Brake Manufacturing: Exploring Components and Technologies
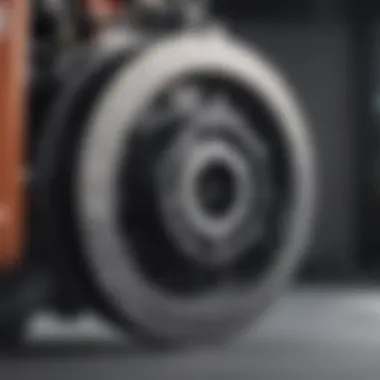
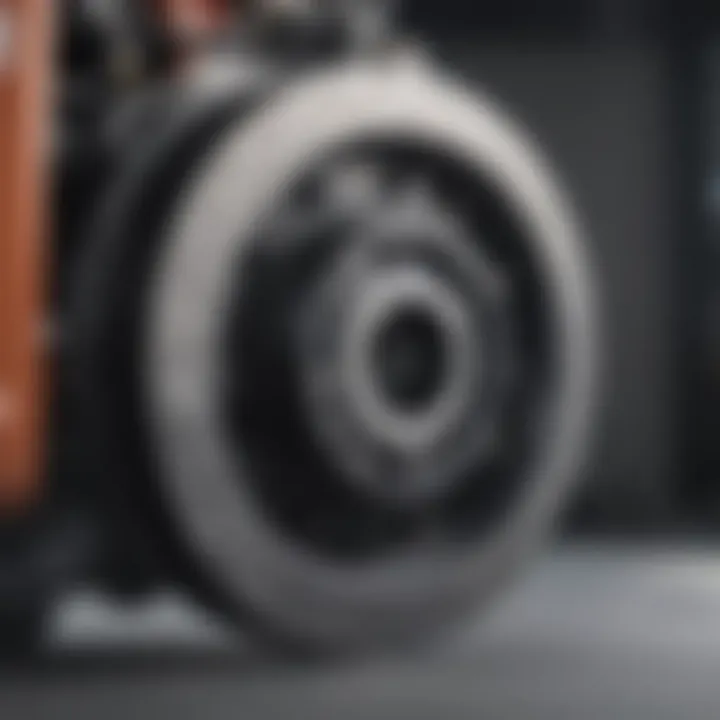
Intro
The automotive sector has seen a dramatic transformation over the decades, with brake manufacturing at the forefront of these advancements. Understanding the nuances of brake systems is not just an academic pursuit; it is crucial for ensuring safety on the roads. From the rusted drums of yesteryears to today's high-tech disc brakes, the journey reflects a commitment to innovation and efficiency. This article endeavors to dissect the intricate layers of brake manufacturing, examining both the art and the science behind these vital components.
Research Context
Background Information
At its core, brake manufacturing encompasses a critical blend of materials, engineering, and technology. Various components come into play: rotors, calipers, pads, and more. Each plays a role in how effectively a vehicle can decelerate. The selection of materials, such as ceramic and composite, greatly influences performance and longevity. Moreover, environmental factors also need to be considered, with manufacturers consistently seeking ways to enhance durability while minimizing ecological impact.
Importance of the Study
This study is pivotal for several reasons. First, the safety of vehicles heavily relies on braking systems. Poorly manufactured brakes can lead to catastrophic failures, putting lives at risk. Understanding the processes behind brake manufacturing can serve to educate both industry professionals and consumers, fostering informed decisions in vehicle purchasing and maintenance. Additionally, by analyzing advancements in brake technology, we gather insights that can lead to further improvements in automotive safety standards and regulations.
Discussion
Interpretation of Results
As we traverse through the history of brake manufacturing, there is a evident trend toward higher performance and safety. For instance, the shift from simple mechanical systems to advanced hydraulic and electronic brake systems offers a glimpse into the industryβs evolution. Modern developments like Anti-lock Braking Systems (ABS) and Electronic Stability Control (ESC) exemplify this shift, providing drivers with an enhanced level of control during adverse conditions.
Comparison with Previous Research
Comparing todayβs technologies with earlier methodologies reveals significant progress. Research from the early 2000s focused primarily on material strength and thermal resistance, while recent studies dive deeper into integrating smart technologies into braking systems. Systems that adjust braking force based on driving conditions not only improve safety but also boost overall vehicle performance.
"The refinement in brake technology has a direct correlation with both vehicle performance and occupant safety, making it a critical focal point for research and development in the automotive industry."
Such advancements underscore the importance of continual research and adaptation in this domain. The connection between improved manufacturing processes and increased vehicle safety is a testament to the necessity for innovation in brake systems in the automotive sector.
