Sintered PTFE Sheets: Properties and Applications
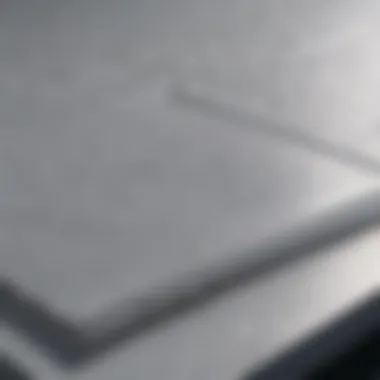
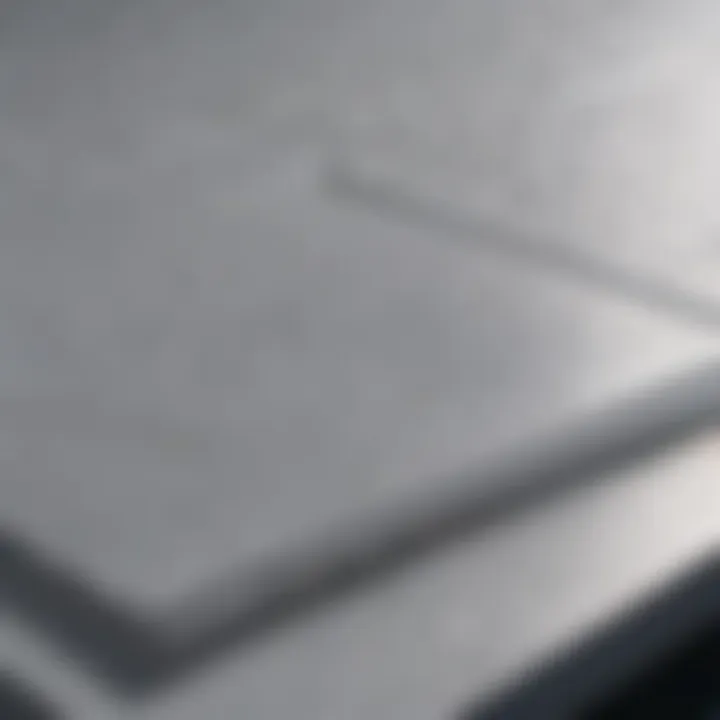
Intro
Understanding sintered polytetrafluoroethylene (PTFE) sheets is key for many industries looking for durable and highly resistant materials. PTFE is widely known for its exceptional chemical resistance, thermal stability, and non-stick properties. These characteristics make sintered PTFE sheets a valuable asset in applications ranging from aerospace to electronics.
This article delves into its properties, manufacturing processes, and practical uses while giving insight into its comparisons with alternative materials.
Research Context
Background Information
In the realm of materials science, sintered PTFE has carved a niche due to its unique capabilities. Originally discovered in the 1930s, PTFE finds its roots in the chemical structuring of tetrafluoroethylene. The sintering process enhances its mechanical properties by creating a solid structural matrix. This process occurs when PTFE powder is heated, thus causing particles to adhere without melting, retaining its distinct molecular composition.
The applications of this material are diverse: from gaskets to bearings, it has found its way into various sectors.
Importance of the Study
The evaluation of sintered PTFE sheets brings to light not only their advantages but also the potential limitations. By studying these attributes, professionals can make informed decisions about material selection, ultimately impacting efficiency and efficacy in various applications. Moreover, understanding the economic implications is crucial for industries looking to optimize production costs and maintain performance.
Discussion
Interpretation of Results
The survey of sintered PTFE reveals several compelling advantages. Its low friction coefficient allows it to outshine many other materials where wear and tear are critical concerns. Additionally, this material exhibits remarkable thermal insulation properties, often being used in high-temperature environments without degrading. However, it is essential to note that despite its strengths, certain applications may expose it to stress levels that could compromise its integrity over time.
Comparison with Previous Research
Previous investigations into PTFE have highlighted similar trends regarding its performance; however, recent studies emphasize the evolving manufacturing techniques that enhance its properties further. Research indicates that newer sintering methods can produce sheets with improved mechanical strength and reduced porosity. Even so, comparisons with materials such as nylon or rubber demonstrate that while PTFE excels in specific categories, it may not be the best choice universally.
"Sintered PTFE holds its ground against competitive materials when it comes to chemical resistance and moisture uptake, albeit at a higher cost in some cases."
As the discourse around advanced materials evolves, continual assessments of sintered PTFE’s features and advantages will provide critical insights for researchers and practitioners alike. This understanding is paramount for navigating the technological advancements and economic factors that shape today’s material choices.
Prologue to Sintered PTFE Sheets
The topic of sintered polytetrafluoroethylene (PTFE) sheets stands at the intersection of material science and practical application across numerous industries. Understanding these materials is crucial as they possess unique properties that set them apart from other common plastics. Sintered PTFE is known not just for its high resistance to chemicals but also for its remarkable thermal stability and low friction characteristics. These attributes make it an essential component in sectors ranging from manufacturing to food processing.
