Understanding SLS 3D Printing: A Comprehensive Overview
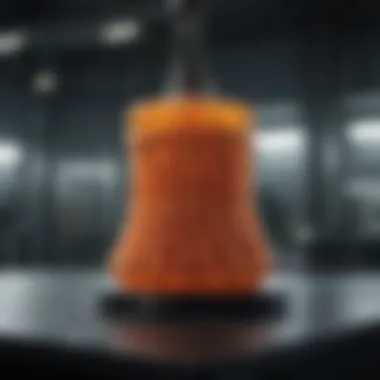
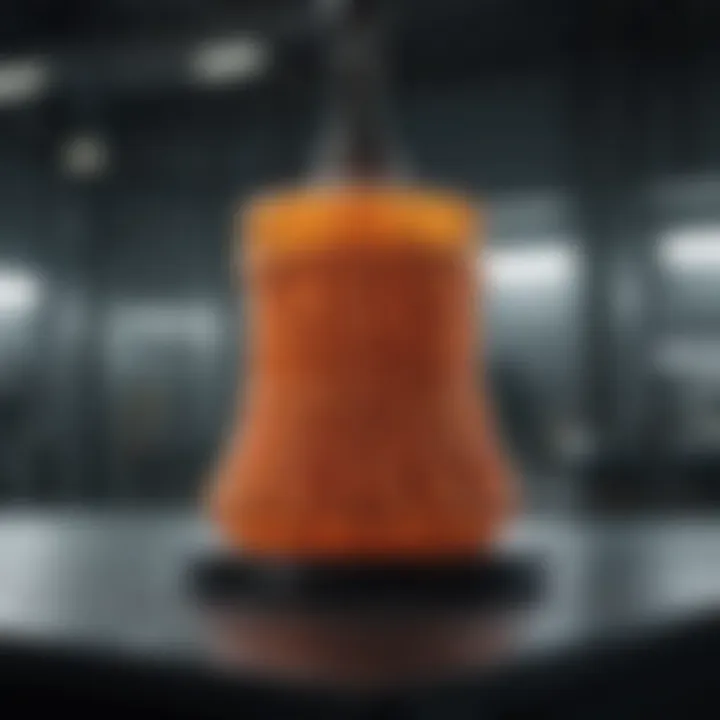
Intro
Selective Laser Sintering (SLS) has emerged as a cornerstone in the realm of 3D printing technologies. Its prominence is attributed to its ability to create complex geometries with exceptional precision, making it a preferred choice across diverse sectors. From rapid prototyping in the automotive industry to intricate medical applications, SLS's influence is pervasive. This article provides a comprehensive exploration of SLS, elucidating its fundamental principles, operational mechanisms, and material requirements. By understanding these aspects, professionals and researchers can better appreciate the technology's advantages and limitations.
Research Context
Background Information
SLS technology first appeared in the 1980s and represents a significant advancement in additive manufacturing. Unlike traditional manufacturing processes, which often involve subtractive methods, SLS builds objects layer by layer from powdered materials. The process uses a high-powered laser to selectively fuse powdered material, typically nylon or polymers, based on a digital model. This method provides versatility, enabling the production of parts with intricate details and various mechanical properties.
Importance of the Study
This study aims to dissect the intricacies of SLS 3D printing, addressing its importance in modern manufacturing. Understanding SLS can empower industries to innovate, refine product design, and enhance operational efficiency. Moreover, grasping its limitations will guide experts in choosing the right technology for specific applications. In todayβs competitive landscape, where agility and precision matter significantly, an in-depth comprehension of SLS is invaluable.
Discussion
Benefits of SLS
SLS brings several benefits to the table, especially in industrial settings. Key advantages include:
- Design Flexibility: SLS allows for the creation of geometries that are impossible to achieve with traditional methods.
- Material Options: A variety of materials can be used, including polymers, metals, and composites, broadening its application scope.
- No Support Structures Needed: Parts are built within the unsintered powder, reducing the need for additional support.
- Durability: The finished products exhibit high strength and rigidity, making them suitable for functional testing.
Limitations of SLS
However, certain limitations also accompany this technology. Noteworthy drawbacks include:
- Surface Finish Quality: The surface quality may require post-processing for aesthetic applications.
- Speed: Compared to some other 3D printing technologies, SLS can be slower, especially for larger builds.
- Cost: The initial setup and material costs can be higher than conventional methods.
"Understanding the capabilities and constraints of SLS enables informed decision-making in manufacturing processes."
