Understanding Electrical Lamination: Key Principles and Innovations
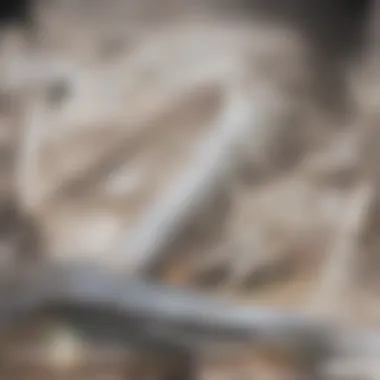
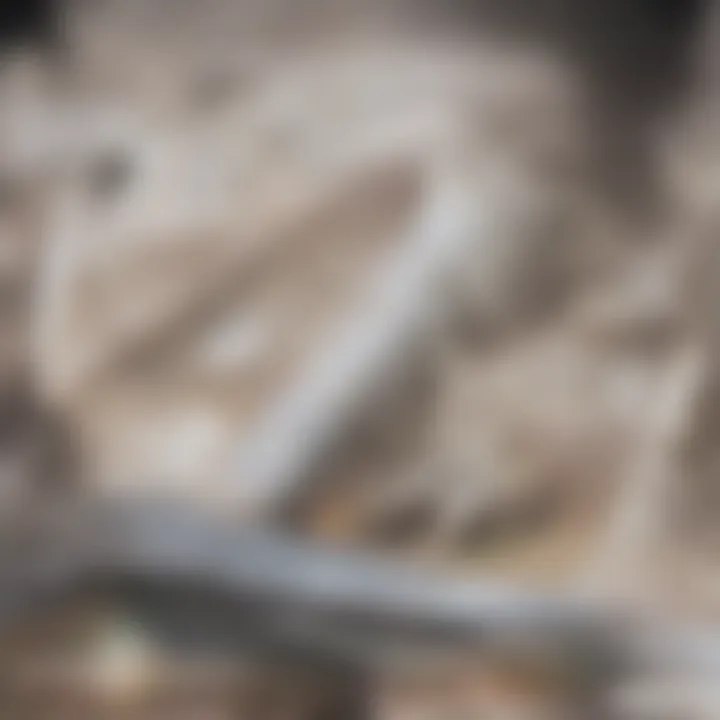
Intro
Electrical lamination is a vital process in the production of electric motors and transformers. Its significance lies in its capacity to reduce energy losses that often occur due to electromagnetic induction. This technique involves layering thin sheets of electrical steel, helping to enhance performance in various applications. The purpose of this article is to provide a detailed examination of the principles, applications, and emerging innovations within the domain of electrical lamination.
Research Context
Background Information
The concept of electrical lamination has been in practice for several decades. It emerged as a solution to combat the energy losses associated with traditional solid cores. The industrial revolution and the subsequent advancements in electrical engineering prompted the need for more efficient methods in energy conversion devices. As a result, understanding the fundamentals of lamination has become essential in designing more effective and durable electrical machines.
Importance of the Study
Investing in the study of electrical lamination is imperative for several reasons. First, it contributes to improving energy efficiency in motors and transformers, which are fundamental in today's industrial applications. The reduction of energy losses not only enhances functionality but also aligns with global initiatives aimed at sustainability and energy conservation. Moreover, with increasing concerns surrounding environmental impact, exploring innovations in lamination processes can offer significant advantages in reducing the carbon footprint associated with energy consumption.
Discussion
Interpretation of Results
Research and empirical data demonstrate that laminated cores can minimize eddy current losses effectively. By using thin sheets and insulating layers, the paths available for induced currents are restricted. As a result, manufacturers can produce motors and transformers that operate at higher efficiencies. The evolution of materials, such as silicon steel and amorphous metals, has further improved the lamination process, yielding components with superior magnetic properties and lower losses.
Comparison with Previous Research
Studies conducted in the past have focused primarily on traditional iron cores. However, recent findings indicate a shift in preference to advanced lamination techniques using more innovative materials. This transition stems from rising energy costs and the demand for greater operational efficiency. Notably, earlier data emphasized the limitations of thick iron cores, while newer research underlines the advantages of laminated systems, demonstrating their significant impact on performance and longevity.
