Understanding Rust Proof Steel Coating: Insights and Trends
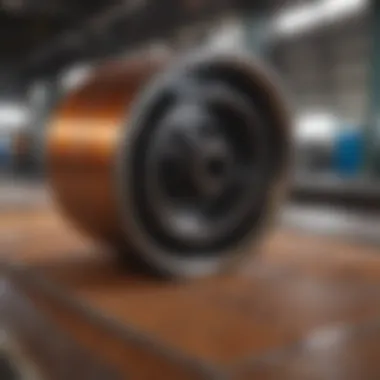
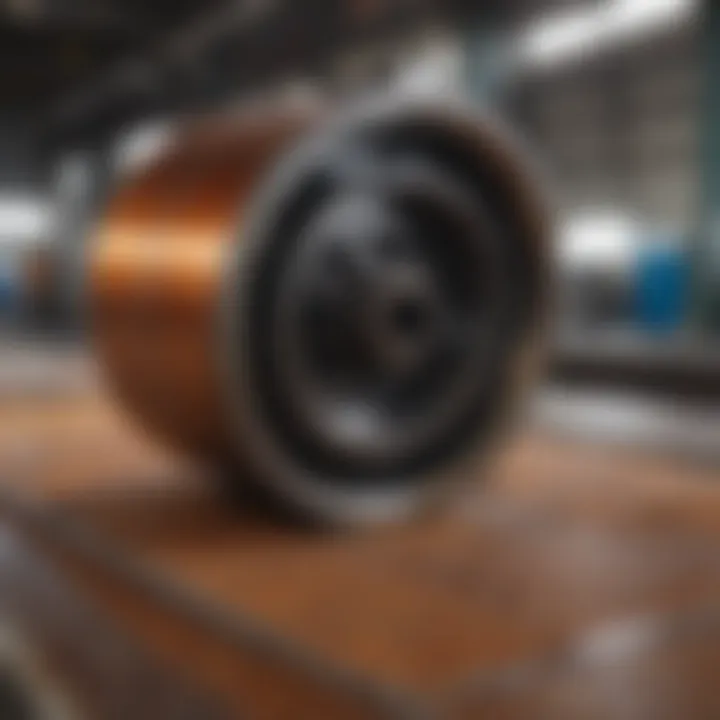
Intro
Rust proof steel coating is a crucial innovation in the realm of materials science and engineering. The presence of rust poses significant challenges to the longevity and functionality of steel. This article seeks to unpack the various dimensions of rust proof steel coating, outlining its importance in different sectors, including construction, automotive, and manufacturing.
The necessity for effective corrosion resistance measures is not merely an industry concern; it transcends into environmental and economic realms. With rising costs associated with maintenance and replacement of corroded steel structures, understanding the intricacies of effective coatings is more important than ever.
Moreover, advancements in technology have paved the way for innovative coatings that not only promise enhanced durability but also prioritize environmental safety. These developments garner attention from researchers, professionals, and students who strive to understand the complexities involved in achieving effective rust proofing.
To provide a compelling narrative, this article will first delve into the research context surrounding rust proof coatings, followed by an in-depth discussion involving interpretations of findings, and future trends in this essential field.
Prelims to Rust Proof Steel Coating
Rust proof steel coating is a critical aspect of materials engineering, especially in industries where metal structures face harsh environments. Effective coatings protect steel from corrosion, prolonging its lifespan significantly and reducing maintenance costs. These coatings not only enhance the durability of steel but also contribute to safety and sustainability in various applications.
Definition and Purpose
Rust proof steel coatings are used to protect steel surfaces from the damaging effects of corrosion. Corrosion is a natural process that deteriorates metals through chemical reactions with environmental elements like moisture and oxygen. The primary purpose of these coatings is to create a barrier between the steel and its surrounding environment.
In most cases, rust proof coatings are applied to surfaces that will experience exposure to aggressive elements. For example, steel used in bridges, buildings, and vehicle components often require special coatings. The choice of coating depends on several factors, including the expected environment and the desired lifespan of the structure.
Historical Context
The history of rust proof coatings can be traced back to ancient civilizations. Ancient Egyptians explored various methods to protect their metal tools and structures, showcasing an early understanding of the need for corrosion resistance. However, the modern development of protective coatings began in the late 19th century with the introduction of zinc galvanizing.
