Understanding Reverse Logistics in Supply Chain Management
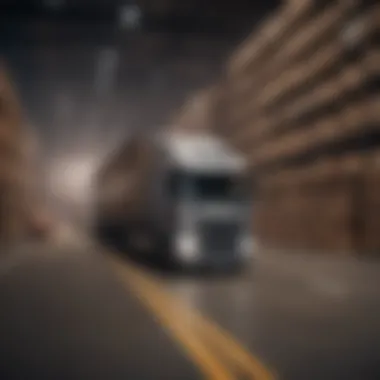
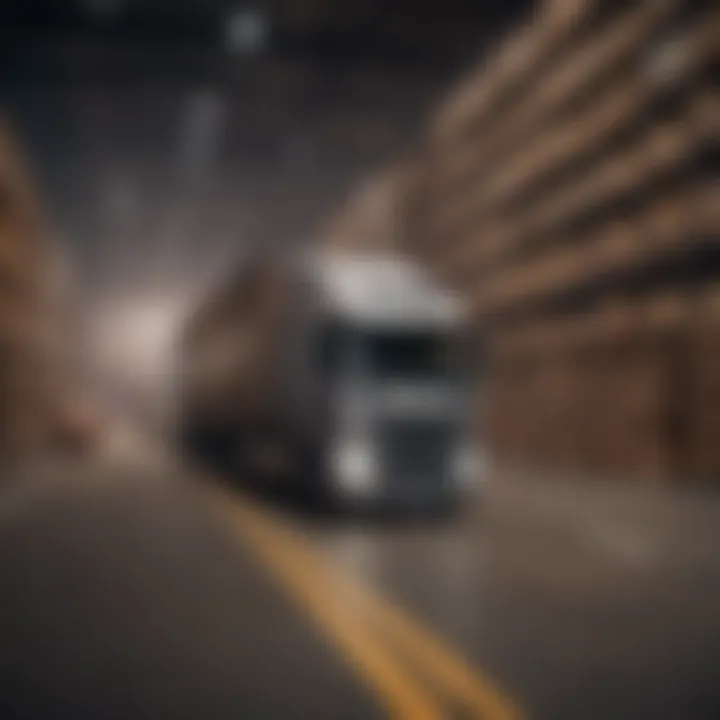
Intro
Reverse logistics is a crucial aspect of supply chain management that often goes unnoticed despite its significant implications for business operations. At its core, reverse logistics involves the process of planning, implementing, and controlling the efficient flow of goods that move from their final consumption back to the point of origin. This process is not merely about moving products back; it encompasses the entire lifecycle of a product, including ensuring product returns, repairs, recycling, and even proper disposal.
Understanding reverse logistics is essential for modern businesses as it directly impacts profitability, sustainability, and consumer satisfaction. In recent years, organizations have recognized that effective reverse logistics not only enhances operational efficiency but also contributes to competitive advantage. It encourages companies to adopt practices that minimize waste and decrease costs while meeting the growing demand for environmentally responsible operations.
This article will explore various elements of reverse logistics, including its definition, significance in contemporary supply chains, and how it differs from traditional logistics. We will delve into the components, benefits, and challenges associated with it, providing a thorough understanding of its role in business environments.
In the forthcoming sections, we aim to unfold the complexities surrounding reverse logistics and provide readers with insights relevant to students, researchers, and practitioners in supply chain management. By grasping these concepts, readers can better appreciate how reverse logistics contributes to improved business outcomes and aligns with today’s sustainable practices.
What is Reverse Logistics?
Reverse logistics is a critical aspect of supply chain management that focuses on the reverse flow of goods, from the customer back to the manufacturer or supplier. This process includes activities associated with the return of products, their reuse, recycling, and proper disposal. Its relevance continues to grow as companies strive to optimize their operations and enhance environmental sustainability. In an era where consumer expectations have risen for quick resolutions and sustainable practices, understanding reverse logistics becomes essential.
Definition and Scope
Reverse logistics refers to all operations related to the reuse of products and materials. It encompasses a variety of processes such as returns management, refurbishment, recycling, and waste management. As businesses recognize the need to manage this flow, they identify reverse logistics not only as a necessity but also as a potential revenue stream. The scope of reverse logistics is wide, including:
- Returns handling
- Warranty recovery
- Asset recovery
- Remanufacturing
- Recycling initiatives
Understanding the scope allows organizations to design systems that can handle these operations efficiently.
Key Components
Several key components drive the efficiency and effectiveness of reverse logistics. These include:
- Returns Management: This involves handling returned goods and determining their next steps—whether they will be restocked, repaired, or recycled.