One might wonder why the focus on sintered PTFE sheets is warranted. Firstly, the growing demand for materials that can withstand extreme conditions without deteriorating is constantly on the rise. Secondly, as industries continue to innovate, materials like PTFE are being re-evaluated for new applications, which could lead to breakthroughs in efficiency and product longevity. This section serves as an essential primer, offering insights into what exactly sintered PTFE is, how it has evolved over time, and why it is a preferred choice among professionals dealing with demanding environments.
Definition and Composition
Sintered PTFE is a solid form of polytetrafluoroethylene produced through a specific manufacturing process involving heating and compression. At its core, PTFE is a polymer made from tetrafluoroethylene, a compound that serves as the building block. The sintering aspect refers to the method of compacting and forming PTFE powder into a solid sheet without melting it. This results in a porous structure that retains the beneficial properties of PTFE while enhancing its strength and durability.
The composition primarily consists of carbon and fluorine atoms, forming a stable lattice structure. This configuration contributes to its non-reactivity with most chemical agents, making it a popular choice in corrosive environments. Furthermore, its unique structure enables superior thermal stability and mechanical strength, even at elevated temperatures.
In summary, sintered PTFE is not just a mere plastic; its composition and manufacturing process afford it a set of distinct characteristics that make it indispensable in many advanced applications.
Historical Background
The origins of polytetrafluoroethylene date back to the early 20th century. Discovered in 1938 by Dr. Roy Plunkett, PTFE was initially utilized in specialized industrial contexts. However, it was during the 1950s that its potential began to burgeon, particularly after the development of sintered processes which further enhanced its durability. Sintered PTFE quickly found its niche in sectors demanding resilience against corrosive substances, high temperatures, and wear.
As industries progressed, so did the applications of sintered PTFE sheets. From the early uses in electrical insulation and seals, today it has evolved into a multifaceted material used in diverse fields such as aerospace, healthcare, and food processing. Its versatility continues to foster innovations, leading to new uses and driving research into its properties and potential further.
This foundation highlights the importance of understanding the historical context of sintered PTFE sheets, as it informs present-day applications and guides future explorations into this remarkable material.
Manufacturing Process of Sintered PTFE
The manufacturing process of sintered PTFE sheets plays a pivotal role when assessing their quality, usability, and application across various industries. Understanding how these sheets are made shines a light on the intricate relationship between the production methods and the distinct features these materials offer. Effectively, mastering the conversation around this topic not only informs best practices for industries but also influences design choices and further research avenues. As we delve into this section, we'll explore the essential components that underpin the manufacturing process, including raw material selection, the sintering techniques employed, and stringent quality control measures.
Raw Material Selection
Selecting the right raw materials is crucial in the production of sintered PTFE sheets. The main ingredient here is polytetrafluoroethylene resin, part of a family of materials that exhibit unparalleled chemical resistance. The purity of the PTFE resin used can significantly affect the overall qualities of the finished product. Typically, manufacturers will seek PTFE that has a high molecular weight, as it contributes to improved mechanical strength and thermal stability. Moreover, the choice of additives—if any—can help tailor the final properties of the material for specific applications.
In addition to the main resin, careful attention should be paid to the initial processing aids, which can include lubricants that unpack the resin easier and enhance its flow during manufacturing. However, using these aids must be done judiciously, balancing their benefits against the potential for contamination in the final product.
Sintering Techniques
The heart of creating sintered PTFE sheets lies in the sintering techniques. Sintering can be seen as a dance of heat and pressure that melds loose powder into a cohesive, functional sheet. There are a few primary methods employed in this process.
- Conventional Sintering: This involves heating the PTFE powder at carefully-controlled temperatures, allowing the particles to bond and solidify into sheets. With precise temperature regulation, this can yield dense materials with desirable properties.
- Compression Molding: In this technique, PTFE resin powder is compressed and then heated to fuse it into a solid sheet. This approach efficiently utilizes the material and can result in sheets of varying thickness, catering to diverse needs.
- Injection Molding: Although less common for PTFE, this method may also be utilized, especially for complex shapes and forms. It involves injecting molten PTFE into molds, which is quite different from sintering but worth mentioning due to its versatility.
