EPDM and 3D Printing: Innovations and Implications
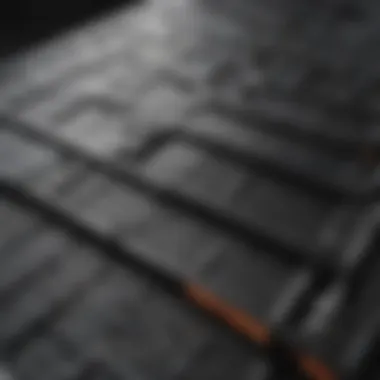
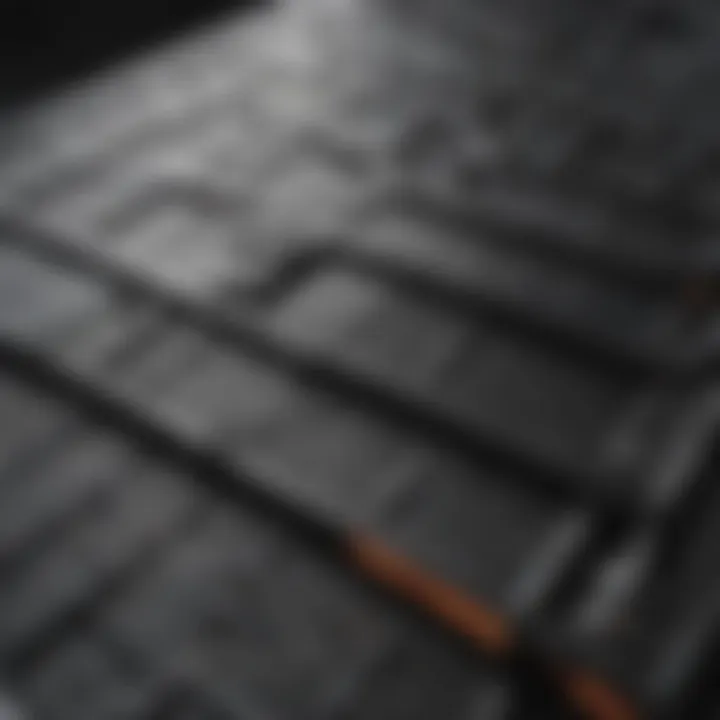
Intro
In recent years, the realms of material science and additive manufacturing have undergone significant transformations. A growing interest in exploring new materials for 3D printing has led to the examination of versatile polymers like Ethylene Propylene Diene Monomer, commonly known as EPDM. This elastomer, distinguished by its excellent weather resistance, flexibility, and durability, emerges as a compelling candidate for various applications.
As industries look for new ways to innovate and improve manufacturing processes, integrating EPDM in 3D printing presents both opportunities and challenges. Understanding the properties of EPDM and its compatibility with different printing technologies is crucial for researchers and practitioners alike. This article outlines the crucial intersections of EPDM and 3D printing, focusing on the implications and innovations stirred by this combination.
Research Context
Background Information
EPDM is a synthetic rubber widely used in automotive, construction, and consumer goods. Due to its unique chemical structure, it performs exceptionally well in extreme temperatures and under exposure to environmental factors. This versatility positions it well within the context of 3D printing, where adaptability and material properties are paramount.
3D printing, or additive manufacturing, allows the production of complex geometries that traditional manufacturing methods cannot achieve. This technology has gained traction across various sectors, from aerospace to healthcare. The intersection of EPDM and 3D printing is still an emerging field. Recent advancements in material science aim to explore how existing properties of EPDM can be harnessed through 3D printing techniques.
Importance of the Study
Investigating the integration of EPDM with 3D printing is essential for multiple reasons. First, it contributes to a better understanding of how elastomers can be effectively utilized in additive manufacturing. Second, it opens avenues for developing more sustainable production processes. Traditional manufacturing can be resource-intensive and produce significant waste. However, 3D printing has the potential to mitigate some of these impacts.
