Effective Adhesive Strategies for Nylon and Metal
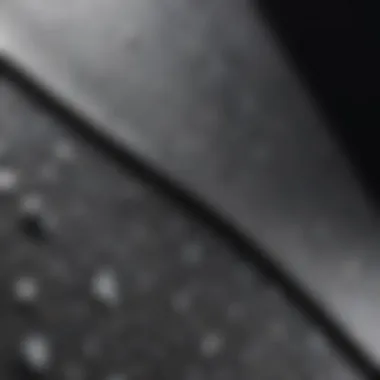
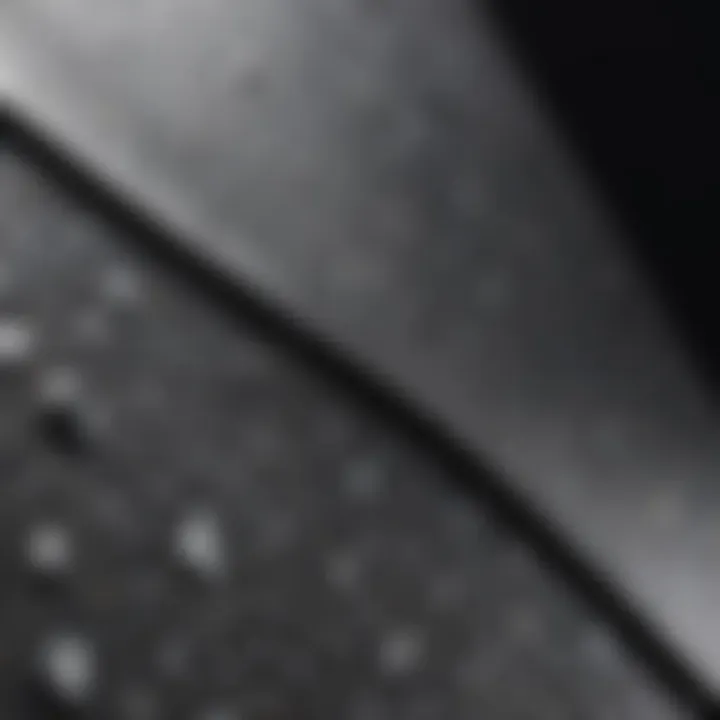
Intro
Bonding nylon to metal can present quite the puzzle, especially when considering the unique properties of both materials. Nylon, a versatile and durable synthetic polymer, possesses a low coefficient of friction, excellent wear resistance, and high tensile strength. On the other hand, metal offers solidity and structural integrity, making it indispensable in many industrial and DIY applications. When these two elements come together, the challenge is not only to achieve a strong bond but to ensure the bond can withstand various stresses over time.
Understanding how to effectively join these materials is crucial across a multitude of fields, including automotive, aerospace, and the manufacturing industry. When done right, the bond can result in enhanced performance, longevity, and adaptability of products. Yet, the intricacies involved in creating a reliable adhesive joint between nylon and metal cannot be overstated.
This article will cover essential topics, such as the types of adhesives suitable for this specific bonding task, the necessary surface preparation techniques, and practical applications. Further, we'll discuss performance considerations and environmental factors that could affect adhesive effectiveness. By the end of our exploration, readers should have a solid grasp of how to achieve strong and lasting connections between nylon and metal, whether in professional settings or personal projects.
Understanding Nylon and Metal Bonding
Nylon and metal are often found in various applications across industries, given their diverse properties and capabilities. Bonding these two materials can open a treasure trove of possibilities, from automotive parts to consumer products. Understanding the nuances of this bonding process is crucial, as it ensures that engineers and makers alike achieve durable and effective connections.
Nylon, a synthetic polymer, is valued for its tensile strength, flexibility, and resistance to wear and tear. On the flipside, metals, be it aluminum, steel, or brass, bring forth a whole different array of strengths, durability, and aesthetic appeal. When you start the process of bonding these materials, it’s not just a matter of slapping some glue on and calling it a day. There’s a careful choreography at play, involving material compatibility, surface preparation, and adhesive choice.
The Relevance of Bonding Nylon to Metal
- Mechanical Strength: The bond needs to withstand physical forces; hence understanding properties helps in selecting the right adhesive.
- Chemical Resistance: Different adhesives offer varying resistance to chemicals, which is crucial depending on the environment the bond will encounter.
- Thermal Properties: Both nylon and metal have unique responses to heat; thus, understanding these properties is crucial in preventing bond failure at elevated temperatures.
In our journey through this article, we’ll break down the specific characteristics of nylon and metals, dive into the adhesive options available, and explore the challenges faced in this dual-material bonding. By getting down to the nitty-gritty, we aim to equip professionals with nuanced insights and hands-on techniques to navigate this complicated terrain effectively.
