Forging Cast Iron: Techniques and Applications
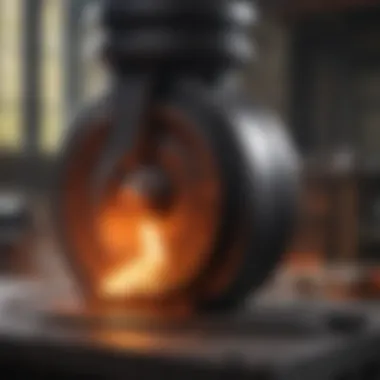
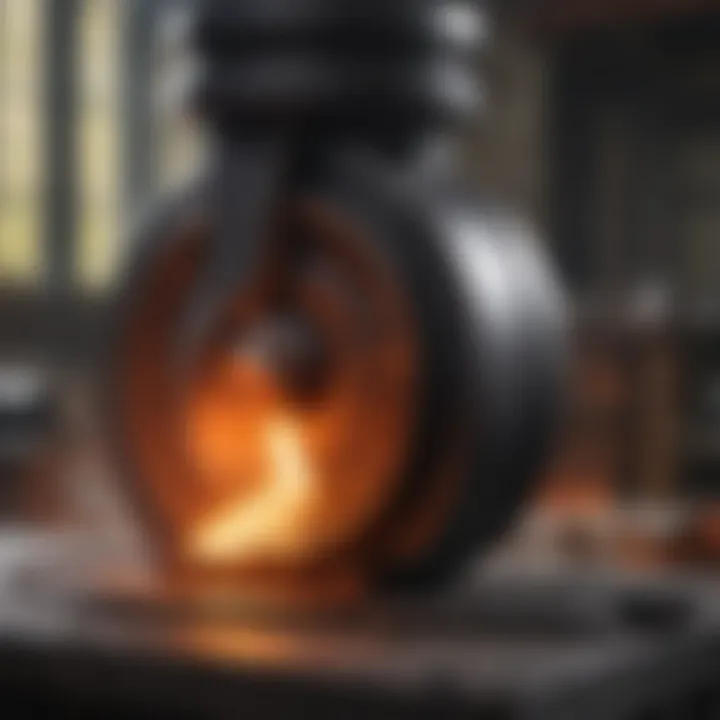
Intro
Forging cast iron is a complex process that involves manipulating metal to enhance its properties and create useful objects. Although cast iron is often viewed primarily as a material for casting, its forging capabilities are equally significant. Understanding the techniques, applications, and theoretical underpinnings of forging cast iron allows for a deeper appreciation of its role in various industries.
In this article, we will explore the various methodologies used in forging cast iron. We will discuss what makes cast iron unique compared to other metals, and highlight its diverse applications across fields such as construction, automotive, and art. By examining the advantages and disadvantages of this forging process, we aim to present a comprehensive overview that is relevant for scholars, engineers, and students alike.
Prelude to Cast Iron Forging
Forging cast iron is a specialized area within metallurgy that warrants a comprehensive exploration. Its importance lies not just in the techniques employed, but also in its broad range of applications that impact various industries. Being able to manipulate cast iron effectively offers the potential for creating innovative products, enhancing performance in existing applications, and understanding fundamental engineering principles. In the following sections, we will delve into the intricacies of cast iron forging, highlighting its nuances and relevance.
Historical Context of Cast Iron Use
The evolution of cast iron can be traced back to ancient civilizations. While its forging techniques were not extensively documented until much later, cast iron played a significant role in advancing construction and weaponry. By the late Middle Ages, cast iron had established itself as a vital material for a plethora of applications including cookware, machinery, and infrastructure. This historical background not only highlights the adaptability of cast iron but also sets the stage for contemporary practices in metallurgy. The transition from simple casting to more refined forging techniques reflects an ongoing journey to harness the material's full potential.
Definition and Characteristics of Cast Iron
Cast iron is primarily an iron-carbon alloy with a carbon content between 2% and 4%. Its defining characteristic is the presence of graphite, which forms during the solidification process, giving cast iron its unique properties. These properties include excellent castability, wear resistance, and a good balance of machinability with strength. Important types of cast iron include gray cast iron, ductile cast iron, and white cast iron, each presenting distinct attributes suitable for different applications.