By delving into this study, we gather crucial insights into the efficiencies that might arise from using EPDM in 3D-printed applications. It raises questions about scalability, feasibility, and the long-term implications for materials engineering and manufacturing techniques.
"The exploration of EPDM within 3D printing represents a critical juncture for several industries that demand high-performing, flexible materials."
Discussion
Interpretation of Results
As the research surrounding EPDM and 3D printing evolves, preliminary results indicate a viable path towards its application in producing durable parts. Initial experiments suggest compatible printing methods like fused deposition modeling or selective laser sintering can efficiently process EPDM.
A deeper analysis of mechanical properties suggests that 3D-printed EPDM parts retain fundamental qualities like elasticity and strength. These characteristics are instrumental for applications that require resilience under stress. Considerations around print speed, layer adhesion, and resin formulation further enhance our understanding of how to optimize production.
Comparison with Previous Research
Past studies on 3D printing elastomers primarily focused on thermoplastic materials, often sidelining EPDM. However, this emerging body of research illustrates marked advantages over traditional formulations. Compared to other elastomers, EPDM showcases a unique ability to withstand harsher environments, giving it an edge in specific applications.
Researchers now have the challenge of bridging historical knowledge with experimental findings. This synergy could unlock new innovations in manufacturing, potentially impacting industries needing advanced material solutions. Detailed comparisons can inform future studies and guide practical applications in 3D printing with EPDM.
By continuing to explore the implications of EPDM in additive manufacturing, the field stands to benefit immensely from fresh perspectives and novel applications.
Prelude to EPDM
In the emerging landscape of manufacturing, Ethylene Propylene Diene Monomer (EPDM) has gained notable attention due to its unique properties and versatility. This section delves into the substance that has become essential in various applications, paving the way for innovative uses, including its integration with 3D printing technology. Understanding EPDM is vital not only for those directly involved in materials science but also for engineers and designers looking to expand their toolkit.
Definition and Composition
Ethylene Propylene Diene Monomer, commonly known as EPDM, is a type of synthetic rubber. It is primarily composed of three monomers: ethylene, propylene, and a diene component, which can vary. The combination of these materials results in a polymer with excellent weather resistance, UV stability, and enhanced elasticity. This chemical structure allows EPDM to maintain its flexibility in a wide range of temperatures and conditions, making it suitable for outdoor applications. It is worth noting that the diene is essential for cross-linking during the vulcanization process, which contributes to the final product's strength and durability.
Properties of EPDM
EPDM is characterized by several significant properties that enhance its functionality:
- Weather Resistance: EPDM rubber is highly resistant to ozone and UV light, making it ideal for outdoor applications.
- Thermal Stability: It exhibits excellent performance in both high and low temperatures, remaining functional in a range from -50Β°C to 150Β°C.
- Chemical Resistance: EPDM is resistant to a variety of chemicals, including acids and alkalis, making it suitable for multiple industrial environments.
- Elasticity and Flexibility: The rubber maintains its elasticity, which is crucial in applications such as seals and gaskets.
These attributes make EPDM a valuable material for industries that require dependable performance under varying conditions, especially when exposed to harsh environments.