Since then, numerous techniques and materials have emerged. The industrial revolution brought about more advanced materials and application methods. Today, various coatings, including organic and inorganic compounds, are available on the market. Each development aimed at addressing specific challenges posed by different corrosive environments and advancing protective methods in construction and manufacturing.
Understanding the evolution of rust proof coatings can provide valuable insights into current practices and innovations in corrosion protection.
The continued research in this field remains essential as industries push for better performance standards in protective coatings. This foundation sets the stage for exploring the following sections on corrosion mechanisms and the composition of rust proof coatings.
Corrosion Mechanisms
Understanding corrosion is pivotal in grasping the overall efficacy of rust proof steel coatings. Corrosion is a natural process that leads to the deterioration of metal through reactions with its environment. This topic is essential because it informs the selection and application of coatings intended to mitigate this damaging phenomenon. A solid understanding of corrosion mechanisms enables better design solutions and helps in the development of more effective protective technologies.
Understanding Corrosion
Corrosion occurs when metals react with moisture, oxygen, or other chemicals, resulting in the breakdown of the protective layers of steel. The most common form of corrosion is rusting, which specifically affects iron and steel alloys. When exposed to oxygen and water, iron undergoes an electrochemical reaction leading to the formation of iron oxide, commonly known as rust. This process is not only a chemical change but also involves physical alterations in the structure of the metal.
Several factors influence how corrosion manifests. These include the presence of electrolytes, pH levels of the surrounding environment, and temperature. For instance, higher humidity can enhance the electrolytic process, accelerating rust formation. Additionally, the presence of salts or chloride compounds significantly exacerbates corrosion rates, particularly in marine environments. Understanding these elements is critical for developing reliable rust proof coatings and ensuring the longevity of steel structures.
Factors Contributing to Rust Formation
Numerous factors contribute to the formation of rust, and comprehending these can guide the implementation of effective protective measures. Some significant factors include:
- Environmental Conditions: Humidity and temperature directly affect moisture retention on steel surfaces. Higher humidity levels often lead to increased corrosion potential.
- Material Composition: Different steel alloys exhibit varying resistance to corrosion. Products like stainless steel, which contain chromium, tend to show lower rust rates compared to plain carbon steels.
- Surface Condition: The initial condition of the steel surface plays a notable role. Clean, smooth surfaces are generally less prone to rust compared to those that are contaminated or poorly finished.
- Electrochemical Corrosion: This occurs when dissimilar metals are in contact in the presence of an electrolyte, leading to galvanic corrosion.
- Contaminants: Pollutants in the environment, such as industrial emissions or salt from seawater, can accelerate rust formation significantly.
"Understanding the roots of corrosion allows engineers to create more robust solutions that not only protect steel but also prolong its useful life."
By analyzing these factors, professionals can better design rust proof coatings tailored to the specific environmental challenges faced by steel applications. Each aspect of corrosion mechanisms contributes valuable insights into how to combat rust effectively.
Composition of Rust Proof Coatings
The composition of rust proof coatings is a fundamental aspect that influences their effectiveness in preventing corrosion in steel. Various materials are used in these coatings, each offering distinct protection mechanisms that can significantly affect their performance and suitability for specific applications. Understanding these compositions helps professionals and researchers select the best coating for their needs based on environmental conditions, desired durability, and economic considerations.
Types of Protective Coatings
Zinc Coatings
Zinc coatings, often applied through processes like hot-dip galvanizing, are crucial for protecting steel against rust. These coatings work through a mechanism where zinc acts as a sacrificial metal. When exposed to corrosive elements, zinc oxidizes before the underlying steel does.
A key characteristic of zinc coatings is their ability to weld well with steel, which enhances adhesion and durability. This property makes them a popular choice for various applications, including construction and automotive industries. The unique feature of zinc is its sacrificial nature; when scratched, zinc continues to provide protection to the exposed steel surface.
However, zinc coatings have disadvantages as well. Their performance can diminish in highly acidic or alkaline environments, limiting their use in those conditions.
Polymer Coatings
Polymer coatings, including epoxy and polyurethane, are another significant category in rust proofing technology. These coatings form a thick, resilient film on the steel surface, providing a barrier that prevents moisture and corrosive agents from reaching the metal. Their flexibility and impact resistance are notable advantages.
The key characteristic of polymer coatings is their variety of formulations, allowing customization based on need. These coatings can offer excellent chemical resistance and UV stability. Thus, they are often used in environments exposed to harsh conditions, such as in marine applications or chemical plants.
