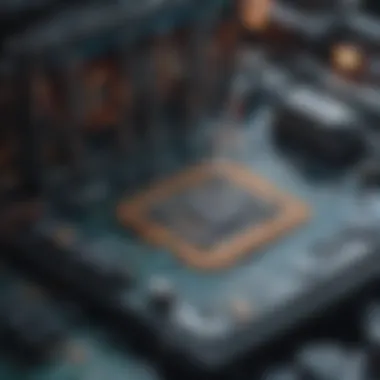
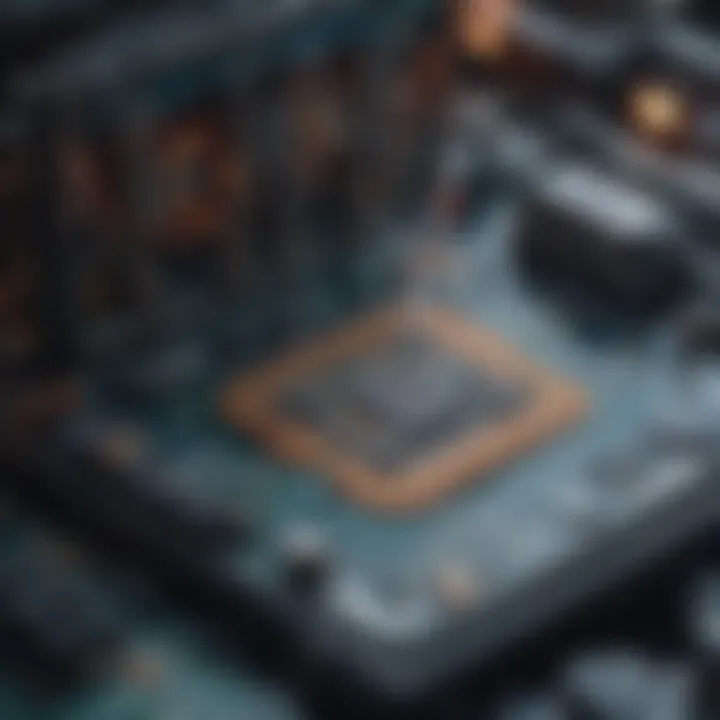
- More flexibility in design changes without the need for new tooling.
- Lower material waste, directly addressing modern sustainability concerns.
Subtractive Processes:
- Conversely, subtractive techniques involve cutting away material from a bulk piece; this has been the industry standard for a long time.
- Typically offers higher precision for certain applications, though at the cost of increased waste.
- Established methodologies have a wealth of knowledge and resources backing them.
In summary, while subtractive processes dominate in the landscape of established manufacturing practices, additive technologies are carving out significant niches due to their customization potential and efficiency. Familiarity with both methods enables firms to select an approach that aligns best with their production goals and market demands.
The ongoing dialogue between additive and subtractive approaches will undoubtedly continue to shape the future of circuit board manufacturing, as each technology informs and influences improvements in the other.
Materials Used in 3D Printed Circuit Boards
The significance of materials in the realm of 3D printed circuit boards cannot be overstated. As the backbone of the entire structure, the choice of materials directly influences conductivity, durability, flexibility, and overall performance. This section delves into the specific types of materials that are at play, detailing their roles and impacts on the efficiency of 3D printing technology within electronic manufacturing.
Conductive Inks and Pastes
One of the most compelling advancements in the production of printed circuit boards is the use of conductive inks and pastes. These substances serve as the lifeline for creating electrical pathways on a PCB, allowing for effective signal transmission. Typically, these inks are based on silver or copper particles suspended in a polymer matrix.
The advantages of utilizing conductive inks include:
- Flexibility: Unlike traditional copper layers, printed conductive inks can branch and curve, which is essential in applications where space is constrained.
- Lower Temperature: The printing process often requires lower thermal profiles compared to traditional methods, which opens doors for heat-sensitive substrates.
- Eco-friendliness: Many of these inks are formulated to be less harmful than conventional materials, paving the way for greener practices.
However, some challenges still lurk in the shadows. The resistance levels of conductive inks can be higher than that of metals like copper, necessitating careful balance in design to ensure efficient signal flow.
