Understanding Tempered Glass Sizing for Applications
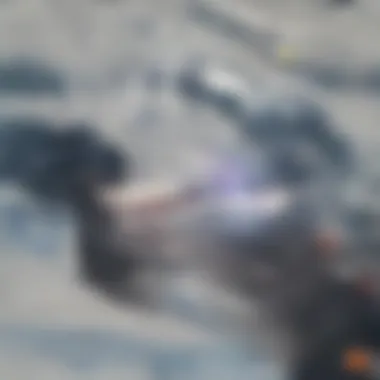

Intro
Tempered glass is a critical material used in many applications, ranging from residential windows to commercial structures and facades. Understanding its sizing is essential for ensuring safety, durability, and aesthetic appeal in architectural designs. The process of tempering enhances its strength compared to standard glass, but specific dimensions must be adhered to in order to maintain its structural integrity during use.
This section serves as an entry point into the various dimensions and characteristics of tempered glass. We explore its applications, implications of size choices, and how precise measurements play a significant role in the manufacturing processes. It’s vital to grasp these concepts to appreciate why tempered glass is preferred in diverse sectors, especially in architecture and construction.
Patterns of usage vary widely based on geographical location, design regulations, and technological advancement. Therefore, this overview intends to enlighten students, researchers, and professionals about the implications of tempered glass sizing across multiple fields.
Research Context
Background Information
Tempered glass is manufactured through a process of extreme heating and rapid cooling, which results in a stronger product. The sizing of tempered glass is dictated not only by the end application but also by regulatory standards and technical specifications unique to each project.
Standardization plays a crucial role, as many industries rely on uniform measurements to facilitate compatibility and safety. Typically, glass is measured in millimeters and varying standards can exist in different regions. It is paramount for professionals to navigate these variances to ensure compliance and performance.
Importance of the Study
Examining tempered glass sizing has significant implications. Understanding the dimensions and manufacturing protocols underscored in this article can help mitigate risks associated with installation failures and structural weaknesses.
Furthermore, insight into measurement techniques and selection criteria empowers architects and engineers to make informed decisions. This study highlights not just the technical aspects of tempered glass but also its overarching importance in contemporary architecture and design.
"The right dimensions for tempered glass significantly influence both its aesthetic appeal and functional performance."
Discussion
Interpretation of Results
In various testing scenarios, the relationship between size and performance has shown clear correlations. Larger segments of tempered glass tend to require more stringent production controls to avoid imperfections that could impair performance. Thus, understanding how sizing factors into the overall functionality ensures safety.
Comparison with Previous Research
Earlier studies have pointed out the discrepancies in tempered glass usage across different applications. However, more recent research has started mapping standardized approaches focusing on glass thickness and market trends. The evolution of tempered glass technology also raises new questions about how current practices align with historical data.
By engaging with both past and contemporary findings, we uncover a comprehensive view that informs best practices in the field. This synthesis of information ultimately enhances strategies for utilizing tempered glass effectively in architecture.
Preamble to Tempered Glass
Tempered glass is a critical material in modern architecture and product design. It is known for its strength and ability to withstand extreme temperatures. Understanding its properties helps in effectively using it in varying applications. Knowing about tempered glass is not just about physical properties but also about how these factors contribute to its practical applications.
Being aware of the definition and characteristics of tempered glass can assist architects and engineers in deciding when to use it. Its design features allow for greater safety and durability, which are crucial in places like buildings and vehicles. The benefits of using tempered glass can be found in its increased resistance to thermal stress and breakage, making it a favored choice in environments where safety is paramount.
Another important consideration is the application of tempered glass. The knowledge of where tempered glass is commonly used can guide professionals to make informed decisions for their projects. Its applications span across various industries, from residential buildings to commercial and automotive uses. This extensive range underscores the necessity of a comprehensive understanding of tempered glass and its sizing.
Definition and Characteristics
Tempered glass, also known as toughened glass, is manufactured through a process of extreme heating and rapid cooling. This procedure increases the glass's strength compared to standard glass. The heat treatment causes the glass to undergo a transformation in its structure, resulting in enhanced durability and safety parameters.