"The shift towards laminated materials reflects a growing awareness of the need for efficiency in the production of electrical machines."
Prolusion to Electrical Lamination
Electrical lamination is integral to the efficiency and performance of electric motors and transformers. At its core, the lamination process involves layering thin sheets of magnetic material, primarily electrical steel, to minimize energy losses during operation. This article aims to provide comprehensive insights into the principles, materials, and innovations that govern electrical lamination, underscoring its significance in various domains of electrical engineering.
Definition and Importance
Electrical lamination refers to the practice of stacking thin sheets of ferromagnetic materials in electrical devices. The key purpose of this technique is to enhance the magnetic efficiency while reducing energy losses from various sources, such as eddy currents and hysteresis. In practical terms, by implementing a laminated structure, manufacturers can create devices that consume less energy and generate less heat, thus improving overall performance and longevity.
The importance of electrical lamination cannot be overstated. In a world increasingly focused on energy efficiency, this technology allows for notably enhanced performance in electric motors, transformers, and inductive components. The higher efficiency translates to lower operational costs and a positive environmental impact. Maximizing output while minimizing energy input plays a crucial role in both commercial and industrial applications.
Historical Development
The concept of electrical lamination has evolved significantly over time. In the early days of electrical engineering, the use of solid metal cores was common, but it became clear that this led to considerable energy losses, particularly due to eddy currents generated within the core material. Recognizing this challenge, engineers began to explore alternatives.
By the late 19th century, the introduction of laminated cores marked a significant advancement. The first applications were in transformers, where reducing heat generation and improving efficiency were vital. Over the decades, electrical lamination practices have continued to advance, influenced by breakthroughs in materials science and manufacturing techniques. Today, the development of high-performance electrical steels and innovative insulating coatings enhances the effectiveness of lamination, making it essential for modern electrical equipment.
"The use of laminated electrical core materials has changed the landscape of electrical engineering, paving the way for more energy-efficient designs."
In summary, the journey of electrical lamination reflects the changing demands of technology and the pursuit of efficiency in energy utilization. Understanding its evolution provides critical insights into current and future trends in electrical applications.
Fundamental Principles of Electrical Lamination
The topic of fundamental principles of electrical lamination is crucial for understanding how laminated materials enhance performance in electrical applications. At its core, electrical lamination is designed to improve the efficiency of devices like motors and transformers. As devices operate, they encounter various magnetic fields and losses, making it essential to focus on the principles that govern these behaviors.
Understanding the underlying magnetic properties, loss mechanisms, and how lamination thickness and configuration affect performance is vital for any effective design. Each of these elements plays a distinct role in reducing energy waste and improving the overall function of electrical systems.
Magnetic Properties
Magnetic properties of materials utilized in lamination affect how much energy can be retained and efficiently transferred. Higher permeability materials are typically favored. They can easily convert electrical energy to magnetic energy and vice versa. This conversion is essential for the efficiency of electrical machinery.
The orientation of magnetic domains significantly influences how well a material performs in actual devices. For example, the grain-oriented electrical steel has better magnetic characteristics than non-oriented steel, enhancing the effectiveness of magnetic circuits in transformers and motors.
Loss Mechanisms
Loss mechanisms define the energy that is wasted during the operation of electrical machines. Understanding these mechanisms helps in reducing wasted energy and improving efficiency. There are three primary loss mechanisms to consider here: core losses, eddy current losses, and hysteresis losses.