Dielectric Materials
Dielectric materials, which serve to insulate and separate conductive elements on a PCB, are equally vital in 3D printing. These materials ensure that circuits do not short-circuit and provide the necessary structural integrity. 3D printing technologies commonly leverage thermoplastics, such as polylactic acid (PLA) and acrylonitrile butadiene styrene (ABS), for this purpose.
The choice of dielectric materials is guided by:
- Electrical Properties: The material should restrict electrical current flow in unwanted areas.
- Thermal Stability: Many applications, especially in automotive or industrial settings, require enduring heat without deformation.
- Mechanical Strength: Enough robustness is needed to withstand the operational stresses throughout its life cycle.
As there is always a trade-off with dielectric materials, determining the right mix becomes crucial for practical applications. For instance, higher dielectric constants may enhance performance but can make materials brittle.
Composite Materials
Composite materials combine the properties of different substances to achieve superior characteristics. In the context of 3D printed circuit boards, composites may blend conductive and dielectric elements to create materials that offer both electrical conductivity and necessary insulation. This duality is remarkably advantageous, allowing for more compact designs while maintaining functionality.
Key aspects concerning composite materials include:
- Customization: Using a mix of materials facilitates tailored solutions that meet specific performance metrics without over-engineering.
- Weight Reduction: In sectors like aerospace or portable electronics, reducing weight while maintaining strength and functionality is paramount.
- Improved Performance: Properly engineered composites can lead to enhanced electrical efficiency and overall reliability of the boards.
"The material choice in 3D printing is not merely a technical detail; it is the cornerstone to successful design and application in electronics."
Adapting these materials to specific applications will define the advancements in industries ranging from consumer electronics to medical devices. Understanding the underlying properties and limitations allows researchers, students, and professionals to make informed decisions, driving the future of circuit board technology forward.
The Process of 3D Printing Circuit Boards
Understanding the process of 3D printing circuit boards is central to grasping the full scope of this technological revolution in the world of electronics. The ability to create customizable electronic structures directly from a digital model offers unprecedented flexibility, enabling advancements in many fields. This section will dissect the multifaceted stages involved in printing circuit boards, each critical in developing components that are not just functional but also optimized for a variety of applications. The crux of this process entails a well-coordinated blend of design, execution, and refining, ensuring that every circuit meets its intended specifications.
Designing the Circuit
Designing the circuit is the backbone of 3D printing in electronics. Before a single layer of material is laid down, a thorough design must be prepared, often accomplished through sophisticated software programs like Eagle or KiCAD.
The design phase involves several fundamental tasks:
- Schematic Creation: It begins with drafting a schematic that outlines the desired electronic functions, showing how various components interact. Many designers opt for user-friendly interfaces that reduce the complexity of circuit layout.
- Layout Planning: After the schematic is approved, the layout planning follows, converting the idea into a grid-like formation. This is where the meticulous placement of traces, pads, and vias comes into play.
- Simulation Testing: A crucial, yet often overlooked, step involves simulating the circuit to anticipate performance issues. This ensures that potential problems are identified before production, saving time and costs in physical alterations later.
Overall, proper design not only enhances functionality but also accounts for manufacturability, ensuring the printed circuit board adheres to vital industry standards.
Printing Techniques and Settings
With designs in hand, the next phase delves into the selections of techniques and settings for printing the circuit boards. Various methods exist, each tailored to meet specific project needs.
Some noteworthy techniques include:
- Inkjet Printing: This technique applies conductive inks in precisely controlled droplets, allowing for intricate designs. The printers must be calibrated meticulously to maintain the quality of printed lines, as a fraction off can lead to performance issues.
- Screen Printing: This method involves using a mesh screen to apply a layer of conductive material. While effective for mass production, it often requires additional steps for complex circuit designs.
- Extrusion-based Methods: In this approach, materials like PLA or ABS are extruded to form the circuit layers. It combines mechanical strength with flexibility, suitable for applications requiring durability.
Setting parameters, such as temperature, speed, and layer height, also play a pivotal role in ensuring the integrity of the board. Such decisions can affect not just the aesthetics but also the performance of the end product.