Material Properties of Nylon
Nylon is a versatile material that has captured the interests of many within the engineering and crafting communities. It boasts a high level of flexibility, making it an ideal choice for applications requiring repeated bending or movement. This polymer is also known for its chemical resistance, which means it's less likely to deteriorate when exposed to certain substances. When bonding nylon, one must consider the surface energy of the material; nylon typically has a lower surface energy compared to metals, meaning that proper adhesion could require specific treatments to enhance the bond.
Characteristics of Metals
Metals offer their own set of benefits. High tensile strength, rigidity, and resistance to environmental factors like rust (in the case of stainless steel) are just a few of their characteristics. However, they also introduce challenges such as potential corrosion, especially when in contact with nylon over time. Metal surfaces can often be smooth and non-porous, which can hinder the adhesion process if not treated adequately. The choice of metal can greatly affect the choice of adhesive and the overall bonding strategy.
Challenges in Bonding Nylon to Metal
Bonding nylon to metal isn't without its hurdles. One significant challenge arises from the significant difference in their thermal expansion coefficients, with metals typically expanding or contracting more than nylon when subjected to temperature changes. This can lead to mechanical stress at the bond point and may jeopardize durability. Additionally, the natural oils, plasticizers, or coatings that frequently exist on metal surfaces can further complicate the bonding process. Adequate surface preparation, including cleaning and possibly roughening the surface, becomes paramount to ensure a successful adhesion process.
"Understanding the properties of both nylon and metal, as well as the challenges inherent in bonding them, is essential for developing effective adhesive solutions that withstand the test of time."
In summary, a thorough grasp of the specifics surrounding nylon and metal bonding is vital for achieving desired results in various applications. As we move further along this guide, we’ll delve deeper into adhesive types tailored for such bonding, ensuring that the insights shared will pave the way for successful projects.
Types of Adhesives
In the world of bonding nylon to metal, selecting the right adhesive is not just a technical choice; it's a strategic decision that can greatly influence the durability and performance of the bond. Given the varied nature of both nylon and different metals, understanding the specific characteristics of each adhesive type becomes paramount. This section will examine the most effective adhesive types for this intricate task, each possessing unique benefits and considerations that make them suitable for specific applications.
Epoxy Resins
Epoxy resins are among the most versatile adhesives available. They consist of two components – a resin and a hardener – that, when mixed, undergo a chemical reaction resulting in a solid, durable bond. The strength of epoxy resins lies in their ability to fill gaps and adhere to a wide variety of surfaces, including the distinct textures of nylon and metal.
- Benefits:
- High shear strength: Once cured, epoxy forms a bond that is resistant to shear forces, making it ideal for structural applications.
- Heat resistant: Many epoxy formulations can withstand elevated temperatures, a significant factor in environments where heat is a concern.
- Versatility: They can be formulated to suit myriad applications, with variations available for flexibility or rigidity.
However, applying epoxy does require careful attention to the mixing ratios and timing in application to ensure optimal results. Keep in mind that while epoxy can offer outstanding performance, the curing time may be longer compared to other adhesives.
Polyurethane Adhesives
Polyurethane adhesives are celebrated for their exceptional flexibility and ability to bond dissimilar materials, making them a popular choice for bonding nylon to metal. They are moisture-curing adhesives that provide strong bonds and can accommodate thermal expansions, which is often beneficial in applications subjected to varying temperatures.
- Key Features:
- Strong and flexible bond: Ideal for applications requiring shock resistance or flexing, like in automotive or aerospace industries.
- Good adhesion: They perform well on both porous and non-porous substrates, which means they can effectively bond nylon and metal surfaces.
Their downside may include sensitivity to environmental conditions during the curing process, as excessive moisture can sometimes alter the adhesion properties. Therefore, it’s advised to monitor the climate in which you’re working.
Acrylic Adhesives
Acrylic adhesives appear as an optimum solution for applications needing rapid bonding and performance. They can bond unlike materials together such as nylon and metal with impressive results. Their curing mechanisms allow them to set quickly, making them excellent for production environments where time is of the essence.
- Advantages:
- Fast curing: Many acrylics can bond in just a few minutes, allowing for speedy assembly processes.
- Versatility: They can be found in various formulations, some designed for specific conditions such as low temperature or extreme pH levels.
One should note, however, that while acrylic adhesives are quick to set, their long-term durability in high-shear applications may not quite match that of epoxies.