Core Losses
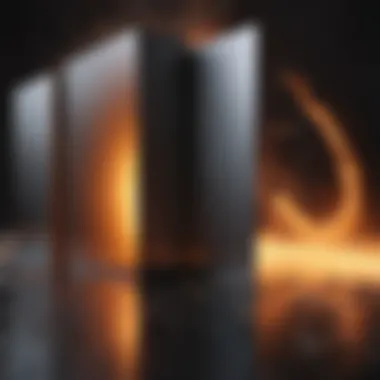
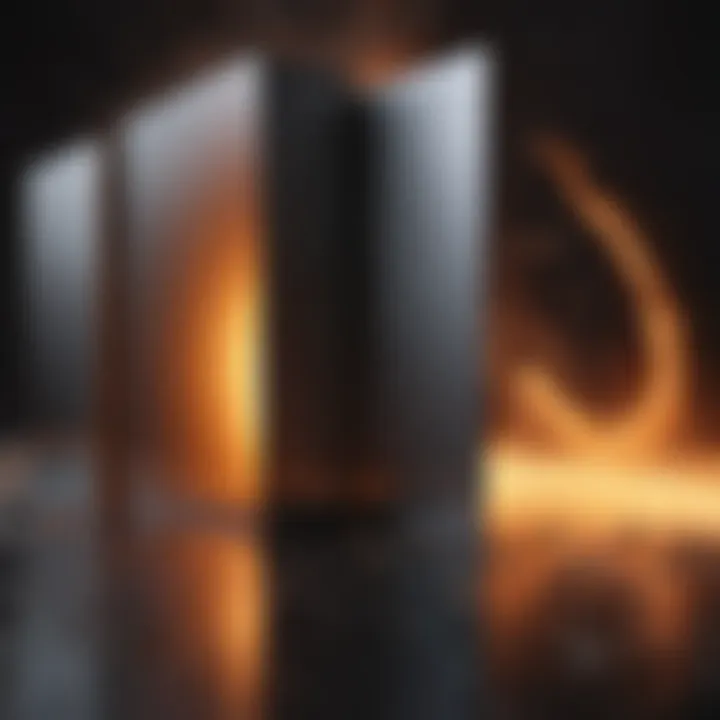
Core losses are critical in the context of electrical lamination. They consist mainly of hysteresis and eddy current losses. Core losses occur due to the lagging of magnetization behind changes in the magnetic field, leading to energy loss in the form of heat.
A significant characteristic of core losses is that they are constant for a given magnetic material and depend on the frequency and maximum flux density. They are particularly a concern when designing motors and transformers because they can significantly reduce efficiency.
To counteract these losses, electrical steels with lower hysteresis coefficients are often utilized. These materials enhance the lifetime and performance of electrical devices.
Eddy Current Losses
Eddy current losses occur when changing magnetic fields induce circulating currents within the laminated materials. These currents produce heat and thus lead to energy dissipation. A primary characteristic of eddy current losses is that they are proportional to the square of the thickness of the lamination sheets.
Using thinner laminations reduces the area available for eddy currents, effectively minimizing these losses. This reduction is a critical reason why manufacturers prefer thinner sheets in production processes.
Hysteresis Losses
Hysteresis losses are another significant factor in the efficiency of electrical machinery. They arise from the resistance of magnetic materials to changing magnetization. The area within the hysteresis loopβgraphically representing the relationship between the magnetic field strength and magnetic flux densityβindicates energy loss.
The cycle of magnetization and demagnetization of the material results in heat generation, contributing to energy losses. Understanding how to select materials with smaller hysteresis loops provides an opportunity to enhance efficiency in electrical applications.
Lamination Thickness and Configuration
Lamination thickness and configuration directly influence the performance of electrical devices. Thicker laminations usually increase eddy current losses, reducing appealing performance.
Conversely, thinner laminations allow for higher efficiency due to reduced losses, but the balance of mechanical strength and ease of manufacture must also be considered.
In summary, the fundamental principles of electrical lamination focus on the interactions of magnetic properties, loss mechanisms, and lamination configuration, each playing a vital role in enhancing the efficiency and functionality of motors, transformers, and other electrical devices. Understanding these principles is essential for the development of more efficient electrical technologies.
Materials Used in Electrical Lamination
Understanding the materials used in electrical lamination is crucial for optimizing the design and performance of electric motors and transformers. The choice of materials directly affects the efficiency, performance, and longevity of these components. As industries become more energy-conscious, selecting the appropriate lamination materials is a key factor in achieving significant energy savings and emissions reductions.
