Epoxy Adhesives for Steel-Aluminum Bonding Analysis
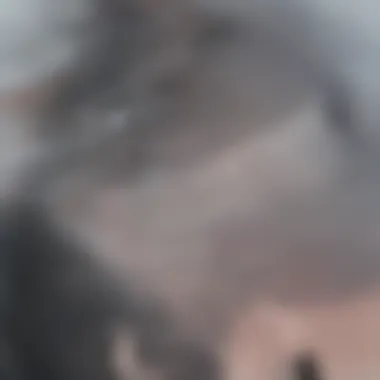
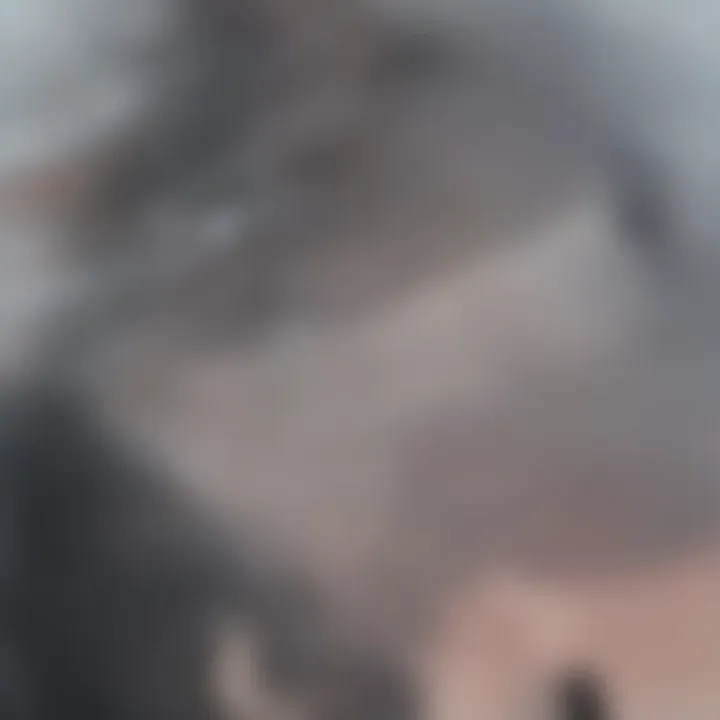
Intro
This article explores the complex yet fascinating world of bonding steel to aluminum using epoxy adhesives. In recent years, the need for effective bonding methods has grown significantly. This is particularly evident in fields such as aerospace, automotive, and construction, where the lightweight nature of aluminum must be combined with the strength of steel.
Understanding the properties and capabilities of epoxy adhesives is crucial. These adhesives offer not only high strength but also resistance to environmental factors. Therefore, they become ideal candidates for projects requiring durable bonds between these two distinct metals. It is essential to comprehend how to prepare surfaces properly and the techniques to apply these adhesives effectively.
As we navigate through this discussion, we will emphasize why this topic deserves attention. The challenges posed by dissimilar materials, like steel and aluminum, must be fully understood for successful applications. Thus, this article aims to equip researchers and professionals with the insights necessary for effective bonding practices.
Prolusion to Epoxy Adhesives
Epoxy adhesives are increasingly recognized for their exceptional bonding capabilities, particularly in joining dissimilar materials such as steel and aluminum. Understanding the fundamentals of these adhesives is crucial for practitioners and researchers alike. This section provides an overview of epoxy adhesives, their composition, and the various types available, making it a key starting point for anyone interested in the complexities of adhesive technology.
Definition and Composition of Epoxy
Epoxy adhesives consist of two primary components: a resin and a hardener. When these components are mixed, a chemical reaction occurs. This reaction results in the formation of a rigid polymer matrix. The strength and durability of an epoxy bond largely depend on the quality and composition of these components. The resin is typically derived from epichlorohydrin and bisphenol A, while the hardener is often an amine or an acid anhydride. This blend creates a three-dimensional network that endows the resulting adhesive with strong mechanical properties.
The unique structure of epoxy allows for excellent adhesion to a variety of substrates, including metals, plastics, and ceramics. Additionally, the versatility of epoxy formulations enables customization for specific applications, addressing various environmental resistances such as heat, moisture, and chemical exposure. Understanding these ingredients and how they interact is essential for selecting the right epoxy for a given task, especially when bonding steel to aluminum.