This overview sets the groundwork for a detailed exploration of the specific processes, technologies, and materials that define modern brake manufacturing. The focus will shift to practical applications and breakdowns of how these systems are implemented in vehicles today.
Prolusion to Brake Manufacturing
In the world of automotive engineering, the importance of effective brake systems cannot be overstated. They are an essential component that enhances safety, performance, and overall vehicle reliability. By enabling rapid deceleration and providing the driver with a sense of control, brake systems play a crucial role in vehicular safety.
A well-designed brake system requires a comprehensive understanding of various materials, processes, and technologies. Itβs not merely about products that stop a car; itβs about engineering precision, quality control, and continual advancement for enhanced safety.
Importance of Brake Systems in Vehicles
Brake systems serve as the primary means for controlling a vehicle's speed and stability. They are not just mechanical components; they are the lifeline that ensures the driver can stop safely. Without effective braking mechanisms, the risk of accidents dramatically increases. Consider the role of brake systems in emergency situations, where instantaneous stopping can distinguish between a near-miss and a serious collision.
The safety implications are profound β faulty brakes lead to catastrophic failures. For instance, between 2011 and 2015, it was reported by the National Highway Traffic Safety Administration that almost 30% of all vehicle crashes were a direct result of brake failure.
Thus, an understanding of the intricacies of brake systems is essential for engineers, manufacturers, and consumers alike. Proper maintenance and the right choice of materials can make all the difference in safety and efficiency.
Overview of the Brake Manufacturing Industry
Brake manufacturing is a highly specialized field that encompasses a wide array of processes, materials, and innovations. It is influenced by legislative requirements, technological advancements, and consumer expectations. As the automotive industry continues to evolve, those engaged in brake manufacturing must also adapt to changes in design methodologies and sustainability practices.
Manufacturers focus on techniques such as casting, machining, and quality control to ensure that each component meets rigorous standards. Not only do they need to adhere to safety regulations, but they also face the challenge of creating products that are environmentally friendly and economically viable.
Moreover, in this competitive market, manufacturers invest heavily in research and development to push boundaries, aiming to create more efficient, effective, and durable braking systems. The integration of innovative materials and smart technologies has paved the way for advanced braking solutions that can significantly enhance vehicle performance.
The brake manufacturing industry is an evolving landscape where safety, quality, and performance converge.
Historical Development of Brake Technology
The journey of brake technology is as vital as the brake systems themselves. This section maps out how brakes have transformed over the decades and why understanding this evolution is crucial. The progression in brake technology reflects the broader advancements within the automotive sector. Old-fashioned systems often posed challenges related to safety and performance. By examining the timelines and changes, we can gain insights into not just the development of materials and designs, but also the regulatory responses that have shaped modern braking systems.
Early Brake Designs
Looking back at the origins of braking systems, one might picture rudimentary designs that were as dependable as a house of cards. The earliest brakes were often created of wood, leather, or metal and were fitted to carriages. For instance, the wooden blocks that were pressed against the wheels of horse-drawn vehicles showcased both ingenuity and limitation. These brakes often relied heavily on friction, but they lacked sophistication and reliability.
Unfortunately, their weaknesses were all too apparent. In heavy rain or rough landscapes, those wooden brakes could easily fail, resulting in quite the calamity. As the automotive industry began to blossom in the early 20th century, the demand for more effective braking mechanisms became apparent. The introduction of drum brakes marked the first significant stride towards more efficient designs.
Drum brakes operate by using friction generated between the inner surface of a spinning drum and an outer brake shoe. However, they too had their quirks and limitations, especially when it came to dissipating heat. As brake fade became a problem during prolonged usage, manufacturers began to innovate, laying the groundwork for the evolution that was to follow.