Electrical Steel
Electrical steel is one of the primary materials used in the lamination process. This material, often silicon steel, is designed specifically to have high magnetic permeability and low hysteresis losses. The addition of silicon improves the electrical resistivity of the steel, which enhances its performance by reducing eddy current losses. High-quality electrical steel can maintain its magnetic properties even after prolonged use, which is essential in high-efficiency motors and transformers.
There are different grades of electrical steel available, such as grain-oriented and non-grain-oriented. Grain-oriented steels are preferred for applications with strong magnetic fields, as they allow for better magnetic alignment. Non-grain-oriented steels, on the other hand, are more suitable for applications where the magnetic field direction changes, such as in some electric motor designs.
The manufacturing process of electrical steel also plays a significant role in its performance. Techniques like cold rolling and annealing give the steel its desirable magnetic properties. Higher thicknesses may lead to increased losses, hence manufacturers focus on optimizing thickness for specific applications.
"The selection of proper electrical steel is pivotal for minimizing losses and maximizing the performance of electrical devices."
Insulating Coatings
Insulating coatings are another critical component in electrical lamination. They serve several essential purposes, notably separating the laminated sheets to reduce eddy currents. By preventing physical contact between the steel layers, these coatings help maintain the integrity of each lamination, ultimately contributing to reducing core losses.
The most common materials for insulating coatings are epoxy, varnish, and phenolic compounds. Each of these materials offers different properties, and the choice often depends on the specific application. For instance, epoxy coatings provide superior resistance to moisture and mechanical damage, making them ideal for outdoor and high-stress environments.
Beyond their primary insulating function, coatings also contribute to the durability and longevity of laminated components. They can offer thermal stability and corrosion resistance, ensuring that the electrical devices operate effectively under various environmental conditions. Selecting the right coating is as important as the choice of the underlying laminate material, as it affects the overall performance and reliability of the electrical device.
In summary, the materials used in electrical lamination, primarily electrical steel and insulating coatings, play a pivotal role in enhancing the efficiency of electrical devices. By understanding and applying the appropriate materials, engineers and manufacturers can significantly impact energy consumption and performance.
Manufacturing Processes of Electrical Lamination
Manufacturing electrical lamination involves critical processes that significantly affect the efficiency and performance of electrical devices. Proper execution of these processes ensures minimal energy losses and improved functionality in applications such as electric motors and transformers. This section will delve into two key processes: sheet cutting techniques and stacking and bonding methods. Each process holds importance in achieving optimal electrical characteristics and durability of laminated materials.
Sheet Cutting Techniques
Sheet cutting is the first step in preparing electrical laminations. Precision in this cutting process is crucial as it determines the final dimensions and usability of the laminations. Various techniques can be employed in this stage, including:
- Die Cutting: This method uses a specialized die to cut the lamination sheets into desired shapes. It allows for high precision and is commonly used for large production runs.
- Laser Cutting: This technique uses focused laser beams to cut steel sheets. It provides exceptional accuracy and is often used when complex shapes are required.
- Waterjet Cutting: Utilizing high-pressure water jets, this method can cut through various materials. It is advantageous for its ability to cut without causing heat-related distortions.
Selecting the proper cutting technique affects the edge quality and surface finish of the laminated sheets, which then influences the magnetic properties of the final product. A clean cut is essential to reduce any potential loss of energy during operation. Additionally, advancements in technology have led to automated systems that enhance efficiency and reduce human error during this phase of manufacturing.