A unique feature of polymer coatings is their blend of aesthetic qualities and strong protection, making them attractive for applications where appearance is also a concern. However, they may require careful surface preparation and application techniques to ensure optimal performance, which can increase cost and labor.
Galvanization
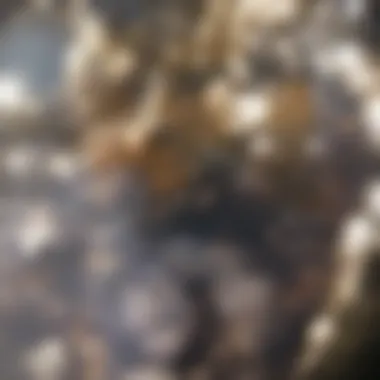
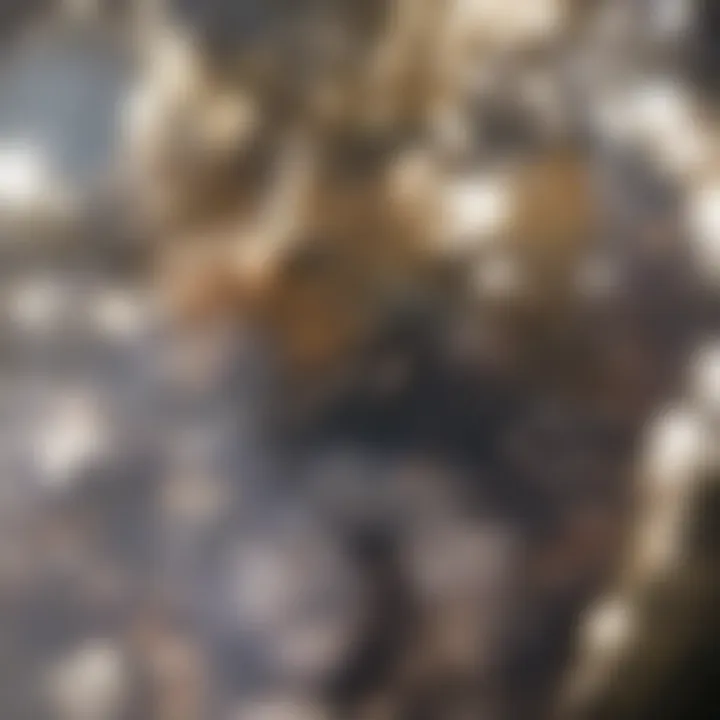
Galvanization often refers specifically to the process of applying a protective zinc coating to steel. This method includes both hot-dip galvanizing and electro-galvanizing, each providing different advantages. Hot-dip galvanizing involves dipping steel parts into molten zinc, ensuring that even the most intricate geometries receive proper coverage.
A key characteristic of galvanization is its long-lasting protection. Typically, a hot-dip galvanized coating can last several decades when correctly applied and maintained. The unique feature of galvanization lies in its comprehensive coverage, which shields steel from corrosive factors. However, the process can be expensive compared to other coating methods, and the finish may not be ideal for all aesthetic applications.
Chemical Properties
The chemical properties of rust proof coatings also play a vital role in their effectiveness. These properties determine how well the coating interacts with the environment, steel substrate, and other chemicals it may encounter throughout its lifespan. Understanding these chemical characteristics ensures the selection of the most appropriate coating system, aligning with the specific needs of the project or application.
Application Techniques
Understanding the various application techniques for rust proof steel coating is essential for achieving optimal corrosion resistance. The method chosen for applying these coatings can greatly affect the final performance, lifespan, and effectiveness of the coating. Each technique has its unique requirements, advantages, and limitations which must be considered to ensure successful implementation.
Surface Preparation
Surface preparation is a crucial step before the application of rust proof coatings. It involves cleaning the substrate to remove contaminants, such as dust, grease, and oxidation. The quality of surface preparation directly influences adhesion, which is vital for the effectiveness of the coating.
Common practices for surface preparation include:
- Mechanical Cleaning: Using tools like sanders or grinders to physically remove surface contaminants.
- Chemical Cleaning: Employing solvents or acids to dissolve impurities.
- Abrasive Blasting: Utilizing high-pressure streams of sand or other materials to clean surfaces thoroughly.
Ensuring the surface is properly prepared reduces the risk of premature failure in the coating. Therefore, investing time in this step pays off in the long term by enhancing durability and performance.