Evolution of Automotive Braking Systems
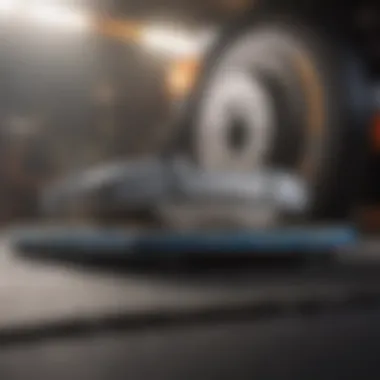
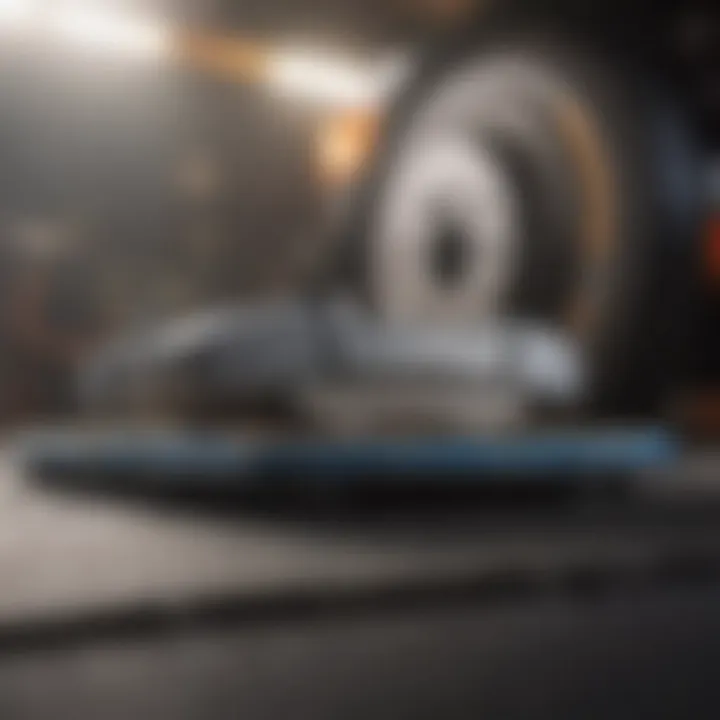
Fast forwarding through time, the evolution of automotive braking systems is a testament to human ingenuity and the relentless pursuit of safety and reliability. In the mid-20th century, disc brakes started making waves. This change was not just an improvement β it was a revolution. Disc brakes, with their rotor-and-caliper design, provided significantly better performance and heat dissipation. Drivers could feel the difference almost immediately β improved stopping power and response were simply undeniable.
As we moved into the 21st century, advancements in technology brought about electronic braking systems. These systems rely on electronic signals to adjust the brake force applied, leading to more precise control and efficiency. Features such as Anti-lock Braking Systems (ABS) and Electronic Brake-force Distribution (EBD) have made todayβs vehicles safer than ever. No longer is braking a leap of faith; itβs a finely tuned orchestration of engineering marvels.
"The progress in brake technology is not merely an advancement against time; itβs a pledge to safety, functionality, and control."
Among the latest innovations, regenerative braking systems, often found in electric and hybrid vehicles, utilize the kinetic energy produced during braking to charge the vehicleβs battery. This not only enhances efficiency but also reduces wear on traditional brake components. Itβs a perfect illustration of how the past informs the future, balancing traditional braking techniques with modern sustainability goals.
In summary, understanding the historical development of brake technology is essential. It provides clarity on why current standards exist and emphasizes the continual need for improvement in safety and functionality. As we look ahead, itβs important to recognize that while we stand on the shoulders of past innovations, the road to future enhancements is paved with ongoing research and development.
Key Components of Brake Systems
A brake system is not simply a collection of parts; itβs a finely tuned assembly that plays a vital role in vehicular safety and performance. Understanding the key components of brake systems is essential not just for manufacturers but also for consumers and anyone involved in the automotive sector. Each part has its specific function, and their collective harmony ensures that a vehicle stops efficiently and safely. Let's delve deeper into the primary components that make up this critical system.
Brake Pads and Shoes
Brake pads and shoes are the frontline defenders in stopping a vehicle. Made from friction materials, they press against the rotors or drums when the brake pedal is engaged, creating the necessary friction to slow down or halt the vehicle. The choice of material, commonly ceramic, organic, or semi-metallic, directly influences the performance, noise levels, and longevity. For instance, ceramic pads often produce less dust and noise compared to their metal counterparts but may not withstand high temperatures as effectively.
Regular inspection of brake pads is crucial, as worn-out pads can lead to increased stopping distance and potential damage to other components, such as rotors. Ignoring signs of wear can ultimately result in more costly repairs down the line. As such, manufacturers emphasize the importance of using high-quality materials that meet or exceed industry standards, ensuring safety while maintaining cost-effectiveness.
Rotors and Discs
Rotors, or brake discs, are the surface against which the brake pads work. They are typically made from cast iron or carbon composite materials, designed to dissipate heat generated during braking. Heat management is essential since excessive temperatures can lead to brake fade, a condition where brakes become less effective due to overheating.
Different types of rotors exist: vented, slotted, and drilled, each designed to optimize performance under various conditions.
- Vented rotors allow for better cooling.
- Slotted rotors help in keeping the pad surface clean by venting gas generated during braking.
- Drilled rotors, though common in performance applications, are often less durable due to their weight reduction.
Selecting the right type of rotor can significantly impact the braking performance of a vehicle, especially in high-performance and heavy-duty applications.