Stacking and Bonding
Once the laminations are cut, the next step involves stacking and bonding. This process is vital for assembling the laminated sheets into cores that will be used in various electrical applications. The following considerations are important:
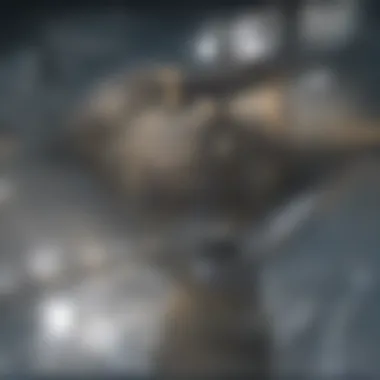
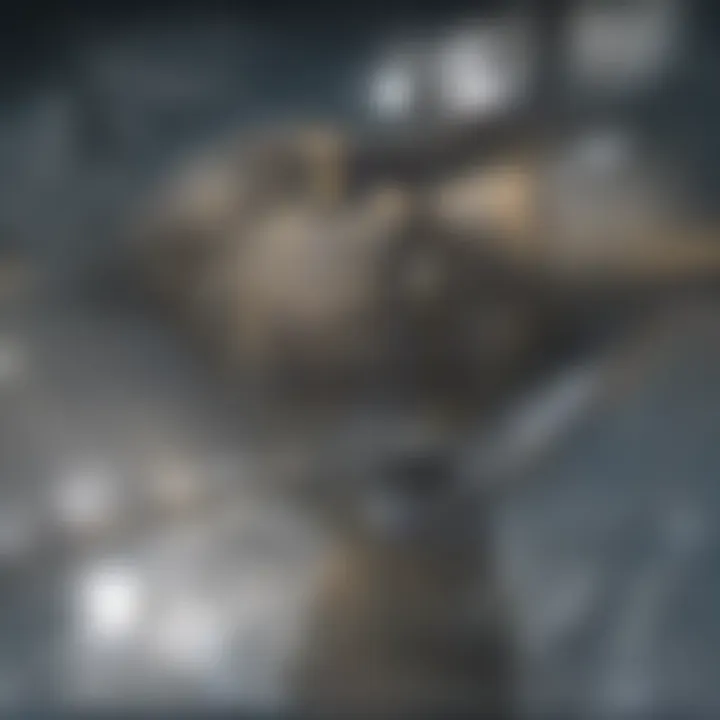
- Alignment: Proper alignment of the sheets during stacking ensures that the magnetic paths are optimally established. Misalignment can lead to increased losses and reduce core performance.
- Bonding Methods: The bonding of sheets can be achieved through adhesive bonding or mechanical fastening. Adhesive bonding offers a uniform connection across large areas, while mechanical fastening can facilitate easier assembly and disassembly for maintenance purposes.
- Compression Methods: Applying pressure during bonding enhances the cohesiveness of the stack. This step is vital to avoid air gaps that could impact magnetic performance.
The integrity of the laminated core is determined by how well they are stacked and bonded. Poor bonding may lead to inefficiencies in operation, while robust bonding can improve durability and performance in demanding environments.
Proper manufacturing processes are essential for the effective performance of electrical lamination, impacting energy efficiency and longevity of devices.
In summary, both sheet cutting techniques and stacking and bonding methods are essential processes in the manufacturing of electrical lamination. Mastery of these processes leads to improved efficiency, reduced losses, and the production of high-quality laminated materials suitable for varied applications in the electrical industry.
Advantages of Electrical Lamination
Electrical lamination, an essential process in the production of electrical devices, presents several significant advantages that enhance performance and efficiency. Understanding these benefits is crucial for researchers and professionals in related fields. This section delves into two primary advantages: reducing energy loss and improving efficiency.
Reducing Energy Loss
One of the primary advantages of electrical lamination is its ability to reduce energy loss in magnetic components. Energy losses mainly occur due to various mechanisms like iron losses and hysteresis losses. By laminating the core, manufacturers can substantially mitigate these losses.
The concept is based on reducing the path for eddy currents, which are loops of electrical current that can create significant heat and loss of energy. Thinner laminated sheets restrict the flow of these currents, thereby diminishing their impact. Also, using high-grade electrical steel with insulating coatings further enhances this effect.
"Laminating the core can result in a reduction of energy loss by up to 50% compared to solid steel forms."
Additionally, this reduction in energy loss translates to lower operating temperatures, which further increases the longevity and reliability of electric motors and transformers. The overall performance enhancement resulting from this reduction is a vital argument for the widespread use of laminations in electrical applications.