The main characteristic of tempered glass is its high strength. It can endure substantial mechanical load and thermal impact, making it suitable for various applications. If broken, tempered glass shatters into small, blunt pieces instead of sharp shards. This aspect significantly decreases the risk of injury.
Additionally, tempered glass can be produced in various thicknesses and sizes. Its versatility allows for specialized designs tailored to specific needs. This adaptability is particularly relevant in the construction and design worlds.
Common Applications of Tempered Glass
The various applications of tempered glass are a direct result of its unique properties. It is commonly used in a range of areas, including:
- Building and Construction: Tempered glass is widely used in facades, windows, and doors for both aesthetic and safety reasons. Large glass panels can create open spaces while ensuring structural integrity.
- Automotive: In vehicles, tempered glass is used for side and rear windows. Its strength and shatter-resistant properties enhance safety for passengers.
- Interior Design: Many modern interiors incorporate tempered glass in partitions, shower doors, and balustrades. This seamless appearance adds a sense of space without compromising safety.
Utilizing tempered glass in these applications greatly reduces risks associated with breakage, which is crucial in both public and private environments. Understanding where and how to use this material can lead to more innovative and safe design practices.
Significance of Glass Size in Design
The size of tempered glass plays a pivotal role in both structural and artistic frameworks of contemporary architecture. Its significance goes beyond simple dimensions, affecting durability, safety, and visual appeal. In various applications ranging from residential buildings to commercial spaces, the selection of appropriate glass size is critical.
Impact on Structural Integrity
Structural integrity relies on the resistance of materials against forces such as wind pressure, thermal changes, and stress from loads. Tempered glass, when designed to specific sizes, can provide exceptional strength compared to its untreated counterparts. This strength is paramount for maintaining safety standards.
When glass panels are too large, they may exert undue pressure on frames and supports, risking potential failure. Therefore, understanding the load-bearing capability of tempered glass in relation to its size is crucial. Manufacturers must adhere to specific engineering principles when sizing to ensure that each piece can withstand anticipated stresses in its intended environment.
Factors influencing structural performance include:
- Thickness of the glass: Thicker glass can bear more weight and resist breakage better.
- Support configuration: Proper support is necessary to prevent bending and breaking.
- Environmental conditions: Temperature fluctuations can cause expansion and contraction, affecting how glass is mounted.
"Proper sizing of tempered glass not only enhances durability but also ensures compliance with safety regulations, vital for any construction project."
Aesthetic Considerations
In additon to practical aspects, the aesthetic impact of tempered glass size cannot be understated. Designers and architects consider the visual effects that different sizes can create in a space. Larger panels can provide unobstructed views and an open feel to interiors, making them an attractive option for storefronts and facades.
Conversely, smaller glass pieces can lead to intricate designs, allowing creativity in architecture. The balance between safety and aesthetics lies in choosing the right size.
Key aesthetic considerations include:
- Proportions and ratios: The way glass sizes interact with other materials can create visual harmony or contrast.
- Light transmission: Larger glass surfaces can enhance natural lighting, contributing to energy efficiency.
- Framing choices: The choice of framing can affect how glass sizes appear within a design, impacting overall aesthetics.
In the context of design, understanding the significance of tempered glass sizes allows for a cohesive blend of functionality and beauty.
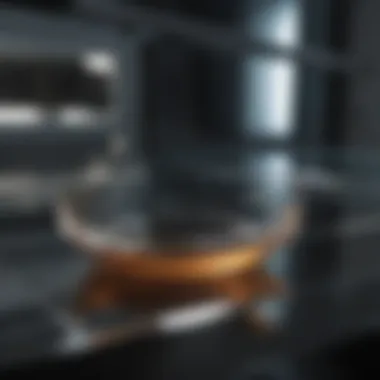

Measurement Techniques for Tempered Glass
Measuring tempered glass is a highly critical aspect of its production and application. The precise sizing of glass is fundamental to ensure both its functionality and aesthetics. Accurate measurement techniques help avoid issues related to structural integrity and visual appeal, thereby safeguarding safety and performance in various designs. This section outlines the essential tools used for measurement and the standardized practices that shape the industry.