Applications in Various Industries
The adaptability of EPDM allows it to be utilized in a myriad of industries. Some key sectors include:
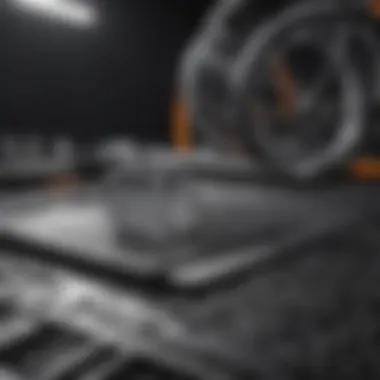
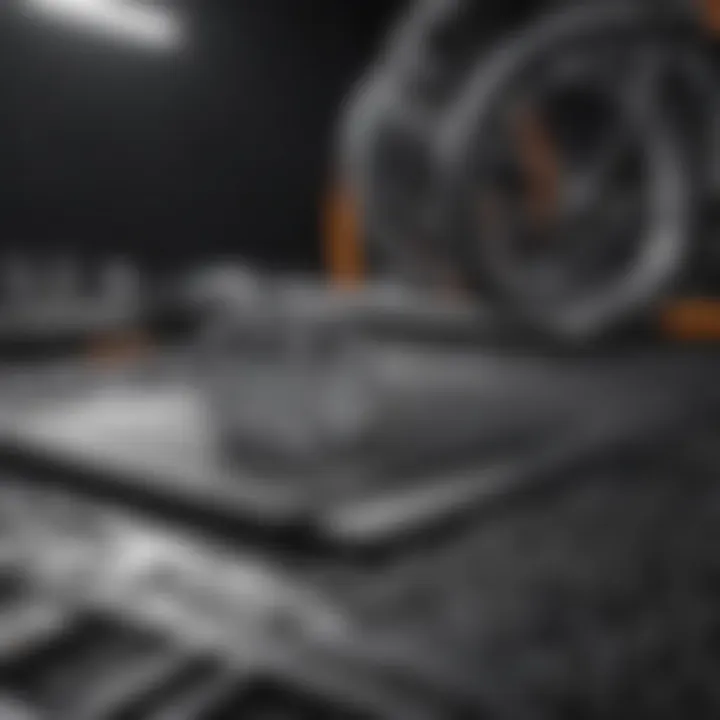
- Automotive: EPDM is commonly used for seals, hoses, and gaskets due to its weather resistance. It helps in ensuring the longevity of components within vehicles.
- Construction: In building applications, EPDM serves as an effective roofing membrane. Its durability under climatic stress extends the lifespan of roofs.
- Electrical: Its insulating properties make EPDM a preferred choice for wire and cable sheathing.
- Consumer Goods: Products ranging from garden hoses to footwear often incorporate EPDM for its elasticity and resistance to wear.
By reviewing these applications, it is clear that EPDM plays a pivotal role in modern industries, setting the stage for revolutionary advances, particularly when combined with 3D printing technologies.
Understanding 3D Printing Technologies
Understanding 3D printing technologies is critical in the context of EPDM integration. This section outlines how the various printing methods provide unique benefits and challenges that impact the use of EPDM in manufacturing. Knowledge of these methodologies deepens insight into practical applications, guiding industries in making informed decisions regarding material selection.
Overview of 3D Printing Methods
3D printing encompasses a range of technologies, each suitable for different applications. Key methods include Fused Deposition Modeling, Selective Laser Sintering, and Inkjet Printing. Each method has unique characteristics. For instance, Fused Deposition Modeling (FDM) applies melted material layer by layer. This method suits the production of flexible components like those made from EPDM. In contrast, Selective Laser Sintering (SLS) uses a laser to fuse powdered material, allowing for intricate designs. Understanding these methods enables comparisons concerning efficiency, material usage, and end-product characteristics.
Materials Used in 3D Printing
Materials play a crucial role in 3D printing. Thermoplastics, metals, ceramics, and elastomers are commonly used. Each material contributes uniquely to product properties. Thermoplastics like ABS and PLA are prevalent due to their ease of use and compatibility with various printers. However, the use of elastomers, such as EPDM, is gaining traction for its flexibility and durability. Knowing the properties of these materials helps to optimize designs for specific applications, leading to better performance and longevity of the final products.
The Role of Thermoplastics and Elastomers
Thermoplastics are widely used in 3D printing due to their favorable characteristics. They can undergo repeated melting and solidifying processes without significant degradation. Elastomers, like EPDM, provide distinct benefits in terms of flexibility and resilience. This makes EPDM particularly valuable for applications requiring dimensional stability under varying conditions. The integration of thermoplastics and elastomers in printing techniques expands functionality and opens avenues for innovative designs.
The synergy between thermoplastics and elastomers may become a focal point of future research and development, pushing the boundaries of what is possible in additive manufacturing.
Understanding the interplay of these materials and methods is vital for developers and engineers in enhancing manufacturing practices.