- Refurbishing and Repair: This process gives new life to products through refurbishment and repair, contributing to both customer satisfaction and resource optimization.
- Recycling and Disposal: Effective recycling strategies ensure that materials are recovered and reused, reducing environmental impact. Proper disposal practices are necessary for materials that cannot be recycled.
Each of these components plays a vital role in shaping a robust reverse logistics framework while also influencing cost savings and enhancing customer service. Understanding these elements is crucial for industries aiming to streamline operations and respond effectively to the growing demands of the market.
"Reverse logistics not only contributes to company profits but also plays a pivotal role in meeting increasing sustainability goals."
Historical Context of Reverse Logistics
The historical context of reverse logistics plays an essential role in understanding how this concept has developed within supply chain management. It reveals the progression of practices and strategies that have shaped current operations. Recognizing this evolution gives insights into why businesses implement reverse logistics and its benefits.
Evolution of Supply Chain Practices
Initially, traditional logistics focused primarily on the forward flow of products, from manufacturers to consumers. The return of goods was often an afterthought, handled in a piecemeal fashion. As global trade expanded and consumer expectations changed, the necessity for a more systematic approach to handling returns emerged. This transition marked the beginning of reverse logistics as a recognized field.
The 1990s represented a crucial period for reverse logistics. Companies started to notice that managing product returns and excess inventory was not just about cost, but also about opportunity. Emphasis shifted from merely disposing of unsold products to recovering value. This shift allowed firms to reclaim substantial resources through returns management, recycling, and remanufacturing processes.
Recent trends indicate that technology has further influenced the evolution of reverse logistics. Supply chain professionals now leverage data analytics to optimize return processes. Advanced inventory management systems aid in tracking returned items and assessing their potential for refurbishment. Moreover, the rise of e-commerce has drastically transformed how returns are handled, pushing businesses to refine their reverse logistics practices.
Pioneering Companies in Reverse Logistics
Several companies have placed reverse logistics at the core of their operations. Dell, for example, revolutionized the computer industry with its focus on remanufacturing. The company encouraged customers to return old electronics, which were then refurbished and sold at reduced prices. This practice not only reduced electronic waste but also enhanced customer loyalty.
Coca-Cola has implemented effective reverse logistics systems for managing returned packaging. By facilitating the collection of bottles and cans, Coca-Cola minimizes environmental impact while preserving resources. Their initiative not only emphasizes sustainability but also focuses on efficiency in operations.
Furthermore, Zappos, an online shoe retailer, offers a robust returns policy, prioritizing customer satisfaction. Their hassle-free return process serves as a competitive advantage, illustrating the value of effective reverse logistics in advancing consumer trust.
"The historical development of reverse logistics is not just a reflection of change; it also indicates the evolving nature of consumer expectations and corporate responsibility."
Understanding the historical context gives relevant insights into how companies can advantageously adapt to dynamic market demands. It opens avenues for further research and innovation in the field of reverse logistics.
Reverse Logistics vs. Traditional Logistics
Understanding the differences and similarities between reverse logistics and traditional logistics is core to grasping the complexities of supply chain management. Reverse logistics is concerned with the processes involved in moving goods from their final destination back to the manufacturer or distributor for recapture, reuse, remanufacturing, or recycling. Traditional logistics, on the other hand, primarily focuses on the flow of products from suppliers to consumers with the intent of maximizing efficiency in deliveries.
When evaluating these two systems, the distinctions become apparent. Traditional logistics emphasizes the forward flow of goods. It often overlooks the significance of returns and aftersales support. In stark contrast, reverse logistics prioritizes the recovery and management of products that have deviated from the typical supply chain flow. This may include defective items, excess inventory, or returned products. This difference highlights the importance of adopting a holistic approach to logistics that incorporates both forward and reverse perspectives.
Comparative Analysis
The comparative analysis of reverse logistics and traditional logistics reveals distinct objectives and methodologies.
- Focus: Traditional logistics aims to deliver products efficiently, while reverse logistics aims to recover value from products that have already been sold and returned.
- Processes: Traditional logistics encompasses activities like transportation, storage, and inventory management. Reverse logistics involves processing returns, refurbishing, and recycling.
- Metrics: Success in traditional logistics is often measured by on-time delivery rates and cost efficiency. In reverse logistics, success is measured by recovery rates, customer satisfaction after returns, and overall product lifecycle management.