Types of Epoxy Adhesives
Epoxy adhesives can be classified into several categories based on their intended application. Each type offers distinct features that make it suitable for specific bonding tasks. Key types include:
- Structural Epoxies: These are formulated for high-strength applications where load-bearing is critical. They are often used in construction and automotive sectors.
- Non-structural Epoxies: Typically used for smaller, less load-bearing applications, these adhesives are more flexible and easier to work with.
- Flexible Epoxies: Designed to withstand movement and vibration, these can be used in applications where some flexibility is required, such as in certain automotive applications.
- Rapid Cure Epoxies: These allow for quicker bond formation, making them economical for high-volume production scenarios.
- High-Temperature Epoxies: Specialized for environments that require heat resistance, these adhesives maintain their integrity under elevated temperatures.
Choosing the appropriate type of epoxy adhesive is critical, as it determines the effectiveness of the bond under specific conditions. Each epoxy formulation should align with the requirements of the project, considering factors like mechanical load, exposure to environmental stresses, and the nature of the surfaces being bonded. Understanding these types provides the necessary foundation for anyone looking to explore the bonding of steel to aluminum using epoxy.
Properties of Epoxy Adhesives
The properties of epoxy adhesives play a vital role in their application, especially when bonding dissimilar materials like steel and aluminum. Understanding these properties helps practitioners select the appropriate adhesive for their specific needs. Epoxy adhesives are known for their excellent mechanical properties, thermal stability, and chemical resistance. These characteristics make them suitable for various industrial applications.
Mechanical Properties
Mechanical properties define how epoxy adhesives perform under various forces and conditions. Key elements include shear strength, tensile strength, and impact resistance, each contributing to the adhesive’s overall effectiveness.
Shear Strength
Shear strength refers to the adhesive’s ability to resist forces that tend to slide one material over another. This is crucial when bonding steel to aluminum, as both materials can experience different stresses in service. High shear strength ensures the bond remains intact during use, preventing separation.
The key characteristic of shear strength is its capacity to maintain adhesion under load. This makes it a beneficial choice because it ensures durability over time. A unique feature is its dependence on surface preparation; clean surfaces enhance shear strength by eliminating contaminants that can weaken the bond. The advantage of high shear strength is that it facilitates reliable performance in demanding applications.
Tensile Strength
Tensile strength measures how much pulling force the adhesive can withstand before failing. This property is important for applications where tension might be applied, ensuring the materials stay bonded under stress.
Tensile strength is significant because it allows for the bonding of materials that may face stretching forces. Epoxy’s high tensile strength is beneficial because it allows for thinner application layers without compromising bond integrity. However, if the joint is incorrectly designed, it may lead to premature failure.
Impact Resistance
Impact resistance indicates how well the adhesive can withstand sudden and forceful impacts, which can occur in various applications. This property is particularly relevant in environments where the bonded surfaces may be subjected to shocks or vibrations.
The key characteristic of impact resistance lies in its ability to absorb and disperse energy, reducing the risk of bond failure. It is a beneficial feature as it extends the lifespan of the bonded joint in high-stress environments. However, if not properly formulated, some epoxy adhesives may exhibit poor impact resistance, leading to brittleness.
Thermal Properties
Thermal properties, including temperature resistance and thermal conductivity, define how epoxy adhesives behave under thermal stress. These properties influence the adhesive's performance in various temperature environments.
Temperature Resistance
Temperature resistance is essential for ensuring that the adhesive maintains its properties under thermal stress. This characteristic is crucial when bonding materials exposed to fluctuating temperatures.
The significant aspect of temperature resistance is its role in maintaining bond integrity at high and low temperatures. This makes it a popular choice for applications exposed to thermal cycles. A unique feature of high temperature resistance is the ability to ensure stable performance, avoiding failure in elevated thermal conditions. A disadvantage, however, can be the potential increase in curing times for high-temperature-resistant formulations.
Thermal Conductivity
Thermal conductivity refers to how well heat can pass through the adhesive. It is crucial in applications where heat dissipation is necessary.
The key characteristic of thermal conductivity is its ability to affect temperature control in joint applications. This property makes it beneficial for preventing overheating in certain scenarios. On the flip side, adhesives with high thermal conductivity may also allow heat loss, which can be detrimental in other applications requiring insulation.