Improving Efficiency
Improving efficiency is another substantial advantage of electrical lamination. By optimizing the design of electrical cores through lamination, devices can operate with less energy input while providing the same output. This aspect is particularly noteworthy in applications such as electric motors and transformers, where efficiency is paramount.
Laminated cores enable better control of magnetic flux. This means that, under operational conditions, magnetic materials can achieve higher magnetic flux densities more effectively. The result is an improved power-to-weight ratio in motors, which is highly desirable in industries where performance and weight are critical considerations.
Furthermore, efficiencies can also lead to a reduction in energy consumption, aligning well with environmental goals. Enhanced efficiency means lower energy costs, which can significantly impact both production and operational budgets.
In summary, the advantages of electrical lamination, particularly in reducing energy loss and improving efficiency, underscore the necessity of this process in the development of modern electrical devices. As industries continue to seek ways to enhance performance while minimizing energy consumption, these benefits will play a crucial role in shaping future innovations within the field.
Applications of Electrical Lamination
Electrical lamination is integral in multiple sectors, particularly where efficiency and performance are paramount. Laminated materials play a vital role in numerous electrical devices. The deployment of lamination in various components minimizes energy loss and enhances functionality. Its applications are extensive, ranging from electric motors to transformers and inductive components.
Electric Motors
In electric motors, lamination is used to improve the magnetic efficiency of the core. Laminated cores reduce eddy currents, which can contribute to energy losses. Electrical steel sheets are commonly laminated to achieve this. The thickness of each lamination affects both the performance and efficiency of motors. A well-constructed laminated core ensures that energy conversion is optimal. Additionally, it helps in reducing overheating, which can affect the overall lifespan of the motor. Thus, proper lamination not only boosts the efficiency but also increases the reliability of electric motors.
Transformers
Transformers heavily rely on laminated cores to operate efficiently. The primary purpose of lamination in transformers is to minimize losses caused by magnetic flux. By using laminated electrical steel, the design limits energy dissipation more effectively compared to solid cores. The arrangement of the laminations can affect the transformer's performance significantly. The insulation between layers also plays a crucial role in preventing eddy currents. This careful engineering ensures that transformers can handle varying loads while maintaining efficiency. Owing to these characteristics, laminated transformers are essential in power distribution networks.
Inductive Components
Inductive components, such as inductors and chokes, utilize lamination to enhance performance. Lamination is critical in these devices to manage losses while maintaining inductance. By employing laminated cores, manufacturers can improve saturation resistance and minimize losses. Inductive components contribute crucially to power conversion and signal processing in electronic circuits. The quality of the lamination directly influences the overall efficiency of these components. As a result, innovations in lamination techniques continue to permeate this field, driving enhanced designs and applications.
Electrical lamination not only advances performance in electric motors and transformers but also enables innovations in inductive components.
Innovations in Electrical Lamination Techniques
Innovation in the field of electrical lamination is vital to advancing manufacturing processes. As demand increases for energy-efficient motors and transformers, the development of new techniques becomes essential. Innovations lead to better performance, reduced costs, and lower environmental impacts. Understanding these modern advancements is crucial for anyone involved in research or application of electrical lamination.
Advanced Materials
The exploration of advanced materials in electrical lamination is reshaping how electrical components are designed and produced. These materials include high-grade silicon steel and other alloy compositions. Silicon steel, for instance, displays improved magnetic properties and lower core losses compared to traditional materials. This improvement translates to more efficient electrical machines, which is a significant benefit for the industry.
In addition, new materials often possess better insulating properties, enhancing performance and lifespan of laminated products. Specialized coatings, for example, provide enhanced protection against corrosion and mechanical stress. Thus, choosing the right advanced material is pivotal for optimizing performance across various applications.
Nanotechnology in Lamination
Nanotechnology represents a groundbreaking innovation in the electrical lamination space. By manipulating materials at a molecular level, researchers can enhance properties like magnetic permeability and thermal conductivity. This development can result in much thinner lamination layers without sacrificing performance. Thinner lamination will mean reduced eddy currents and hysteresis losses, further improving energy efficiency.