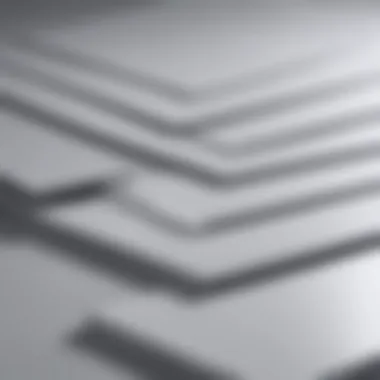
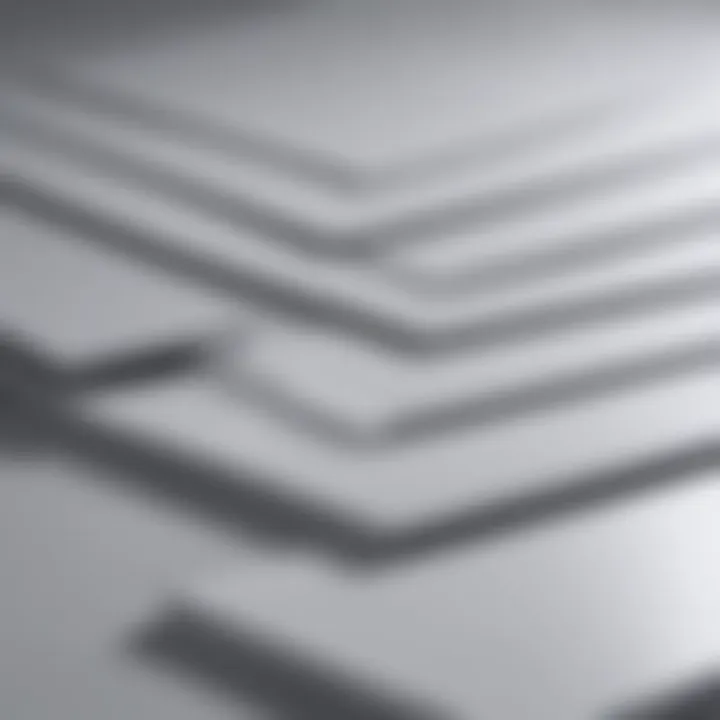
Each method carries its own set of advantages and challenges. For instance, compression molding generally offers better dimensional tolerances, while conventional sintering tends to produce more uniform material. Therefore, manufacturers often assess the specific requirements and constraints of their application before determining the appropriate technique.
Quality Control Measures
When it comes to production, ensuring the quality of sintered PTFE sheets is non-negotiable. Implementing rigorous quality control measures is essential for maintaining the integrity of the product and meeting industry standards. Various checks are carried out through the manufacturing process, from the initial raw material evaluation to the final product inspection.
- Material Testing: This includes analyzing the physical properties of the PTFE resin before production. Tests for particle size distribution or thermal stability indicate how suitable the material is for sintering.
- In-Process Inspections: Monitoring each stage of the manufacturing process helps identify issues before they escalate. This can involve monitoring temperature ranges during sintering or checking for consistency in the sheet thickness.
- Final Product Testing: After the sheets are produced, they undergo a series of tests, including tensile strength, chemical resistance, and thermal properties. These tests are meant to ensure that the final output meets or exceeds the expected standards.
Moreover, documenting the manufacturing processes and maintaining traceability of the materials used supports compliance with industry regulations. This diligence reinforces customer confidence and enhances the reputation of manufacturers in competitive markets.
In sum, the manufacturing process for sintered PTFE sheets is a blend of science, art, and quality assurance, directly impacting the material's performance across a spectrum of applications.
Unique Properties of Sintered PTFE Sheets
The unique properties of sintered PTFE sheets are fundamental in understanding how this material stacks up against alternatives in various applications. Their distinctive characteristics inform not just their functionality but also influence decision-making in material selection across industries. From outstanding chemical resistance to excellent thermal stability, the myriad properties of PTFE sheets make them an indispensable material in challenging environments.
Chemical Resistance
One of the top-notch attributes of sintered PTFE sheets is their unrivaled chemical resistance. PTFE is known for its capacity to withstand aggressive substances, including strong acids and bases. Because of this property, it emerges as a critical option in sectors that deal with corrosive materials, like the chemical manufacturing or pharmaceutical industries.
For instance, in a pharmaceutical lab, sintered PTFE sheets can be utilized for lining containers that hold caustic solutions without degrading. This protectiveness extends to many solvents, ensuring longevity in various applications. With PTFE, you can bet that the components will resist corrosion dramatically longer, helping reduce replacement costs and downtimes.
"The exceptional resistance to corrosion and chemicals makes sintered PTFE sheets a favorite for demanding applications."
Thermal Stability
When it comes to thermal stability, sintered PTFE sheets are a cut above the rest. These sheets can perform effectively within a wide temperature range, typically from -200°C to 260°C. This ability ensures that they maintain operational efficiency without losing structural integrity, even under fluctuating thermal conditions. For example, in industrial machinery where high heat is a factor, using sintered PTFE sheets can avoid many issues related to thermal expansion and contraction, thus prolonging equipment lifespan.
Moreover, the thermal properties help in applications involving electrical insulation, which is also much needed for reliability in electronics and other high-performance environments. Choosing PTFE means you’re betting on resilience against heat – a crucial game changer in many scenarios.