Post-Processing Requirements
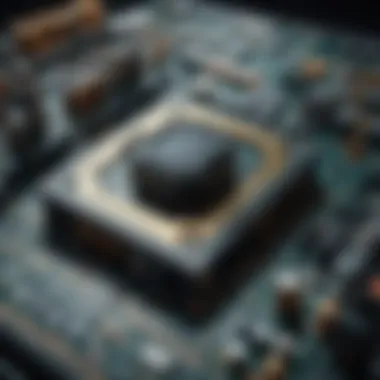
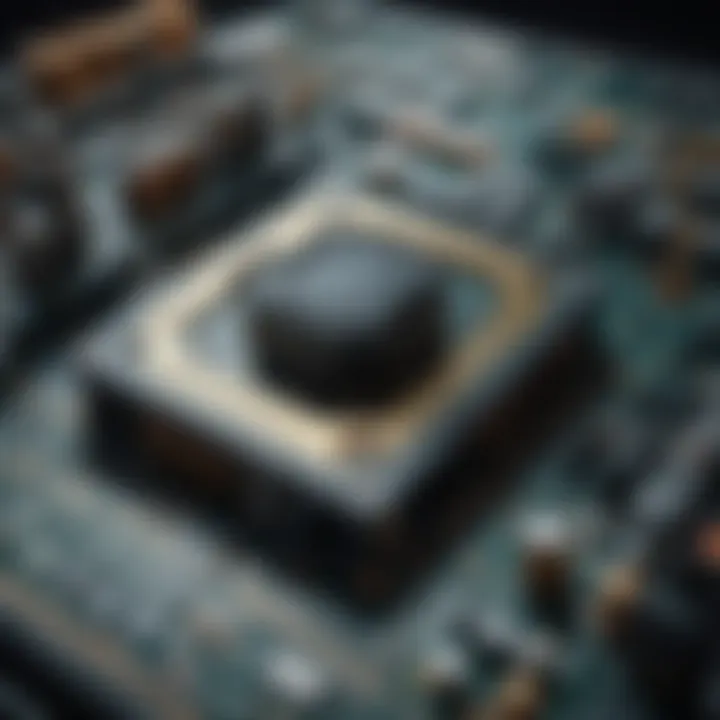
The work does not end when the printing machine stops; post-processing is essential for achieving optimal circuit performance. These subsequent steps can range from simple to elaborate, depending on the complexity of the design.
- Cleaning: Once printed, boards typically require a cleaning process to remove any residual materials. This is especially vital for inkjet techniques, where dried ink could obstruct electrical pathways.
- Curing: For certain inks, a curing process under UV light may be necessary to enhance conductivity and ensure that the printed components adhere firmly.
- Testing: Rigorous testing follows, including electrical tests to check for shorts or incomplete connections. This phase is crucial for preventing failures in real-world applications.
- Finishing Touches: Finally, applying protective coatings can greatly extend the life of the circuit board. This protects against environmental factors like moisture or dust, which can compromise functionality.
In closing, mastering the complete cycle from designing to post-processing is essential for anyone looking to harness the power of 3D printed circuit boards. By appreciating this process's intricate details, manufacturers can push the boundaries of what is possible in modern electronics.
Advantages of 3D Printing Circuit Boards
The advantages of 3D printing in the realm of circuit boards have reshaped how we perceive electronic production. In an age where speed, efficiency, and customization are king, itβs no wonder that this technology has been embraced quickly by various sectors. The benefits extend beyond mere cost reduction; they touch upon empowerment in design and innovation in applications.
Customization and Flexibility
One of the standout features of 3D printing is customization. Traditional manufacturing methods often require rigid tooling and setup, limiting a designerβs creative scope. With 3D printing, however, hobbyists and experts alike can churn out unique circuit board designs tailored to distinct requirements. This adaptability can be invaluable when working on specialized projects, such as custom gadgets that need unique layouts. Whether itβs adjusting the size for fitting into smaller devices or modifying the shape to accommodate specific components, the level of flexibility offered by additive manufacturing is unmatched.
Not only does this approach allow for tailored designs, but it also promotes rapid iteration. Designers can tweak their circuits, print a new version quickly, and test it in real-time. This leads to innovations that wouldβve been slow to materialize with traditional means. Essentially, one can say this customization isnβt just an option; itβs often the key to unlocking new technologies.