Coating Methods
Spray Application
Spray application is a widely-adopted technique known for its flexibility and efficiency. It allows for even coverage over complex shapes and hard-to-reach areas, which is essential in ensuring that all surfaces receive adequate protection against corrosion.
The key characteristic of spray application is its adaptability. It can be employed with various types of coatings, including liquid and powder formulations. This versatility makes it a popular choice among professionals in the industry.
However, this method has some disadvantages, such as overspray loss and the requirement for protective gear due to potential inhalation of particles. Attention to detail during the application process is also crucial to minimize wastage.
Dip Coating
Dip coating involves submerging the steel components into a coating solution, allowing complete coverage. This method is particularly effective for items with intricate geometries, ensuring that the protective layer penetrates all crevices.
One key characteristic of dip coating is its ability to create a thick, consistent layer. This feature makes it a favorable choice when a robust protective barrier is required. The unique advantage of this method is its simplicity and uniformity; however, it can lead to increased material usage and potential run-off issues that must be managed.
Electrostatic Application
Electrostatic application is a sophisticated technique that employs electrical charges to help powder coatings adhere to the surface of the steel. This method is efficient and reduces waste significantly, as the charged powder particles are attracted to the grounded substrate.
The key characteristic of electrostatic application is its high transfer efficiency. As a result, it is often seen as an eco-friendly option. The unique feature of this technique is its precision, as it can apply coatings uniformly, even on complicated shapes. Nonetheless, this method may require specialized equipment and is sensitive to environmental conditions during application.
Effective application techniques are vital for achieving long-lasting rust protection. Proper methods not only enhance durability but also contribute to overall project efficiency.
Performance Evaluation
A structured evaluation helps in identifying both the strengths and weaknesses of different coatings. For industries heavily reliant on steel structures, knowing the performance dynamics can lead to better material choices. Failures can be costly, thus highlighting the value of thorough testing and evaluation.
Testing Methods
Salt Spray Test
The salt spray test is a standard method used to assess the corrosion resistance of materials. It simulates a saline environment that is common in coastal regions or industrial settings. The key characteristic of this test is its ability to accelerate corrosion processes, making it a popular choice in evaluating coatings.
This test works by exposing the coated samples to a saline mist at controlled temperatures. After a defined period, inspectors analyze the amount of corrosion present on the steel. The main advantage of the salt spray test is that it provides quick results, allowing for efficient decision-making. However, it is worth noting that this test can sometimes misrepresent the real-world performances of coatings, as it encapsulates a specific environment rather than diverse conditions.
Adhesion Testing
Adhesion testing evaluates how well a coating adheres to the substrate. This is crucial. Poor adhesion can lead to delamination and failure, even if the coating itself is corrosion-resistant. The primary method used for adhesion testing includes tape tests, where adhesive tape is applied to the coating and then pulled away.
A high bond strength indicates good adhesion. This method is beneficial because it is straightforward and provides immediate feedback about the integrity of the coated surface. On the downside, it may not detect subtle adhesion issues that could occur under different stress conditions.
Thickness Measurement
Thickness measurement is another vital component in performance evaluation. It helps in determining if a coating is applied uniformly and sufficiently. Measurement devices such as micrometers or ultrasonic thickness gauges are used to obtain accurate readings.
The main advantage of measuring coating thickness is that it can predict long-term performance. An inadequate thickness may lead to premature failure. However, this method requires precise calibration of measuring instruments to yield reliable results.
Durability Assessments
Durability assessments offer insights into how coatings perform over time. These tests often include cyclic corrosion testing, thermal cycling, and impact resistance tests. They provide a comprehensive view of how coatings behave under stress, environmental changes, and extended exposure to corrosive conditions.
By focusing on durability, industries can choose coatings that not only inhibit rust but also withstand the challenges posed by their specific applications. In an era where material longevity is paramount, such assessments become integral to the selection process of rust-proof coatings.