Mechanical Strength
Though PTFE is often perceived as a softer material in the plastics family, sintered PTFE sheets do possess a commendable mechanical strength. When discussing applications that require robust physical properties, these sheets can hold their own remarkably well. Their ability to withstand significant mechanical loads while remaining flexible makes them an alluring option in the manufacturing of seals, gaskets, and bushings.
Now, it’s essential to keep in mind that while PTFE has impressive compressive strength, it can exhibit lower tensile strength. This quality can be both a benefit and a limitation, depending on the intended application. Using sintered PTFE sheets where flexibility and resistance to wear are needed can lead to enhanced functionality, but utilizing them for structural applications must be approached with caution.
Surface Properties
Sintered PTFE sheets also stand out due to their superior surface properties. The non-stick surface is what many users find appealing—think about kitchen equipment or industrial machinery—that requires smooth operations without material sticking. The low coefficient of friction translates into reduced wear and tear on equipment and surfaces.
In applications like food processing, having a material that provides easy cleaning without compromising safety is essential. The inert nature of PTFE means it does not interact with food products, making these sheets a wise choice in food processing operations.
In summary, the unique properties of sintered PTFE sheets equip them to cater to various challenges in specialized industries. Their chemical resistance, thermal stability, mechanical strength, and remarkable surface properties create a versatile platform for applications requiring high-performance materials. The deep dive into these individual aspects illustrates their immense potential and encourages further exploration into their applications.
Applications of Sintered PTFE Sheets
Sintered PTFE sheets find their niche across a wide panorama of industries, illustrating their adaptability and multifaceted nature. Understanding these applications is key to recognizing the significance PTFE materials hold in solving real-world challenges. Their ability to withstand harsh environments and their chemical resilience bring forth not only opportunities for efficiency but also safety. Whether in industrial sectors, healthcare, electronics, or food processing, the implications of deploying sintered PTFE sheets are profound.
Industrial Uses
In industrial settings, sintered PTFE sheets are akin to having a Swiss Army knife on hand. From gaskets to seals and bearings, their versatility is unparalleled. PTFE's unique non-stick properties allow machines to operate smoothly, reducing wear and tear significantly.
- Sealing Applications: In environments where corrosive substances abound, PTFE stands tall. It prevents leakages, thus safeguarding machinery and keeping operational costs in check.
- Bearings: Used inside pumps and machinery, PTFE's low friction ensures a longer lifespan and less maintenance.
- Gaskets: The chemical inertness of PTFE makes it the go-to choice for various manufacturing processes, effectively resisting aggressive chemicals without degrading.
With these applications, PTFE isn’t just another material; it becomes an essential ally in enhancing productivity and performance.
Medical Applications
The medical field relies heavily on materials that guarantee safety and integrity. Sintered PTFE sheets play a significant role in this space, particularly when it comes to medical devices and implants.
- Biocompatibility: PTFE's chemical stability translates to biocompatibility, making it suitable for use in blood-contacting applications. Medicine delivery systems often utilize PTFE components for ensuring reliability.
- Surgical Instruments: Non-stick attributes are a blessing in surgical contexts, enabling easy cleaning and minimizing the risk of contamination.
- Dental Applications: In dentistry, PTFE is used for its effective sealing properties in various procedures, particularly regarding dental implants and grafts.
The implications of using PTFE in medical technology extend from enhancing patient safety to improving procedural outcomes.
Electronics and Insulation
Electronics have emerged as a critical sector where the applications of sintered PTFE sheets are increasingly prevalent. Given their insulating properties, they serve a pivotal role in safeguarding electronic components from environmental damage.
- Insulation: PTFE is known for possessing excellent insulative qualities, ideal for applications in high-frequency electronics, encouraging minimal signal loss.
- Circuit Boards: Its durability ensures the longevity of circuit boards, thus optimizing performance while also minimizing risk of failure.
- Connectors: PTFE sheets are used to insulate connectors, providing reliable performance under various environmental conditions.
In summary, the contribution of PTFE to electronics is critical in maintaining the integrity and functionality of devices, from everyday gadgets to advanced technology.