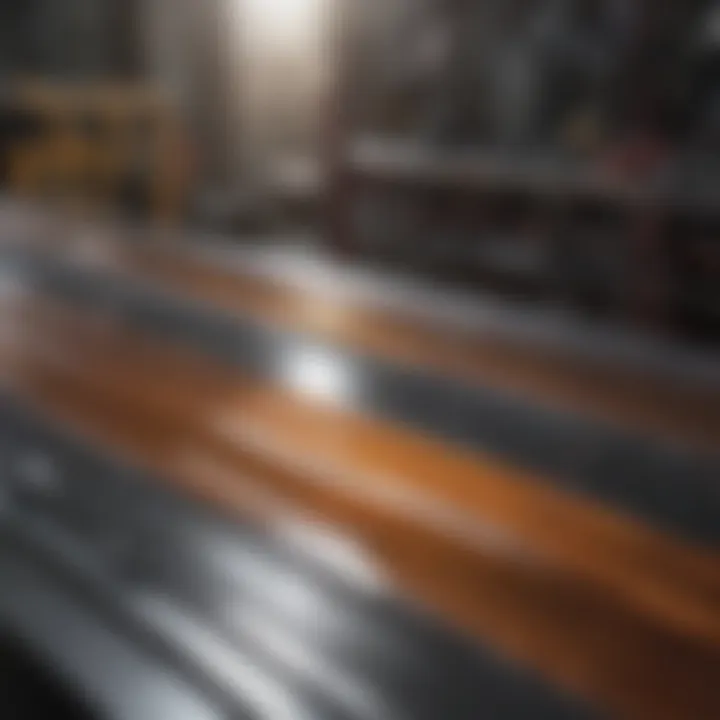
Moreover, nanotechnology facilitates the integration of multifunctional features into laminates. For instance, laminated components can potentially gain improved heat resistance or self-healing capabilities. These advancements reflect the growing trend towards smart materials that can adapt to varying operational conditions.
"The incorporation of nanotechnology into electrical lamination not only enhances performance but also opens doors for new applications that were previously infeasible."
In summary, innovations in electrical lamination techniques, including advanced materials and nanotechnology, are essential to meet the needs of contemporary electrical devices. Emphasis on these innovations will lead to better efficiency, reduced energy loss, and longer service life of electrical components. This makes it a key area to watch for future advancements.
Environmental Impact of Electrical Lamination
The environmental implications of electrical lamination are increasingly significant in todayβs industrial landscape. As the world grapples with energy consumption and sustainability, understanding how electrical lamination contributes to both resource efficiency and environmental impacts becomes crucial. This section delves into two vital areas: sustainability considerations and recycling practices surrounding laminated materials.
Sustainability Considerations
Sustainability in electrical lamination encompasses various factors, including resource usage, energy efficiency, and the lifecycle of products. The manufacturing of laminated electrical components often involves materials that may have substantial environmental footprints if not managed properly. Materials like electrical steel, often used in lamination, require energy-intensive processes for extraction and refinement.
To mitigate these issues, manufacturers are increasingly focusing on approaches that reduce waste and energy consumption during production. This can include:
- Optimizing processes: Improving techniques in cutting and stacking can lower energy use.
- Material efficiency: Using thinner laminations can reduce material needs while still maintaining performance.
- Adopting cleaner energy sources: Transitioning to renewable energy systems for manufacturing can lessen the overall carbon footprint.
Furthermore, the design of laminated products often emphasizes durability and long-term functionality, which can reduce the frequency of replacements, ultimately benefiting the environment.
Recycling of Laminated Materials
Recycling laminated materials is an essential aspect of reducing waste and promoting circular economy principles. The challenges associated with recycling laminated electrical components stem from the layering of materials, which can complicate separating steel from insulating coatings. However, advancements in recycling technology have made it viable to reclaim valuable materials from such components.
Some key points in the recycling process include:
- Separation Techniques: Innovations like mechanical processes or chemical treatments improve efficiency in extracting pure metals from laminated structures.