Reduced Time and Costs
In terms of production speed, the changes brought about by 3D printing are broadranging. Traditional methods can involve substantial lead times due to setup requirements and material procurement. A single mistake can lead to considerable waste and rework. Meanwhile, with 3D printing, once the design is ready, the printing process can begin almost immediately. This feature allows for quicker turnaround times on projects.
Additionally, the cost implications of 3D printing are noteworthy. Where traditional manufacturing often requires expensive molds and setups, 3D printers operate with far less overhead. Smaller production runs, often necessary in the prototyping stage, can be done affordably without sacrificing quality. Moreover, as materials improve and printers become more cost-effective, expenses are expected to drop even further. Itβs like having a workshop that doesn't require financial strain for every change or trial run.
Prototyping Capabilities
The prototyping capabilities offered by 3D printing are a game changer in the electronics field. Developers can create several prototypes in a fraction of the time traditionally required. This rapid prototyping is crucial when striving for perfection in circuit design. It allows for an experimental approach where differences in schematics can be tested with ease, confirming or refuting design hypotheses before mass production.
Notably, failure in the prototyping stage, which can often be devastating in established systems, becomes a learning opportunity. If a specific arrangement of components isnβt performing as desired, itβs merely a matter of redesigning and reprinting β a much easier situation than reordering parts or remaking vast batches.
All these advantages present a persuasive case for adopting 3D printing technologies in the circuit board manufacture process. By providing customization, reducing production times and costs, alongside unparalleled prototyping capabilities, it not only transforms ways of working but also greatly expands the horizons for innovations in the field. Moving forward, such advantages will undoubtedly play a crucial role in shaping the future of electronic production and design.
"3D printing is dethroning traditional methods by removing barriers to creativity and accelerating the path to market for innovative electronics." - Francesca Smith, Electronics Innovator
Challenges and Limitations
In the world of 3D printing, especially when it comes to circuit boards, challenges and limitations often rear their heads. Understanding these hurdles is crucial for anyone who dares to navigate this innovative field. While the promise of customization and swift prototyping captivates many, the underlying complexities can pose substantial obstacles. The challenges related to materials, durability, and scalability can affect not only the production process but also the overall effectiveness of circuit boards in diverse applications. Addressing these limitations is necessary to fully harness the potential that 3D printing holds for the future of electronics.
Material Constraints
Material selection for 3D printed circuit boards is indeed a sticking point. While thereβs no shortage of dazzling conductive inks and paste options on the market, each of these materials comes with its own quirks. For instance, the conductivity of a material may not hold up when stretched or subjected to heat. Traditional materials used in circuit boards are notable for their reliability, making it tricky to switch completely to 3D printed alternatives. The constraints in material choices also extend to dielectric propertiesβmany materials struggle to provide adequate insulation, which is critical for preventing short circuits.
"The quality of the materials directly influences the end performance of the circuit boards, making it a key factor in the manufacturing process."
Furthermore, the printing process can introduce its own set of inconsistencies. Variation in layer thickness or print resolution often leads to weak spots within the circuit. It's a precarious balance, choosing materials that can print effectively while also providing the conductivity and durability that electronics demand.
Durability and Reliability Issues
When it comes to durability, 3D printed circuit boards often face the heatβliterally. The thermal stability of many printed materials does not match that of their traditionally manufactured counterparts. For applications requiring higher operational temperatures, like automotive electronics or industrial machinery, this can be a dealbreaker. A board that warps or breaks during use is not just inconvenientβit renders itself practically useless.
Reliability is another significant concern. In traditional manufacturing, years of trial and error have established standards for durability that newer technologies are yet to meet. The long-term performance of 3D printed circuit boards can vary considerably based on a range of factors including the operating environment and the specific materials used. These inconsistencies can lead to failures in critical applications, thus hindering their adoption in sensitive areas like medical devices or aerospace technologies where reliability is a non-negotiable.
Scalability Concerns
Scalability poses another critical challenge. While 3D printing allows for small batch productions and prototypes, scaling these processes to meet larger demands can prove to be a whole different ballgame. As production volumes increase, the time required to print each circuit board can lead to significant delays. In industries where rapid rollout is essential, such as consumer electronics, this can create bottlenecks that hinder competitiveness.