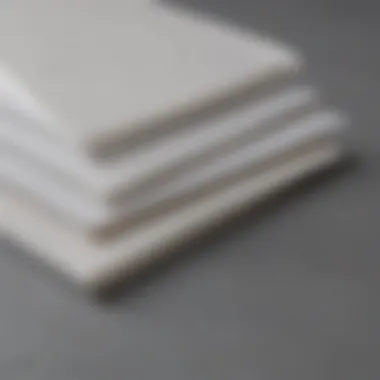
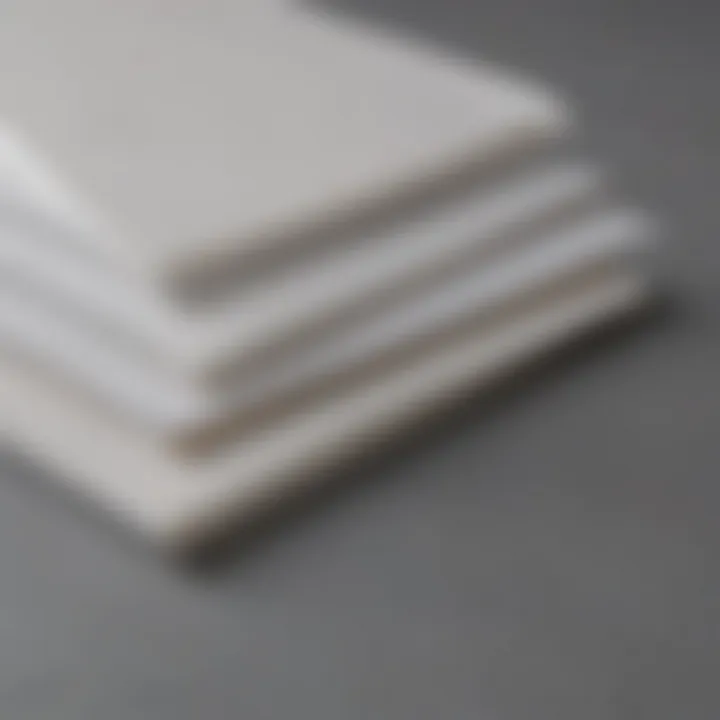
Food Processing
Sintered PTFE sheets offer an irreplaceable role in the food sector, rooted primarily in their non-reactivity and ease of cleaning, essential for food safety.
- Food Machinery: As equipment surfaces, PTFE provides a safe, non-stick interface, mitigating contamination risks while enhancing cleaning processes.
- Packaging: The ability to withstand heat and chemical interactions makes PTFE materials suitable for food packaging, extending shelf life without compromise.
- Sanitation: Its non-porous nature effectively prevents bacterial growth, making it a prime candidate for surfaces in food processing plants.
The use of sintered PTFE sheets in food processing is not just a matter of convenience but a critical aspect of ensuring food hygiene and quality.
In totality, the applications of sintered PTFE sheets weave a narrative of efficiency, safety, and reliability across diverse sectors, marking their place as a quintessential material in modern industrial practices.
Comparative Analysis with Other Materials
In understanding the framework of material science, the comparative analysis of sintered polytetrafluoroethylene (PTFE) sheets with other prevalent materials is crucial. This exploration not only underscores the unique advantages of PTFE but also highlights specific scenarios where alternative materials may prove more efficient or effective. The insights gained from such analyses can aid researchers, engineers, and industry professionals in making informed decisions tailored to their unique applications.
Versus Traditional Plastics
Sintered PTFE stands apart from traditional plastics like polyvinyl chloride (PVC) or polypropylene in several key aspects. First off, there's the issue of chemical resistance. PTFE is incredibly resistant to corrosive substances, whereas traditional plastics often succumb to chemical degradation when confronted with harsh environments.
- Thermal Stability: PTFE maintains its integrity at higher temperatures, unlike plastics that might warp or degrade, leading to failure in high-heat applications.
- Lubricity: The low friction characteristics of PTFE are markedly superior compared to traditional plastics, making it a standout material for applications requiring sliding or rotating motions.
- Durability: PTFE has a longer lifespan in aggressive chemical settings, reducing the need for frequent replacements, which can save considerable time and money in the long run.
However, it’s important to note that traditional plastics often come at a lower cost. Depending on the application, budget constraints may dictate choosing a conventional plastic despite the potential risks.
Versus Metals
When evaluating sintered PTFE against metals, such as steel or aluminum, the contrasts become even more pronounced. While metals boast higher tensile strength and rigidity, they often lack the inert properties that PTFE offers:
- Corrosive Environment Suitability: PTFE exhibits an outstanding ability to resist corrosive and oxidation scenarios, where metals can quickly deteriorate.
- Weight Considerations: PTFE weighs significantly less than metals, making it more suitable for lightweight applications, such as those in aerospace or automotive industries.
- Electrical Insulation: The dielectric properties of PTFE allow it to serve effectively as an insulator in electrical applications, a function not typically satisfied by metals.
Despite these advantages, metals are commonly favored in structural applications where strength is a non-negotiable factor. Thus, the choice may come down to a balance between material properties and application requirements.
Versus Composite Materials
Composite materials present a unique challenge when compared to sintered PTFE sheets. Composites, combining two or more different materials, can achieve custom properties that suit particular requirements:
- Tailored Attributes: Many composites are engineered for specific properties such as enhanced strength, light weight, or improved thermal performance, which can sometimes outshine PTFE for niche applications.