Tools and Equipment Used
To accurately measure tempered glass, one must employ specific tools designed for precision and reliability. Common tools include:
- Calipers: Digital or dial calipers allow for precise measurement of the thickness and other dimensions of glass panels. They are valued for their accuracy and ease of use in various settings.
- Measuring Tapes: Especially for larger installations, non-stretchable measuring tapes are crucial for capturing length and width. They should be made of a material resistant to bending or damage to ensure durability.
- Laser Measurement Devices: These devices provide high-accuracy distance measurements. They also minimize human error, making them favorable in commercial applications.
- Thickness Gauges: Specific gauges are designed to check glass thickness as discrepancies can affect the glass's strength and performance.
Using the right tools not only improves accuracy but also streamlines the measurement process. Professionals must be well-acquainted with each tool's functionality to select the appropriate one based on project requirements.
Standard Measurement Practices
Standard measurement practices ensure consistency and adherence to industry norms. These practices involve:
- Calibration: Regular calibration of measuring tools is essential. This action ensures ongoing accuracy and reliability. Calibration adjustments may be necessary after extended use and exposure to various environments.
- Check Multiple Points: For uniformity, measurements should be taken at several points across the glass panel. This approach is important as it accounts for any non-uniformities in thickness or dimensions.
- Maintain Environmental Conditions: When taking measurements, it is crucial to conduct assessments in controlled environments. Temperature fluctuations can cause glass to expand or contract, leading to inaccurate readings.
Accurate measurement techniques are vital not just for ensuring proper fit and usability but also for meeting legal and safety standards.
By adhering to these practices, professionals can guarantee the quality of tempered glass in various types of constructions and applications. Overall, the methodologies discussed form the backbone of effective tempered glass measurement, impacting its functionality, safety, and longevity.
Standards and Regulations in the Industry
Understanding the standards and regulations in the tempered glass industry is crucial for several reasons. Compliance with these guidelines ensures safety, structural integrity, and customer satisfaction. As tempered glass serves various applications, from buildings to furniture, adhering to established benchmarks is essential to maintain quality and reliability.
Two main areas guide the production and use of tempered glass: international standards and local building codes.
International Standards
International standards play a significant role in ensuring consistency and safety across various regions. Organizations such as the International Organization for Standardization (ISO) and ASTM International set guidelines that manufacturers must follow to certify the quality of tempered glass. These standards often address the following aspects:
- Manufacturing processes: Guidelines dictate how tempered glass should be produced, including heating and cooling methods to ensure correct tempering.
- Safety requirements: Standards specify the minimum safety characteristics, including impact resistance and breakage patterns which are vital for both user safety and longevity.
- Performance metrics: Specific international benchmarks exist for evaluating the thermal and mechanical properties of tempered glass.
Compliance with these international standards not only enhances product quality but also fosters consumer trust. Buyers can make informed decisions knowing that they are purchasing glass that meets globally recognized criteria.
Local Building Codes
Local building codes add another layer of regulation that manufacturers and builders must navigate. These codes vary widely based on geographic location, reflecting local safety concerns, climate factors, and architectural styles. Understanding local codes involves several considerations:
- Regional specifications: Each locale may require specific glass thickness and size based on prevailing weather conditions and seismic activity. For example, a high-wind area may mandate thicker glass to withstand external pressures.
- Installation guidelines: Local codes often provide requirements for how glass must be installed. This ensures it will perform correctly under various conditions. Failure to adhere to these could lead to structural inadequacies or hazards.
- Building permits: Before construction begins, compliance with local codes is required to obtain necessary permits. This process ensures that all aspects of the building, including the tempered glass, meet safety standards.
In summary, standards and regulations form the backbone of the tempered glass industry, influencing not just production but also application and structural integrity.
Effective navigation of these regulations is critical for architects, builders, and manufacturers to ensure both compliance and safety.