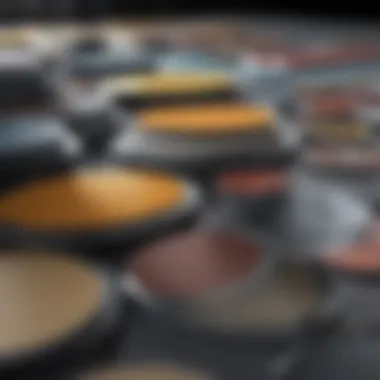
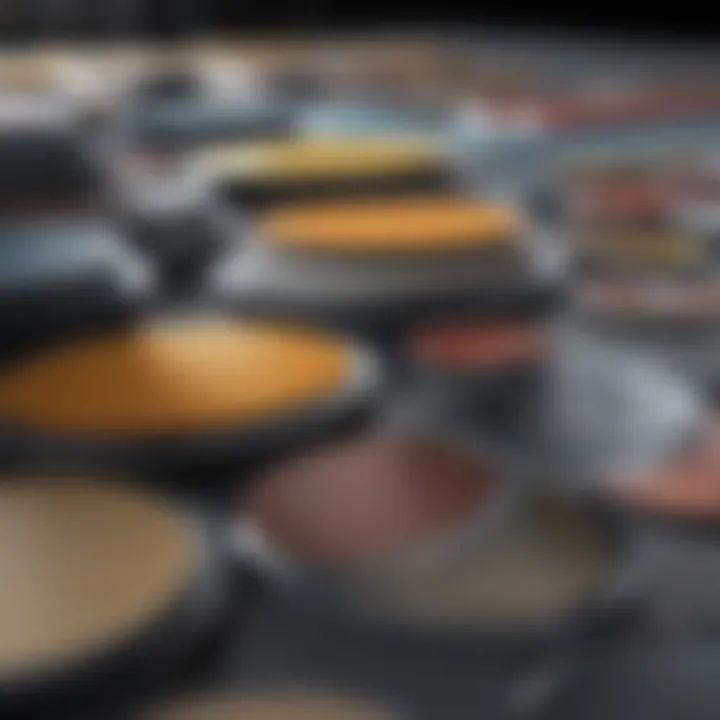
Cyanoacrylate Adhesives
Commonly referred to as superglue, cyanoacrylate adhesives are very fast-setting adhesives that are excellent for bonding nylon to metal in small-scale applications. They work best when the surfaces are clean and tightly fitting, allowing for quick polymerization of the cyanoacrylate.
- Noteworthy Characteristics:
- Ultra quick bonding: They set almost instantaneously, making them perfect for quick repairs or assembly tasks.
- Transparency: Upon curing, they are generally clear, allowing for aesthetic appeal in visible applications.
Despite their immediacy, cyanoacrylates can be somewhat fragile in terms of resistance to impact or environmental factors. They also tend to be less effective for porous materials or large surface areas.
In summary, the choice of adhesive between epoxy, polyurethane, acrylic, and cyanoacrylate should be dictated by the specific requirements of the project, including the materials' properties and the operating conditions. Evaluating each option's advantages helps ensure a successful bonding process.
Surface Preparation Techniques
Surface preparation is a crucial step when bonding nylon to metal. The integrity and durability of the adhesive bond significantly depend on how well the surfaces are prepared before applying the adhesive. Ignoring this phase can lead to weak joints, which may fail under stress or environmental challenges. A well-prepared surface ensures that the adhesive can form a strong, lasting bond. The main benefits of thorough surface preparation include improved adhesive penetration, enhanced bonding strength, and reduced likelihood of contamination affecting the bond performance.
Cleaning the Surfaces
Cleaning the surfaces thoroughly is the first and foremost step in surface preparation. Dust, grease, oil, or any contaminants can significantly hinder the adhesive's ability to stick effectively. When dealing with nylon and metal, it is often recommended to use specific cleaning agents to ensure all residues are removed. Acetone or isopropyl alcohol usually works great for metal, while nylon might respond well to soap and water or specialized nylon-safe cleaners.
Here are some important cleaning tips:
- Use lint-free cloths: This prevents fibers from getting stuck on the surfaces.
- Rinse and dry: After using cleaning agents, make sure to rinse and dry effectively to avoid leaving any residues.
Physical Treatment Methods
In this phase, physical treatment methods can be utilized to improve adhesion between nylon and metal. These methods alter the surface characteristics, promoting a stronger adhesive bond. Mechanical abrasion, such as sanding or scouring, is one example that increases the surface area and introduces micromechanical interlocking.
Some physical treatment techniques include:
- Sandblasting: This processes creates a rough texture on the metal surface, facilitating better adhesion.
- Plasma treatment: A more advanced option, plasma treatment alters the surface properties at the molecular level, enhancing bonding capabilities. It can effectively increase the surface energy of nylon, allowing for better adhesive infiltration.