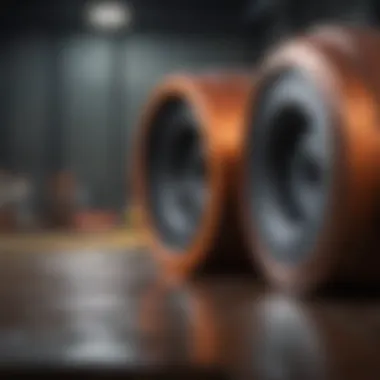
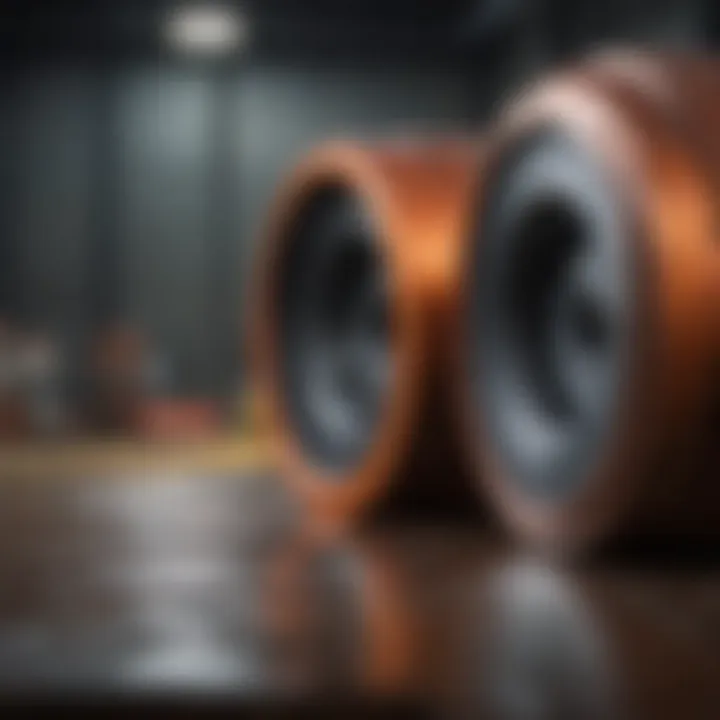
The evaluation of rust proof coatings goes beyond mere performance; it shapes decisions that protect investments and ensure safety across industries.
Industry Applications
The area of rust proof steel coating serves numerous industries, each with distinct needs and benefits. The relevance of this section in the overall article lies in showcasing how these coatings extend the life of steel structures and components. Prioritizing durability and performance is essential in sectors like construction, automotive, and marine. Each of these industries has unique environmental challenges that make rust proof coatings indispensable.
Construction
In the construction industry, rust proof steel coating plays a vital role in protecting steel structures against various forms of corrosion, which can severely reduce their lifespan. For instance, exposed reinforcing steel bars are often at risk of rust formation due to moisture exposure. Applying a rust proof coating ensures durability and safety in buildings, bridges, and other structures.
This protective measure not only enhances longevity but also reduces maintenance costs. It minimizes the frequency of repairs and replacements, which can be both costly and time-consuming. Moreover, the aesthetic appeal of buildings can also be preserved, as coatings can be designed to maintain their appearance over years.
Automotive
The automotive sector relies heavily on rust proof coatings to protect vehicles from the harsh elements of the environment. Cars are exposed to rain, snow, salt, and other corrosive agents that can trigger rust formation. Rust proof coatings create a barrier that guards the metal against these elements, enhancing the vehicle's lifespan and overall performance.
Additionally, the application of these coatings can also contribute to fuel efficiency. During manufacturing, lightweight and corrosion-resistant materials are utilized, aiding in the reduction of vehicle weight and therefore improving fuel economy. The long-term cost savings from reduced maintenance are a significant advantage for car manufacturers.
Marine
The marine industry is singularly affected by corrosion due to constant exposure to saltwater, humidity, and temperature fluctuations. Rust proof coatings are essential in protecting boats and ships, which face these harsh conditions daily. Without proper protection, metal components can deteriorate quickly, leading to expensive replacements and potential safety hazards at sea.
Different marine-grade coatings are designed specifically for this environment, offering significant resistance to the corrosive properties of saltwater. The long-term benefits include not only safety but also enhanced operational efficiency and sustainability in marine operations.
Understanding how rust proof steel coatings are applied in these industries helps underline their importance in maintaining infrastructure and vehicles. The continual advancements in coating technologies reflect the need for innovation in response to environmental challenges and industrial demands.
Environmental Considerations
The integration of environmental considerations within the realm of rust proof steel coating serves as a critical element, especially as industries strive for sustainability. This section examines the relationship between protective coatings and environmental impact, emphasizing the need for eco-friendly approaches while maintaining performance standards.