Factors Influencing Glass Size Selection
The selection of tempered glass size is a crucial step in various applications, influencing both functionality and safety. This discussion revolves around environmental factors and mechanical stresses that determine the appropriate dimensions of tempered glass. Accurate sizing not only enhances performance but also ensures compliance with safety regulations. Understanding the nuances of the influencing elements is essential for architects, designers, and engineers.
Environmental Considerations
Environmental factors play a significant role in glass selection. Understanding the local climate is vital. For instance, regions subject to high winds or extreme temperatures require thicker or specially treated glass to withstand the forces. In coastal areas, resistance to corrosion becomes critical, pushing for specific treatments.
- Temperature Fluctuations: Variations in temperature can lead to expansion and contraction in glass. This effect may lead to thermal stress if the glass is not sized properly.
- Humidity Levels: High humidity can affect adhesives used in mounting glass. Choosing appropriate sizes can mitigate risks of failure.
- UV Exposure: In areas with high ultraviolet exposure, glass must be treated to resist deterioration. The size might also change based on requirements for coating applications.
- Pollution and Air Quality: The quality of the air can influence the lifespan of glass. Higher levels of pollutants may require more robust glass to avoid cracking.
When considering environmental impacts, it is imperative to balance aesthetics with practicality to ensure longevity and performance.
Thermal and Mechanical Stress
Understanding thermal and mechanical stresses is vital for determining tempered glass dimensions. Glass is inherently strong, but it is not immune to forces that may lead to cracking or breaking. Proper sizing can prevent issues related to stress.
- Thermal Stress: As mentioned, significant temperature changes can cause glass to expand or contract. If the glass is not sized correctly, it may lead to breakage.
- Mechanical Loads: Depending on the application, tempered glass may face various loads. Heavy wind loads on buildings or the weight of mounting systems can necessitate thicker glass.
- Installation Practices: Incorrect installations can introduce undue stresses. The size must also account for mounting hardware and installation methods.
- Impact Resistance: The possibility of impact needs to be considered, especially in safety glass applications like in architecture or vehicles.
Properly sized tempered glass will not only withstand thermal fluctuations but also mechanical loads, thereby ensuring safety and durability.
Cutting and Processing of Tempered Glass
Cutting and processing tempered glass is a crucial stage in its overall lifecycle. It involves specialized methods and careful considerations to achieve precise dimensions while maintaining the glass’s strength and safety characteristics. Understanding this process aids in optimizing the utility and performance of glass in various applications, including architecture, automotive, and consumer products.
Techniques for Cutting Glass
The cutting of tempered glass requires specific techniques that differ significantly from standard glass cutting. This is because tempered glass undergoes a heat treatment to increase its strength, making it more challenging to cut once it has been processed.
- Water Jet Cutting: This technique utilizes high-pressure water jets mixed with abrasive materials. Water jet cutting is precise and does not introduce heat, which can cause the glass to shatter.
- Diamond Blade Cutting: Specialized diamond blades are employed for their cutting accuracy and ability to handle the hardness of tempered glass. This method involves a diamond saw that can cut through glass smoothly.
- Laser Cutting: Involves using focused laser beams to cut glass. This method is growing in popularity due to its precision and the ability to create intricate patterns and designs.
The tools and methods chosen often depend on the specific requirements of a project. It’s essential to ensure that the cutting technique used aligns with the desired application and meets any relevant safety standards.
Post-Cutting Processing Techniques
After glass has been cut, additional processing techniques are necessary to prepare it for use. Each technique focuses on enhancing the glass's performance and ensuring it meets quality standards.
- Edge Finishing: After cutting, edges may be sharp and rough. Edge finishing involves grinding and polishing the edges to eliminate sharpness and prevent injury during installation or use.
- Surface Treatment: This process may involve applying coatings to improve resistance to scratches, chemicals, or environmental conditions. Surface treatments can enhance the aesthetic appeal of the glass as well.
- Cleaning: Proper cleaning processes must be carried out to remove any contaminants or dust that could affect appearance or adhesion during installation.
These post-cutting techniques are critical. They address not only aesthetic aspects but also functional performance in applications, ensuring that tempered glass delivers on its promise of strength and safety.