Understanding these characteristics is crucial for engineers and metallurgists looking to apply cast iron forging techniques effectively. Key attributes include:
- Fluidity: This allows cast iron to fill intricate molds effectively.
- Castability: Cast iron can be cast into complex shapes, enhancing its usability across various applications.
- Strength and brittleness: Different types exhibit varying levels of strength, making certain forms more suitable for critical load-bearing applications.
As we explore further sections on forging techniques and applications, the current knowledge of cast iron characteristics will provide a foundation for understanding the nuances of the forging process.
The Fundamentals of Forging
The topic of The Fundamentals of Forging is crucial in understanding the entire landscape of cast iron forging. It forms the backbone for many processes that connect theory and practical application. Grasping these fundamentals is essential for professionals and students alike, as it equips them with the necessary insights into the techniques and theoretical principles that govern this field. It enhances our understanding of the benefits and challenges faced in forging cast iron, which has diverse implications across various industries.
Overview of Forging Techniques
Forging techniques refer to the methods used to shape metal, specifically through deformation under pressure. Among the most common techniques are open-die forging and closed-die forging. Each method has its unique features and applications.
- Open-die forging involves placing the metal between two dies and applying forces to shape it. This technique allows for great flexibility in producing large parts and is typically used for simpler shapes.
- Closed-die forging, on the other hand, involves a high level of precision due to the design of the dies. This method is best suitable for mass production, yielding intricate shapes with a controlled dimensional tolerance.
Understanding the specifics of these techniques is necessary for anyone interested in metallurgy or manufacturing. Each technique presents different implications in terms of costs, material properties, and production capabilities. The choice of technique also depends on the desired final characteristics of the forged iron, influencing strength, ductility, and subsequent processing stages.
Difference between Casting and Forging
The distinction between casting and forging is foundational in metallurgy. While both involve metal-forming processes, they have essential differences that determine their respective applications and properties.
- Casting involves melting metal and pouring it into a mold where it solidifies. This method allows for complex shapes but may introduce defects like porosity or inclusions due to gas entrapment or impurities in the metal. Additionally, cast metals may not possess the same mechanical strength as forged metals.
- Forging, in contrast, processes metal below its melting point, resulting in a denser and often stronger metal. The forging process aligns the grain structure, enhancing its mechanical properties. For applications requiring high strength and reliability, forging is generally preferred over casting.
In summary, understanding these differences is critical for material selection and processing decisions in industries where cast iron's potential is maximized.
Key Insight: Forging typically offers superior mechanical properties compared to casting, making it a favored process in applications demanding high strength and reliability.
Cast Iron Types and Their Properties
Understanding the various types of cast iron and their distinctive properties is vital in the context of forging. Different types of cast iron possess unique characteristics that significantly impact their workability, strength, and suitability for specific applications. Knowledge of these properties not only aids in choosing the right material for forging but also informs the techniques and processes that will yield optimal results. Each type of cast iron has its strengths and challenges, thus offering diverse possibilities in both industrial and artistic endeavors.
Gray Cast Iron and Its Forging Potential
Gray cast iron is among the most common forms of cast iron, made primarily from iron, carbon, and silicon. Its microstructure features graphite flakes, which impart excellent machinability and thermal conductivity. The forging potential of gray cast iron lies in its ability to absorb shock and resist deformation. This makes it highly valued in applications that require components that endure stress.

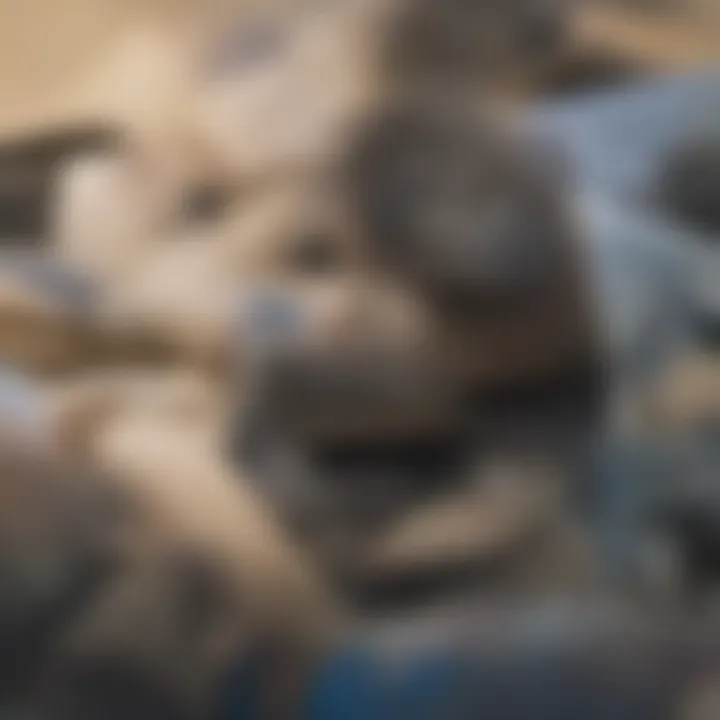
In forging processes, gray cast iron can be shaped at elevated temperatures, allowing for increased ductility. However, care must be taken to avoid rapid cooling, which can lead to brittle fractures.