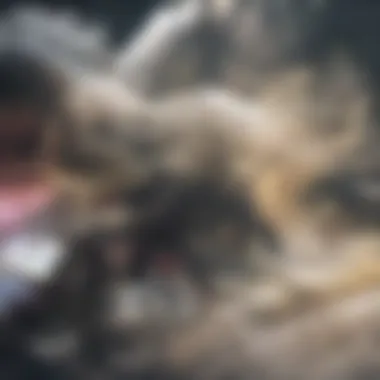
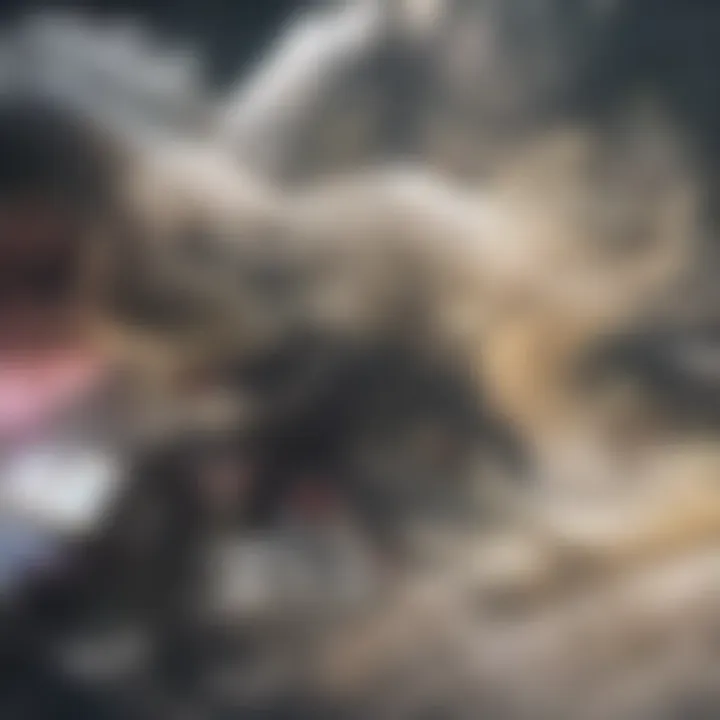
Both play essential roles in supply chain management, yet they require different strategies and technologies to optimize their effectiveness. Understanding their dynamics is critical for any business intending to balance operational efficiency with customer satisfaction and sustainability.
Operational Differences
Operational differences between reverse logistics and traditional logistics manifest in various forms.
- Flow of Information: Traditional logistics relies on demand forecasting to inform inventory decisions. Reverse logistics needs real-time data on returns and reasons for returns to improve processes and reduce future occurrences.
- Customer Interaction: Traditional logistics primarily interacts with the customer at the point of sale. In contrast, reverse logistics often requires ongoing communication post-purchase regarding returns, replacement, or refund processes.
- Cost Structure: The cost implications are also different. Traditional logistics can achieve economies of scale through bulk shipment and storage. Reverse logistics often incurs varying costs due to unpredictable return rates, the need for quick processing, and the requirement for specific handling of returned goods.
- Technology Utilization: Technology application differs as well. While traditional logistics makes heavy use of supply chain management systems for tracking deliveries, reverse logistics increasingly employs analytics and artificial intelligence to assess return patterns and optimize future product designs.
In summary, while reverse and traditional logistics may share objectives related to the efficient handling of goods, their operational frameworks compel businesses to adapt their strategies significantly to address the unique challenges and opportunities presented by each. The recognition of this distinction is vital for organizations aiming to enhance their supply chain performance.
Importance of Reverse Logistics in Supply Chain
Reverse logistics holds a pivotal role in the effectiveness of supply chain management. It encompasses all operations related to the reuse of products and materials. Emphasizing this aspect can yield substantial benefits for businesses. Understanding the importance of reverse logistics allows organizations to enhance profitability while offering superior service. It moves beyond merely handling returns. It aims to create a systematic approach that optimizes resource recovery and minimizes waste.
Cost Efficiency
A crucial aspect of reverse logistics is its impact on cost efficiency. Companies often overlook the potential savings from efficient returns management. By refining processes, businesses can significantly reduce transportation and storage costs. Efficient reverse logistics practices include:
- Optimizing transportation routes for returning products
- Utilizing technology to streamline processes
- Implementing effective inventory management practices
These methods help cut unnecessary expenses. For instance, a well-organized return process can reduce the costs associated with faulty goods. Moreover, the refurbishment of returned items can also generate revenue. Companies like Dell have shown how effectively managing returns can become a profit center.