"Proper cutting and processing of tempered glass are vital for both performance and safety in its application."
Overall, understanding the methods used in cutting and processing tempered glass serves to inform better practices and innovation in manufacturing. This knowledge is beneficial to students, researchers, and professionals seeking to enhance their expertise in glass technology and related fields.
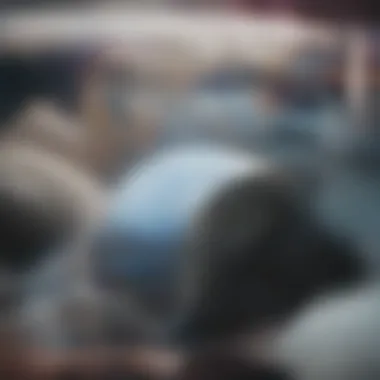

Quality Control Measures
Quality control measures are vital in the production of tempered glass. They ensure that the glass meets safety and performance standards. Such measures help in identifying defects and inconsistencies during manufacturing. Implementing a systematic approach to quality control increases the reliability of tempered glass products.
Regular inspections are essential. These inspections can detect surface imperfections, thickness variances, or thermal strength issues early in the production process. Technicians utilize various inspection techniques to uphold these quality standards.
Effective quality control contributes to several benefits:
- Safety Assurance: Ensures that the glass can withstand specified stresses, reducing the risk of failures and accidents.
- Consistent Quality: Provides uniformity in products, which is crucial for both aesthetics and structural integrity.
- Cost Efficiency: Helps in identifying defective items before they reach the market, thus saving on potential recall costs.
All these factors lead to greater trust from customers and stakeholders in the tempered glass industry.
Inspection Techniques
Inspection techniques in quality control involve various methods to examine tempered glass. These methods include visual inspections and non-destructive testing. Visual inspections are the first line of defense; they allow workers to check for visible cracks or chips.
Non-destructive testing is also paramount. Techniques such as ultrasonic testing or stress testing can be used. These methods evaluate internal integrity without damaging the glass. Effective implementation can be seen through:
- Regular training of staff on best practices for inspection.
- Use of advanced technology to capture defects not easily seen by the naked eye.
- Establishment of standard checklists to ensure consistency in inspections.
Incorporating these practices can lead to a more thorough quality assurance process. Inspections should be performed throughout the entire production cycle, from raw materials to finished products.
Testing Tolerance Levels
Testing tolerance levels is a critical function in quality control. It determines how much variation is acceptable in physical dimensions of tempered glass. Various types of tolerance levels are set based on industry standards and project requirements.
Measurement tools such as calipers and micrometers help assess the precision of glass dimensions. Following accepted tolerances ensures that the glass fits correctly in its intended application.
Key factors influencing tolerance testing include:
- Glass Thickness: Variation here can significantly affect performance. Consistency in thickness needs strict testing.
- Edge Quality: Rough or uneven edges can lead to breakage. Thus, edge tolerances must meet specified standards.
- Overall Dimensions: Height, width, and length are critical dimensions that require precise measurement to ensure compatibility with frames and structures.
By implementing robust testing of tolerance levels, producers can ensure that their products comply with necessary standards. This commitment ultimately leads to higher customer satisfaction and fewer issues post-installation.
Customization of Tempered Glass Sizes
Customization of tempered glass sizes is a crucial aspect that significantly impacts various industries, including architecture, interior design, and manufacturing. Custom sizes allow a better fit for unique design specifications and functional requirements. This practice is not just about aesthetics but also involves practicality and safety in applications.
When discussing customization, one must consider several elements. First, the physical dimensions of the glass must align with the intended application. For instance, residential structures may require specific sizes for windows or shower doors. On the other hand, commercial applications could call for larger panels to create expansive facades. Additionally, custom sizes can reduce waste during production, resulting in cost savings and a more efficient use of materials.
There are benefits to customizing tempered glass sizes, including:
- Enhanced Design Flexibility: Designers can create spaces that are truly unique through tailored measurements.
- Improved Functionality: Specific sizes can lead to better performance in different environments, such as increased durability against external forces.