Calipers and Master Cylinders
The brake caliper plays a pivotal role in the braking process. It houses the brake pads and contains pistons that apply pressure to them. When the brake pedal is pressed, the master cylinder sends brake fluid through the hydraulic lines, pushing the caliper pistons, which in turn clamps the brake pads onto the rotor. This action converts hydraulic energy into mechanical force, resulting in vehicle deceleration.
The master cylinder is often overlooked, but itβs the heart of the hydraulic brake system. Any malfunction here can lead to total brake failure, making its regular maintenance critical. Different vehicles may utilize single or dual master cylinders, depending on their design and safety requirements.
"In a braking system, the coordination among calipers, pads, and rotors is as crucial as a well-timed clockwork. Mess one up, and the whole system falters."
Understanding how these components work together not only enhances manufacturing designs but also informs consumers when maintaining their vehicle's braking system. Itβs vital for both safety and performance to ensure every part is in good working order, as deficiencies in one can compromise the entire system.
Materials Used in Brake Manufacturing
Understanding the materials used in brake manufacturing is pivotal for anyone delving into this industry. The choice of materials not only influences the performance of the brake systems but also impacts safety, longevity, and environmental sustainability. With vehicles increasingly adopting more advanced braking technologies, the materials must match these innovations while adhering to strict safety standards.
Types of Friction Materials
Friction materials are at the heart of brake systems, and their selection can make or break performance. Traditional options, like asbestos, have fallen out of favor due to health hazards; instead, modern materials are often formulated from a blend of organic compounds, metallics, and ceramics.
When evaluating these materials, consider the following:
- Organic Materials: These typically contain a mix of synthetic resins. Theyβre quieter and generate less dust, making them a popular choice for passenger vehicles.
- Semi-Metallic Materials: Incorporating steel fibers, these materials provide excellent thermal resistance and performance under extreme conditions but may produce more noise during operation.
- Ceramic Materials: These deliver excellent heat dissipation and low levels of dust, all while achieving a longer lifespan. Their high performance makes them suitable for a range of vehicles, especially in high-performance and luxury categories.
One example of innovative friction material is the use of carbon-based compounds, designed to enhance both performance and environmental friendliness.
Metals and Alloys in Brake Components
The metals and alloys involved in brake components are selected for their unique properties. The most frequently used materials include iron, aluminum, and various steel alloys. Their roles are crucial in construction to ensure durability and performance.
- Cast Iron: This material is commonly used in rotors because of its excellent wear resistance and ability to absorb heat effectively.
- Aluminum Alloys: Used mainly in caliper designs, these materials help reduce weight, which contributes to overall vehicle efficiency without compromising performance.
- High-Carbon Steels: Known for being robust, these are used in components that require exceptional strength.
Each choice can lead to distinct outcomes in brake performance, like fade resistance under heavy braking or sensitivity to temperature changes, showing how materials deeply affect driving experience.
Innovative Materials in Modern Brakes
Progress in brake technology has led to the exploration and use of several innovative materials. These newer options aim at not just performance enhancement but also environmental considerations.
- Carbon-Carbon Composites: These are used in high-performance applications like aviation and motorsport due to their lightweight and impressive thermal properties.
- Thermoplastics: Emerging as a viable option, these materials can withstand high temperatures and thereby improve overall brake efficiency.
- Natural Fibers: Research into biodegradable options has led to the investigation of materials such as hemp and flax in brake pads, reflecting a growing emphasis on sustainability.
"The materials we choose not only affect braking efficiency but also the broader environmental impact of vehicle operations," said a recent publication on innovations in brake systems.