Eco-Friendly Coatings
Eco-friendly coatings are designed to reduce the impact on the environment throughout their lifecycle. Traditional coatings often contain volatile organic compounds (VOCs) that contribute to air pollution. Modern eco-friendly alternatives aim to minimize or eliminate these harmful substances.
- Water-based Coatings: These coatings utilize water as a solvent, significantly reducing VOC emissions. They offer comparable performance to traditional coatings while being safer for both users and the environment.
- Biodegradable Coatings: Some innovations include coatings made from natural materials that break down more easily in the environment. These coatings can mitigate adverse ecological impacts while still providing rust protection.
- Recyclable or Reusable: Coatings that can be repurposed after their use represent an environmentally responsible choice. This approach prevents waste and promotes a circular economy.
Regulations and Standards
The implementation of regulations and standards relative to rust proof coatings is crucial in ensuring that these products are both effective and environmentally safe. Various organizations have established guidelines that manufacturers must comply with, promoting responsible production and usage of protective coatings.
- EPA Regulations: The Environmental Protection Agency has set limits on VOC emissions from coatings. This pushes manufacturers to adopt greener technologies to align with these standards.
- ISO Standards: The International Organization for Standardization provides frameworks for evaluating environmental impact. Coatings meeting these standards are recognized for their reduced ecological footprint.
- Green Certifications: Programs such as the Green Seal certify products based on their environmental benefits, offering consumers guided choices. This creates market incentive for manufacturers to invest in eco-friendly innovations.
Adhering to these regulations not only ensures compliance but also promotes corporate responsibility and sustainability.
Future Trends in Rust Proof Coatings
As industries evolve, so too do the methods and materials used to combat corrosion. The future trends in rust proof coatings are not merely about improving existing products but are essential in adapting to new challenges faced by various sectors. The integration of advanced technologies, the growing emphasis on sustainability, and the quest for enhancing performance are key elements under discussion in this section.
Innovations in Material Science
The field of material science is pivotal for developing innovative rust proof coatings. Researchers are continually seeking to enhance the durability and effectiveness of these coatings. New formulations that combine various materials are now being investigated. For example, smart coatings that can self-repair damaged areas are a significant advancement. These coatings utilize microcapsules that release healing agents when the coating is scratched or damaged, such as with ExoCoat products.
Also, the use of bio-based materials is gaining traction. Traditional coatings often rely heavily on petroleum-based chemicals. However, more research is directed towards plant-based alternatives which are not only eco-friendly but can also perform comparably to conventional materials. This transition is driven by both regulatory changes and a societal push for sustainable practices.
"The future of coatings lies in the balance between effectiveness and environmental responsibility."
Nanotechnology in Coatings
Nanotechnology is reshaping the landscape of rust proof coatings. By manipulating materials at the atomic or molecular level, scientists are able to create coatings that possess superior protective qualities. For example, nanostructured coatings can exhibit enhanced resistance to moisture, UV light, and physical abrasion.
These nanoparticles can be engineered to create a multi-layered barrier that significantly reduces corrosion rates. Additionally, they can facilitate better adhesion to surfaces, leading to longer-lasting performance. Nanotechnology also enables the development of coatings with tailored properties, such as antimicrobial effects, which can be crucial in certain applications.
The merging of nanotechnology with rust proof coatings highlights a new direction for not only improving performance but also extending the lifespan of components in harsh environments. Industry sectors such as automotive and marine are particularly focused on these advances, ensuring equipment longevity and efficiency.
In summary, the future trends in rust proof coatings indicate a shift towards sustainability and technological innovation. By leveraging material science and nanotechnology, industries can better combat corrosion, leading to better product performance and less environmental impact. The continued exploration in these areas will be vital for meeting future corrosion challenges.
Challenges in Rust Proof Coating Applications
Rust proof steel coatings provide essential protection against corrosion in various industries. Yet, their application faces certain challenges that can hinder their effectiveness and market acceptance. Understanding these challenges is crucial for enhancing performance and driving innovation. The focal points in this section include material limitations and economic factors, which greatly influence the adoption and performance of these coatings.
Material Limitations
One prominent challenge in rust proof coatings is associated with material limitations. Various substrates have distinct properties which can complicate adhesion and overall performance.
For example, the surface texture and composition of steel can affect how well a coating sticks. If the steel has impurities or oxidation, the coating may not adhere properly. Additionally, certain coatings may not perform well at high temperatures or when exposed to aggressive chemicals. These limitations may restrict their application in particular environments, making it necessary for manufacturers to choose the appropriate type of coating based on specific conditions.