Moreover, consistency becomes a nagging problem at scale. Maintaining uniform quality across a production run can be tricky. Variability in the printing process, whether due to machine calibration or fluctuations in material properties, often leads to discrepancies that might not surface until later in the production cycle. This unpredictability can thwart manufacturers looking to scale up quickly.
In summary, while the advancements in 3D printing for circuit boards bring forth intriguing possibilities, being aware of the challenges and limitations is essential for navigating the landscape effectively. Addressing these issues will pave the way for wider adoption and innovative applications, enhancing the potential of this technology in the electronics sector.
Current Applications of 3D Printed Circuit Boards
The integration of 3D printing technology into circuit board manufacturing has opened doors to a myriad of applications across various industries. From consumer electronics to automotive innovations, this approach presents significant opportunities that can reshape how we conceive electronics. The growing trend of personalization and rapid prototyping lends itself well to 3D printed circuit boards, allowing for tailored solutions that meet specific operational needs while reducing time and cost.
Consumer Electronics
In the realm of consumer electronics, 3D printed circuit boards are revolutionizing the way gadgets are produced and used. Traditional methods often involve multiple steps, requiring various components to be assembled separately. However, with 3D printing, companies can fabricate custom circuit boards that are highly tailored to fit specific designs and functionalities.
For instance, companies like Apple and Samsung are investing in additive manufacturing to create more compact and integrated devices. These boards can incorporate essential components like antennas and sensors directly, saving both space and assembly time. This means that next-generation smartphones could be sleeker, lighter, and hold enhanced functionalities.
In addition, the rapid prototyping capability allows manufacturers to quickly iterate designs. This flexibility means that consumer preferences can be addressed faster, which is a crucial value-add in a market that frequently changes.
Medical Devices
The application of 3D printed circuit boards in medical devices presents a particularly exciting opportunity. In healthcare, precision and reliability are paramount. Manufacturers are leveraging 3D printing to create circuit boards that are not just innovative but also highly customized for specific medical devices like implants or diagnostic tools.
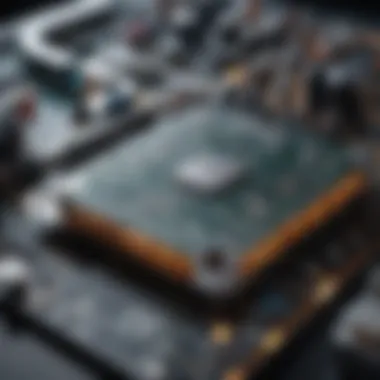
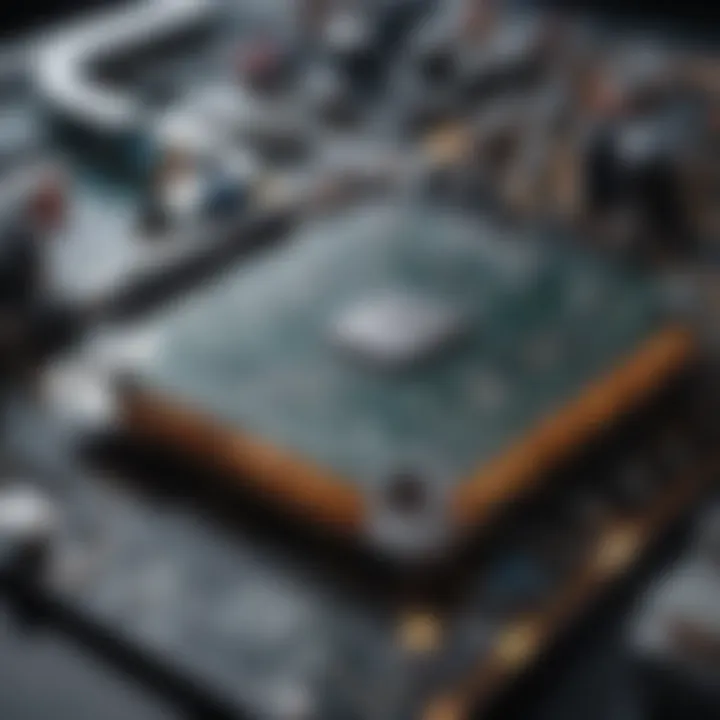
For example, Medtronic has experimented with additively manufactured circuit elements that can be integrated into wearable devices. These devices can monitor vital signs and send data in real-time, offering unparalleled insights into patient health. Because the requirements for medical applications can vary significantly from one device to another, having the ability to produce circuit boards on demand streamlines processes while adhering to strict safety regulations.