Chemical Treatments for Enhanced Bonding
Chemical treatments serve to alter the surface of both nylon and metal to create a more conducive environment for adhesive bonding. This can involve the application of primers or special coatings that enhance the adhesive's effectiveness. For metal surfaces, using an acid or treating agents like phosphoric acid can clean the surface and improve corrosion resistance, in addition to boosting adhesion.
On the nylon side, applying a chemical bonding agent or a surface modifier can enhance the interfacial adhesion properties. These treatments may include:
- Silane coupling agents: These can provide a bond between organic and inorganic materials remarkably well.
- Primers specifically designed for nylon: These can significantly improve adhesion and are worth considering in various applications.
Effective surface preparation enhances the longevity and reliability of adhesive bonds. Skipping this step can be akin to building a house on sand—flimsy and compromised from the start.
By paying attention to surface preparation techniques, one can create a robust bond between nylon and metal that withstands both mechanical and environmental challenges.
Application Techniques
Understanding how to effectively apply adhesive is crucial to achieving strong bonds between nylon and metal. Application techniques not only dictate the integrity and durability of the bond but also impact the efficiency of the entire bonding process. These techniques encompass the methods of adhesive application, curing processes, and the importance of providing adequate support during curing. By mastering these techniques, professionals can ensure that they maximize the adhesive's potential, creating robust and long-lasting connections.
Adhesive Application Methods
When it comes to bonding nylon to metal, there are various adhesive application methods that can be adopted. Each method has its benefits, and the choice often hinges on the specific requirements of the task. Here are some common methods:
- Brush Application: Suitable for controlled application, this method allows precise placement of adhesive, ideal for fine or intricate work.
- Roller Application: Used for larger surfaces, rollers help in achieving an even adhesive layer, ensuring good coverage and preventing air bubbles.
- Spray Application: For rapidly bonding large areas, spraying is efficient, although it requires specialized equipment and proper ventilation.
- Extrusion: A method often used for liquid adhesives where controlled beads of adhesive can be applied, ensuring an even spread with minimal waste.
The choice largely depends on the project scale and the type of bond required. Each method offers unique advantages that, if chosen wisely, can enhance the bond strength considerably.
Curing Processes
Curing is the process where the adhesive transitions from its liquid state to a solid, permanent bond. This stage is vital and can vary depending on the adhesive type used. The curing process may take place via chemical reaction, evaporation of solvents, or exposure to heat or light.
- Heat curing: This process activates the adhesive's curing agents through heat, speeding up the bond formation, which is beneficial for industrial applications.
- Room temperature curing: Many adhesives are designed to cure at ambient temperatures, providing convenience for day-to-day tasks.
- UV curing: Certain adhesives require ultraviolet light to initiate curing, often utilized in specialized applications like electronics or optical devices.
It's essential to adhere to the manufacturer's guidelines for curing times, as improper curing can lead to weak bonds, ultimately compromising the structure.
Clamping and Support During Curing
The role of clamping and support throughout the curing phase cannot be overstated. Proper alignment and pressure are key to forming a strong bond. Here’s what to consider:
- Alignment: Ensure that the nylon and metal surfaces are aligned properly before the adhesive sets. Misalignment can lead to uneven pressure and hence a weak bond.
- Clamping: Use clamps or weights to maintain pressure as the adhesive cures. This helps in ensuring that the surfaces remain in contact.
- Support: Depending on the size and configuration of the bonded materials, additional support might be needed to prevent sagging or shifting during the cure period.
By carrying out these steps, the chances of producing a reliable bond increase significantly, making it fundamental for any application involving nylon and metal adhesives.