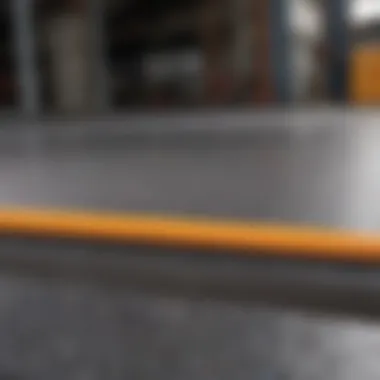
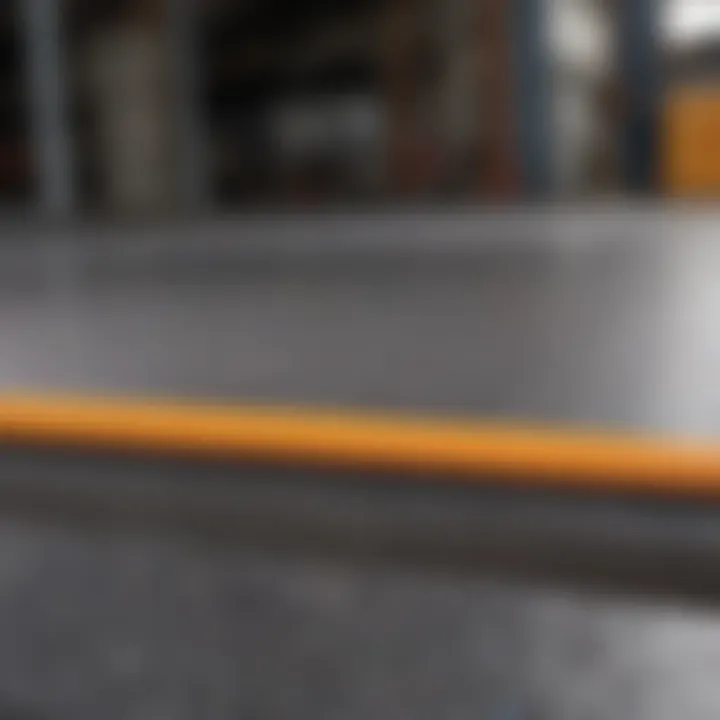
Chemical Resistance
Chemical resistance defines the adhesive’s ability to withstand exposure to various substances without degrading. This property is crucial in industries where adhesives may encounter solvents, fuels, or other harsh chemicals.
The importance of chemical resistance cannot be understated. It ensures longevity and reliability in hostile environments, making epoxy adhesives a popular choice in automotive, aerospace, and industrial applications. A high level of chemical resistance can also limit the need for frequent maintenance or replacement, thus offering economic advantages. However, formulations vary, and some may offer limited resistance to specific chemicals, which raises the necessity for careful selection based on application usage.
Understanding Aluminum and Steel Characteristics
Understanding the characteristics of aluminum and steel is essential for effectively bonding these two materials using epoxy adhesives. Each metal has a distinct set of properties that influences the bonding process. The compatibility of the two metals, primarily their differing physical and chemical properties, presents unique challenges. Therefore, an in-depth comprehension of these metals not only enhances the effectiveness of the adhesive but also addresses potential issues that could arise during and after bonding.
Aluminum: Properties and Applications
Aluminum is a lightweight metal known for its strength-to-weight ratio, corrosion resistance, and malleability. Its properties make it suitable for a variety of applications in industries such as automotive, aerospace, and construction. Aluminum exhibits high thermal and electrical conductivity, which is beneficial in applications requiring efficient heat exchange or electrical transmission.
The important properties of aluminum include:
- Lightweight: Aluminum is about one-third the weight of steel, making it a preferred choice in applications where reducing weight is critical.
- Corrosion Resistance: Aluminum naturally forms a protective oxide layer, which helps in resisting corrosion, extending its lifespan in various environments.
- Malleability: This property allows aluminum to be shaped easily without breaking, making it versatile for manufacturing components of various shapes and sizes.
In the automotive industry, aluminum components are increasingly used to reduce vehicle weight and improve fuel efficiency. In aerospace, its lightweight nature is crucial for aircraft design. The construction industry frequently utilizes aluminum for window frames and roofing materials.
Steel: Properties and Applications
Steel is favored for its superior strength and mechanical properties. It offers greater tensile strength compared to aluminum, which is beneficial in structural applications. Steel can be alloyed with various materials to enhance different characteristics such as toughness, hardness, and ductility.
Key properties of steel include:
- High Strength: Steel's high tensile strength allows it to withstand high loads, making it ideal for construction and structural applications.
- Ductility: Steel can be stretched into a wire or deformed without breaking, which is important for many manufacturing processes.