Customer Satisfaction
Customer satisfaction is increasingly linked to how efficiently returns are processed. A seamless return experience enhances customer trust. If customers perceive the return process as hassle-free, it encourages repeat business. Key strategies to boost satisfaction include:
- Providing clear return policies
- Communicating transparently about return procedures
- Offering multiple return channels
Enhancing customer satisfaction through effective reverse logistics can lead to increased loyalty and ultimately higher sales. According to a recent survey, 92% of consumers will buy again if the returns process is easy. Therefore, businesses must recognize that reverse logistics is integral to customer experience.
Sustainability and Environmental Impact
In today's world, sustainability is a pressing concern. Reverse logistics directly contributes to reducing the environmental footprint of businesses. By focusing on sustainability, companies can:
- Reduce waste through recycling and refurbishing products
- Lower carbon emissions from transportation
- Promote a circular economy by redistributing resources
Implementing sustainable reverse logistics can enhance corporate reputation and compliance with regulations. More consumers lean towards brands that demonstrate environmental responsibility. This shift shows companies can no longer afford to view reverse logistics as a cost center. Instead, they should see it as a strategic opportunity to foster sustainability and innovation.
Processes Involved in Reverse Logistics
Reverse logistics plays a vital role in modern supply chain management. It encompasses a series of processes that aim to maximize value from returned products and reduce waste. Understanding these key processes is essential for organizations that seek to enhance their operational efficiency and sustainability initiatives. In this section, we will explore the three main processes involved in reverse logistics: returns management, refurbishing and repair, and recycling and disposal.
Returns Management
Returns management is a critical process in reverse logistics. This involves handling products that customers return for various reasons, such as defects, dissatisfaction, or changes in preferences. Effective returns management can improve customer satisfaction by providing a seamless experience. Companies should establish a robust return policy that communicates clearly to customers about how to return products.
The returns process typically includes several steps:
- Authorization: The customer must obtain approval to return the item.
- Inspection: Each returned item should be inspected to assess its condition and determine the next steps.
- Restocking: Products in good condition can be restocked, while defective or damaged items may need to be addressed differently.
By streamlining returns management, organizations not only enhance customer experience but can also recover value from returned goods.
Refurbishing and Repair
Refurbishing and repair are crucial for extending the life cycle of products. This process involves restoring products to a condition that can either return them to market or ensure they can be used within the organization itself. Refurbishing might include cosmetic repairs, cleaning, or upgrading components.
The decision to refurbish depends on several factors:
- Cost: It must be financially viable to refurbish the product compared to other options.
- Market Demand: Companies must assess whether customers will still find the refurbished item appealing.
- Technical Feasibility: Technical issues must be solvable to ensure a successful refurbishment.
Well-executed refurbishing processes not only recover assets but also support sustainability initiatives by reducing waste.
Recycling and Disposal
Recycling and disposal focus on addressing products that cannot be resold or refurbished. This process ensures that materials are handled responsibly, minimizing environmental impact. Proper recycling can recover valuable materials such as metals, plastics, and components that can be reused in manufacturing. In some cases, products may be disposed of due to safety concerns or if they cannot be recycled economically.
To successfully implement recycling and disposal, organizations should follow these considerations:
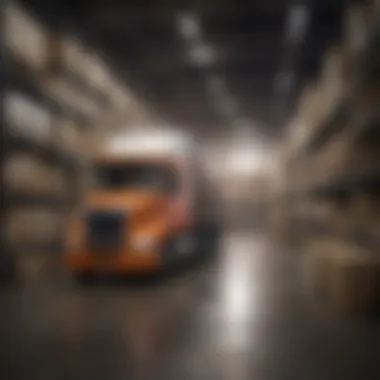
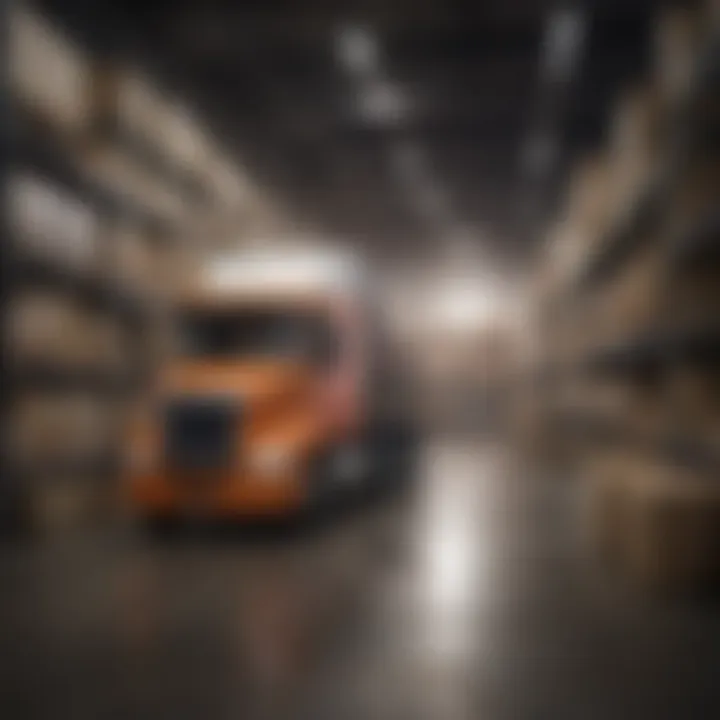
- Compliance: Companies must adhere to environmental regulations relevant to waste management.