Essential points about gray cast iron include:
- High machinability: This property makes it easier to shape after forging.
- Shock resistance: Ideal for parts subjected to fluctuating stresses.
- Density: Heavier than many other materials, it requires adjustments in machinery.
In summary, gray cast iron's unique characteristics establish its importance in many forged applications.
Ductile Cast Iron: Advantages in Forging
Ductile cast iron, also known as nodular cast iron, distinguishes itself with its spheroidal graphite structure. This design enhances its ductility and tensile strength, providing a robust material suitable for forging.
The advantages of ductile cast iron in the forging process are substantial. The material exhibits a remarkable capacity to deform without breaking, allowing for intricate shapes and designs. Additionally, ductile cast iron can absorb energy better than its gray counterpart, making it effective in conditions that involve repeated impacts.
Key attributes of ductile cast iron include:
- Superior tensile strength: Essential for high-load applications.
- Enhanced shock resistance: Ideal for components in dynamic environments.
- Versatile: Can be used in various applications, including automotive and structural components.
Given these advantages, ductile cast iron has become increasingly popular in forging, reflecting its value to engineers and manufacturers alike.
White Cast Iron: Challenges in Forging
White cast iron is characterized by a highly cemented structure that lacks free graphite. This results in a very hard material that poses unique challenges for forging. While it has excellent wear resistance, white cast iron is notoriously brittle.
The rigidity of white cast iron limits its capacity to be forged effectively. Attempts to shape this material often result in cracks or fractures, particularly if not managed with precise temperature control. The need for high heating temperatures may also lead to further complications, as maintaining uniform heat distribution proves challenging.
Some challenges associated with white cast iron include:
- Brittleness: Reduced capacity to handle stress without fracturing.
- Difficult forging process: Increased risk of defects during shaping.
- Limited applications: Primarily used in wear-resistant applications where impact is minimal.
Forging Process for Cast Iron
The forging process for cast iron is a crucial aspect of its use in various applications. This is not just about shaping metal; it is about enhancing the material's mechanical properties. By refining cast iron through forging, we can achieve better performance characteristics, making it more suitable for specific industrial purposes. Understanding the different stages of this process leads to insights that can improve results and overall output quality.
Preparation Techniques
Preparing cast iron for forging involves several steps that ensure successful manipulation of the material. Prior to forging, it is essential to assess the type and quality of cast iron being used. Factors such as composition and prior treatments can influence the subsequent forging steps.
- Inspection: Checking for flaws or defects in the cast iron prior to the forging process allows for adjustments or selection of alternative materials.
- Machining: Some pieces may require initial machining to achieve desired dimensions. Removing excess material helps in achieving a better final shape during forging.
- Cleaning: Surface contaminants, like rust or oils, must be eliminated. A clean surface helps in achieving uniform heating during the next stages.
Thus, thorough preparation not only expedites the forging process but also contributes to higher quality final products.
Heating Methods and Their Effects
Heating is one of the most important phases in the forging process. Proper heating methods directly affect the malleability and ductility of cast iron, making it easier to shape during forging. There are several methods of heating, including:
- Oven Heating: This method provides consistent heat, allowing for uniform temperature distribution throughout the material.
- Induction Heating: This technique offers rapid heating and is efficient for smaller workpieces. It raises the temperature without heating the surrounding environment.