- Weldability: The ability to easily weld steel makes it a suitable choice for fabrication and repair tasks.
Steel finds its applications in construction, automotive, and machinery production. Buildings utilize steel for frames due to its high strength. In the automotive industry, steel is used for portions of the chassis and safety components.
Understanding the unique characteristics of aluminum and steel is crucial in overcoming challenges associated with bonding these two metals. It lays the groundwork for employing appropriate surface treatments and adhesive techniques.
"The successful bonding of aluminum and steel can yield remarkable structural integrity, provided the materials' characteristics are thoroughly understood."
Surface Preparation for Bonding
Surface preparation is a critical step in the process of bonding steel to aluminum using epoxy adhesives. Proper surface preparation ensures optimal adhesion and prolongs the lifespan of the bond. It involves a series of methods to clean and treat the surfaces, making them suitable for effective bonding. The overall goal is to remove contaminants, enhance surface characteristics, and ensure compatibility between the materials. Understanding the necessity of these processes can significantly improve the final outcome of any bonding endeavor.
Cleaning Processes
To achieve a strong bond, it is essential to clean the surfaces meticulously. Cleaning removes oils, dust, and other contaminants. This process can be divided into two main methods: solvent cleaning and mechanical cleaning.
Solvent Cleaning
Solvent cleaning is a popular method for removing contaminants from surfaces before epoxy application. It involves using specific solvents to dissolve and remove grease, dirt, and other residues. Solvents like acetone or isopropyl alcohol are commonly used due to their effectiveness in cleaning metal surfaces. A key characteristic of solvent cleaning is its ability to reach intricate areas that might be inaccessible through mechanical means.
The benefit of this method lies in its simplicity and effectiveness. It requires minimal equipment and can easily be performed in various settings. However, there are some disadvantages to consider. Over-reliance on solvents may pose environmental health risks, and improper use can lead to residue that hinders adhesion. Careful selection and use of solvents are essential.
Mechanical Cleaning
Mechanical cleaning employs physical methods to scrub and polish surfaces. This could involve using abrasive pads, sandblasting, or grinding tools. A key advantage of mechanical cleaning is its thoroughness. It can effectively remove old paint, rust, and other strong contaminants that solvent cleaning might not eliminate.
Mechanical cleaning is beneficial due to its immediate results. The unique feature is its capacity to create a rough surface texture, which can improve adhesion by increasing the surface area for the epoxy. One drawback is the potential for surface damage. If not performed carefully, mechanical methods can scratch or gouge the material, leading to weak bonds.
Surface Treatments
After cleaning, surfaces often require treatment to improve bonding performance. Surface treatments can include etching and priming.
Etching
Etching involves using chemicals or abrasives to create a textured surface that enhances bonding. This process helps remove the oxide layer on aluminum surfaces, which can hinder adhesion. A key characteristic of etching is its ability to significantly increase the surface area.
This unique feature contributes to a stronger mechanical bond. Etching is a popular choice because it prepares surfaces effectively for adhesive application. However, it requires careful handling, as improper etching can erode the substrate overly, affecting its strength.
Priming
Priming involves applying a specific primer to enhance adhesion between the adhesive and the substrate. A key characteristic of priming is that it can provide a more uniform layer for the epoxy to adhere to. Primers are often formulated to improve chemical bonding and offer some protection against environmental factors.
The unique feature of priming is its compatibility with various epoxy systems, allowing for greater flexibility. However, it does introduce an additional step in the preparation process, which may increase time and cost. Balance is needed to determine if priming is necessary based on the specific application and environment.