- Minimized Waste: Proper measurements can reduce offcuts and excess material usage.
However, customization also requires careful consideration regarding the production capabilities of glass manufacturers. Meeting precise specifications may necessitate advanced machines and skilled technicians, which can influence lead times and costs.
Tailoring Sizes for Specific Applications
Tailoring tempered glass sizes for specific applications involves understanding the needs of both the project and its environment. For example, glass panels in high-rise buildings require precise engineering to handle wind loads and thermal expansion. These considerations go beyond mere aesthetics, focusing on safety and longevity.
In residential applications, tempered glass often serves as balustrades or partitions. Here, precise sizing is essential to ensure compliance with safety regulations. The same attention applies to the hospitality industry, where custom glass sizes can elevate a guest's experience through unique designs that blend seamlessly with the overall ambiance.
Ultimately, tailoring sizes to meet application needs enhances overall performance, making it a vital component of design and engineering processes.
Client-Driven Specifications
Client-driven specifications are an integral part of the customization process. They reflect the client's vision, practicality, and adherence to regulations. Having clear communication between clients and manufacturers is essential to effectively translate client requirements into tangible products.
This interaction often involves detailed discussions on:
- Dimensions: Accurate measurements to meet the spaces' constraints and requirements.
- Design Intent: Achieving a specific look or feel that aligns with the client’s aesthetic preferences.
- Performance Criteria: Requirements regarding tension, temperature resistance, and other physical properties.
Customizing tempered glass to client specifications often leads to enhanced satisfaction and overall project success.
A well-defined specification process can also streamline production. Creating a prototype or a sample can allow for adjustments before full-scale manufacturing.
Costs Associated with Tempered Glass
Understanding the costs associated with tempered glass is crucial for designers, architects, and engineers. The price can greatly impact budget and project feasibility. Several elements contribute to the final cost, which can influence decisions in both design and implementation.
One of the first factors is the raw materials used in the production process. Quality of the original glass plays a significant role. Higher quality materials usually mean a higher price. Besides raw material cost, the manufacturing process also affects pricing. Specialized equipment and techniques, such as tempering, increase the costs. The more complex the process, the higher the potential expenses.
Another cost consideration is transportation. Shipping tempered glass can be expensive due to its weight and fragility. Ensuring safe transport demands special packaging and handling. This adds to the overall cost.
Moreover, labor costs in the production facilities can’t be ignored. Skilled workers are often required to handle the precise cutting and processing necessary for tempered glass, which adds to expenses.
Finally, market demand can fluctuate prices. Higher demand may increase cost, while lower demand may lead to discounts. Evaluating these elements not only enriches understanding but also aids in strategic budget management for projects.
Factors Affecting Cost
Several key factors directly influence the cost of tempered glass. These include:
- Glass thickness: Thicker glass often commands higher prices due to more material used in production.
- Custom size and shape: Unique requirements may require additional processing, which raises costs.
- Quality certifications: Compliance with industry standards often necessitates testing and inspections, increasing costs.
- Finishes and treatments: Special treatments for UV protection, for instance, can add to the expense.
- Volume of purchase: Buying in bulk can often lead to cost reductions.
Understanding these factors allows professionals to make informed decisions regarding their projects.
Budgeting for Projects
When it comes to budgeting for projects involving tempered glass, a clear plan is essential. Start with a precise estimation of costs discussed earlier. Prepare a detailed breakdown of all related expenses, including material, labor, transportation, and any additional treatments.
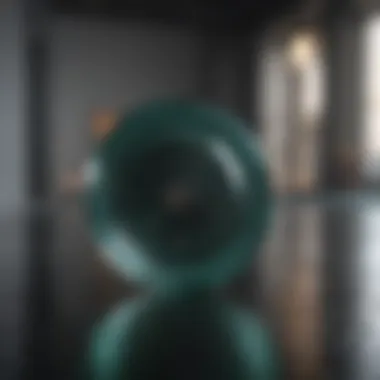

Be sure to include a buffer for unexpected costs, as projects often do not go entirely as planned. This may include:
- Delays in manufacturing or delivery
- Changes in project scope or design
- Additional requirements for safety or compliance
Lastly, consider consulting with suppliers or contractors during the budgeting phase. They can provide valuable insights and help refine estimates based on current market conditions. This collaborative approach can greatly assist in establishing a realistic budget, aligning financial resources with project goals.