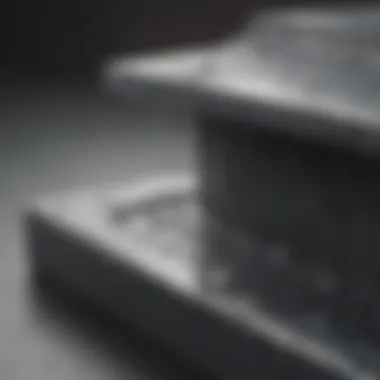
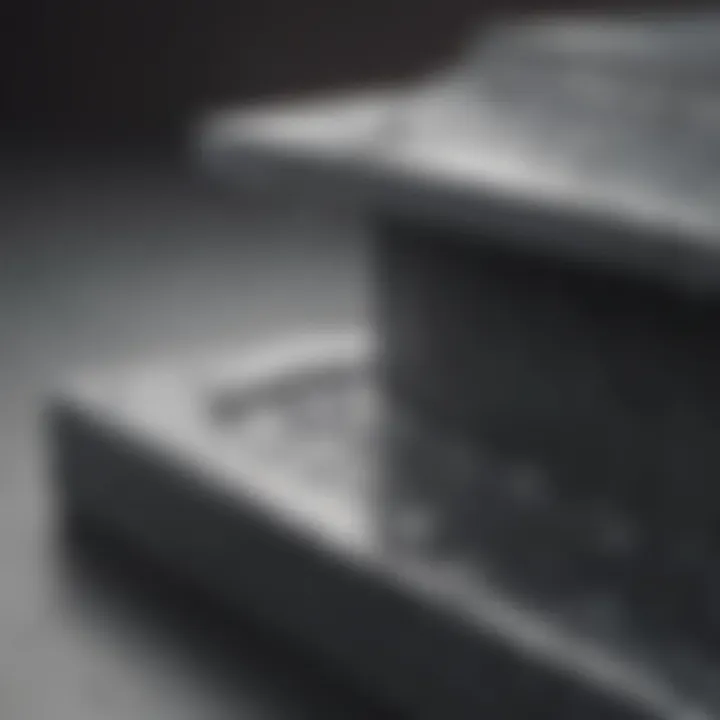
Effective adhesive application techniques are the backbone of successful bonding. Ignoring these details can lead to disaster, whereas attention to them can yield superior results.
Performance Considerations
When it comes to bonding nylon to metal, performance considerations play a pivotal role in ensuring the longevity and effectiveness of the adhesive solutions employed. This section dives into various elements that can significantly influence the success of the bonding process. It is crucial to evaluate aspects like temperature resistance, chemical resistance, and the mechanical properties of the bond. By understanding these factors, professionals can make informed decisions that enhance the durability of the bond, leading to improved outcomes across various applications.
Temperature Resistance
Temperature fluctuations can pose a serious challenge for bonded surfaces. Depending on the application, the materials may be subject to varying temperatures, from the sweltering heat of industrial environments to the chill of outdoor usage. Nylon, for instance, has a glass transition temperature around 50°C, which can affect its structural integrity and adhesion when subjected to high heat.
- High-Temperature Considerations: If the bonded nylon and metal will face elevated temperatures, selecting an adhesive that can withstand such conditions is paramount. Epoxy resins are often ideal due to their superior heat resistance.
- Low-Temperature Considerations: Similarly, when dealing with colder climates, ensure that the adhesive maintains its bonding strength. Many adhesives exhibit brittle behavior at low temperatures, which could lead to failure of the bond.
Overall, considering temperature resistance allows manufacturers and hobbyists alike to preemptively address potential bond degradation, ensuring reliability under real-world conditions.
Chemical Resistance
Adhesives can encounter hostile environments that introduce various chemicals, oils, or solvents. For instance, applications in automotive or industrial settings often expose bonded nylon and metals to oils or cleaning agents. Choosing the right adhesive with robust chemical resistance can increase the longevity of the bond and, ultimately, the product itself.
- Adhesive Types: Some adhesives, like polyurethanes and certain epoxies, exhibit strong resistance to chemicals, making them suitable for environments prone to spills or leaks.
- Testing for Compatibility: It’s also wise to conduct compatibility tests with the specific chemicals involved to evaluate how the adhesive will respond over time. Inadequate chemical resistance can lead to adhesive degradation, resulting in bond failure.
Understanding chemical resistance can therefore provide a clear insight into how different adhesives will perform in varied environments, giving a leg up on potential issues before they arise.
Mechanical Properties of the Bond
The strength of the bond is not only about the adhesive, but also how it interacts with nylon and metal at a mechanical level. Parameters such as tensile strength, shear strength, and elasticity are fundamental here. A robust adhesive must not only bond the two materials but also accommodate the operational stresses they may endure.
- Tensile Strength: Adequately bonding materials must withstand pulling forces; thus, knowing the tensile strength of an adhesive helps gauge its suitability for high-stress applications.
- Shear Strength: This aspect pertains to how well the adhesive holds under lateral forces. If not considered, it could lead to a failure of the bond when subjected to stresses, whether from movement or operational activity.
- Elasticity: A degree of flexibility in the adhesive can aid in absorbing shock and accommodating minor expansions or contractions of the materials, preventing cracks over time.
Choosing an adhesive that manifests high mechanical properties ensures the bond remains intact under operational pressures, creating stronger, more reliable assemblies.
"It’s not always about the adhesive itself but how well it works with the materials and conditions at hand that determines success."
Understanding these performance considerations provides a solid foundation for making informed choices in adhesive applications. It emphasizes that careful evaluation can yield the desired durability and reliability when bonding nylon to metal.