- Furnace Heating: Larger components can benefit from traditional furnace heating, which can accommodate multiple parts at once.
The temperature at which cast iron is forged depends significantly on its type. For example, ductile iron can benefit from heating to 1,500°F, while gray iron may require slight variations.
Understanding the heating method's influence assists in avoiding issues such as cracking or brittleness in the forged product.
Mechanical Processes Involved
The mechanical processes involved in forging cast iron encompass several techniques and tools, which directly influence the quality and characteristics of the finished product. The main mechanical processes include:
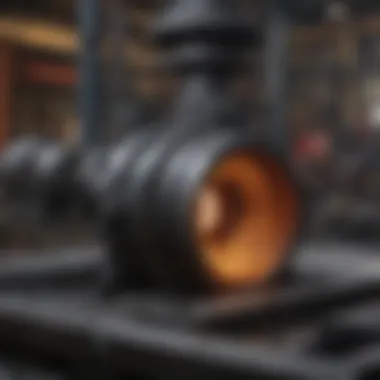
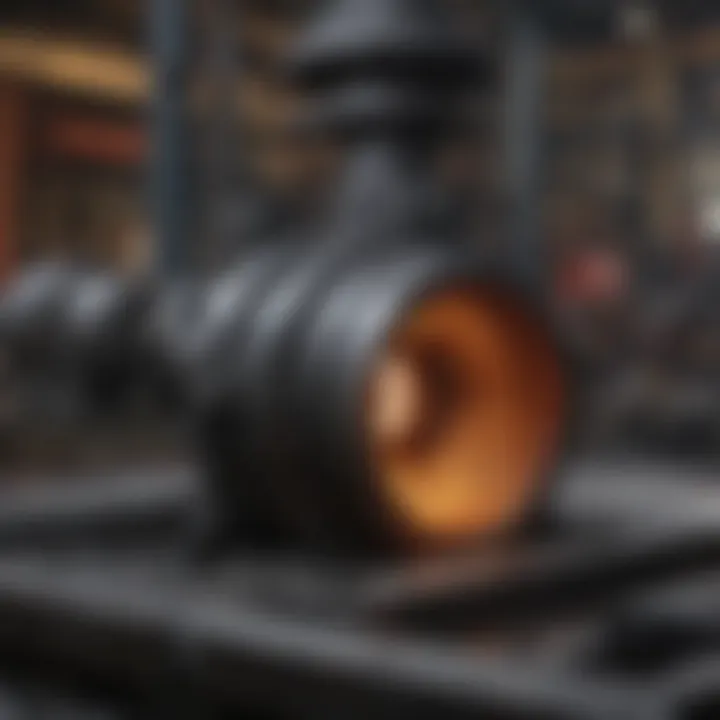
- Hammering: This traditional method involves using a hammer to shape the iron. Hammering applies compressive forces, which induce changes in the microstructure of the material.
- Press Forging: Utilizing a mechanical press, this method applies slow, steady pressure to the material. It is particularly useful for mass production.
- Die Forging: In this technique, the cast iron is formed into a specific shape using customized dies. This method ensures high accuracy and repeatability.
Combining these mechanical processes effectively can lead to improved strength and durability of the forged piece. A knowledge of the appropriate methods to use based on the type of cast iron and application requirements is vital for successful forging.
Applications of Forged Cast Iron
The significance of forged cast iron in various sectors cannot be overstated. Its adaptability, strength, and durability make it a favored material in many applications. Understanding these applications is essential for engineers and designers who seek to utilize cast iron's unique properties.
The applications can be broadly categorized into industrial and artistic uses, showcasing the versatility of the material. Each of these categories offers insights into the practical benefits and considerations of using forged cast iron.
Industrial Applications
Forged cast iron finds extensive use in industrial settings. Its inherent toughness allows it to endure high-pressure conditions, making it suitable for a range of mechanical components. Common applications in the industrial domain include:
- Automotive Parts: Components such as engine blocks and crankshafts often utilize forged cast iron. Its strength-to-weight ratio provides reliability under various operating conditions.
- Pipes and Fittings: Cast iron pipes, particularly those used in water and sewer systems, benefit from the material's resistance to corrosion and wear. Forging enhances their durability further.
- Machinery Components: Gears and housings made from forged cast iron support heavy machinery. They are engineered to handle high levels of stress and impact, essential for sustained performance.