- Cost-Effectiveness: Often, certain composite materials can be produced at lower costs than sintered PTFE, which may lead engineers to opt for them when budget is a considerable factor.
- Flexibility in Design: Composites can be designed in numerous forms and shapes through layering, which allows for greater versatility in design compared to PTFE's sheet form.
Nevertheless, sintered PTFE retains a distinct edge in chemical resistance and durability, particularly where aggressive environments are concerned.
The decision to choose one material over another often hinges on specific project requirements, risk tolerance regarding material performance, and economic considerations.
In summary, it's crucial to weigh the properties and specifications of sintered PTFE against alternative materials carefully. Each material presents its own set of advantages and disadvantages, and understanding these nuances can dramatically influence the success of engineering projects.
Economic Aspects of Sintered PTFE Sheets
The economic dimensions surrounding sintered PTFE sheets are vital for comprehending their role, utility, and potential impact in various sectors. With their unique properties, these materials are not just functional; they also represent a significant financial investment that requires careful consideration. Understanding the economic aspects involves evaluating costs, market trends, and emerging opportunities, which form the backbone of any decision-making process regarding their use.
Cost-Benefit Analysis
When diving into a cost-benefit analysis of sintered PTFE sheets, one must weigh the initial purchase price against the long-term advantages they offer. While the upfront costs can be considerable, especially when sourcing high-grade PTFE, the intrinsic benefits often justify this expense.
- Longevity and Reduced Maintenance: Sintered PTFE sheets exhibit remarkable durability. They resist wear and tear, which minimizes replacement frequency. Long-term, this can save businesses a chunk of change.
- Energy Efficiency: In many applications, using sintered PTFE can lead to lower energy consumption, thus reducing operational costs. The material's thermal stability means better performance at high temperatures without thermal degradation.
- Chemical Resilience: The chemical resistance of PTFE minimizes the risk of structural failure, which can be financially disastrous in a plant setting. Fewer breakdowns translate into less unplanned downtime and lower repair costs.
While the initial investment seems hefty at first glance, the return on investment can be substantially beneficial over time, proving that sometimes you have to spend a bit to save a whole lot.
Market Trends
The market for sintered PTFE is evolving rapidly, driven by innovation, technology, and growing awareness of its unique features. Thus, keeping an eye on market trends is essential for stakeholders. Some factors to consider include:
- Increased Demand in Various Industries: Industries such as aerospace, pharmaceuticals, electronics, and food processing are increasingly recognizing the worth of sintered PTFE sheets. This rising demand is a robust indicator of the material's growing footprint.
- Sustainability Movement: With sustainability being the buzzword, businesses are looking for materials that align with their green initiatives. Sintered PTFE, with its long lifespan and recyclability, fits the bill, pushing its acceptance further in markets that value eco-friendliness.
- Technological Advancements: Innovations in manufacturing techniques and applications enhance the material's appeal. These advancements often lead to new products, further driving market interest.
The shifting landscape presents a panorama of opportunities for both current and future stakeholders.
Potential for New Markets
Looking towards the horizon, the potential for new markets is one of the most intriguing aspects of sintered PTFE sheets. Entrepreneurs and businesses are tapping into several areas ripe for exploration:
- Biomedical Applications: With the material's biocompatibility, sintered PTFE is making waves in medical device manufacturing. Its unique properties lend themselves excellently to surgical implants and prosthetics.
- Renewable Energy Sector: As the world transitions towards cleaner energy sources, sintered PTFE sheets are gaining traction in applications involving solar panels and hydrogen fuel cells, where their chemical resistance is of great benefit.
- Automotive Innovations: With the automotive industry's shift towards electric and hybrid vehicles, sintered PTFE has a place in gaskets and seals that can enhance vehicle performance and durability.
New markets emerge as innovative thinkers continue to explore how sintered PTFE can play a role. As such, staying informed about shifts in these areas could be vital for tapping into lucrative avenues.
"Understanding the underlying economics of sintered PTFE is critical for informed decisions that can save costs and enhance operational efficiency in the long run."