The Synergy Between EPDM and 3D Printing
The intersection of EPDM and 3D printing presents an intriguing area of exploration. Understanding how EPDM integrates with this technology can yield significant insights into its potential applications and impact. This synergy can lead to innovative solutions in various sectors, which rely on the unique properties of EPDM.
Compatibility of EPDM with 3D Printing Techniques
EPDM's compatibility with different 3D printing methods is vital. For instance, when incorporating EPDM into Fused Deposition Modeling (FDM), it must maintain its elastomeric properties while being extruded through the nozzle. The viscosity and temperature profile of EPDM are core factors that dictate its performance in 3D printing. Furthermore, Selective Laser Sintering (SLS) technology might require different material formulations to achieve desired mechanical characteristics. The careful selection of techniques based on EPDM's attributes is essential for optimal results.
Advantages of Using EPDM in 3D Printing
Utilizing EPDM in 3D printing brings several advantages. Some of the unparalleled properties include:
- High Elasticity: This feature allows printed parts to resist deformation under stress.
- Weather Resistance: EPDM exhibits superior resistance to UV degradation, making it suitable for outdoor applications.
- Chemical Resistance: Its compatibility with various chemicals extends the potential for use in specific industries like automotive and medical.
- Customization: The flexibility in design through 3D printing enables tailored solutions that traditional manufacturing methods cannot easily achieve.
These characteristics make EPDM a material of choice for many advanced applications across industries.
Limitations and Challenges
Despite its advantages, using EPDM in 3D printing does not come without its problems. Some key limitations include:
- Processing Temperatures: The optimal processing temperature for EPDM can be a hurdle, necessitating specialized equipment for successful printing.
- Adhesion Issues: Achieving proper adhesion between the layers can be tricky, possibly leading to weaker structures.
- Material Sourcing: High-quality EPDM compatible with 3D printing technology may not be readily available, impacting production timelines.
"Integrating EPDM with 3D printing requires a comprehensive understanding of material properties and printing techniques."
Navigating these challenges is critical for harnessing the full potential of EPDM in 3D printing applications. Identifying and addressing these issues can lead to innovative solutions that push the boundaries of what is achievable in manufacturing.
3D Printing Techniques for EPDM
The exploration of 3D printing techniques specifically for Ethylene Propylene Diene Monomer (EPDM) rubber is essential for understanding its practical applications and advantages in various industries. EPDM, known for its durability and elasticity, is gaining traction in the 3D printing domain. The choice of printing techniques influences the material's properties and the final application.
In this section, we examine three primary techniques used for 3D printing with EPDM: Fused Deposition Modeling, Selective Laser Sintering, and Inkjet Printing. Each has its unique benefits and considerations that affect the overall printing process and resulting properties of the printed parts.
Fused Deposition Modeling with EPDM
Fused Deposition Modeling (FDM) is one of the most accessible 3D printing techniques and is well-suited for EPDM. In FDM, a thermoplastic filament is melted and extruded through a heated nozzle. For EPDM, specific filaments must be developed to ensure proper melting and flow characteristics. The temperature settings and nozzle design are crucial for maintaining the integrity of the material.