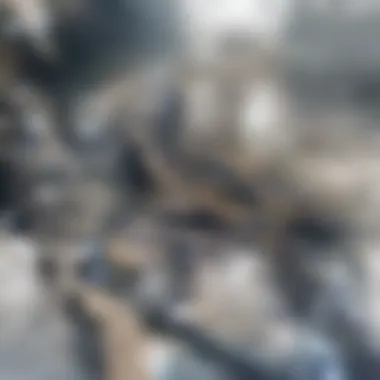
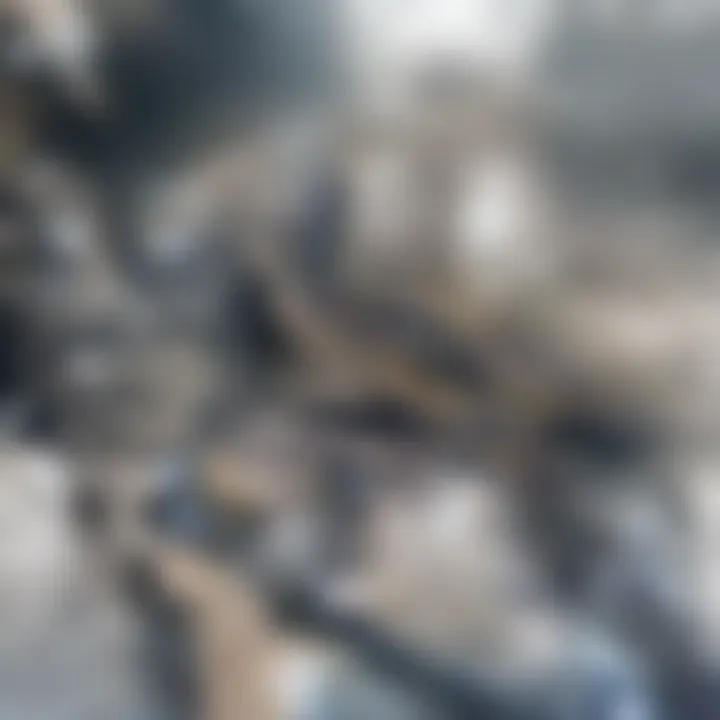
Proper surface preparation is non-negotiable. It ensures that the bond formed is not only strong but also durable against external stresses.
In summary, effective surface preparation via cleaning and treatment is vital for bonding steel to aluminum with epoxy adhesives. Each method has its merits and potential drawbacks, which need to be considered based on the intended application. Achieving a solid bond begins with thorough preparation, setting the stage for successful adhesion.
Bonding Techniques for Steel to Aluminum
Bonding techniques play a crucial role when it comes to connecting steel and aluminum using epoxy adhesives. Essentially, these techniques determine the effectiveness, reliability, and longevity of the bond. Different methods come with their own set of benefits and limitations that practitioners must consider. By understanding the various application methods and curing processes, one can make informed decisions to achieve optimal bonding in different settings.
Application Methods
Brush Application
Brush application is a method that involves using a paintbrush or similar tool to apply epoxy adhesive onto the surfaces of steel and aluminum. This technique is advantageous because of its simplicity and the control it offers to the user. A key characteristic of brush application is that it allows for precision, especially in small or intricate areas. This makes it a popular choice for applications that require attention to detail.
However, the unique feature of brush application comes with some drawbacks. The process may be slower compared to other methods, particularly when bonding larger surfaces. The need for multiple coats can contribute to extended curing times and possible inconsistencies in bonding thickness. Nevertheless, the ability to target specific spots makes it a favored option in many projects where precision is paramount.
Spray Application
Spray application is another effective method utilized in bonding processes. This technique allows for a quick and even distribution of adhesive across surfaces. A notable benefit of spray application is its ability to cover larger areas in less time, which significantly speeds up the entire bonding process. It is often employed in industrial settings where efficiency is a priority.
The unique aspect of spray application lies in its capacity to produce a uniform adhesive layer. This results in a consistent bond across the surfaces, which enhances the overall reliability of the connection. However, one should also consider the potential for overspray and wasted material. Proper masking and controlled environments are essential to maximize the advantages of this method and minimize drawbacks.
Dispensing Systems
Dispensing systems involve using specialized equipment to deliver precise amounts of epoxy adhesive. This method is known for accuracy and consistency. A key characteristic of dispensing systems is their capacity for automation, which can lead to high productivity levels in industrial applications.
One unique feature of dispensing systems is their ability to adapt to various types of adhesives and application scenarios. This flexibility is beneficial in environments where different bonding requirements exist. However, the initial investment in equipment may be high, and training may be necessary to effectively operate these systems. Despite these challenges, the precision and repeatability offered by dispensing systems can substantially improve bonding reliability in complex projects.
Curing Processes
Room Temperature Curing
Room temperature curing is a straightforward process where epoxy adhesives harden at ambient conditions. This method is exceptionally beneficial because it does not require additional heating or special equipment, making it accessible for various projects. The key characteristic of room temperature curing is its convenience, allowing for straightforward setups and minimal intervention.
The unique aspect of this method is that it often results in sufficient strength for many applications without the need for expedited processes. However, longer curing times might be a disadvantage. Patience is required, particularly in industrial settings where time is critical. Practitioners must weigh the advantages and disadvantages to determine when this curing method is appropriate.