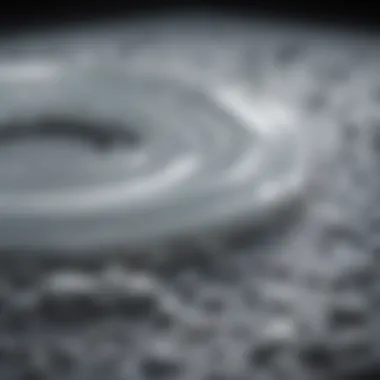
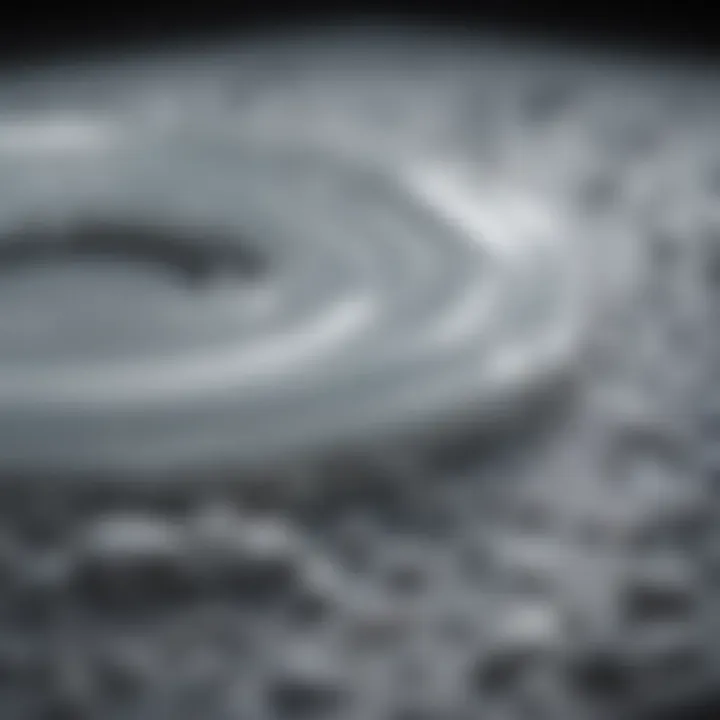
In summary, the economic aspects of sintered PTFE sheets encompass far more than mere pricing. They reflect a comprehensive framework that encompasses cost-saving opportunities, current market insights, and the potential for diversification into new territories. As such, evaluating these dimensions can significantly influence the overall success of PTFE sheet applications.
Challenges Associated with Sintered PTFE
Sintered PTFE sheets, while highly regarded for their unique properties and applications, do not come without their share of hurdles. Understanding these challenges is crucial for anyone considering their use in various industries. This section dives into the complexities that surround processing, environmental concerns, and regulatory issues associated with sintered PTFE.
Processing Difficulties
One of the significant challenges in working with sintered PTFE is related to the processing itself. PTFE's high melting point, which hovers around 327°C, makes traditional molding methods quite difficult. It doesn’t behave like other thermoplastics; instead, it requires specialized approaches to shape it without compromising its integrity.
The sintering process, although effective in giving PTFE its desired properties, is sensitive. Operators must maintain specific temperatures and pressure levels carefully throughout the process. Having even a slight variation can lead to defects in the final product, such as uneven texture or compromised strength. These processing difficulties necessitate skilled labor and may drive up manufacturing costs, which manufacturers must account for in their overall economic models.
"The care taken during the sintering process can mean the difference between a robust material or one that crumbles at first touch."
Moreover, the equipment required for processing PTFE can be quite costly. Standard machinery often cannot handle the high-temperature requirements or the abrasive nature of PTFE, thus leading companies to invest heavily in specialized machinery. The complexity of the processing can turn away some manufacturers, particularly smaller firms that are unable to absorb such high costs.
Environmental Concerns
Environmental concerns surrounding sintered PTFE are another focal point that cannot be overlooked. While PTFE itself is inert and can withstand a wide array of chemicals, the production process generates waste and emissions that can be harmful. Environmental regulations concerning chemical production are becoming increasingly stringent worldwide, putting pressure on manufacturers to find cleaner methods of production.
The disposal of PTFE waste also poses a problem. Since it is non-biodegradable, conventional disposal methods are inadequate. Incineration can release harmful byproducts, which contributes to a larger conversation around the sustainability of materials used in any given industry. Emerging initiatives in recycling PTFE are promising but still in their infancy. Efforts are underway to develop processes that can reclaim and reuse PTFE, but these methods need to be scalable and economically viable.
Regulatory Issues
On the regulatory front, sintered PTFE falls under various jurisdictional regulations depending on the application. Different countries have unique standards that can affect how PTFE products are made and marketed. This inconsistently can complicate things for manufacturers who may intend to sell their products internationally.
Regulations often center around health and safety standards, particularly in industries like food processing and medical applications. Manufacturers must ensure that their PTFE sheets meet the required specifications, which often involves extensive testing and certification procedures. The costs associated with these processes can be prohibitive and require additional time for compliance.
Furthermore, businesses must stay up to date with changing regulations that may impact their operations. Non-compliance can result in heavy fines or even a complete ban on their products. To navigate this complex landscape, regular consultations with regulatory bodies can be imperative. Companies need to allocate resources for compliance to avoid red tape that could hamper productivity.
Future Directions in PTFE Technology
The exploration of future directions in PTFE technology is crucial in understanding how sintered PTFE sheets can evolve and meet the changing demands of various industries. These advancements not only enhance the performance characteristics of PTFE but also broaden its application horizons. As we look ahead, several key areas warrant closer examination, particularly regarding innovative applications, manufacturing advancements, and sustainability considerations.