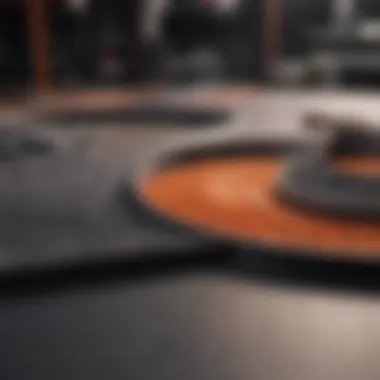
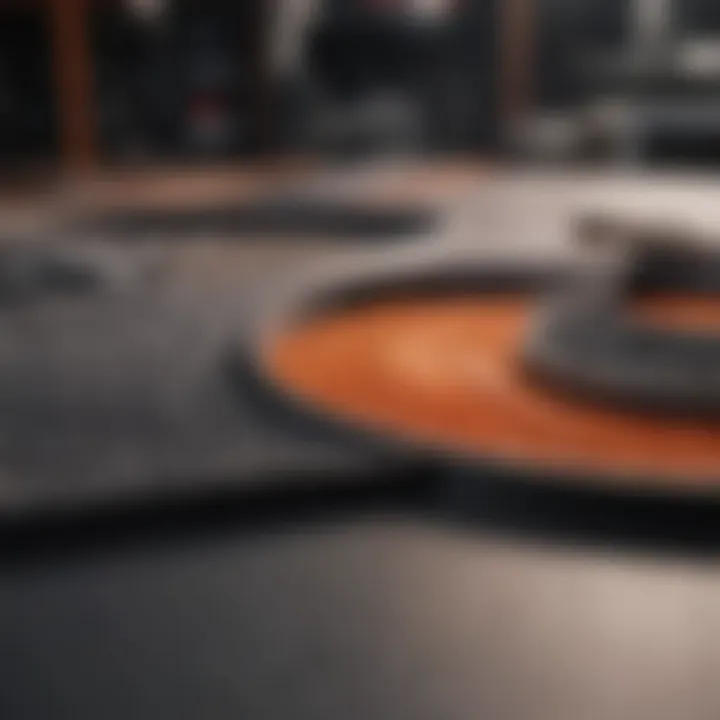
Advantages of using FDM with EPDM include:
- Cost-effectiveness: FDM equipment and materials are generally affordable and widely available.
- Ease of use: The technique is user-friendly and does not require advanced technical expertise.
- Material versatility: FDM allows for the use of blended materials, integrating EPDM with other polymers for enhanced properties.
However, there are challenges as well:
- Print resolution limitations: FDM may not achieve the fine detail that other techniques can, which can affect the surface finish.
- Thermal sensitivity: EPDM can degrade if exposed to high temperatures for too long during printing.
Selective Laser Sintering and EPDM
Selective Laser Sintering (SLS) represents another sophisticated method for 3D printing with EPDM. In SLS, a laser selectively fuses powdered material together layer by layer to create a solid object. This process is particularly advantageous for EPDM as it allows for complex geometries and strong interlayer bonding.
The benefits of using SLS include:
- High precision and detail: SLS can produce intricate designs with sharper edges and smoother surfaces.
- Durability: Parts printed with EPDM using SLS generally have superior mechanical properties and can withstand harsh environments.
- Customization: SLS enables the production of both small and large batches with minimal reconfiguration, making it ideal for prototyping.
Yet, there are some considerations to keep in mind:
- Higher costs: SLS equipment and materials can be expensive compared to other methods.
- Post-processing requirements: Often, parts need additional finishing to remove excess powder and improve surface finish.
Inkjet Printing Applications
Inkjet printing is an emerging technology in the realm of 3D printing, offering a direct method for layer formation through liquid deposition. This technique is advancing the capabilities of EPDM in producing complex structures with minimal waste. Inkjet printing utilizes a print head to jet liquid EPDM precursor onto a substrate or previous layer, where it solidifies.
The potential benefits of inkjet applications include:
- High detail reproduction: Inkjet can achieve fine details and complex designs, which is particularly useful in specialized applications like medical devices.
- Lower material waste: The process typically creates less excess material compared to bulk processes like FDM or SLS.
- Rapid prototyping capabilities: Changes can often be made quickly, allowing for iterative design processes.
However, inkjet printing also faces challenges:
- Material limitations: Finding suitable ink formulations that preserve EPDM's desirable properties can be challenging.
- Speed: While details are high, inkjet printing can be slower than other methods for larger objects.
In summary, the choice of 3D printing technique has significant implications for how EPDM is utilized in production. Each method offers unique advantages and drawbacks that should be evaluated in the context of specific applications.