Environmental Factors
The interaction between adhesive solutions and their surroundings is crucial for ensuring the long-lasting performance of nylon-to-metal bonds. Environmental factors can profoundly influence the adhesive's effectiveness, affecting how it performs under various conditions. Understanding these dynamics helps in selecting the right adhesive and applications for specific uses.
Humidity Effects
Humidity often has a sneaky way of affecting the bond between nylon and metal. When the air is moist, it can create an environment that promotes the absorption of water into the nylon material. This absorbed moisture can weaken the bond by introducing a layer of water between the adhesive and the surfaces being bonded.
In applications where exposure to varying humidity levels is common, more than just consideration for the adhesive's initial bonding strength is vital. It becomes necessary to evaluate the adhesive's durability and performance in such environments. For instance, adhesives with water-resistant properties, such as epoxy resins, tend to perform better. However, a pre-treatment like drying out the surfaces before bonding might be beneficial in some cases.
UV Exposure Considerations
Another environmental factor to consider is UV exposure. In many applications, especially outdoor ones, the adhesive bond can be directly exposed to sunlight. UV radiation can degrade certain adhesives over time, leading to a breakdown in the molecular structure. For adhesives used in areas where sunlight is relentless, it is crucial to choose products that can withstand UV radiation without losing integrity.
Adhesives like polyurethane are known for their resilience against UV light. Additionally, incorporating a topcoat or protective layer can offer an extra shield against potential UV damage, significantly extending the bond’s life in outdoor applications. As the saying goes, "an ounce of prevention is worth a pound of cure."
Impact of Temperature Variations
Temperature plays a significant role too. Extreme heat or cold can alter the physical properties of both the adhesive and the materials being bonded. High temperatures may cause some adhesives to soften or become too fluid, risking bond failure, while extreme cold can lead to brittleness in the adhesive.
For instance, an adhesive like cyanoacrylate might cure too quickly in high temperatures, while acrylic-based adhesives may have enhanced properties for thermal variation. Knowing these characteristics can guide choices based on expected temperature conditions.
"Selecting an adhesive is equal parts science and art; understanding the environment shapes that choice uniquely."
Given the diverse applications of nylon and metal bonding, it’s crucial to assess not only the adhesive's strength but also its resilience to the environmental factors at play. A careful evaluation ensures that the chosen adhesive will perform effectively, even when faced with nature’s challenges.
Testing and Quality Assurance
When it comes to bonding nylon to metal, the significance of testing and quality assurance cannot be overstated. This process serves as the backbone that supports the reliability and functionality of the adhesive bond. Testing helps to ensure that the bond meets the specific requirements set by the end use, while quality assurance provides the necessary checks to maintain consistency throughout the production process.
Proper testing addresses critical aspects such as bond strength, environmental resistance, and overall durability under different conditions. Every application might demand something different; hence, knowing how well an adhesive holds up can make or break a project's success. On the flip side, quality assurance processes incorporate standardization to monitor the properties of adhesives, confirming they perform as expected day in and day out.
In addition to performance benefits, adequate testing can offer peace of mind. Stakeholders can have confidence in their products, knowing they comply with industry standards and will withstand the rigors of real-world applications. It minimizes the risk of failures that could lead to safety hazards and costly setbacks.
"Quality isn’t just about meeting a deadline; it’s about ensuring the results last in the long run."