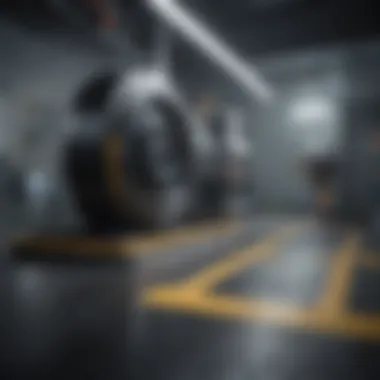
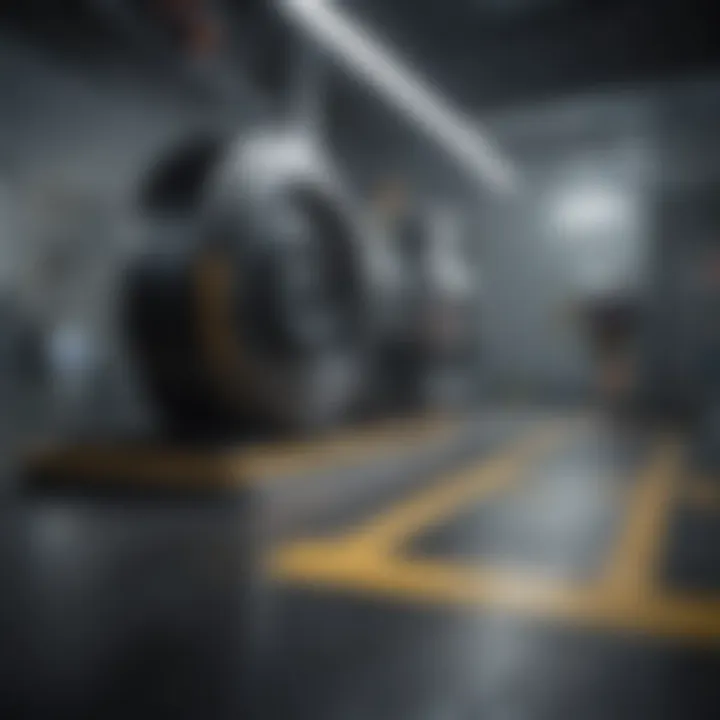
Brake Manufacturing Processes
The process of brake manufacturing is an integral part of the automotive industry, as it ensures the utility and reliability of one of the most critical systems in any vehicle. The value of understanding brake manufacturing lies in today's world where safety cannot be compromised. Efficient brake systems not only constitute a vehicle's performance but can also make the difference between life and death on the road. From the selection of materials to the machining techniques employed in production, every aspect plays a role in the final product's effectiveness.
Casting and Forging Techniques
Casting and forging are pivotal in the initial stages of brake component manufacturing. Casting allows for larger and more intricate shapes to be created easily by pouring molten metal into molds. This technique is especially popular for manufacturing brake rotors. The intricate patterns that can be cast help create better heat dissipation characteristics in performance brake systems. Different alloys also lend themselves well to casting, often enhancing performance and longevity of the components.
On the other hand, forging tends to produce stronger components. The process involves shaping metal using localized compressive forces. Many high-performance brake parts utilize forging techniques, leading to superior mechanical properties. For instance, calipers often undergo forging to withstand the pressure generated during braking.
In summary, both casting and forging play specific yet crucial roles in ensuring that brake components meet rigorous standards for performance and durability. The choice between the two can depend on the desired properties of the finished product.
Machining and Surface Finishing
Once the initial shape of the brake components has been established through casting or forging, they undergo machining and surface finishing processes. This step is all about precision. Components such as brake pads require fine tolerances to ensure proper contact with rotors. Various machining techniques, including milling and grinding, are employed to achieve these specifications.
Surface finishing is equally important. A smooth surface finish can help prevent stress concentrators that lead to cracking. Brake components often go through processes like shot peening or polishing to improve surface characteristics. Such enhancements lead to better wear resistance and prolong the component's life, aligning with broader safety and sustainability goals in manufacturing.
Quality Control in Manufacturing
Quality control serves as the backbone of brake manufacturing processes. All items must adhere to specific standards to ensure safety and reliability. Various methods are used to scrutinize the products, from visual inspections to sophisticated nondestructive testing.
A few critical points regarding quality control include:
- Compliance with Standards: It's crucial that manufacturers adhere to stringent regulations, such as those outlined by the Society of Automotive Engineers or ISO standards.
- Performance Testing: Components are often tested under simulated conditions to evaluate their performance, checking for factors like friction and thermal stability.
- Documentation and Traceability: Each component often has a detailed history of its manufacturing process, which becomes vital for recalls or safety analyses in the future.
"Quality control isn't just a checkpoint; it's a culture ingrained in the manufacturing process that regards safety above all else."
Ultimately, effective quality control measures contribute to the overall safety of brake systems and enable manufacturers to uphold their reputations in the industry.
Safety Considerations in Brake Design
When one thinks about automotive design, the first thing that comes to mind might be power, speed, or innovative features. However, none of these mean a hill of beans if the brakes donβt inspire confidence. The importance of safety considerations in brake design cannot be overstated. With lives literally hanging in the balance every time a vehicle hits the road, manufacturers must adhere to stringent safety protocols throughout the entire design and production process.
Safety in brake manufacturing encompasses various facets, including regulatory compliance, material selection, design methods, and constant performance evaluation. Each of these elements works in tandem to ensure that vehicles not only stop reliably but do so under the diverse conditions they face daily. Without a focus on these safety considerations, the repercussions could be catastrophicβfor drivers, passengers, and pedestrians alike.