Case Studies and Real-World Applications
In the context of this article, exploring case studies and real-world applications of EPDM in 3D printing serves a crucial role. It bridges the gap between theoretical discussions and practical uses, offering tangible examples of how this integration is transforming various industries. By examining actual implementations, we can better understand the material benefits, tackle challenges effectively, and inspire further research and innovation in the field.
Automotive Industry Innovations
The automotive sector has witnessed significant advancements through the use of EPDM in 3D printing. As car manufacturers continue to seek lighter, more durable materials that can be produced rapidly, EPDM emerges as a fitting candidate. Its excellent elasticity and resistance to weathering make it suitable for seals, gaskets, and other components. For instance, BMW has reportedly utilized 3D printing with EPDM to produce custom seals for vehicle interiors, which enhances both comfort and vehicle performance.
Another noteworthy example is Ford, which has explored creating prototypes using 3D-printed EPDM components. This method not only reduces traditional production times but also allows for customization at a scale that was previously impractical. The ability to iterate designs quickly aids engineers in refining vehicle parts, significantly boosting efficacy and innovation.
Medical Device Development
Medical device development benefits enormously from the properties of EPDM when 3D printed. This materialβs flexibility and biocompatibility make it an ideal choice for devices that require both durability and the ability to withstand various physiological conditions. As an example, the production of custom prosthetics has been revolutionized through the integration of EPDM in 3D printing. Companies like Limbitless Solutions have successfully created lightweight prosthetic limbs that offer improved comfort for users.
Furthermore, 3D printing allows for the rapid prototyping of medical devices such as tubing and connectors. These components often require specific properties that EPDM can provide, such as resistance to chemicals and temperature fluctuations. By harnessing EPDMβs qualities, doctors can create tailored solutions for patients, enhancing overall healthcare outcomes.
Consumer Product Design
Lastly, the consumer product design industry has seen a significant impact from using EPDM in 3D printing. Products like footwear and home appliances have incorporated EPDM's elastomeric properties to achieve better functionality and design aesthetics. Companies such as Adidas have explored the possibilities of 3D-printed footwear featuring EPDM soles, which combine comfort with style. This not only caters to the growing demand for customization among consumers but also leverages the benefits of swift production times that 3D printing offers.
Additionally, household items have also been brought to life using EPDM. The flexibility and durability of this material enable the development of innovative storage solutions, tools, and custom-designed decor. As manufacturers continue to test and explore EPDM's potential, the possibilities in consumer product design remain rich and diverse.
In summary, case studies across automotive, medical, and consumer product sectors demonstrate the practical viability of EPDM in 3D printing, showcasing specific innovations that drive industry advancements.
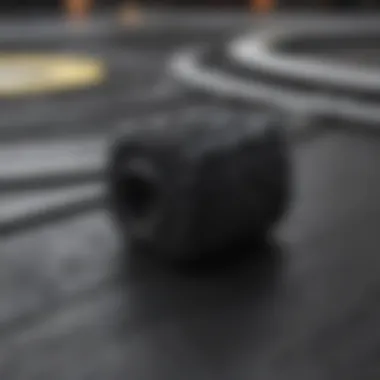
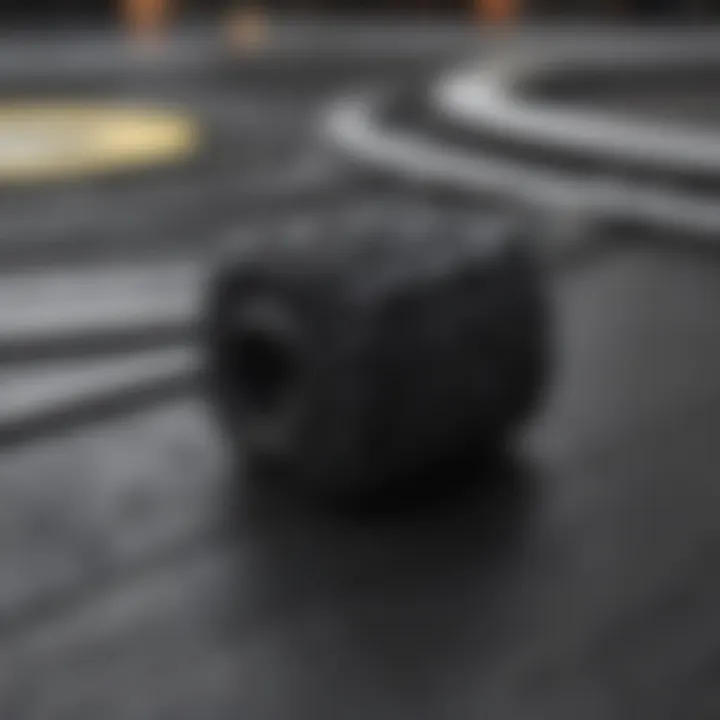
With these examples, it is clear that the intersection of EPDM and 3D printing leads to innovations that enhance functionality while addressing the specific needs of various market segments.