Applications in Various Industries
SLS finds utility across numerous sectors:
- Aerospace: Lightweight parts, components for drones, and flight-ready prototypes.
- Automotive: Prototype parts, custom tooling, and functional testing prototypes.
- Healthcare: Custom implants, anatomical models, and surgical tools.
Future Trends
The field is poised for growth, with ongoing innovations enhancing SLS technology. Areas of interest include advancements in material science, which may expand available options for printing. Moreover, improvements in laser technology could lead to faster and more efficient printing processes.
Comparison with Other Technologies
SLS stands apart from other 3D printing methodsβsuch as Fused Deposition Modeling (FDM) and Stereo Lithography (SLA)βby its approach to layer construction. Each technology has unique benefits and drawbacks, making it crucial for users to select based on specific project requirements. While FDM is often more accessible for hobbyists due to its cost-effectiveness, SLS excels in applications requiring superior mechanical properties.
Prologue to SLS 3D Printing
Selective Laser Sintering (SLS) is a significant advancement in 3D printing technology. It represents a shift in how industries approach design, prototyping, and production. The importance of understanding SLS lies in its versatility and precision, making it a go-to technology for various applications, especially in sectors like aerospace, automotive, and healthcare. With the ability to produce complex geometries, SLS enables designers to create parts that traditional manufacturing methods cannot achieve.
By exploring the fundamentals of SLS, one recognizes its operational principles, materials used, and the advantages it presents over other printing methods. Understanding SLS is essential not only for those engaged in engineering or manufacturing but also for researchers and educators involved in advancing this technology.
The development of SLS technology has led to a variety of benefits, including greater design freedom, faster production times, and the ability to use diverse materials. However, it also brings certain considerations such as equipment costs and material behavior during the sintering process. This comprehensive overview aims to provide clarity and a deep understanding of SLS technology, emphasizing its relevance and impact in today's manufacturing landscape.
Definition of SLS
Selective Laser Sintering is a 3D printing process that uses a laser to fuse powdered materials together to create a solid object. In this method, a laser selectively melts powder particles, allowing them to bond and form a layer. Each layer is added successively to build the final part. This technique enables the creation of intricate designs without the need for support structures. While predominantly used with plastic powders, SLS can also utilize metals and ceramics.
Historical Development
SLS technology was developed in the 1980s by Dr. Carl Deckard at the University of Texas. His pioneering research focused on the application of lasers to sinter powdered materials. The first SLS system became commercially available in the late 1980s. Over the years, advancements in laser technology, powder materials, and machine design have improved SLS processes, making them faster, more reliable, and more cost-effective. This evolution has allowed SLS to grow from a niche technique to a common choice in various industries. Today, companies can harness its capabilities for rapid prototyping and low-volume production, leading to innovations that were previously thought impossible.
How SLS Works
Understanding how Selective Laser Sintering (SLS) works is critical to grasping its significance in the 3D printing industry. SLS distinguishes itself through its process, which involves building parts layer by layer using powdered materials. This section delves into the core principles governing SLS and the specific workflow that enables the production of highly precise and complex components. Each stage plays a vital role in ensuring that the final product meets the desired specifications and quality standards.
Core Principles of Operation
The core principle of SLS lies in its use of a laser to sinter powdered material, binding it together to create a solid structure. This is accomplished by directing a laser beam at the surface of a powder layer, which heats the particles sufficiently to fuse them without completely melting them. This sintering method allows for the creation of complex geometries that are often unachievable with traditional manufacturing methods.
The ability to produce intricate designs directly from a digital 3D model is a significant advantage. The accuracy in layer thickness and the control over powder distribution contribute to the overall dimensional fidelity of the parts produced. Moreover, the layer-by-layer process reduces material waste, aligning with the principles of efficiency and sustainability in manufacturing.
Process Workflow
The SLS process can be broken down into several key stages:
Preparation of 3D Models
The preparation of 3D models is foundational to the SLS process. It involves creating a digital file that contains the specifications for the part being produced. This model must be designed with precision, reflecting the intended geometry and functional requirements.
A key characteristic of preparation is the need for optimization to ensure the model supports the desired attributes of strength and durability. This makes it a popular choice within the context of SLS 3D printing since it directly impacts the efficiency of the printing process and the structural integrity of the final product.