Heat Curing
Heat curing is a process where elevated temperatures are used to accelerate the curing of epoxy adhesives. This method is often favored in situations requiring rapid turnaround. The key characteristic of heat curing is its ability to significantly reduce curing time, which can enhance productivity in manufacturing processes.
A unique feature of heat curing is that it usually results in superior bond strengths, making it ideal for high-performance applications. However, this method requires careful monitoring of temperature and time to avoid compromising the adhesive’s properties. An inadequately controlled heat curing process can lead to potential failures in bonding, which practitioners must avoid. Consequently, this technique, despite its advantages, requires a diligent approach to ensure successful outcomes.
Challenges in Bonding Steel to Aluminum
The junction of steel and aluminum presents complex challenges when utilizing epoxy adhesives. Understanding these challenges is crucial for effective application across various industries, such as automotive and aerospace. The differences in the materials not only influence the bonding process but also affect the longevity and reliability of the joint formed. Recognizing these hurdles allows practitioners to develop strategies that enhance adhesive performance, ensuring lasting bonds between steel and aluminum.
Thermal Expansion Mismatch
A significant concern when bonding steel to aluminum is thermal expansion mismatch. Steel and aluminum, while both metals, behave differently under temperature changes. Steel has a lower coefficient of thermal expansion compared to aluminum, which can lead to stresses at the joint during temperature fluctuations.
- Effects on Bonding: As temperatures rise, aluminum expands more than steel, which can result in microscopic cracks in the epoxy bond. Over time, these cracks can lead to failure. Consideration of the service temperature range is therefore vital in application decisions.
- Strategies for Management: To mitigate these stresses, one may consider using flexible epoxy adhesives that can better accommodate the differential movement between the two materials. Additionally, designs that allow for movement or that feature strategic placement of adhesives can also help in managing the thermal expansion mismatch.
Corrosion Issues
Corrosion is another critical issue when bonding steel to aluminum, primarily due to galvanic corrosion. This phenomenon occurs when two different metals are in electrical contact within a conductive solution, leading to the deterioration of one material, typically the aluminum.
- Collision of Properties: The differing electrochemical potentials of aluminum and steel create a galvanic cell when exposed to moisture or other corrosive environments, putting the aluminum at risk. As corrosion progresses, the integrity of the adhesive bond is compromised, potentially leading to premature failure of the adhesive joint.
- Preventative Measures: To reduce corrosion risk, practitioners should consider surface treatments for the metals before bonding. Techniques such as anodizing the aluminum or using primers can create a protective barrier that minimizes the chance of galvanic corrosion. Additionally, selecting epoxy adhesives that are highly resistant to moisture and chemicals can further enhance the longevity of the bond.
"Addressing the challenges in bonding steel to aluminum is the first step toward achieving successful, durable attachments across multiple industries."
In summary, the challenges of thermal expansion mismatch and corrosion can considerably affect the bond between steel and aluminum. Understanding these factors and employing appropriate strategies are essential for achieving reliable and durable adhesive joints.
Applications of Steel to Aluminum Bonding
Bonding steel to aluminum through the use of epoxy adhesives is increasingly recognized for its practical applications across various industries. This method is especially significant due to the unique attributes of both materials; steel offers high strength while aluminum is lightweight and resistant to corrosion. This combination results in products that are both durable and efficient. The epoxy adhesive serves as a connector that utilizes these distinct benefits while overcoming some inherent challenges related to the bonding process.
The applications in the automotive, aerospace, and construction sectors illustrate the versatility of epoxy bonding techniques. Each of these applications showcases not only the practical benefits of steel-aluminum combinations but also highlights considerations such as cost, performance, and long-term reliability.