- Partnering with Specialists: Collaborating with recycling experts can ensure efficient and responsible handling of waste.
- Consumer Education: Informing consumers about recycling programs can stimulate participation.
The efficient management of recycling and disposal can bolster a company’s reputation as an environmentally conscious entity, positively impacting brand loyalty.
Remember, the effectiveness of these processes directly influences both operational efficiency and customer satisfaction.
In summary, the processes involved in reverse logistics—returns management, refurbishing and repair, recycling and disposal—are integral to creating value and minimizing waste in supply chains. Focusing on these areas can lead to improved resource utilization and contribute to broader sustainability efforts.
Challenges in Implementing Reverse Logistics
The implementation of reverse logistics presents several hurdles for businesses aiming to optimize their supply chain management. The nature of reverse logistics adds complexity that distinguishes it from traditional logistics. Companies must navigate multifaceted processes and operations that can lead to inefficiencies if not managed correctly. Understanding these challenges is essential for any organization looking to enhance its reverse logistics functions.
Complexity of Returns Process
The returns process in reverse logistics is inherently complicated. Unlike traditional logistics, where the flow of goods is straightforward from supplier to consumer, reverse logistics often involves returning items from consumers back to suppliers or manufacturers. Several factors contribute to this complexity:
- Product Diversity: Different products have unique return policies and processes. For example, electronics may require specific handling while clothing might have less stringent requirements.
- Condition Assessment: Determining the state of returned items—whether they are defective, undamaged, or simply unwanted—adds another layer of complexity. Each condition requires a different subsequent action, such as repair, refurbishment, or disposal.
- Documentation and Regulations: Proper paperwork is critical in reverse logistics. Compliance with regulations, especially when dealing with hazardous materials or sensitive products, is crucial and can become cumbersome.
Overlooking the intricacies of these processes can lead to delays, poor customer satisfaction, and increased operational costs.
Data Management Issues
Data management presents another significant challenge within the realm of reverse logistics. The management of returned goods is data-intensive and requires robust systems to track and analyze various metrics. The issues in this area include:
- Inconsistent Data Entry: In many organizations, different teams might enter data about returns differently, leading to inconsistent information. This can create misinformation and hinder effective decision-making.
- Integration across Systems: Effective reverse logistics requires seamless integration between various systems such as Inventory Management Systems, Customer Relationship Management software, and Enterprise Resource Planning tools. Many firms struggle with achieving this integration, causing disruptions in the return process.
- Real-Time Analytics: Understanding the reasons behind returns is vital for minimizing them. Companies frequently lack the tools to provide real-time analytics on returned products, making it difficult to address issues before they escalate.
Without effective data management, businesses may find themselves unable to capitalize on learning opportunities from the reverse logistics processes and risk persistently repeating mistakes.
Financial Considerations
Financial challenges are often the most daunting aspect of implementing reverse logistics. The costs associated with handling returns can be significant, and organizations must carefully evaluate these aspects. Key financial considerations include:
- Operational Costs: Each return incurs costs related to shipping, processing, and restocking. Mismanagement of these can spiral into considerable financial losses.
- Irrecoverable Inventory: Products returned that cannot be refurbished or resold lead to financial strain. Businesses must find effective strategies to minimize this through better assessment and logistics practices.
- Forecasting Returns: Predicting return rates accurately can be difficult yet is necessary for maintaining healthy cash flow and inventory levels. Unexpected spikes can drown a company in logistics costs.
Overall, the financial implications of reverse logistics processes must be approached with a strategic mindset to avoid potential pitfalls and optimize profitability.
Effective management of reverse logistics requires an in-depth understanding of these challenges, accompanied by a willingness to invest in solutions that streamline processes, enhance data handling, and minimize costs.
Technology and Reverse Logistics
Technology plays a crucial role in the field of reverse logistics. As businesses strive to improve efficiency and reduce costs, integrating technology into reverse logistics processes becomes essential. It enhances communication, data management, and tracking, which are critical elements in managing returns and other reverse processes. The relationship between technology and reverse logistics is not only beneficial but also pivotal in shaping the future of supply chains.