Environmental Impact and Sustainability
Understanding the environmental implications of using Ethylene Propylene Diene Monomer (EPDM) in 3D printing is crucial for future developments in both fields. As concerns about waste management and sustainability increase, industries must adapt and innovate. This is especially true for materials like EPDM, which, while offering distinct advantages in various applications, also poses environmental challenges. By examining the environmental impact and sustainability of EPDM in 3D printing, we can gain insights into responsible manufacturing practices and aim for a more sustainable future.
Recycling EPDM Waste in 3D Printing
Recycling EPDM waste presents challenges but also opportunities. EPDM is known for its durability and resistance to environmental factors, making it less susceptible to degradation. This stability means that once it is used, waste can linger in landfills if not properly managed. However, advances in recycling technologies allow for the reclamation of EPDM waste.
- Material Recovery: Through methods like grinding and reprocessing, waste EPDM can be transformed back into usable materials for 3D printing. This process minimizes the volume of rubber waste, contributing to a more circular economy.
- Energy Savings: Recycling reduces the energy required to produce new EPDM products from raw materials. This not only lowers the carbon footprint but also promotes resource conservation.
- Collaborative Efforts: Companies in the 3D printing industry can partner with recycling facilities to develop better systems for EPDM waste. These strategic alliances can improve the efficiency of waste management practices.
"The future of 3D printing relies heavily on how well we manage material waste. Recycling is a cornerstone of this challenge."
Biodegradability of 3D Printed EPDM Products
Biodegradability is another significant aspect when assessing the environmental impact of 3D printed EPDM products. Traditional EPDM does not decompose easily, which raises concerns regarding long-term environmental effects. Current research is aimed at understanding and improving the biodegradability of this elastomer within 3D printed applications.
- Innovative Blends: Researchers are exploring the creation of EPDM blends with biodegradable additives. These blends could potentially break down more easily in natural environments.
- Testing Protocols: Various standards and methods can be implemented to test the biodegradability of 3D printed EPDM. By establishing performance benchmarks, manufacturers can better understand the environmental behavior of their products.
Sustainable Manufacturing Practices
Embracing sustainable manufacturing practices in conjunction with 3D printing technologies is vital. Companies must consider not only the material itself but also how it is produced and disposed of. The following practices can help mitigate the environmental impact of using EPDM in 3D printing:
- Efficiency in Production: Utilizing additive manufacturing allows for precise material usage, which reduces waste during production. It is essential to optimize processes to further limit the consumption of energy and resources.
- Lifecycle Analysis: Conduct comprehensive lifecycle assessments of 3D printed EPDM products. This involves examining every stage, from sourcing materials through manufacturing to disposal, improving areas that impact overall sustainability.
- Supplier Collaboration: Work with suppliers who prioritize sustainability. This can help ensure that the sourced materials meet environmental standards and are responsibly produced.
In summary, the intersection of EPDM and 3D printing requires a commitment to environmental considerations. Recycling EPDM waste, improving biodegradability, and adopting sustainable practices will drive advancements in this field, allowing industries to innovate while addressing ecological concerns.