Regulatory Standards and Compliance
In the evolving landscape of vehicle technology, adhering to regulatory standards is paramount. These standards, often established by governing bodies worldwide, provide a framework for what qualifies as a safe brake system. For instance, in Europe, the ECE Regulation No. 90 outlines how replacement brake pads should meet performance standards similar to original equipment.
Manufacturers must stay abreast of these regulations to ensure compliance. Failing to meet these obligations can lead to costly recalls or, worse yet, a loss of faith from consumers. In today's market, where consumer safety is a primary selling point, companies can't afford to cut corners.
Furthermore, regulatory agencies frequently update standards based on advances in technology and feedback about performance. For example, electronic braking systems have introduced new performance metrics that must be accounted for under these regulations. Keeping ahead of the curve requires an ongoing commitment to monitoring the developing standards and integrating them into production and design strategies.
Impact of Brake Failure
Ah, brake failureβthe stuff of nightmares for any driver. The implications of malfunctioning braking systems can be severe, ranging from minor accidents to catastrophic collisions, especially at high speeds. Understanding the impact of brake failure on vehicle safety is essential for manufacturers who wish to design effective systems.
Common causes of brake failure include wear and tear on components, air bubbles in brake lines, or even software issues in advanced electronic systems. An alarming statistic reveals that around 30% of vehicle accidents can be attributed to issues with brakingβthis speaks volumes about the necessity of thorough testing and reliable design.
When a brake system fails, it is often a series of failures rather than a lone issue. For example, worn-out brake pads can lead to increased wear on rotors, causing a cascading effect that can compromise the entire braking system. Addressing these potential pitfalls requires rigorous quality control and proactive maintenance strategies.
"A vehicle with inadequate brakes is like a ship without sailsβset adrift and vulnerable to disaster."
To mitigate the impact of brake failure, manufacturers must implement enhanced safety features, such as redundant systems that ensure braking capabilities, even when one component fails. This layered approach helps safeguard against unexpected failures, protecting both the driver and other road users.
In summary, safety considerations in brake design are not just a checkbox on a listβthey are the backbone of successful and responsible automotive manufacturing. By focusing on regulatory compliance and understanding the ramifications of brake failure, manufacturers take essential steps toward ensuring the safety of their customers. This vigilance is what ultimately leads to increased trust and reliability in brake systems, reinforcing the foundation of a well-designed vehicle.
Advancements in Brake Technology
The realm of brake technology has seen remarkable advancements in recent years. As vehicles evolve and become more complex, so too must the systems that ensure their safety. With an ever-increasing demand for efficiency and reliability in braking systems, understanding these innovations is crucial not just for professionals in the automotive industry but also for consumers who expect durability and effectiveness in their vehicles. This section will explore specific advancements such as electronic brake control systems and adaptive braking technologies, shedding light on their significance and implications.
Electronic Brake Control Systems
Electronic brake control systems represent a leap forward in both safety and functionality in automotive braking. By integrating electronic monitoring and control of braking actions, these systems enhance responsiveness and precision. In layman's terms, instead of relying solely on hydraulic pressure, these systems utilize electronic signals to control brake force. This effectively allows for a more nuanced response during different driving conditions.
- Improved Safety: One of the main benefits of electronic brake control systems is the reduction in stopping distance. With real-time data processing, these systems can adjust brake pressure more rapidly than traditional ones.
- Enhanced Vehicle Stability: These systems often work in conjunction with other vehicle dynamics systems to maintain stability. For example, during hard braking, they can modulate braking force to prevent skidding.
- Diagnostic Capabilities: The electronic nature of these systems facilitates better monitoring of brake performance. This can alert drivers to potential issues before they result in failure, fostering proactive maintenance.