Efficient reverse logistics management hinges on the use of advanced technology. Systems like Enterprise Resource Planning (ERP) and specialized reverse logistics software help organizations streamline operations. These technologies offer visibility across the supply chain, ensuring that returns can be tracked and managed effectively. This capability diminishes the risk of inventory loss and mismanagement.
Key benefits of employing technology in reverse logistics include:
- Improved Inventory Management: Automation and real-time tracking enable companies to maintain optimal inventory levels, reduce overstock, and eliminate shortages.
- Cost Reduction: By optimizing returns processes, companies can significantly lower transportation and handling costs.
- Enhanced Customer Experience: Quick processing of returns can lead to higher customer satisfaction, as customers prefer efficient, hassle-free return policies.
In summary, technology is not just a facilitator in reverse logistics; it is a game changer that enhances overall efficiency and customer satisfaction.
Role of Technology in Optimization
The role of technology is paramount to optimizing reverse logistics. Through advanced software solutions, businesses can analyze data and develop insights that directly improve their processes. This optimization often translates to better decision-making and streamlined operations.
Technologies such as RFID (Radio-Frequency Identification) and IoT (Internet of Things) provide real-time data that supports inventory tracking and returns management. With this ability to monitor products throughout their lifecycle, organizations can better predict returns and manage their supply chain effectively.
Moreover, predictive analytics assists in anticipating customer behavior regarding returns. Organizations can forecast return rates based on historical data and appropriately adjust their strategies to manage inventory and resources efficiently.
- Data-Driven Decisions: Organizations can use historical data to formulate return policies that minimize losses and enhance customer satisfaction.
- Automated Processes: Technologies automate labor-intensive tasks, thereby freeing up resources to focus on strategic activities.
- Scenarios Simulation: Advanced modeling and simulation tools help businesses test various strategies and identify the best possible options for returns management.
Emerging Trends: AI and Analytics
Artificial Intelligence (AI) and analytics are shaping the future of reverse logistics. Companies that harness these technologies gain competitive advantages. AI can analyze vast amounts of data to identify trends and patterns, providing insights that would be impossible to achieve manually.
Several emerging trends in this field include:
- AI for Predictive Analysis: AI tools can forecast which products are likely to be returned based on customer purchase behavior. Businesses can thus prepare in advance for handling returns more efficiently.
- Automation of Returns Processing: Intelligent systems can automate aspects of the returns process, reducing errors and improving throughput.
- Sentiment Analysis: Monitoring customer feedback through AI-driven analytics can help businesses understand pain points in their return processes, enabling them to refine their strategies accordingly.
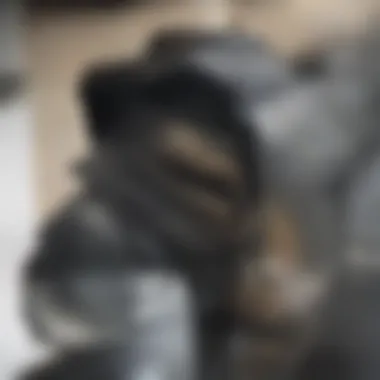
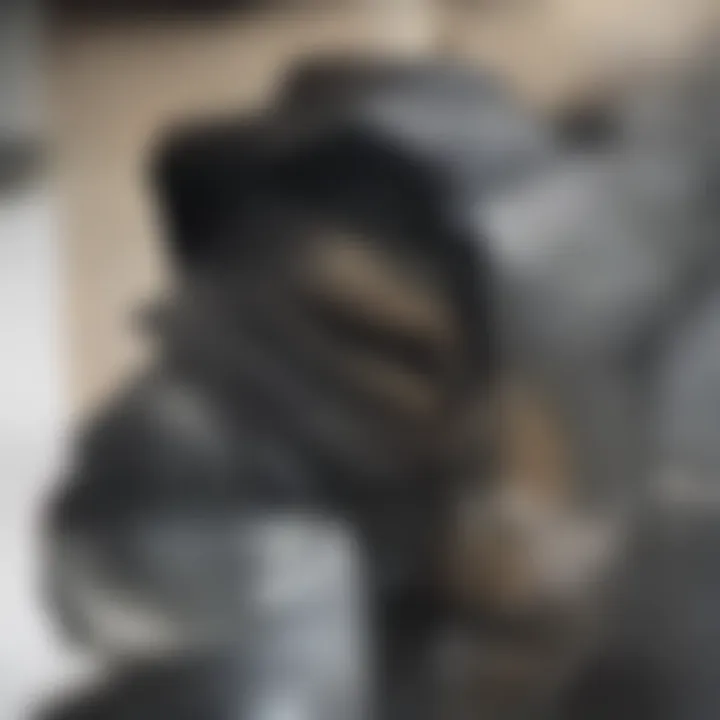
"Innovation in technology is revolutionizing the approach to reverse logistics, leading organizations towards a more efficient and profitable future."