Innovative Applications
Sintered PTFE sheets have already made their mark across sectors such as electronics, medical, and food processing. However, as technology advances, the potential for new applications expands significantly. For instance, researchers are investigating the use of PTFE in semiconductors, where its dielectric properties could improve the performance of electronic components.
Additionally, in the field of medical devices, there is ongoing experimentation with PTFE as a biocompatible material for implants, potentially enhancing the success rates of surgeries. The development of PTFE nanocomposites also opens doors for applications in permeable membranes, which could enhance filtration processes in various industries. The versatility of PTFE, combined with innovation, sets the stage for its broader utilization.
Advances in Manufacturing Techniques
Advancements in manufacturing techniques play a pivotal role in the future of PTFE technology. Traditional manufacturing methods, while effective, may not meet the fast-paced demands of modern industries. New techniques, like additive manufacturing, could allow for greater customization and efficiency in producing sintered PTFE sheets. For example, 3D printing enables the crafting of complex shapes and sizes that traditional processes struggle to achieve, reducing waste and energy consumption.
Moreover, the integration of smart technologies in PTFE manufacturing can facilitate quality control through automated systems, ensuring consistent product specifications. This evolution in manufacturing not only optimizes production processes but also positions PTFE as a competitive material against alternatives that may not offer the same advantages.
Sustainability Considerations
With increasing scrutiny regarding environmental impacts, sustainability is becoming a cornerstone of material science, including PTFE technology. Efforts to make the production of sintered PTFE sheets more sustainable are of utmost importance. One avenue of exploration is the utilization of recycled feedstocks, which can significantly reduce the ecological footprint associated with new material production.
Furthermore, innovations in biodegradability research could offer insights into how to enhance the lifespan of PTFE products or develop alternatives that share functional properties while being greener. Companies are also examining end-of-life strategies that not only comply with regulations but actively contribute to a circular economy.
"Creating sustainable materials and practices is not merely an option; it is an imperative for both industry growth and environmental preservation."
Summary and The Ends
In this article, we have journeyed through the intricate world of sintered polytetrafluoroethylene (PTFE) sheets, uncovering their remarkable properties, versatile applications, and the complexities surrounding their production. The significance of summarizing our findings is pivotal for several reasons, especially when considering the expansive realm of materials sciences and engineering.
First, the summary serves as a vital synthesis that encapsulates core insights, ensuring that even those skimming for information can grasp the essential points. The properties of sintered PTFE, such as their chemical resistance, thermal stability, and mechanical strength, are not merely technical details but keys to understanding how these sheets stand out against other materials. Highlighting these aspects emphasizes their suitability across various industries—from healthcare to electronics—and articulates the value they bring.
Moreover, diving into the manufacturing processes, we illuminated the challenges and innovations involved. Quality control and advancements in techniques are not just operational perks; they are paramount for producing reliable materials that meet rigorous standards. Economically, recognizing market trends and potential areas for expansion allows stakeholders to make informed decisions, positioning PTFE sheets as a lucrative investment in manufacturing.
Challenges were not skirted either. Exploring the processing difficulties, environmental impacts, and regulatory hurdles provides an honest view of the field. Embracing these insights empowers professionals to strategize effectively, mitigating risks associated with PTFE applications.
Finally, as we turn our gaze to the future directions in PTFE technology, the possibilities seem almost endless, with sustainability considerations gaining paramount importance. Proactively addressing these concerns while fostering innovation will no doubt shape the trajectory of PTFE in the years to come.
Recap of Key Points
- Unique Properties: Sintered PTFE stands out due to its superior chemical resistance, thermal stability, and high mechanical strength which are critical in various applications.
- Versatile Applications: From industrial uses to medical applications, PTFE sheets find relevance across diverse sectors, showcasing their multifunctionality.
- Manufacturing Insights: The manufacturing process involves careful raw material selection, innovative sintering techniques, and stringent quality control measures.
- Economic Considerations: A thorough cost-benefit analysis coupled with an understanding of market trends provides insights into the economic viability of these sheets.
- Future Prospects: Innovations in PTFE technology highlight the need for continuous advancements, while sustainability remains a focal point for future developments.
Closing Thoughts
As we conclude this exploration of sintered PTFE sheets, it's clear that they are not just another plastic but a multifaceted material that holds significant potential in various fields. Understanding their properties and applications allows industries to harness the benefits of PTFE effectively.
This article provides a launching pad for researchers, engineers, and industry professionals alike, pushing forward the dialogue surrounding advanced materials. With the rapid pace of material science, staying abreast of innovations in PTFE—especially regarding environmental sustainability—will be crucial for maintaining a competitive edge and ensuring responsible material usage moving forward.
As highlighted through our exploration, embracing the strengths and addressing the challenges of sintered PTFE is paramount for future advancements and applications, which are bound to reshape several industries.