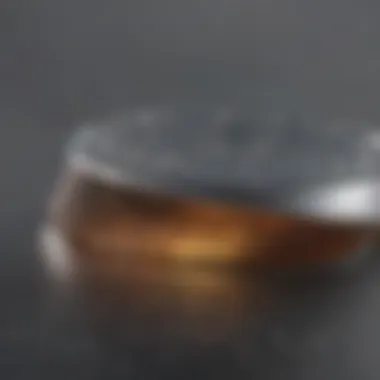
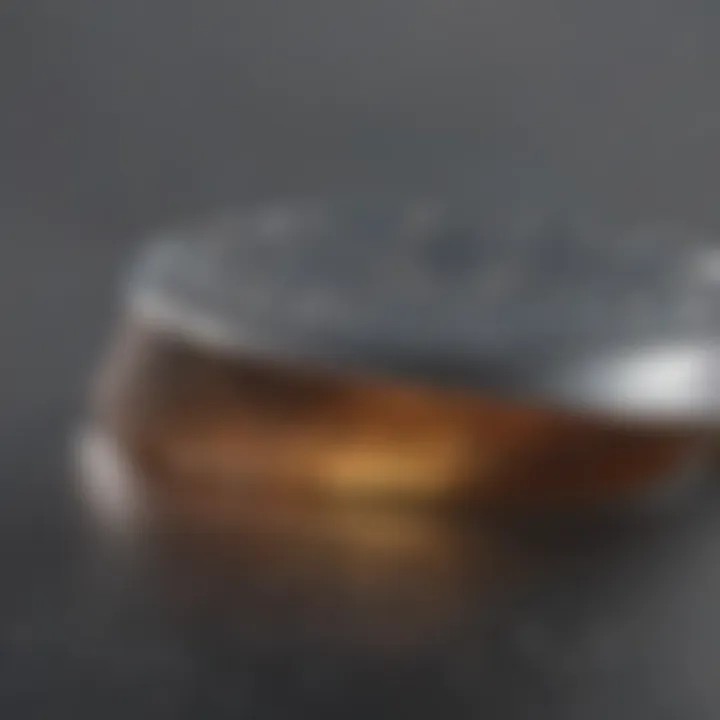
"The fusion of steel and aluminum utilizing epoxy adhesives marks a pivotal progression in manufacturing processes, yielding products that align with contemporary engineering demands."
Automotive Industry
In the automotive sector, bonding steel to aluminum is crucial for the design of lightweight structures that do not compromise safety or performance. One of the key advantages of using epoxy adhesives in this context is the ability to create strong joints without adding significant weight. This is particularly important as manufacturers strive to enhance fuel efficiency while adhering to stringent safety standards.
The use of epoxy adhesives allows for the assembly of components such as body frames and panels. Some notable benefits include:
- Reduced weight of vehicles contributes to better fuel economy.
- Increased design flexibility, enabling more complex shapes that can enhance aerodynamics.
However, it is essential for manufacturers to consider factors like thermal expansion and corrosion when using steel and aluminum together. Proper surface preparation is also vital to ensure strong adhesion.
Aerospace Industry
The aerospace industry leverages the unique properties of steel-aluminum bonding to meet rigorous standards of performance and safety. Here, epoxy adhesives are utilized to bond various components like fuselage skins and wing sections. The importance of weight reduction in aircraft design cannot be overstated; using aluminum helps save weight while maintaining the structural integrity needed for flight.
Some considerations within this field include:
- Reliability of joints under extreme conditions, including temperature fluctuations.
- The ability of epoxy adhesives to withstand varying levels of stress during operation.
Adhesives can also simplify the manufacturing process, potentially reducing labor costs and assembly time, which is critical in a rapidly advancing industry.
Construction Applications
In construction, the ability to bond steel to aluminum is invaluable, particularly in applications such as building facades, structural frameworks, and high-rise buildings. Epoxy adhesives contribute to the longevity of structures through enhanced resistance to environmental factors and corrosion.
When applied in construction, steel-aluminum bonding offers:
- Enhanced structural stability in community buildings and other large infrastructures.
- Aesthetic benefits from the natural appearance of aluminum combined with the strength of steel.
Furthermore, effective adhesion can lead to faster project timelines and reduce the need for heavy machinery since lighter materials can be used without sacrificing strength. This makes epoxy adhesives a valuable asset to the construction industry.
Overall, the applications for bonding steel to aluminum using epoxy adhesives are vast and essential to advancing technology in various sectors. Each industry benefits from improved efficiency, durability, and design versatility, demonstrating the adaptability of epoxy adhesion in modern engineering.
Future Trends in Epoxy Adhesive Technology
The realm of epoxy adhesives is evolving rapidly. As industries increasingly seek efficient, reliable, and sustainable bonding solutions, attention turns towards the future trends that will shape the development of these materials. The ongoing research and innovation in this field are not merely enhancements; they represent significant progress in manufacturing, environmental impact, and formulation technology. Understanding these trends is essential for industry professionals and researchers alike, as it aids in making informed choices about adhesive applications.