Adhesive Bond Testing Methods
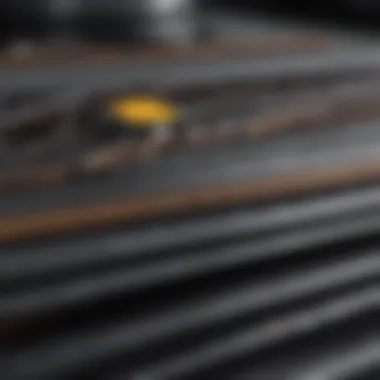
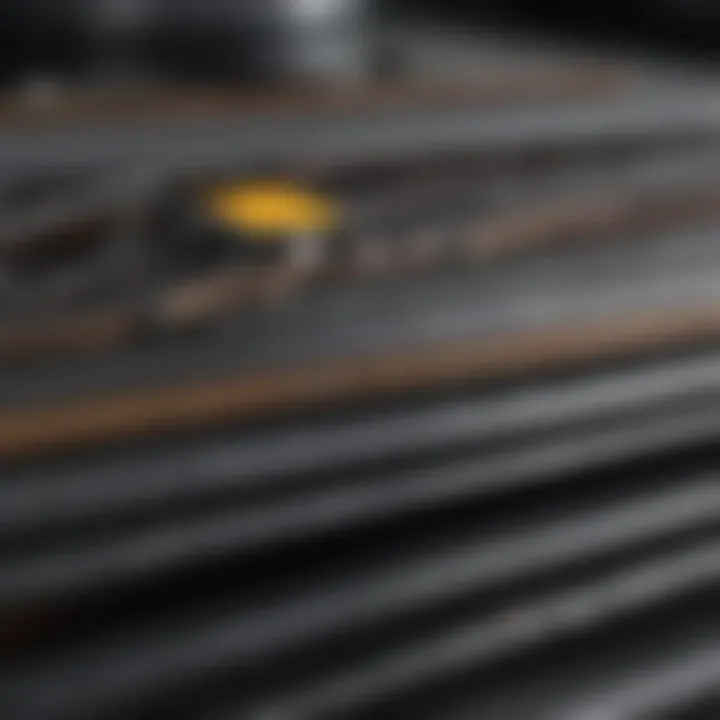
Evaluating the strength and reliability of adhesive bonds involves several testing methods. Each serves its purpose, providing vital information on how the bond will perform under various conditions. Some widely accepted adhesive bond testing methods include:
- Tensile Testing: This method measures the force required to pull two bonded pieces apart. It helps determine how much load the bond can withstand before failing.
- Peel Testing: This test examines the resistance to forces applied perpendicular to the bond line. It's particularly useful in gauging the performance of the adhesive when exposed to shear forces.
- Shear Testing: Unlike peel testing, shear testing assesses the load capacity of the adhesive when applied parallel to the bonded surfaces. It's crucial for understanding how the bond will behave under actual use conditions.
- Environmental Testing: Conducting tests in simulated environments—like high humidity or extreme temperatures—can provide insights into how external factors influence the bonded materials.
By utilizing these methods, manufacturers can evaluate whether their adhesive choices meet the specific demands of their applications, allowing adjustments before final production.
Standards and Compliance
Meeting industry standards and compliance requirements plays a significant role in ensuring adhesive performance in bonding nylon to metal. Adhering to established benchmarks creates a structured approach to evaluating an adhesive’s effectiveness and reliability. Different organizations often set these standards based on the intended use of the bonded materials.
For instance:
- ISO Standards: The International Organization for Standardization provides a comprehensive set of guidelines covering numerous aspects including testing methods and material properties.
- ASTM Standards: The American Society for Testing and Materials publishes standards that detail various tests for adhesive performance, ensuring consistent and reliable results across the industry.
Becoming compliant with these standards fosters greater trust among manufacturers, clients, and consumers. It signals a commitment to quality, performance, and safety, setting products apart in a competitive market.
Selected Case Studies
Understanding selected case studies in the bonding of nylon to metal offers a practical aspect of adhesive solutions. The real-world applicability of various bonding techniques helps us to reflect on the effectiveness and challenges faced across different environments. Not only do these examples illustrate successful strategies but they also shed light on common issues encountered and how they were resolved. This section will hone in on two main categories: industrial applications and consumer product use cases.
Industrial Applications
In industrial settings, the need for durable and reliable adhesion between nylon and metals is paramount. Industries such as automotive, aerospace, and electronics heavily rely on strong, resilient bonds for both performance and safety. Adhesives like epoxy resins are often employed due to their high strength and resistance to harsh conditions.
Example 1: Automotive Industry
In recent years, an automotive manufacturer faced significant challenges when attempting to bond nylon components to metal frames of their vehicles. The design called for lightweight materials that could withstand rigorous operational demands, such as high temperatures and constant vibrations. By opting for polyurethane adhesives, the company realized a successful combination that not only met their weight-saving targets but also exhibited excellent flexibility and shock absorption. This allowed for a longer lifespan of parts, ultimately leading to improved vehicle performance and lower maintenance costs.
Example 2: Aerospace Engineering
Another notable case comes from the aerospace sector, where an aircraft manufacturer needed to affix lightweight nylon components to aluminum structures. Given the strict regulations about safety and reliability, they turned to a specialized cyanoacrylate adhesive known for its fast curing time and exceptional weather resistance. The application required meticulous surface preparation to ensure adhesion integrity. This choice resulted in substantial weight reductions in their aircraft models, driving fuel efficiency without sacrificing safety or performance.
Consumer Products Use Cases
The consumer market also presents unique situations where bonding nylon to metal can make or break product functionality. From gear mechanisms in appliances to sports equipment, the applications are wide-ranging.