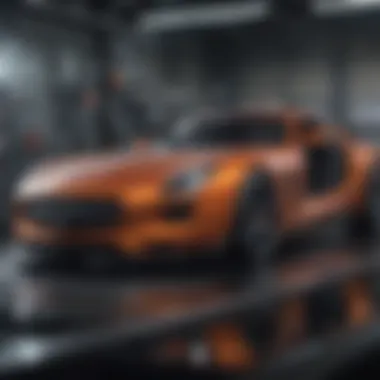
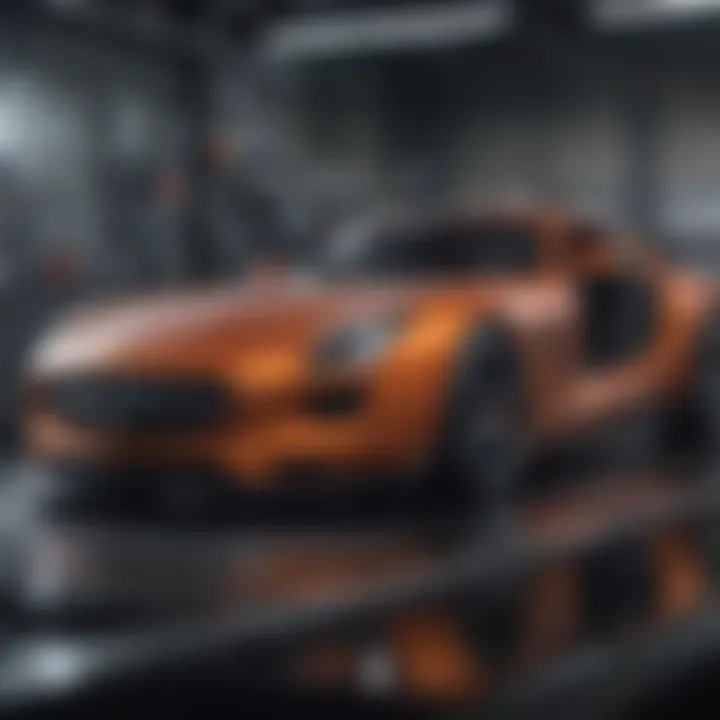
The unique feature of preparing a 3D model includes the possibility to conduct simulations and modifications before actual production. This reduces the risk of errors and minimizes the number of trial prints needed, saving time and costs.
Material Layering
Material layering refers to the systematic application of powdered material during the SLS process. In this stage, a thin layer of powder is spread evenly over the build platform. This forms the basis for the subsequent laser sintering steps.
The key characteristic of this layering process is the uniformity and consistency of the powder distribution. This aspect is vital since it ensures that each layer is of the same thickness, leading to accurate dimensional outcomes in the final piece. For SLS, this is beneficial as it promotes robust layer adhesion and overall part durability.
The unique feature here is the ability to use varied powder materials in a single print job. This flexibility allows manufacturers to employ different materials tailored to specific mechanical properties, although it does pose challenges in terms of process control and quality assurance.
Laser Sintering
Laser sintering is the heart of the SLS technique, where the laser selectively fuses the powdered material. During this phase, the laser scans across the surface of the powder bed, sintering the material only where needed to form the part.
The key characteristic of laser sintering is its precision. The focused energy from the laser enables extremely detailed features to be created, which is why SLS is often chosen for producing complex geometries. This method allows for parts to have very little excess material, making it a cost-effective option.
However, it also has limitations. The sintering process can sometimes lead to thermal stress within the part, potentially impacting its mechanical properties. Careful calibration of laser parameters is crucial to mitigating these risks.
Cooling and Finish Processing
After the sintering process is complete, the part needs to cool down before it can be handled. Cooling and finishing processing involves removing the finished piece from the powder bed and allowing it to return to room temperature.
A key characteristic of this stage is its effect on part quality. Proper cooling minimizes the chances of warping or cracking due to rapid temperature changes. This is important for maintaining the structural integrity of the final product.
The unique feature of cooling and finishing processing includes the potential for post-processing techniques such as polishing or coating. While these processes can enhance surface finish and aesthetic qualities, they may add to the overall manufacturing time and cost.
"The effective operation of SLS relies heavily on both the preparation processes and the precise execution of its workflows."
In summary, the SLS process is a meticulous interplay of multiple stages, from preparing the digital model to post-processing the finished parts. Understanding how SLS operates provides a strong foundation for evaluating its advantages and limitations in various applications.