Innovative Formulations
Innovative formulations of epoxy adhesives are paving the way for enhanced performance and application versatility. New technological advancements focus on modifying the chemical structure of epoxy resins. This leads to improved adhesion properties, faster curing times, and broader temperature ranges in which adhesives can maintain effectiveness.
For example, the introduction of various fillers and additives can enhance the mechanical properties of the epoxy. These modifications can lead to increased shear strength and impact resistance, making the adhesives more appropriate for demanding environments. Additionally, smart adhesives that change properties based on environmental stimuli are gaining traction. This includes epoxies that can repair themselves after damage, thus prolonging the life of bonded materials.
"Innovative formulations are not just a trend but a necessity to meet the evolving demands of material bonding in diverse applications."
Sustainability Considerations
Sustainability is becoming a crucial element in the development of epoxy adhesives. As environmental concerns continue to rise, manufacturers are pressured to design adhesives that minimize negative impacts on the ecosystem. This includes the reduction of volatile organic compounds (VOCs) in epoxy formulations. Products with reduced VOC levels lower toxicity and improve worker safety.
Moreover, recycling options for epoxy adhesives are being explored. Research shows that recycling can be applied to certain types of cured epoxy, thus reducing waste. Biobased adhesives derived from renewable resources are part of the sustainability movement as well, offering viable alternatives to petroleum-based products. Increasing awareness of the lifecycle impact of adhesive use is pushing the industry towards more sustainable practices, ensuring that future innovations align with environmental goals.
As these trends unfold, professionals in the field must stay informed and adapt to the changing landscape of epoxy adhesive technology. Embracing innovation and sustainability will not only benefit organizations but also contribute to a healthier planet.
End
The conclusion of this article serves a crucial purpose. It encapsulates the essence of using epoxy adhesives for bonding steel to aluminum, a process that is intricate due to the properties of both materials involved. Understanding the entire context— from the properties of epoxy, surface preparation, the challenges faced, to practical applications— is critical for effective implementation.
Through our in-depth examination, we have highlighted the significant mechanical, thermal, and chemical properties of epoxy adhesives. These aspects are vital for practitioners in the field, as they assess what specific type of epoxy will best suit their bonding needs. Moreover, the challenges, particularly thermal expansion mismatch and corrosion, underscore the importance of careful selection and preparation of materials.
The relevance of various bonding techniques presented in this article cannot be understated either. Depending on the application, the choice between methods such as brush application and spray application will yield different results. Practitioners must weigh these factors to achieve optimal results.
This comprehensive analysis not only equips individuals in various industries—such as automotive, aerospace, and construction—with knowledge of effective bonding techniques, but it also sets the stage for future advancements in epoxy adhesive technology. As innovations emerge, they promise to improve both bonding efficacy and sustainability.
"A successful bond between steel and aluminum is not just about the adhesive; it's about understanding the entire process."
Ultimately, the conclusion serves as a reminder of the interconnectedness of all components in the bonding process, encouraging professionals to adopt a holistic approach in their practice.
Summary of Key Points
- Epoxy Adhesives Characteristics: They offer superior strength, thermal stability, and resistance to a variety of chemicals. These properties make them ideal for bonding steel to aluminum.
- Surface Preparation Importance: Clean and well-prepared surfaces are crucial for effective adhesion. The methods of cleaning and surface treatments can greatly influence bonding quality.
- Challenges: Understanding thermal expansion differences and possible corrosion issues is vital in preventing bond failure.
- Application Techniques: The choice of application method will affect the outcome and the efficacy of the bonding process. Different curing methods also lead to variations in performance.
- Industry Relevance: Industries such as automotive and aerospace demonstrate the practical applications of bonding steel and aluminum, showcasing the importance of epoxy adhesives in modern manufacturing.
Recommendations for Practitioners
- Select Appropriate Epoxy: Evaluate the mechanical, thermal, and chemical properties needed for your specific application. Choose an epoxy that meets these requirements.
- Prioritize Surface Preparation: Invest time in cleaning and treating surfaces thoroughly. This significantly affects the quality and longevity of the bond.
- Understand the Environment: Be aware of the operational environment the bonded materials will be exposed to. Anticipate challenges like temperature fluctuations and chemical exposure.
- Experiment with Methods: Test different application techniques to find the most effective method for your specific needs. Consider factors like ease of application and curing time.
- Stay Informed on Trends: Keep abreast of new trends and innovations in epoxy adhesive technology. Continuous learning will enhance your practice and the quality of your work.