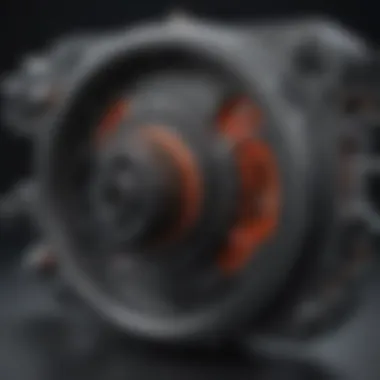
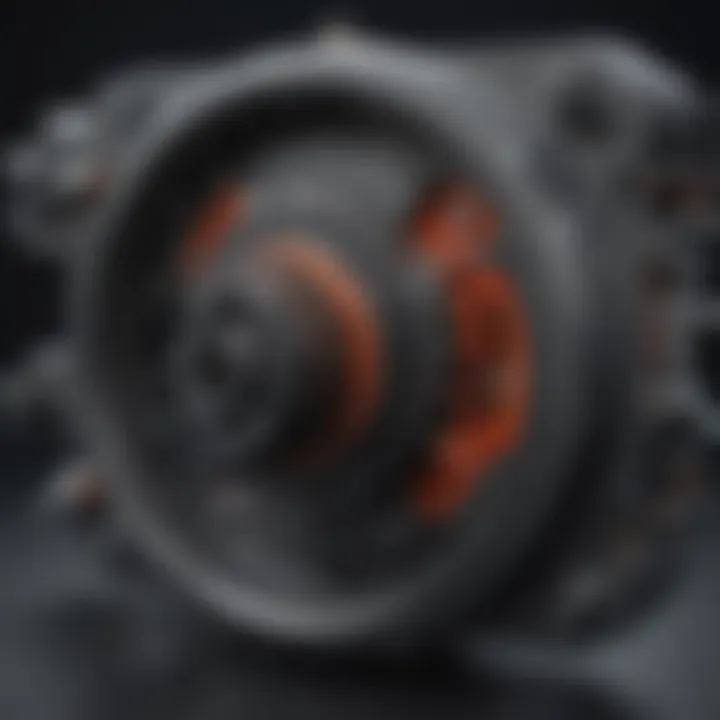
The implications of these systems are profound. With the increasing incorporation of automation in vehicles, understanding and utilizing electronic brake controls is not just advantageous but essential.
Adaptive Braking Technologies
Adaptive braking technologies introduce an innovative layer to traditional braking systems. Essentially, these systems learn from both the driverβs behavior and the driving environment. What sets them apart is their capacity to adapt the braking response based on various factors, making them not just reactive but proactive as well.
- Behavioral Learning: The system can adjust to a driverβs unique braking style. For example, for a driver who often accelerates and brakes hard, the system can provide smoother braking transitions, promoting comfort and safety.
- Environmental Interaction: These technologies take into account factors like road conditions, weather, and load conditions. If the road is slick from rain, the system may increase the brake force gradually to avoid sudden stops that could cause skidding.
- Integration with Navigation Systems: Many newer adaptive braking systems can communicate with vehicle navigation to predict when a stop will be necessary, adjusting brake settings in advance, which can lead to even smoother stops and starts.
"Adaptive braking technologies showcase how far we've come in thinking beyond the basics of vehicle dynamics. It's about enhancing the connection between the driver and the road."
In summary, advancements in brake technology are not just about improving existing systems; they redefine how vehicles interact with their environment and respond to driver input. As the automotive landscape continues to change, remaining apprised of these trends will be vital for anyone involved in brake manufacturing and vehicle design, ensuring they remain at the forefront of innovation.
Environmental Impact of Brake Manufacturing
The environmental implications of brake manufacturing are increasingly gaining attention as the automotive industry continues its journey toward sustainability. There's a fine line that manufacturers must navigate between producing effective braking systems and minimizing their ecological footprint. This balance not only echoes global environmental concerns but also aligns with the growing consumer demand for greener alternatives. In this section, we delve into specific areas such as sustainable materials in brake production and recycling and waste management practices that can mitigate negative impacts.
Sustainable Materials in Brake Production
When it comes to sustainability, materials are at the heart of every manufacturing process, including that of brake systems. For decades, traditional materials like asbestos were common; however, due to health and environmental risks, alternatives are now favored. Manufacturers are continuously focused on sourcing sustainable materials that can withstand wear and tear while being less harmful to our planet.
Some innovative materials include:
- Eco-friendly composites: These materials not only deliver performance but also significantly reduce emissions during production.
- Biodegradable friction materials: Unlike conventional options, these are designed to break down naturally in landfills, which is a huge leap forward for waste management.
- Recycled metals and plastics: Utilizing repurposed materials not only conserves resources but also minimizes the energy required for production.
By shifting to these sustainable materials, manufacturers can decrease their carbon footprint, leading to a more sustainable approach to brake systems.
Recycling and Waste Management
Effective recycling and waste management are crucial in addressing the environmental challenges posed by brake manufacturing. From the outset of production to the end-of-life of the brake systems, careful management of resources can significantly reduce waste.
Primary strategies include:
- Collecting scrap materials: As production facilities generate waste, integrating systems for collecting scrap can promote recycling. This prevents valuable materials from simply being tossed aside.
- Closed-loop recycling systems: Some manufacturers are investing in technologies that allow the reuse of old brake components. For instance, metal scraps can be melted down and reformed into new brake parts.