- Heavy Equipment: Forged cast iron is ideal for parts in construction and agricultural machinery. Its ability to resist deformation makes it a preferred choice for high-load applications.
In a more technical perspective, the performance attributes of forged cast iron, such as fatigue resistance and tensile strength, are critically evaluated in different environmental and operational contexts. This ensures its suitability for precision engineering tasks that require both efficiency and reliability.
Artistic and Decorative Uses
Apart from industrial applications, forged cast iron is also prominent in artistic and decorative contexts. Over the years, artisans have appreciated its aesthetic capabilities along with its structural properties. Some notable areas of application in art include:
- Garden Ornaments: Statues and planters forged from cast iron offer durability and weather resistance. Their designs can range from intricate floral patterns to robust sculptures.
- Architectural Elements: Railings, window grilles, and decorative facades often utilize cast iron for both functionality and appearance. The material can be molded into various artistic shapes, adding character to structures.
- Furniture Design: Cast iron is increasingly found in furniture design. Tables and chairs forged from this material combine strength with unique aesthetics, contributing to contemporary and vintage looks.
"The fusion of functionality and artistry in forged cast iron allows creators to push the boundaries of conventional design."
- Public Installations: Sculptures and installations in public spaces often make use of forged cast iron due to its ability to withstand environmental conditions while maintaining visual integrity.
The remarkable ability of forged cast iron to be both functional and decorative points to its enduring relevance in modern design practices. Artists and designers leverage its characteristics to create pieces that are not just visually appealing but also practical.
In summary, the applications of forged cast iron highlight its multifaceted nature. From critical industrial functions to artistic expressions, its properties drive varied uses across sectors. Engaging with these applications opens avenues for innovation and inspires sustainable practices in future design and production.
Advantages and Disadvantages of Forging Cast Iron
Understanding the advantages and disadvantages of forging cast iron is crucial for those involved in metallurgy, engineering, or manufacturing. This section delves into specific elements that highlight the beneficial aspects of this technique while considering the challenges that come with it. Analyzing these factors provides a comprehensive overview, which can inform decision-making in production and application processes.
Cost-Effectiveness in Production
Forging cast iron can prove to be a cost-effective process, especially for high-volume production. Unlike many other methods, forging reduces waste considerably, allowing for efficient use of materials. The processes involved often require less time, as pre-heating and finishing steps can be streamlined.
Additionally, forged components typically exhibit a high strength-to-weight ratio. This is because forging aligns the grain structure within the material, enhancing its mechanical properties. As a result, products can be made with thinner walls, reducing material costs. For companies focusing on large-scale production, these savings can accumulate significantly.
However, initial equipment costs can be high due to the need for specialized forging machinery. The cost of tooling and dies also adds to this investment. Organizations must consider whether the long-term savings in materials and production efficiency will outweigh these initial expenditures.
Challenges in Forging Processes
Forging cast iron is not without its challenges. One of the primary issues is the processing temperatures required for various types of cast irons. The correct temperature must be maintained consistently to avoid defects like cracking or inadequate deformation. Temperature fluctuations can lead to issues in the final product quality, making precision critical.
Further complications arise from the alloying elements present in cast iron. Elements such as silicon and carbon can affect how the iron behaves during the forging process. Too much carbon can lead to brittleness, while insufficient heat can prevent the material from achieving the desired properties. This interplay requires careful monitoring and adjustment throughout the forging cycle.
Moreover, experienced operators are required to execute these processes effectively. As cast iron forging can exhibit considerable variability in behavior, the need for skilled personnel adds to training costs and operational complexities. Therefore, while forging cast iron can be efficient, appropriate expertise is paramount.
"Understanding the balance between advantages and disadvantages is key to leveraging forging techniques for cast iron effectively."
In summary, while the cost-effectiveness and strength advantages position forging cast iron favorably in modern applications, challenges regarding material behavior and operational demands present real considerations for manufacturers. A balanced understanding enables informed choices that align with organizational goals.