Sustainability in Tempered Glass Production
Sustainability is crucial in production of tempered glass. The pressing need for eco-friendly practices in manufacturing aligns with the global efforts to reduce environmental impacts. Tempered glass offers several benefits due to its durability. This property allows it to have a longer lifespan compared to regular glass, which is a significant factor in sustainability. By selecting tempered glass, industries can decrease waste and minimize replacements over the years.
It also reduces energy consumption during its life cycle, making it a preferred choice when considering materials for green building projects.
Eco-Friendly Practices
Adopting eco-friendly practices in the tempered glass industry involves various methods. First, energy-efficient manufacturing processes can significantly lower carbon footprints. Using renewable energy sources during production, such as wind or solar power, helps in this regard.
Moreover, many manufacturers now focus on minimizing water usage during production. This ensures that less water is wasted and encourages responsible consumption.
Another practice involves selecting raw materials that are sourced sustainably, reducing reliance on non-renewable resources. The shift towards environmentally-conscious choices affects not just the glass itself but also contributes to the overall sustainability of construction projects.
Recyclability of Tempered Glass
Tempered glass is notable for its recyclability, which is another vital aspect of sustainable production. At the end of its life cycle, tempered glass can be crushed and reused as an ingredient in new glass production.
Recycled tempered glass can contribute to the production of various glass products, thus reducing the demand for virgin materials. This process of recycling helps conserve resources and minimizes environmental degradation.
"Recycling tempered glass contributes to a circular economy, reducing waste and decreasing the need for new raw materials."
It is essential for industries to promote glass recycling initiatives, encouraging consumers to return glass for reuse instead of disposing of it unnecessarily. This not only aids in sustainability but also fosters a culture of environmental responsibility.
Future Trends in Tempered Glass Manufacturing
Understanding the future trends in tempered glass manufacturing is vital for a number of reasons. First, it provides insight into how the industry may evolve, bringing forth innovations that can enhance product performance, safety, and sustainability. As global demand for glass products continues to grow, manufacturers must adapt to new challenges and opportunities. This section examines two key aspects: technological advancements and market demand projections.
Technological Advancements
The continual advancement of technology in tempered glass manufacturing leads to improved production methods. Automation and smart manufacturing are at the forefront. These technologies help reduce costs and improve precision in sizing, which is critical in maintaining the integrity of tempered glass.
With innovations like computer numerical control (CNC) cutting, manufacturers can achieve more accurate dimensions with less material wastage. Moreover, the use of artificial intelligence in quality checks ensures that each piece meets the rigorous standards set by the industry.
"Investing in technology is not just about efficiency; it can significantly impact product quality and safety."
Another significant trend is the development of energy-efficient manufacturing processes. The industry is exploring ways to minimize energy consumption during the tempering process. For example, the integration of renewable energy sources and the use of heat recovery systems are becoming common, reducing environmental footprints. Lastly, there is a push towards enhanced safety features in glass products. The incorporation of sensors for monitoring structural integrity in real-time ensures that any potential failure can be addressed proactively.
Market Demand Projections
Market demand for tempered glass is influenced by various sectors, including architecture, automotive, and electronics. Understanding these projections helps manufacturers align their production strategies with consumer needs.
The architectural sector, for instance, is seeing a trend towards larger glass surfaces for both aesthetic and functional purposes. More residences and commercial buildings are opting for facades that incorporate large tempered glass panels. This trend represents an opportunity for manufacturers to offer custom-sized solutions.
In the automotive industry, safety and design flexibility are driving demand. The transition towards electric vehicles is leading to innovative designs that require specialized tempered glass products to maximize both performance and style.
Furthermore, the growth of smart technology integration, such as self-tinting glass and smart windows, is expected to significantly impact market demand. These products require advanced manufacturing methods and materials that enhance their functionality.