Moreover, 3D printing can allow for the creation of smaller, more efficient devices that can be embedded in unconventional places, like clothing or directly into the body. The customization potential not only fuels innovation but also directly caters to the individual needs of patients, thus enhancing their quality of care.
Automotive Industry Innovations
The automotive sector is swiftly adopting 3D printed circuit boards as well, as vehicles become more interconnected and intelligent. Innovations in this area include everything from embedded sensors in vehicles to smarter control modules. Companies like Ford and Tesla are exploring ways to integrate these technologies into their vehicles for improved systems like navigation, safety, and entertainment.
One key advantage is the ability to reduce weight in vehicles. Traditional circuit boards can add considerable bulk, which impacts fuel efficiency. By creating lighter, more integrated circuit boards, manufacturers can improve vehicle performance while reducing emissions.
Furthermore, the ability to produce circuit boards locally can lead to significant cost savings and reduced lead times for automotive parts. As electric vehicles gain traction, the demand for specialized circuitry that integrates seamlessly with advanced battery technologies continues to rise. In this dynamic environment, 3D printing offers the flexibility and speed that the automotive sector needs to keep up with consumer demands and regulatory changes.
Implementing 3D printed circuit boards not only enhances product capabilities but also reshapes supply chains, reducing the dependence on traditional manufacturing methods.
In summary, the current applications of 3D printed circuit boards represent a fascinating crossroads of technology and innovation. Each industry, whether it's consumer electronics, healthcare, or automotive, is poised to benefit from the unique attributes of 3D printing, leading to significant advancements and efficiencies. The adaptability of these circuit boards ensures that they will play a vital role in the future of electronic device manufacturing.
Environmental Considerations
The advent of 3D printing technology in the circuitry domain opens up a wealth of opportunities, yet it also raises pivotal environmental considerations. As industries increasingly pivot towards these innovative production techniques, understanding their ecological impact is crucial. The production process for traditional circuit boards often produces significant waste and relies on toxic chemicals. In contrast, 3D printing can potentially streamline operations and reduce waste, creating a more sustainable future for electronics. Furthermore, the shift towards environmentally friendly practices aligns with global interests in sustainability, thereby enhancing the appeal of 3D printing in circuit design.
Sustainable Materials in Circuit Design
Sustainable materials play a vital role in revolutionizing circuit board manufacturing. By utilizing biocompatible or recyclable materials, manufacturers not only minimize their ecological footprint but also pave the way for innovative solutions. The use of conductive polymers and eco-friendly inks, for example, serves dual purposes: achieving the necessary electrical properties while adhering to environmental standards.
A few key highlights of sustainable materials include:
- Biodegradability: Materials that break down naturally over time reduce long-term landfill impacts.
- Recyclability: These materials can be reused, which decreases waste during production.
- Non-toxicity: Using substances that are less hazardous protects both workers and consumers.
The transition to these materials might present initial challenges, such as requiring additional research or modifying existing production lines. However, the long-term environmental benefits far outweigh these hurdles.
Waste Management Practices
Efficient waste management practices in 3D printed circuit boards are essential for minimizing environmental harm. Traditional circuit board manufacturing leaves a hefty carbon footprint due to the high levels of waste produced. However, with 3D printing, waste can be significantly reduced through more precise manufacturing methods.
Key waste management strategies include:
- Recycling Printed Waste: Leftover materials from the printing process can often be collected and reused, thereby limiting raw material consumption.
- Responsible Disposal: Establishing clear protocols for disposing of old or damaged circuit boards helps reduce e-waste concerns.
- Modular Designs: Designing circuit boards that can be easily upgraded or repaired minimizes waste associated with full replacements.
Through these practices, companies can not only limit their environmental impact but also cultivate a culture of sustainability that resonates with eco-conscious consumers. Emphasizing waste management is not merely a trend; itβs a critical step for future-proofing manufacturing in a world increasingly concerned about sustainable practices.
"Sustainability is key in the transition towards eco-friendly manufacturing, and every small step counts in this lifelong journey."