Future Perspectives of EPDM in 3D Printing
The integration of EPDM with 3D printing holds significant importance for the future of manufacturing. As industries increasingly seek innovative and efficient materials, EPDM emerges as a viable option. Its excellent elasticity and resistance to weathering, heat, and chemicals make it an attractive candidate for numerous applications in 3D printing. This section examines the anticipated developments, market potential, and collaborative efforts that will influence the future landscape of EPDM in this technology.
Technological Advances Expected
The evolution of 3D printing technology is advancing rapidly. EPDM printing methods are improving, as developers focus on enhancing the material's properties for better performance. New techniques, such as optimized printing parameters and advanced nozzle designs, increase the efficiency of printing with EPDM.
- High-resolution printing: New printer models are offering improved resolution, allowing for more intricate designs using EPDM. This will be essential for applications requiring precision, such as in automotive parts or medical devices.
- Hybrid materials: Combining EPDM with other materials may yield enhanced properties. For example, blending it with thermoplastics can provide better adhesion and durability, expanding its scope of application.
- AI-driven design: Utilizing artificial intelligence in the design phase can streamline the process, leading to optimized shapes and geometries that take full advantage of EPDM's flexible nature.
Potential Market Growth
The potential market growth for EPDM in 3D printing is vast. As stakeholders in various sectors recognize the benefits of employing EPDM, demand is likely to surge. Several factors contribute to this expected growth:
- Increased adoption in various industries: Industries such as construction, consumer goods, and electronics are exploring the uses of 3D printed EPDM. This can lead to the development of customized products catered to specific needs.
- Cost-effectiveness: 3D printing reduces production costs and waste. EPDM's availability and recyclability further enhance its appeal in the market.
- Consumer preferences: As consumers demand more sustainable and customized products, companies will need to adapt. Use of EPDM in 3D printing can help satisfy these demands by producing user-centric designs efficiently.
Interdisciplinary Collaborations
Collaborations across disciplines will shape how EPDM is integrated into 3D printing applications. For example, partnerships between material scientists, engineers, and software developers can yield significant advancements. Here are key collaborative avenues:
- Research institutions: Engaging with universities can drive innovation. Research on EPDM's unique properties can lead to better methods of processing and finishing prints.
- Software development: Collaborating with tech companies to create software that optimizes printing with EPDM can enhance the quality of the final product. This ensures that users can efficiently generate prototypes and parts without extensive manual adjustments.
- Industry partnerships: Collaborations among manufacturers can lead to standardized practices. This could streamline the adoption of EPDM in 3D printing facilities, allowing more businesses to harness its benefits effectively.
The future of EPDM in 3D printing looks promising, with numerous advances and collaborations setting the stage for innovative applications across different sectors.
Culmination
In this exploration of EPDM and 3D printing, we understand the profound connections between these two materials. Each section discussed the role of EPDM in the world of additive manufacturing. This conclusion emphasizes the critical aspects outlined throughout the article.
EPDM, known for its excellent weather resistance and flexibility, presents unique advantages when integrated with various 3D printing methods. The material's compatibility with Fused Deposition Modeling, for instance, enhances the efficacy of printed parts in different applications. Moreover, the sustainability aspect of utilizing EPDM in 3D printing cannot be ignored. Recycling opportunities and the potential for biodegradable components contribute positively to environmental goals.
Furthermore, potential market growth in industries ranging from automotive to medical devices illustrates the versatility of this material. As 3D printing technology advances, so too will the techniques related to EPDM. Interdisciplinary collaborations may lead to innovations that further streamline the integration of these technologies.
"A sustainable approach to manufacturing is no longer just an option; it is essential for future success."
In summary, the combination of EPDM with 3D printing offers significant benefits, challenges, and opportunities, marking an important milestone in modern manufacturing practices. This integration signals a shift towards more adaptive, efficient, and environmentally friendly production methods that hold promise for the future.
As professionals, researchers, and students in the field continue to engage with these topics, further exploration and innovation are expected to emerge. The implications derived from this intersection may significantly shape how we approach material usage and technological development."