Best Practices for Effective Reverse Logistics
Effective reverse logistics is critical in a supply chain that seeks to maximize efficiency and customer satisfaction. Implementing best practices in this area aids companies in managing returns, refurbishments, and recyclables, which are not just financial burdens, but also opportunities for growth and sustainability.
Developing a Comprehensive Strategy
A comprehensive strategy encompasses various dimensions, including organizational structure, technology, and process design. Developing this strategy requires a detailed assessment of current operations and future goals. Key steps include:
- Assessment of Needs: Identify the type of returns your company typically processes. Different products might require different approaches.
- Technology Integration: Utilize software tools like SAP or Oracle to streamline return management. This allows for processing information in real-time.
- Collaboration with Partners: Work closely with suppliers and logistics partners to ensure a smooth flow in the return process. This can lead to shared resources and faster resolutions.
- Feedback Mechanism: Establish channels to receive input from customers and employees regarding their experiences with returns. This feedback can inform adjustments to strategy.
Implementing these elements not only ensures a robust return process but also enhances operational agility.
Engaging Stakeholders
Engaging all stakeholders—employees, suppliers, and customers—is essential for successful reverse logistics. Each group has unique insights that can contribute to the whole process. Here are several considerations:
- Employee Training: Comprehensive training programs should be established so employees understand the logistics processes thoroughly. Well-informed staff can handle returns effectively and provide better customer service.
- Supplier Relationships: Develop strong relationships with suppliers to facilitate quicker returns or exchanges. Having aligned goals can streamline efforts and mitigate potential disputes.
- Customer Involvement: Keep customers informed about the reverse logistics procedures. Providing a transparent process can enhance trust and lead to a better overall experience.
Engaging stakeholders is not just about communication; it's about creating a culture of collaboration. By including everyone in the process, companies can adapt and improve their reverse logistics operations significantly.
Successful reverse logistics relies heavily on strategic planning and effective stakeholder engagement.
Case Studies in Reverse Logistics
Case studies provide crucial insights into how organizations successfully navigate the complex world of reverse logistics. By studying real-life examples, readers can grasp the practical applications, challenges, and innovative solutions applicable to their own operations. This section not only highlights success stories but also extrapolates valuable lessons that can empower other businesses to refine their reverse logistics strategies.
Success Stories
- Amazon Amazon is recognized for its robust reverse logistics system. The company has implemented an efficient returns process that allows customers to easily return products, which significantly boosts customer satisfaction. By automating many aspects of returns through their platform, Amazon minimizes processing time and maximizes efficiency. They utilize sophisticated data analytics tools to assess return trends, making it easier to manage inventory and optimize supply chain operations.
- Zara
Zara’s strategy includes swift product returns and reselling of returned garments. The brand effectively manages returns by quickly restocking items that are still in excellent condition, which reduces waste and keeps inventory fresh. Their centralized distribution centers play a significant role in facilitating effective returns management, allowing for rapid reshipment and response times. - Coca-Cola
Coca-Cola employs reverse logistics for managing empty containers and recyclable materials. Their focus on sustainability through initiatives such as "World Without Waste" emphasizes recycling and responsible disposal. This not only contributes positively to their brand image but also underlines their commitment to environmental stewardship.
These cases illustrate the transformative power of well-structured reverse logistics practices. They show how successful companies have turned challenges into opportunities by implementing streamlined returns processes, sustainability initiatives, and efficient inventory management.
Lessons Learned
The examination of successful case studies reveals several critical lessons for organizations looking to enhance their reverse logistics capabilities:
- Customer Experience is Key
Prioritizing customer ease in the returns process can significantly boost loyalty. Feedback mechanisms can help businesses understand pain points in the returns experience, allowing for continuous improvement. - Data Drives Decision Making
Leveraging analytics can help companies anticipate return trends and make informed decisions about inventory management. Understanding customer behavior helps organizations tailor their reverse logistics strategies effectively. - Sustainability Matters
Implementing environmentally friendly practices creates brand differentiation. Organizations that incorporate sustainability into their reverse logistics tend to build stronger connections with their customer base. - Invest in Technology
Automation tools and management systems facilitate smoother operations in reverse logistics. Utilizing technology can lead to reduced costs and enhanced efficiency.