Materials Used in SLS
Materials used in Selective Laser Sintering (SLS) play a crucial role that influences the overall efficacy and results of the 3D printing process. The choice of materials is not only fundamental to the printing operation but also has significant implications for the properties and applications of the finished products. Understanding the different types of powders and their respective material properties helps in optimizing the SLS process to achieve desirable outcomes.
Powder Types
Plastic Powders
Plastic powders are one of the most commonly used materials in SLS printing. They are favored for their lightweight nature and ability to create complex geometries. The most widely utilized plastic powder is polyamide 12 (PA12), known for its durability and flexibility.
One key characteristic of plastic powders is their ease of use. They melt and fuse well, ensuring that printed parts exhibit good mechanical properties. This makes them a favorable choice for various applications, including prototyping and functional parts that require reliability.
However, the thermal stability of plastic powders can be a disadvantage. They can be prone to warping if not managed properly during printing. Optimal control of printing conditions is essential to mitigate these risks.
Metal Powders
Metal powders are another significant category used in SLS. They are often employed when high strength and thermal resistance are required, such as in aerospace and automotive applications. Materials like titanium and aluminum are popular choices due to their favorable properties.
The key characteristic of metal powders is their capacity to produce parts with superior mechanical properties. The end products can withstand high temperatures and loads, making them ideal for demanding applications.
However, the processing of metal powders generally involves higher costs and requires careful handling due to safety considerations associated with fine metal particles. Thus, while they provide excellent performance, they may not always be cost-effective for smaller-scale projects.
Ceramic Powders
Ceramic powders are less commonly used than plastic and metal, but they hold unique advantages for specific applications. They are appreciated for their excellent thermal stability and corrosion resistance. Materials such as alumina and zirconia are frequently utilized for their beneficial properties in medical and dental fields.
A key feature of ceramic powders is their ability to create parts that exhibit outstanding hardness and rigidity. This characteristic is particularly important in sectors that require precision, such as in the manufacturing of dental implants.
On the downside, ceramic powders can be more challenging to process compared to plastics and metals. They tend to be more brittle than other materials and may require additional post-processing steps to achieve desired mechanical properties.
Material Properties
Thermal Characteristics
Thermal characteristics of materials used in SLS are critical because they affect the way powders behave during the laser sintering process. It is essential that materials can withstand the temperatures generated by the laser without degradation.
Plastic powders, for instance, require precise thermal management to prevent issues like melting or excessive warping. This property is beneficial as it enables the production of stable parts, but it also necessitates close control of the printing environment.
Mechanical Strength
Mechanical strength is a key attribute in determining the suitability of a material for SLS applications. Materials like PA12 and metal powders exhibit high mechanical strength, allowing the printed parts to endure rigorous stresses.
This strength is crucial for functional applications, particularly in automotive and aerospace fields, where safety and performance are paramount. While ceramic powders provide exceptional hardness, they may lack the ductility observed in metallic and plastic powders, which limits their use in certain applications.
Surface Finish
Surface finish of SLS printed parts varies according to the material used. Plastic powders tend to yield smoother surfaces compared to metal powders, which can result in a more refined finish.
A good surface finish is important for aesthetic applications and can also influence the performance of functional components. The need for additional post-processing arises if the surface quality does not meet specified requirements. As such, selecting the right material directly influences the end user's satisfaction with the final product.
"Material selection is critical in SLS as it defines the capabilities and limitations of 3D printed parts in various application domains."