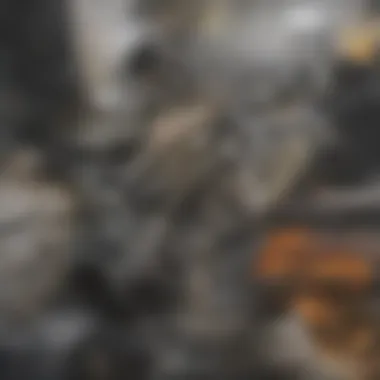
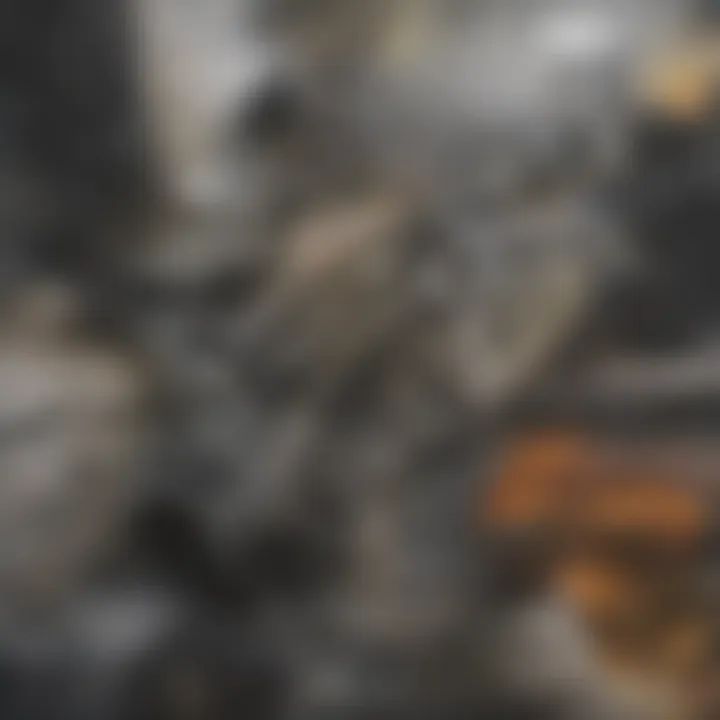
Theoretical Considerations in Cast Iron Forging
The theoretical framework surrounding cast iron forging is crucial for comprehending its intricacies. This section provides insights into the scientific principles underlying the processes involved in forging cast iron. Understanding these principles enhances the efficiency of techniques, informs material selection, and leads to innovations in this field. The significance of exploring the theoretical foundation lies in its ability to inform both practice and research, providing essential knowledge to students, engineers, and researchers.
Thermodynamics of Forging
Thermodynamics plays an essential role in forging cast iron. It addresses the heat transfer and energy conversion processes involved during forging operations. During the heating of cast iron, several thermodynamic principles apply. These include the behavior of materials at elevated temperatures and how they affect phase transitions and mechanical properties.
- Heat Transfer: Understanding heat transfer mechanisms—conduction, convection, and radiation—is vital. Efficient heating ensures the cast iron reaches an appropriate forging temperature, which is usually within a range of 1,500 to 2,500°F (800 to 1,400°C).
- Phase Changes: The ability of cast iron to change phase under heat is critical. The formation of austenite during heating alters the mechanical properties of the material, facilitating easier manipulation during forging.
- Energy Efficiency: Recognizing the energy lost as heat is important in optimizing the heating processes. Techniques like induction heating can support more efficient energy utilization as opposed to traditional methods.
"Understanding thermodynamics in forging processes enables engineers to innovate more efficient methods, reducing costs and enhancing productivity."
Material Science Insights
Material science provides a thorough examination of the microstructure and properties of cast iron, informing its behavior during forging. The interplay between composition, processing conditions, and final properties is significant.
- Microstructure Understanding: The microstructure of cast iron can significantly affect its mechanical properties. Various types of cast iron—gray, ductile, and white—exhibit different behaviors under forging conditions.
- Mechanical Properties: Factors such as tensile strength, ductility, and hardness can be optimized based on material composition. For instance, ductile cast iron tends to show superior properties in projected forging applications.
- Failure Mechanisms: Comprehending potential failure mechanisms during forging, like cracking and warping, is key. Knowledge of how temperature and strain rates affect these can guide better practice in the industry.
In summary, the theoretical considerations in cast iron forging involve a detailed exploration of both thermodynamic principles and material science. These areas not only provide a base for informed decision-making but importantly shape the future of forging technologies.