Future Directions of Reverse Logistics
The topic of future directions of reverse logistics is crucial in understanding how this field will evolve and adapt to ongoing changes in global supply chains. As businesses strive for greater efficiency and customer satisfaction, reverse logistics must also innovate and incorporate new strategies. These advancements are not just beneficial but necessary for companies looking to remain competitive. In examining future directions, it is important to focus on predictive trends and the influence of globalization, as both play a pivotal role in shaping the landscape of reverse logistics.
Predicted Trends
Several trends are predicted to significantly impact reverse logistics over the coming years. Some of the most notable include:
- Increased Automation: Companies will likely invest in automation technologies for returns processing and inventory management. This improves efficiency by reducing processing time and minimizing human error. Automated systems can quickly analyze returned items, categorizing them for reselling, recycling, or disposal.
- Enhanced Data Analytics: With the advent of big data, businesses are more equipped to gather and analyze vast amounts of information. Predictive analytics will enable firms to forecast return rates, helping them prepare for fluctuations in demand and the impact on inventory levels. Data-driven decisions will lead to greater operational efficiency.
- Sustainability Initiatives: Environmental concerns continue to rise, prompting businesses to adopt sustainable practices. Future reverse logistics strategies will lean towards reducing waste through refurbishing and recycling initiatives. This aligns with consumers' increasing preference for eco-friendly brands.
- Integration of E-commerce Returns: The growth of online shopping has resulted in a boom in returns. Future reverse logistics strategies will need to integrate seamlessly with e-commerce platforms, facilitating smoother return processes and enhancing customer satisfaction.
Impact of Globalization
Globalization contributes significantly to the evolution of reverse logistics. As markets become more interconnected, the implications for reverse logistics strategies are extensive. Specifically:
- Complex Supply Chains: Global supply chains introduce complexity to returns processes. Businesses will need to navigate varying regulations, cultural differences, and logistical challenges in different regions, requiring adaptable strategies.
- Cross-border Returns: As products are sold internationally, the number of cross-border returns will increase. Companies will need to establish efficient processes to manage these returns, which may involve understanding different customs regulations and tax implications.
- Collaboration Across Borders: Companies will likely foster partnerships with local firms and logistics providers to improve the efficiency of their reverse logistics operations on a global scale. Collaboration can enhance knowledge sharing, improve logistics networks, and ultimately lead to more effective returns management.
As we consider the future of reverse logistics, it is evident that businesses will need to prioritize adaptability and progressive strategies. This not only helps them manage current challenges but prepares them for an increasingly complex global market. By staying ahead of predicted trends and recognizing the impact of globalization, companies can turn reverse logistics from a cost center into an innovative aspect of their overall supply chain strategy.
Epilogue
Reverse logistics plays a critical role in the broader framework of supply chain management. Its significance cannot be understated as it addresses various facets like cost reduction, environmental sustainability, and customer satisfaction. The concluding segment ties together all the insights discussed in this article, emphasizing how understanding reverse logistics can lead to more efficient and effective operational strategies.
Summarizing Key Points
The article highlights several key aspects of reverse logistics:
- Definition and Scope: Reverse logistics involves the processes that encompass the return, reuse, recycling, and disposal of products. Understanding this definition aids in recognizing its relevance in modern supply chains.
- Comparative Analysis: The differences between reverse logistics and traditional logistics emerge clearly, showcasing the unique challenges and benefits inherent in handling returned goods.
- Importance: The benefits of implementing reverse logistics—such as cost efficiency, enhanced customer satisfaction, and environmental considerations—are crucial for businesses aiming to remain competitive.
- Challenges: Issues like complex returns processes and data management problems reveal the obstacles organizations must overcome to successfully implement reverse logistics practices.
- Future Directions: The anticipated trends and global impacts present opportunities for innovation and adaptation as the supply chain landscape evolves.
"Effective reverse logistics not only aids in cost management but also improves the overall customer experience, reinforcing brand loyalty."
Implications for Future Research
Future research on reverse logistics should focus on several areas:
- Technological Advancements: Investigating how emerging technologies like artificial intelligence and data analytics can optimize reverse logistics processes is vital. Understanding their role can bring efficiency and improvement.
- Sustainability Metrics: Establishing clear metrics for evaluating the environmental impacts of reverse logistics practices can provide companies with guidance on how to enhance sustainability.
- Consumer Behavior Analysis: Delving into how consumer attitudes towards returns affect the efficiency of reverse logistics can yield insights into improving these processes.
- Global Best Practices: Analyzing different geographical implementations of reverse logistics may reveal innovative strategies and practices that contribute to success in various contexts.