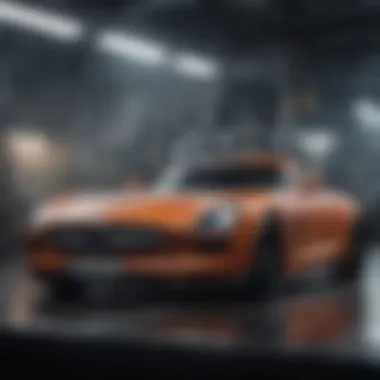
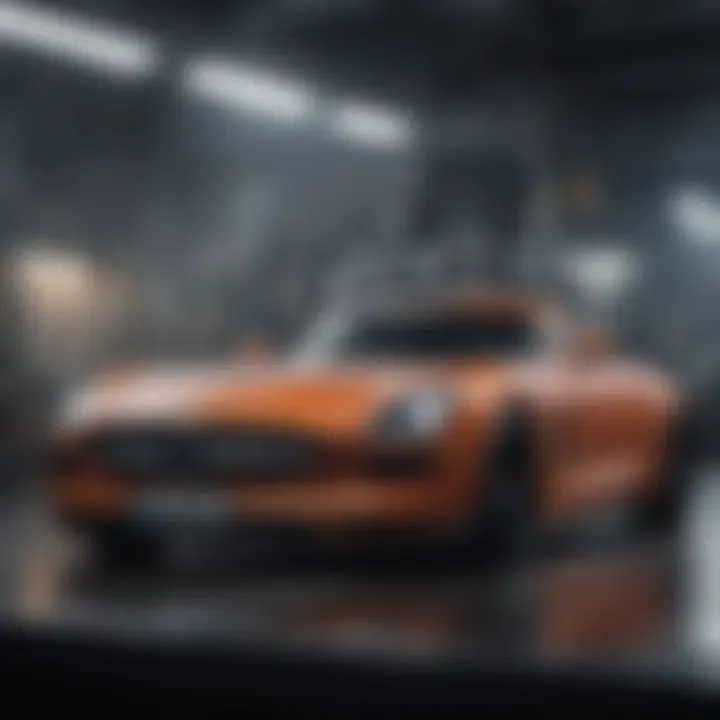
Overall, navigating the intricate landscape of materials used in SLS is essential for achieving optimal performance in 3D printing. The interplay between powder types, their inherent characteristics, and the resulting material properties shapes the reliability and efficacy of SLS technology across diverse industries.
Advantages of SLS 3D Printing
Understanding the advantages of SLS 3D printing is crucial to realizing its potential across various industries. This technology offers numerous benefits that make it a preferred choice for certain applications. Focusing on specific elements such as design flexibility, cost-effectiveness, and the durability of parts enhances comprehension of its contributions to modern manufacturing.
Design Flexibility
One of the most significant advantages of SLS 3D printing is the exceptional design flexibility it provides. Unlike traditional manufacturing methods, SLS allows for the creation of complex geometries that are often impossible to achieve with conventional techniques. This flexibility caters to various requirements in product development, allowing engineers and designers to experiment freely without worrying about constraints imposed by tooling or machining processes.
The ability to create intricate designs also means minimal assembly is required. Many components can be produced as a single, integrated part rather than multiple pieces requiring assembly. This capability not only streamlines production but also enhances performance by eliminating joints and seams that could fail under stress.
More importantly, SLS supports a variety of materials, such as plastics, metals, and ceramics, making it suitable for a wide range of applications. In this regard, designers can tailor their material choice to meet specific demands of their projects.
Cost-Effectiveness
Cost-effectiveness is another key advantage of SLS 3D printing, particularly for short production runs and prototyping. At the outset, initial investment costs for SLS machinery are high. However, when considering the overall manufacturing costs, including material waste, labor, and production time, SLS often proves to be more economical in the long run.
SLS minimizes material waste since unused powder can be recycled in subsequent builds. This attribute significantly lowers material costs over time. Additionally, the shorter lead times associated with SLS can reduce overhead costs.
For many industries, the ability to produce parts quickly and efficiently without incurring high expenses is a substantial advantage. This is particularly critical in sectors like aerospace and healthcare, where rapid prototyping can lead to faster innovations and shorter time-to-market, positioning companies ahead of competitors.
Durability of Parts
The durability of parts produced through SLS is an essential advantage. SLS parts are typically known for their strong mechanical properties, making them suitable for functional applications, not just prototypes. They can withstand significant mechanical loads and resist environmental factors, such as heat or chemicals, depending on the material used.
When compared to parts made with other methods like FDM or SLA, SLS often yields products that are tougher and more resilient. This makes SLS ideal for applications in industries that demand high performance and reliability, such as automotive and aerospace.
Moreover, SLS produces smoother surface finishes compared to some other 3D printing technologies. This characteristic is critical in applications where surface integrity plays a significant role, such as in medical devices or intricate assemblies.
In summary, the advantages of SLS 3D printingβdesign flexibility, cost-effectiveness, and durabilityβunderscore its relevance in modern manufacturing. As industries continue to embrace additive manufacturing, understanding these benefits becomes vital for driving innovations.
Limitations of SLS
Understanding the limitations of Selective Laser Sintering (SLS) is essential for anyone looking to adopt or advance their 3D printing capabilities. While SLS brings numerous advantages, such as design flexibility and strong components, it is crucial to acknowledge the factors that may act as barriers to its broader implementation. This section focuses on key limitations including initial investment costs, post-processing requirements, and material limitations.