- Recovery Rates: Effective recycling can lead to high recovery rates, ensuring that significant portions of the materials are reused.
- End-of-Life Management: Establishing comprehensive programs encourages manufacturers to take responsibility for the products at the end of their life, fostering a proactive approach to recycling.
"The recycling of laminated electrical materials not only conserves resources but also significantly reduces the environmental impact of electrical engineering industries, making it a priority area for future innovations."
Future Trends in Electrical Lamination
The field of electrical lamination is undergoing significant transformation, driven by technological advancement and increasing energy efficiency standards. Understanding these future trends is crucial for professionals seeking to remain competitive in an evolving market. New techniques and materials are emerging, which not only enhance performance but also reduce the environmental footprint of lamination processes. The focus now is on integrating smart materials and automation, which are expected to revolutionize manufacturing methods.
Smart Materials
Smart materials offer exciting possibilities in the realm of electrical lamination. These materials can respond to external stimuli such as temperature, stress, and magnetic fields. The potential for smart coatings on electrical laminates is profound, providing self-regulating attributes that can minimize energy loss further.
The benefits of using smart materials include:
- Enhanced performance: They can adapt to conditions dynamically, improving efficiency.
- Durability: Smart materials often possess stronger resistance to wear and corrosion.
- Cost effective: They may reduce long-term operational costs through improved energy management.
Examples of smart materials that could see use in electrical lamination include shape memory alloys and piezoelectric materials. The research on these materials is still in progress, but their incorporation can lead to significant innovations in motors and transformers.
Automation in Manufacturing
The push towards automation in manufacturing aligns with both efficiency and precision goals. Automated processes in electrical lamination can streamline production lines, significantly reducing cycle times and human error. The integration of robotics and machine learning algorithms ensures consistent quality and quick responses to manufacturing challenges.
Key considerations in automation include:
- Increased output: Automation tends to lead to higher production rates.
- Quality control: Machines can apply consistent pressure and precision that often surpass human capability.
- Flexibility: Adaptability in production lines allows manufacturers to shift quickly between different products.
Moreover, implementing Industry 4.0 principles in lamination factories provides opportunities for real-time monitoring and data collection, which is invaluable for process optimization.
In summary, the future trends in electrical lamination indicate a shift towards smart materials and automated manufacturing. These innovations promise to enhance energy efficiency, bolster performance, and improve the sustainability of products. As research continues and technology evolves, the potential for more sophisticated applications remains vast, ensuring the relevance of electrical lamination in future energy solutions.
Culmination
The conclusion of this article serves a pivotal role in encapsulating the essential insights about electrical lamination. It distills the key concepts discussed throughout the article while emphasizing the significance of electrical lamination in current technology. Understanding the principles and applications of electrical lamination is crucial for advancing energy efficiency in electric motors and transformers. This knowledge equips professionals and researchers with the tools to innovate and improve existing technologies.
Summary of Key Points
The core takeaways from this exploration of electrical lamination include:
- The definition and importance of electrical lamination in reducing energy losses, particularly in electric motors and transformers.
- Insights into the fundamental principles, including magnetic properties and loss mechanisms that impact the efficiency of laminated materials.
- The selection of key materials used in lamination, notably electrical steel and insulating coatings, which significantly influence performance.
- An overview of manufacturing processes like sheet cutting, stacking, and bonding, crucial for creating high-quality laminated products.
- A broad range of applications across industries highlighting the versatility and significance of laminated materials.
- Recent innovations that hint at the future direction of electrical lamination, including advancements in materials and manufacturing automation.
- Environmental considerations, including sustainability and recycling, are becoming increasingly relevant in research and development.
Significance for Future Research
The field of electrical lamination is poised for significant advancement as industries shift towards more energy-efficient technologies. Future research bears the potential to decrease energy losses further and enhance performance. Key areas may include:
- Developing smart materials that could adapt properties according to electric demand or operational conditions.
- Integration of nanotechnology in lamination processes, potentially introducing new materials with superior magnetic properties and reduced losses.
- Exploring automation in manufacturing to streamline production and ensure high-quality standards consistently.