- Education on proper disposal: Getting the word out about safe disposal methods contributes to overall community responsibility, encouraging consumers to recycle old brake systems rather than merely discarding them.
"The rise of awareness regarding environmental sustainability is pushing manufacturers to rethink their processes and consider their ecological impact."
Future Trends in Brake Manufacturing
The world of brake manufacturing is on the verge of significant transformation. Understanding these trends not only informs manufacturers and engineers but provides crucial insights to researchers and academic circles as the automotive industry evolves rapidly. The future of brake systems is deeply intertwined with advancements in technology, regulatory changes, and shifting consumer expectations. In this section, we'll explore two important trends: the emergence of autonomous vehicle braking systems and innovations designed for electric and hybrid vehicles.
Trends in Autonomous Vehicle Braking
As cars increasingly navigate independently, the braking systems must adapt to meet the demands of autonomous driving. Fully automated vehicles rely on sophisticated sensors to monitor their environment in real-time, enabling them to react to road conditions, obstacles, and other vehicles.
- Enhanced Sensor Integration: Autonomous vehicles will use advanced LIDAR, radar, and camera systems to assess their surroundings. This means brake systems will not only engage based on driver inputs but also automatically adjust to feedback from these sensors.
- Predictive Braking Technologies: In these modern braking systems, algorithms will predict the necessary stopping distance based on the speed and trajectory of the vehicle. This predictive capability will enhance safety, enabling smoother braking experiences and reducing wear on components.
- Data-Driven Improvement: Data collected from various braking actions will inform engineers, allowing them to fine-tune system performance over time. This endless improvement cycle can fundamentally change how manufacturers approach design.
"The next generation of braking systems is not just about stopping β itβs about intelligent responses and seamless integration with other autonomous systems."
Innovations in Electric and Hybrid Vehicles
As more consumers shift towards electric and hybrid cars, the demands on brake manufacturing will inevitably change. Electric and hybrid vehicles inherently offer distinct characteristics compared to traditional combustion engines, affecting the design and function of braking systems.
- Regenerative Braking: One of the most significant innovations is the regenerative braking system. This technology captures kinetic energy during braking, converting it into electrical energy to recharge the battery. In this context, brake design must balance effective stopping power with energy efficiency.
- Adaptive Friction Materials: Newer brake pads being developed for electric vehicles are meant to create less dust and noise during operation. This is particularly crucial for maintaining the low noise profile that many electric vehicle owners desire, leading manufacturers to research and develop new materials.
- Smart Features: Innovations like automatically adjusting brake pressure based on battery status and terrain conditions are being explored. This adaptive braking approach can optimize performance while ensuring safety.
End
The conclusion wraps up the extensive exploration of brake manufacturing, presenting the significance of understanding this field for various stakeholders. Recognizing the evolution and current trends in brake technology not only highlights its relevance in safety but also unveils the layers of complexity involved in developing reliable brake systems.
When discussing brake technology, it's imperative to consider the ongoing advancements in materials and production techniques, which play a central role in enhancing braking performance. The integration of electronic control systems, for example, has revolutionized vehicle safety measures, making it crucial to stay updated with such innovations.
Summary of Key Points
- Evolution of braking systems from rudimentary designs to modern electronically controlled systems shows significant technical progress.
- Key components, such as brake pads, rotors, and hydraulic systems, are integral to performance and safety.
- Emphasis on quality control ensures that manufactured brakes meet stringent safety regulations, reducing the risks of failure.
- Incorporation of sustainable practices in material sourcing and waste management reflects the industry's commitment to reducing environmental impact.
- Future trends highlight the importance of adapting to changing vehicle technologies, especially with the rise of electric and hybrid cars.
Implications for the Future of Brake Manufacturing
The future will likely demand an even greater focus on sustainable materials and processes in brake manufacturing. As car manufacturers pivot towards electric and autonomous vehicles, the design of brake systems will need to evolve accordingly. For instance, adaptive braking technologies will become essential to match the sophisticated interfaces of self-driving cars.
Moreover, the integration of advanced data systems in vehicles presents opportunities for real-time monitoring, predictive maintenance, and improved safety features.
Adapting to these trends not only ensures compliance with international regulations but also aligns with consumers' increasing expectations for eco-friendly and efficient products. Staying ahead of the curve in brake technology will be a pivotal aspect for manufacturers aiming to maintain market relevance in the years to come.
"The key to future innovation in brake manufacturing lies in understanding and adapting to technological trends that prioritize safety without compromising performance."
In summary, the exploration of brake manufacturing encapsulates fundamental aspects that are pivotal for researchers, manufacturers, and enthusiasts alike, urging a proactive approach to advancements in this essential automotive sector.