Initial Investment Costs
The initial investment in SLS technology can be significant. Purchasing an SLS printer often requires a substantial financial commitment. Prices can vary widely based on the capabilities and specifications of the machine, ranging from tens of thousands to over a million dollars for industrial models. This might deter small businesses or startups from utilizing SLS for their production needs.
Besides the printer itself, there are other costs to consider. These include purchasing raw materials, which can be pricey, and additional machinery for handling and processing powder materials. Furthermore, the need for highly skilled personnel to operate these machines and optimize the printing process can incur additional costs in training and salaries. The total expense may lead many to seek alternative methods of printing that require lower capital.
Post-Processing Requirements
SLS, while efficient, often requires post-processing to achieve the desired finish. After printing, parts typically contain a significant amount of un-sintered powder, which needs to be removed. This process, known as depowdering, can be time-consuming and labor-intensive. Although there are automated machines to aid in depowdering, they can add to the overall investment.
Moreover, the surface finish of SLS parts might not meet industrial standards straight from the printer. Additional treatments, such as sanding or coating, may be necessary to enhance aesthetics or functionality. Thus, while SLS is a powerful method, the post-processing efforts can lead to increased lead times and costs, impacting production schedules.
Material Limitations
Materials used in SLS, primarily powders, face specific limitations. Not all materials are suitable for SLS printing. While thermoplastics are commonly employed, their mechanical properties, such as heat resistance and impact strength, might not always suffice for certain applications. Furthermore, limited availability of high-performance plastics can constrain design options. Specific requirements like biocompatibility for medical applications can also limit material choices.
Additionally, while SLS allows for complex geometries, the surface finish of printed parts often requires modifications to meet cosmetic and functional requirements. This might necessitate materials that are more costly or less readily available in the market.
"Awareness of the limitations of SLS is essential for informed decision-making regarding its use in production and design."
Applications of SLS 3D Printing
Selective Laser Sintering (SLS) has found unique and growing applications in various sectors due to its ability to produce complex geometries and functional parts. The flexibility offered by this technology makes it a valuable tool across industries. In this section, we discuss the importance of these applications, focusing on specifics that underscore the benefits and considerations regarding their use in real-world situations.
In Aerospace Engineering
SLS plays a critical role in aerospace engineering, providing solutions that enhance design and manufacturing processes. The ability to create lightweight, yet strong components is essential in this industry. SLS allows engineers to produce intricate designs that traditional manufacturing methods cannot achieve.
Some specific applications include:
- Production of fuel nozzles for rockets, which benefit from the ability to incorporate cooling channels.
- Creation of lightweight structural components that contribute to overall weight reduction in aircraft, improving fuel efficiency.
- Rapid prototyping of parts, enabling quick testing and iteration.
By utilizing SLS, aerospace companies can drastically reduce lead times and costs related to tooling and machining. However, it is important to consider the material properties required for compliance with stringent aerospace standards.
In Automotive Production
In automotive production, SLS is extensively used for both prototyping and small-scale production. The technology allows manufacturers to produce parts that can withstand harsh conditions, which is vital for vehicle performance.
Applications include:
- Creating prototypes for testing new designs, enabling faster iterations and reduced time to market.
- Production of end-use parts, such as brackets or housings, that require customization and complexity beyond conventional processes.
- Development of tooling for injection molding, providing an economical solution for low-run production.
This technology permits engineers to explore innovative designs without the constraints of traditional manufacturing. The ability to quickly produce parts allows for adapting to changing vehicle models and consumer demands swiftly.