In summary, the future of tempered glass manufacturing will be shaped by technological advancements and evolving market demands. Manufacturers who can anticipate these trends and adapt to them will hold a competitive edge.
Challenges in Tempered Glass Sizing
Tempered glass has become a preferred choice in many applications where strength and safety are paramount. However, sizing tempered glass presents its own set of challenges. Understanding these obstacles can help manufacturers, architects, and engineers make informed decisions.
Production Limitations
The production of tempered glass involves several processes, including the initial cutting, heating, and rapid cooling. Each phase comes with its own constraints that can affect the final size of the glass.
- Material Variability: The raw glass material can demonstrate variations in thickness and composition. These discrepancies can cause complications in achieving desired dimensions during slicing and tempering.
- Heat Distribution: Uneven heating during the tempering process can warp the glass, leading to inaccuracies in size. This is particularly critical for large sheets of glass where maintaining uniform temperature is challenging.
- Cutting Techniques: Different cutting techniques, such as water jet cutting or laser cutting, may yield varying degrees of precision. Inaccurate cuts can lead to glass that does not meet specifications, impacting both its aesthetic value and structural integrity.
- Thickness Limits: The maximum size and thickness of tempered glass are dictated by equipment capabilities. This, in turn, influences how large a single pane can be while still securely fitting into frames or structures.
Addressing these production limitations requires rigorous quality control measures and continual investment in technology to enhance precision and consistency in manufacturing processes.
Logistical Issues
The transportation and handling of tempered glass also present challenges that can complicate size management.
- Transportation Constraints: Once produced, tempered glass is prone to breakage if not handled carefully. Logistics must ensure that the glass does not experience undue stress, which can deform its size and structural integrity. The type of vehicle and packaging used can greatly impact the glass retention for its intended size.
- Storage Conditions: Proper storage is essential to prevent warping or damage before the glass is installed. Factors such as humidity, temperature, and stacking method can lead to size alteration, requiring strict adherence to recommended handling procedures.
- Installation Variables: During installation, poor handling can lead to scratching or cracking. Installers must work within precise tolerances to ensure the tempered glass fits the designated frame correctly, maintaining the desired dimensions.
"Understanding logistical issues in tempered glass sizing ensures that professionals can mitigate risks associated with handling, storage, and installation."
In summary, addressing the challenges in tempered glass sizing involves understanding both production limitations and logistical issues. This knowledge is critical for producing high-quality glass that meets specific design requirements, ensuring safety and aesthetic value in its application.
Culmination
The conclusion of this article underscores the vital role of understanding tempered glass sizing. In a world increasingly reliant on glass in construction, architecture, and design, knowledge about its dimensions and specifications becomes paramount. Accurate sizing not only ensures enhanced durability of structures but also aligns with aesthetic goals, making it essential for architects and engineers alike.
Summary of Key Points
In reviewing the content, several crucial elements emerge:
- Importance of Size: The size of tempered glass directly influences its performance, including its resistance to thermal stress and structural integrity.
- Measurement Techniques: Proper techniques for measuring glass ensure that it fits seamlessly into various applications, reducing the risk of installation setbacks.
- Standards and Regulations: Adherence to industry standards and local building codes is fundamental to maintaining safety and quality.
- Customization and Costs: Custom sizing is prevalent, and understanding associated costs is necessary for effective budgeting and project planning.
Implications for Future Research
Future research in tempered glass sizing should focus on the following areas:
- Innovative Measurement Methods: Developing advanced measurement techniques could enhance accuracy and efficiency in production processes.
- Environmental Impact Assessments: Investigating the environmental effects of glass sizing and its production may lead to more sustainable practices in the industry.
- Advanced Materials: Exploring new materials or coatings that can optimize the performance of tempered glass in varying sizes can open avenues for further innovation.
Collaborations between academicians, industry professionals, and regulatory bodies will be essential in driving advancements in this field. A shared commitment to improving tempered glass performance through precise sizing can help fulfill the growing demands of modern construction and design.