Future Prospects of Forging Cast Iron
The future prospects of forging cast iron encapsulate a blend of technological innovation and an increasing focus on sustainability. As industries evolve, the demand for more efficient, durable, and environmentally friendly materials continues to rise. Understanding these prospects can help stakeholders in metallurgical fields to adapt and innovate. This section will explore emerging techniques, sustainability concerns, and potential advancements in the industry.
Innovative Techniques on the Horizon
The realm of cast iron forging is on the cusp of transformation. Several innovative techniques are being developed that promise to enhance the quality and sustainability of cast iron products. These include:
- Additive Manufacturing: This technique offers a new approach to create complex geometries that would be difficult or impossible to achieve through traditional methods. By combining forging and 3D printing, manufacturers can optimize material use, reduce waste, and improve design.
- Advanced Automation: The integration of robotics in forging processes can lead to increased precision and efficiency. Automated systems can handle repetitive tasks, allowing human workers to focus on more complex aspects of production.
- Heat Treatment Innovations: New heat treatment methods are emerging that can enhance the mechanical properties of forged cast iron. Techniques like induction heating or microwave-assisted treatments allow for greater control over the heating process, leading to improved material characteristics.
These advancements could offer significant improvements over traditional methods, leading to increased productivity and reduced costs.
Sustainability and Environmental Impacts
As global focus shifts towards sustainability, the forging industry faces pressure to reduce its environmental footprint. The future of forging cast iron holds opportunities for achieving better sustainability goals. Important considerations include:
- Recycling of Materials: The forging industry is exploring better options for recycling scrap metal. Improved recycling processes can reduce the need for new raw materials and decrease waste, making production more sustainable.
- Energy Efficiency: New technology aims to enhance energy efficiency during the forging process. Utilizing renewable energy sources or implementing energy recovery systems can significantly reduce carbon emissions associated with traditional forging practices.
- Bio-based Lubricants: The shift from petroleum-based lubricants to bio-based alternatives can lessen the environmental impact of forging operations. These eco-friendly lubricants can perform effectively while reducing harmful emissions.
The potential for reducing environmental impacts while innovating in forging cast iron is significant. Stakeholders must act to balance technological advancement with ecological responsibility.
End
In the context of this article, the conclusion serves as a pivotal section that synthesizes the broader themes discussed throughout the text. By reflecting on the unique qualities and processes associated with forging cast iron, this conclusion emphasizes the vital role cast iron plays in metallurgical practices, both historically and in modern applications.
The summary of findings encapsulates the in-depth knowledge acquired regarding the various techniques employed in the forging of cast iron. The article illustrates that understanding the diverse types of cast iron and their specific properties is crucial for successful forging. Whether it is the versatility of gray cast iron or the advantageous features of ductile cast iron, each type presents its own set of unique challenges and benefits in forging processes.
Moreover, this section discusses the implications of forging cast iron in different industries. From structural components in construction to artistic creations in decorative metalwork, the applications are extensive and significant. The finding that forged cast iron provides enhanced strength and durability affirms its indispensable role in manufacturing and artistry alike.
Summary of Findings
- Historical Significance: Cast iron has a long history, contributing significantly to various cultural artifacts and industrial products.
- Unique Properties: The characteristics of different types of cast iron influence the forging techniques. Examples include the improved crack resistance of ductile cast iron compared to brittle white cast iron.
- Forging Techniques: Essential methods like heating and mechanical processes are critical for effective forgeability.
- Applications: The sectors utilizing forged cast iron include automotive, construction, and art.
Understanding these core findings not only enriches one’s grasp of metalworking but also highlights the innovative spirit that defines the metallurgical field.
Final Thoughts on Forging Cast Iron
As the field of metallurgy continues to evolve, the prospects for forging cast iron remain substantial. Innovations in technology and techniques are paving the way for more efficient and sustainable practices. In this light, fostering a comprehensive understanding of the theoretical underpinnings alongside practical applications is imperative.
Additionally, considerations around environmental impacts and sustainability increasingly shape the dialogue in forging processes. The future of cast iron forging appears promising, encouraging new research endeavors and industry practices.
The exploration of casting and forging dynamics reveals that while challenges persist, the potential for creative methods and applications is extensive. This evolution will continue to shape the way industries approach the utilization of cast iron, ensuring its relevance in both historic and contemporary contexts.