In Healthcare and Medical Device Development
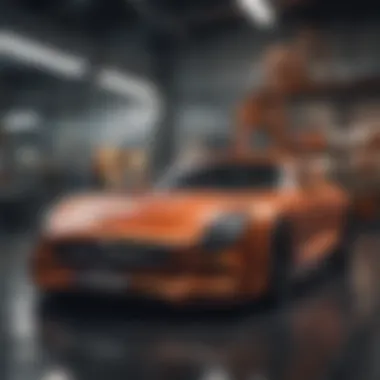
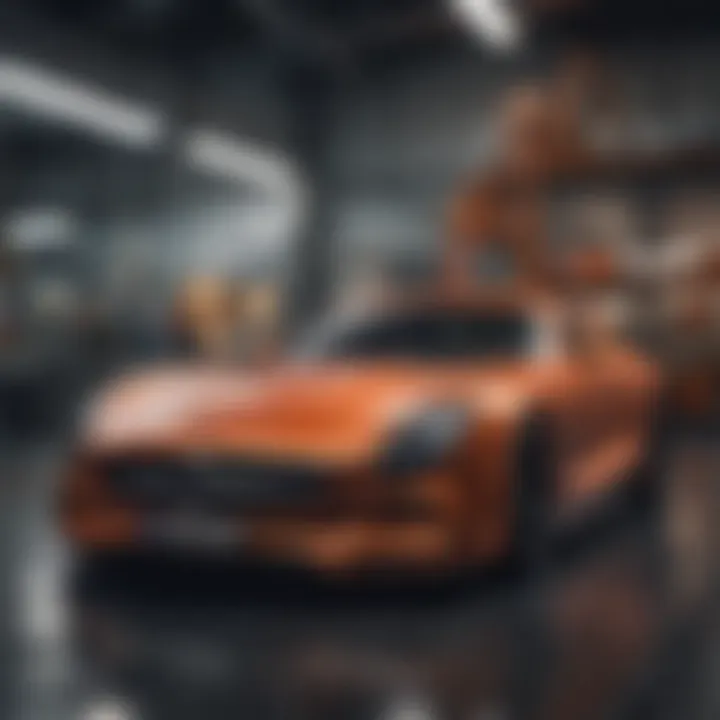
The healthcare sector has increasingly adopted SLS technology for producing customized medical devices and components. One significant advantage is the ability to create patient-specific items that enhance treatment outcomes.
Key applications in healthcare include:
- Fabrication of surgical instruments tailored to specific procedures, which improves precision and efficiency.
- Production of prosthetics and orthotics, allowing for a perfect fit and improved comfort for patients.
- Creation of anatomical models for surgical planning and education, facilitating better surgical outcomes and training.
SLS also supports the development of biocompatible parts, crucial for implants and devices used in direct contact with human tissue.
Comparison with Other 3D Printing Technologies
Exploring the realm of 3D printing is incomplete without understanding how Selective Laser Sintering (SLS) compares to other leading technologies. This comparison highlights vital distinctions in functionality, applications, and limitations that can influence the choice of technology for specific projects. The interplay between different methods provides insight into their respective advantages, ensuring that professionals can make informed decisions based on their specific needs.
FDM (Fused Deposition Modeling)
Fused Deposition Modeling stands as one of the most widely utilized 3D printing techniques. The process involves extruding thermoplastic filament to build objects layer by layer. One significant advantage of FDM is its low cost, mainly due to the affordability of materials and printers. It is user-friendly and often adopted in educational settings.
- Material Options: FDM supports various thermoplastic materials like ABS, PLA, and PETG.
- Applications: Common in prototyping, hobbyist projects, and even some functional parts.
- Surface Finish: FDM typically results in visible layer lines, which may require post-processing for a smoother finish.
However, FDM has limitations in detail and precision compared to SLS. It may struggle with complex geometries that SLS handles more efficiently.
SLA (Stereolithography)
Stereolithography uses an ultraviolet light source to cure liquid resin into hardened plastic. This method excels in producing high-resolution parts with intricate details, making it favorable in industries requiring fine finishing.
- Print Speed: SLA can print faster than SLS, especially for smaller parts.
- Material Variety: Offers a range of photopolymer resins, including flexible and durable options.
- Post-Processing: Often requires washing and curing to remove excess resin, adding to the total time and effort.
The trade-off with SLA is the durability. While the surface finish is superior, the mechanical properties of SLA printed parts may not match those of SLS outputs, especially in high-stress applications.
DLP (Digital Light Processing)
Digital Light Processing is similar to SLA but employs a digital light projector to flash a single image of each layer across the resin vat. This technique can significantly speed up the printing process for large batches of smaller objects.
- Detail and Precision: Like SLA, DLP provides high details and finishes.
- Print Volume: Can produce multiple small parts simultaneously, enhancing productivity.
- Material Behavior: DLP resins tend to have unique characteristics, which may not always align with specific project requirements.
Despite its strengths, DLP may face material limitations similar to SLA, thus narrowing its application scope in comparison to SLS, especially for production parts requiring durability and thermal resistance.
Understanding the nuances between these technologies allows businesses to leverage the most suitable method for their project goals, ensuring efficiency and quality.
Future Trends in SLS Technology
The advances in SLS technology are essential in understanding the future of this printing method. By recognizing these trends, industries can adapt and innovate, ensuring that SLS remains relevant and effective in meeting practical needs. New developments not only improve the efficiency of SLS but also open possibilities for new applications and markets. Innovations in material science, automation, and sustainability will play crucial roles in this evolution.