By considering these environmental aspects, it becomes clear that the integration of 3D printing technologies in circuit board production requires a balanced approachβone that weighs benefits against potential consequences. Moving forward, those engaged in this field must continue to evaluate not just the efficiency and cost of materials, but also the broader impact on our planet.
Future Prospects of 3D Printed Circuit Boards
The exploration into the future of 3D printed circuit boards opens avenues that are not merely theoretical but intensely practical. As technology progresses, the context of electronics manufacturing is shifting, making the understanding of these prospects crucial. Not only does this advancement redefine how circuits are crafted, but it also influences the sustainability and efficiency of production in various sectors.
The potential benefits of embracing 3D printing in circuit board manufacturing are multifaceted. From cost reductions associated with reduced material waste to enhanced design flexibility, manufacturers can push the boundaries of traditional electronics manufacturing. For instance, companies have already started experimenting with multi-functional boards, which can integrate different electronic components into a single print job, saving valuable time and resources.
Innovative Research Directions
In the realm of innovative research directions, scientists and engineers are actively investigating new materials and methods that can amply improve the effectiveness of 3D printed circuit boards. One of the focal points is the development of advanced conductive inks that boast greater conductivity and flexibility than standard materials. This can ultimately lead to a better performance of the end products, especially in wearable and flexible electronics.
Additionally, research into hybrid manufacturing techniques is garnering attention. This involves combining traditional methods with additive techniques to achieve intricate designs that were previously unimaginable. Researchers are exploring bio-compatible materials for medical devices, where safety and reliability become paramount. This not only broadens the application of 3D printed circuit boards but also opens new markets.
"The challenges posed by scaling up production are met with intelligent designs and innovative materials, creating a remarkable synergy for future electronics."
Integration with IoT Devices
As IoT devices proliferate, the interface of 3D printed circuit boards with these technologies is becoming increasingly pertinent. With the need for smaller, lighter, and more efficient components, 3D printing offers a unique solution to these demands. Circuit boards can be tailored specifically for IoT applications, enabling a seamless integration of sensors and communication modules that are crucial for smart devices.
Moreover, this integration presents a strategic advantage for companies looking to rapidly prototype and iterate on their designs. Imagine printing a circuit that can connect directly to smart home systems or wearables that monitor health statistics in real-time. By leveraging 3D printing, manufacturers can quickly adapt designs based on user feedback, enhancing consumer satisfaction and driving innovation.*
Culmination
The exploration of 3D printing technology for circuit boards marks a significant milestone in electronics manufacturing. This article illustrates the various dimensions of 3D printed circuit boards, marrying innovation with practical application. Understanding the implications of this technology is crucial for anyone involved in electronics, from manufacturers to end-users.
The Future of Manufacturing Technology
Looking towards the horizon, the future of manufacturing technology centered around 3D printed circuit boards is bright and full of possibilities. Here are a few key aspects to consider:
- Increased Customization: With 3D printing, manufacturers can create tailored solutions that address specific needs, bridging gaps that traditional methods often overlook. Customized circuit boards can cater to unique device specifications, enhancing performance and user satisfaction.
- Broader Material Applications: As research progresses, new materials that can withstand higher temperatures or offer better conductivity are emerging. This evolution in material science opens doors to various applications across different industries, further integrating 3D printing in sectors like aerospace and wearable technologies.
- Integration with Other Technologies: The convergence of 3D printing with IoT and AI signifies a paradigm shift in manufacturing. Intelligent manufacturing systems capable of adjusting production processes based on real-time data will streamline operations and improve efficiency.
"The blend of 3D printing with cutting-edge technologies like IoT is set to revolutionize how electronic products are designed and produced."
- Environmental Sustainability: As the global community becomes more environmentally conscious, 3D printing offers the potential for reducing waste through precise layer-by-layer construction. Moreover, the exploration of sustainable materials and biodegradable options for circuit fabrication is gaining momentum.
- Educational Evolution: The rise of 3D printing in electronics also underscores the importance of education in this field. Schools and universities are beginning to integrate these technologies into their curricula, preparing future generations for the changing landscape of engineering and design.
In summary, the conclusion of this article reaffirms the transformative journey of 3D printed circuit boards is just beginning. While challenges remain, the advancements made thus far pave the way for a future marked by innovation and enhanced functionality in electronic devices.