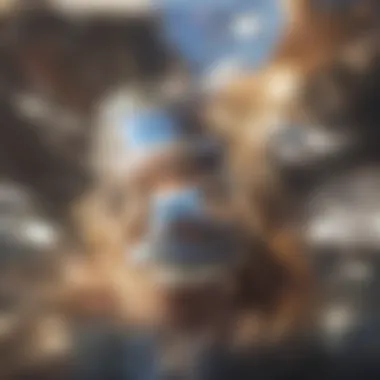
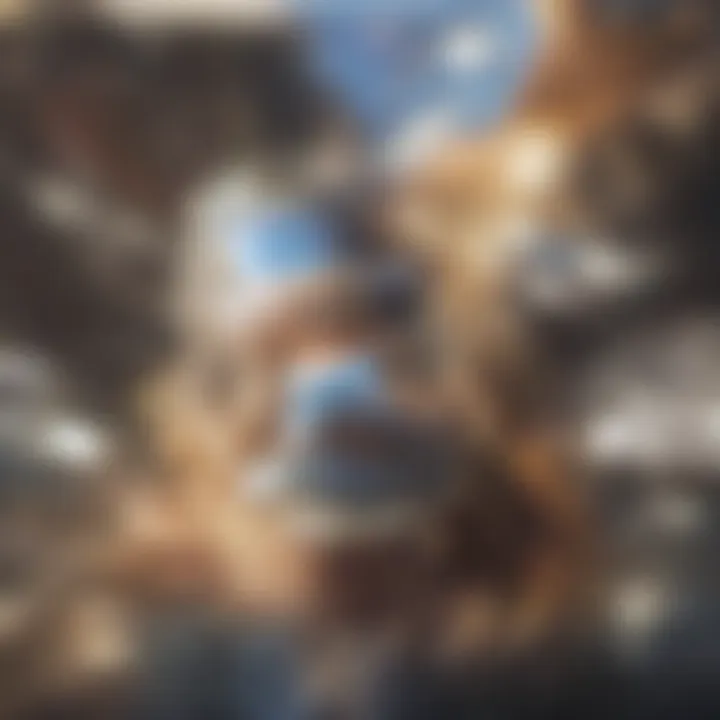
Moreover, not all coatings can withstand physical stress or mechanical abrasion. Coatings that lack toughness can fail prematurely, creating vulnerability to rust. These aspects must be taken into account when selecting a protective solution.
Economic Factors
Economic considerations are also significant in the application of rust proof steel coatings. The cost of the coating material itself can be high, and the processes required for surface preparation and application might add to the overall expenses. For many businesses, especially small and medium enterprises, these costs can be a deterrent to investing in such technology.
On top of the initial investment, ongoing maintenance and inspection costs are factors that should not be overlooked. High-quality coatings may require less frequent maintenance, but if a less durable coating is chosen for cost-saving reasons, the eventual need for repair or reapplication may lead to greater expenses.
Cost-efficiency and long-term reliability are key considerations in selecting rust proof coatings.
Additionally, market fluctuations and varying demand can impact prices. Companies may hesitate to commit to coating solutions, fearing financial risks associated with significant upfront costs. Understanding these economic factors can help industries to navigate challenges and make more informed decisions about rust proofing applications.
Case Studies
Case studies play a crucial role in understanding the practical implications and outcomes of rust proof steel coatings in different environments. They provide real-world evidence of the effectiveness and limitations of various coating technologies. Through analyzing these case studies, researchers, professionals, and students can gain deeper insights into how specific coatings perform, the factors contributing to their success or failure, and the lessons learned from those experiences. This narrative can guide future practices and innovations within the industry.
Successful Implementation
The examination of successful implementations of rust proof steel coatings reveals a number of key factors that contribute to their effectiveness. One notable case study involves the application of Galvalume in industrial storage tanks. The corrosion-resistant properties of this coating extended the lifespan of the tanks significantly, reducing maintenance costs by over 30% compared to traditional coatings.
- Critical Elements of Success:
- Thorough surface preparation ensured strong adhesion.
- Proper application techniques minimized defects in the coating process.
- Environmental controls during application prevented adverse reactions.
In this instance, the synergy of these factors led to measurable performance improvements over time, illustrating the practical benefits of implementing high-quality rust proof coatings in an industrial setting.