Innovations in Material Science
Material science is a cornerstone of SLS technology enhancements. Research and development aim to create new powders and composites that can be used in SLS processes. For instance, polymers with enhanced properties like increased strength and flexibility are becoming available. These materials can allow for the production of intricate components with specific mechanical characteristics. Moreover, multi-material capabilities are starting to emerge, leading to the fabrication of complex parts with varying material properties in a single build.
- New Polymers: Innovations lead to higher durability and heat resistance.
- Composite Materials: These combine multiple traits, enhancing performance in specific applications.
- Biodegradable Options: As sustainability gains importance, environmentally friendly materials are being developed.
Research in material science will continue to drive the adoption of SLS across diverse industries, making it a versatile and crucial tool.
Automation and Speed Improvements
Automation within SLS technology is pivoting towards increased efficiency. Streamlined workflows and advancements in machine designs can reduce production time. The integration of robotics in the post-processing phase also plays a vital role. Quick removal of surplus powder and gradual cooling can enhance part quality and minimize manual labor costs.
- Automated Powder Handling: New systems can manage and recycle powder more efficiently, reducing waste.
- Rapid Build Technologies: More sophisticated lasers and optics allow for faster sintering without compromising detail.
- Monitoring Systems: In-process monitoring tools improve quality control, detecting issues in real-time.
Improvements in automation ultimately enhance throughput and scalability, making it attractive for mass production.
Sustainability Challenges and Solutions
As industries prioritize sustainability, SLS technology faces pressure to minimize its environmental footprint. Challenges include energy consumption and powder waste. However, solutions are emerging to address these concerns.
- Energy Efficient Machines: New designs focus on reduced power usage without sacrificing performance.
- Recycling Initiatives: Enhanced methods for recycling unused powder are crucial for reducing waste.
- Life Cycle Analysis: Implementing strong assessment tools can help companies understand and improve the sustainability of their SLS processes.
Investing in sustainable technologies is not only a duty but also a strategic advantage. As users seek ethical alternatives, SLS must adapt to maintain its role in the market.
The future of SLS technology is shaped by innovations in material science, automation advancements, and sustainability practices. Staying ahead requires continual exploration and adaptation in these areas.
Ending
The conclusion of this article holds substantial importance as it encapsulates the core findings surrounding Selective Laser Sintering (SLS) technology. By summarizing the advances and capabilities discussed, the conclusion assists in reinforcing how SLS stands as a significant player in the realm of 3D printing. This section highlights the effectiveness of SLS in producing complex designs with high precision, which is especially relevant in fields such as aerospace, automotive, and healthcare.
Additionally, it serves as a reminder of the advantages and limitations that accompany the adoption of this technology. Understanding these factors is vital for stakeholders in industries considering SLS for their manufacturing processes. The insights provided here urge continuous exploration of advancements, as SLS evolves with innovations in material science and automation, which have potential implications on cost-effectiveness and efficiency.
Ultimately, this articleβs conclusion not only discusses its key points but also invites a deeper appreciation for the nuanced nature of SLS. It provides a framework for students, researchers, and professionals to carry forward their understanding of SLS technology into practical applications.
Summary of Key Points
- Definition and Mechanism: SLS utilizes laser technology to fuse powdered materials, allowing for intricate designs without the need for support structures.
- Material Variety: The technology accommodates a range of materials, including plastics, metals, and ceramics, which enhances its versatility.
- Advantages: Key benefits of SLS include design freedom, durability of parts, and potential cost savings in production.
- Limitations: Challenges such as high initial costs, post-processing needs, and material restrictions must be recognized.
- Applications: SLS has significant applications in industries like aerospace, automotive, and healthcare, showcasing its importance in real-world scenarios.
- Future Trends: Ongoing innovations and sustainability considerations will shape the evolution of SLS technology.
Call to Research
The study of SLS technology may lead to intriguing discoveries that impact various fields. Continued research can explore multiple angles:
- Innovative Materials Forward: Investigating new powder compositions could open doors to enhanced properties and functionalities.
- Enhancing Efficiency: Research focused on optimizing SLS processes can lead to faster production times and lower costs.
- Sustainability Approaches: Addressing the challenges of waste and energy use in SLS can pave the way for more eco-friendly manufacturing practices.
As sectors across the board look for efficient production methodologies, the demand for empirical research on SLS will grow. This exploration will ensure that organizations maximize the benefits of SLS while navigating its limitations.