Example 1: Kitchen Appliances
Take, for instance, a prominent kitchen appliance brand that developed a line of food processors. The design integrated nylon parts into the metal framework, but earlier attempts at bonding resulted in frequent malfunctions. By analyzing their initial approaches, the engineers shifted to using acrylic adhesives. These adhesives not only provided faster setting times but also ensured resistance against temperature fluctuations inherent in kitchen environments. As a result, the redesigned products saw a marked improvement in durability and consumer satisfaction.
Example 2: Outdoor Gear
In the realm of outdoor sporting goods, a brand that manufactured camping gear faced issues with nylon straps detaching from metal buckles. The solution lay in implementing chemical treatments to the surfaces before adhesive application. The study underscored the importance of preparation methods. By applying this knowledge, they were able to create a more robust connection that withstood rigorous outdoor activities, enhancing customer trust and brand reputation.
“The right adhesive can often be the difference between a product’s success and failure.”
Future Trends in Adhesive Technology
The adhesive industry is on the cusp of significant developments. As sectors evolve, so do the materials and methods used to bond substances like nylon to metal. This section sheds light on the upcoming trends in adhesive technology, outlining their implications for efficiency and effectiveness in practical applications.
As industries seek faster production cycles and greater reliability, the spotlight shines on innovations that not only enhance bond strength but also cater to the increasing demand for environmentally friendly solutions. This shift towards sustainability, coupled with advanced formulations, makes the topic exceedingly relevant for professionals involved in manufacturing and product design.
Innovations in Adhesive Formulations
Recent advancements in adhesive formulations are groundbreaking. Historically, many adhesive products were limited to certain applications due to their rigid structures or compatibility issues. Today, scientists are focusing on creating adhesives that possess enhanced flexibility and strength.
- Smart adhesives: These are responsive to environmental changes—temperature, humidity, or pressure. They adapt their properties, ensuring a stronger bond under varying conditions.
- Nano-reinforced adhesives: Incorporating nanomaterials, these adhesives significantly enhance mechanical and thermal properties. This means better durability and longevity when bonding nylon to metal.
- Hybrid adhesives: Combining the best attributes of various adhesive types can lead to formulations that perform exceptionally well across a range of applications. For example, products that combine aspects of epoxy and polyurethane may offer both strong initial tack and long-term durability.
By focusing on these innovative formulations, we can expect to see adhesives that not only meet but exceed current bonding challenges in industrial, automotive, and consumer product arenas.
Sustainability Considerations
The importance of sustainable practices can't be stressed enough in today's world. The adhesive industry is gradually moving towards greener technologies as regulations tighten and consumer demand shifts.
Key considerations include:
- Biodegradable adhesives: Development in this area is crucial, as traditional adhesives can create long-lasting waste. Bio-based adhesives derived from renewable resources are gaining traction.
- Low-VOC adhesives: Minimizing volatile organic compounds in adhesive formulations is essential for improving indoor air quality. New products are increasingly free of harmful chemicals, paving the way for safer applications.
- Recycling-friendly formulations: Innovators are working on adhesives that facilitate easier disassembly of products, enabling better recycling practices. This can help reduce waste in manufacturing and end-of-life processes.
Adopting sustainable adhesive solutions isn't just good for the planet; it can also enhance a brand's reputation and appeal to eco-conscious consumers.
"Innovators in adhesive technologies are paving the way for a lot more than just sticking things together; they are shaping a sustainable future within the manufacturing ecosystem."
In sum, the future trends in adhesive technology are marked by a clear emphasis on innovation and sustainability. For professionals and researchers, keeping an eye on these advancements is essential to remain competitive and responsible in their practices.
The End
A key takeaway is the critical nature of surface preparation. Properly clean and treated surfaces yield much stronger bonds, ensuring longevity and reliability in applications. Without this preparatory step, even the most advanced adhesives could falter, resulting in costly reworks and damaged reputations.
Moreover, each adhesive type has its strengths and weaknesses. Epoxy resins, for instance, offer exceptional strength yet may require longer cure times. On the other hand, cyanoacrylates feature rapid bond formation but might not withstand harsh environments. Thus, the choice of adhesive must align with the specific requirements of the project at hand. Investors in time and resources towards the right adhesive not only save on potential failures but also enhance product performance.
"One adhesive solution does not fit all; understanding the specific bonding needs is vital for success."
Also, one must factor in environmental impacts when bonding nylon to metal. Changes in temperature, humidity, and exposure to UV light can significantly affect the bond strength and durability. Thus, a well-informed selection process must include potential environmental challenges that the final product may face.
Conclusively, this article serves as a detailed guide through the labyrinth of adhesive technology for joining nylon and metal. The insights shared should empower students, educators, professionals, and enthusiasts alike with the knowledge needed to navigate and apply these techniques effectively across diverse applications.