Failure Analysis
On the other hand, examining failures provides a contrasting perspective that is equally valuable. A relevant failure analysis involved the use of a specific polymer-based coating on a marine vessel. Despite initial expectations, the coating did not adhere well in the high-salinity environment, leading to premature rust formation.
This situation highlights several important considerations:
- Factors Leading to Failure:
- Insufficient surface cleaning prior to application.
- Incompatibility of the coating with environmental conditions.
- Lack of ongoing assessment post-application to monitor performance.
This failure serves as a reminder that the success of rust proof coatings is not only about the choice of material but also the context of application and ongoing evaluation. It underscores the importance of thorough planning and adaptation to specific operational environments.
Key Takeaway: By studying both successful implementations and failures, industry professionals can develop a more comprehensive understanding of the complexities involved in rust proof steel coating applications, ultimately leading to better decision-making and innovation.
Expert Opinions
Understanding the rust proof steel coating requires insights from both industry leaders and academic professionals. Their perspectives highlight crucial developments that shape the field. Industry leaders bring practical experience to the table, while academic opinions provide a theoretical framework.
The integration of these viewpoints forms a multi-dimensional understanding of rust proof coatings. This section will explore how their insights contribute to knowledge in materials science, application techniques, and environmental impacts.
Industry Leaders' Insights
Industry leaders play a pivotal role in advancing rust proof steel coatings. They observe real-world applications and identify trends that influence manufacturing processes. Their insights are essential in adapting coatings to meet specific industry requirements. For example, the automotive industry demands coatings that withstand extreme conditions. As such, leaders often highlight innovations that improve corrosion resistance, longevity, and aesthetic quality in finishes.
These professionals also stress the importance of regulatory compliance. With environmental standards becoming stricter, coatings must not only perform well but also adhere to guidelines. Industry leaders report on the challenges faced in selecting eco-friendly options that maintain effectiveness while reducing harmful emissions. Their practical experiences guide improvements and innovation in formulations and application practices.
Additionally, they provide valuable data on failure rates and performance metrics, enabling better decision-making regarding coating materials and methods.
Academic Perspectives
Academics contribute a different but equally significant viewpoint on rust proof coatings. They focus on research and development, often exploring the science behind corrosion and protective mechanisms. This research is crucial in advancing our understanding of material interactions in various environments.
Scholars conduct experiments to analyze coating performance under controlled conditions, providing data that supports or challenges industry practices. Their work often includes exploring novel materials and methods, enhancing knowledge on long-term durability and effectiveness.
In academic discussions, emphasis is often placed on the need for sustainable practices. Researchers advocate for the development of coatings that are both effective and kind to the environment. Studies demonstrate how these alternative coatings can reduce overall ecological footprints in manufacturing and usage.
Furthermore, the academic community fosters collaborations between manufacturers and researchers. This collaboration promotes the sharing of insights and facilitates a more rigorous testing of products before they reach the market, ensuring that innovations are both functional and safe.
Culmination
The conclusion serves as a vital component of this article, highlighting the main insights and implications of rust proof steel coating in various industries. It summarizes the overarching themes from previous sections, consolidating knowledge that is crucial for stakeholders involved in material science, engineering, and environmental protection.
Summary of Key Points
In our exploration, we have touched on several key points, including:
- The Mechanism of Protection: Understanding how rust proof coatings function to prevent degradation of steel due to corrosion.
- Industry Applications: The diverse uses of such coatings across construction, automotive, and marine sectors.
- Environmental Considerations: The moving landscape of regulations affecting the development and application of these coatings, pushing for eco-friendly solutions.
- Future Trends: Technological advancements and innovations, especially in nanotechnology, which hold promise for the evolution of more effective rust proofing methodologies.
By reviewing these aspects, we can appreciate the depth of knowledge surrounding rust proof coatings and their relevance in contemporary industry practices.
Future Outlook
Looking ahead, the future of rust proof steel coatings is informed by both challenges and opportunities. Innovations in materials may lead to more resilient and less environmentally harmful coatings. Manufacturers may begin to shift toward more sustainable practices, focusing on biodegradable elements within the coatings. A significant trend could be the incorporation of smart technologies that provide real-time monitoring of coating integrity.
In summary, as industries continue to evolve, the significance of understanding and implementing effective rust proof coatings will only grow. Research and investment in this area is likely to expand, providing better solutions for corrosion resistance that align with both performance and environmental stewardship.