Exploring Steel Blast Techniques in Industry
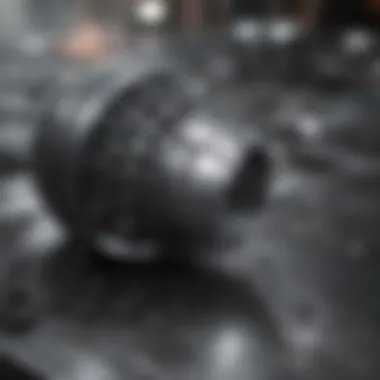
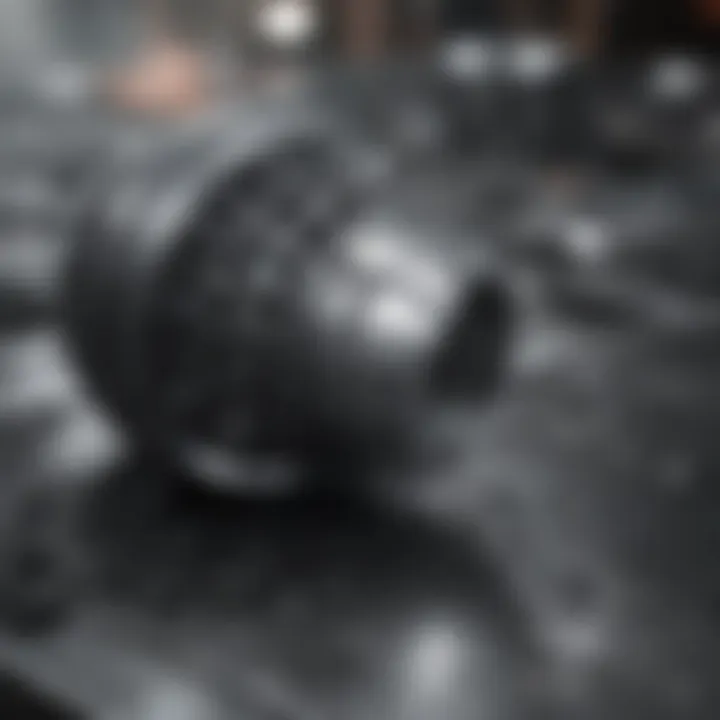
Intro
Steel blast techniques are an essential part of modern industrial practices. Their influence reaches far and wide, impacting everything from manufacturing to construction. At its core, this process involves using high-velocity particles to treat the surface of steel, enhancing its durability and appearance. The science behind these techniques isn't just about aesthetics; it fundamentally changes how materials perform under stress and environmental pressures.
Understanding the nuances of steel blast techniques can be a game changer for professionals in materials science and engineering. As industries strive for both efficiency and sustainability, the benefits of mastering these methods become clear. The following sections will peel back the layers of this versatile technology, revealing not only its practical applications but also the theories and principles that underpin effective execution.
By examining the various methodologies, material types, and safety protocols involved, readers will gain a comprehensive view of why steel blast techniques are a cornerstone in industrial enhancements.
Foreword to Steel Blast Techniques
The significance of steel blast techniques in industrial applications cannot be overstated. These methods are a cornerstone of surface preparation, playing a vital role in ensuring the integrity and durability of steel products across various sectors. While at first glance, one might see blasting as merely a way to clean surfaces, the reality is far richer and warrants a thorough exploration.
Steel blast techniques contribute significantly to improving product longevity. By effectively removing contaminants, such as rust, paint, and other debris, these techniques prepare the metal surface for subsequent treatments, including painting, coating, or welding. Failing to prepare steel surfaces adequately can result in premature failure, leading to costly repairs or compromised safety. Moreover, these processes can enhance adhesion for coatings, ultimately improving performance and aesthetics.
Defining Steel Blast
At its core, steel blasting refers to a method where abrasive materials are projected at high speed onto metal surfaces. This process aims to clean, smooth, or shape the surface of steel items. It's not just a simple cleaning; the mechanics of blasting can influence the structural properties of the metal itself. Different types of abrasives—like sand, steel shot, or garnet—can yield various surface finishes and levels of cleanliness. The choice of blasting technique also plays a role in determining the final quality of the treated steel.
Understanding the specific parameters—such as pressure, travel speed, and distance—of the blasting operation is essential to optimize efficiency and effectiveness. The intended outcome often dictates the combination of these factors, as they directly influence the surface roughness and functional properties capability of the steel parts post-blasting.
Historical Context
To appreciate the stature of steel blast techniques in current manufacturing, one must delve into their history. Blasting methods have evolved considerably since their early iterations. The inception of sandblasting can be traced back to the late 19th century when Benjamin Chew Tilghman patented the process. Initially used for cleaning and etching purposes, the technique soon found its way into various industries due to its effectiveness.
As technology advanced, the method became more sophisticated. By the mid-20th century, shot blasting emerged as a prominent player in the industry, utilizing steel shots instead of sand, thus providing a more effective and controlled cleaning method. This shift not only improved cleaning efficiency but also reduced environmental hazards associated with silica dust, which was a significant concern in earlier sandblasting practices. Today, various innovative techniques, including wet blasting and automated processes, continue to expand the capabilities and applications of steel blasting solutions.
Principles of Steel Blast Formation
Understanding the principles of steel blast formation is vital for grasping how these techniques enhance the quality and durability of surface materials. This section will provide insights into both the basic mechanics of blasting and the materials involved in these processes. The significance lies not just in learning the technical workings, but in appreciating how these methods improve industrial applications.
Basic Mechanics of Blasting
At its core, blasting techniques involve propelling materials at high speeds towards a surface, resulting in a carefully controlled impact. This impact achieves multiple objectives such as surface cleaning, shaping, and altering the physical properties of the material. Typically, the mechanics rely on the appropriate choice of medium, pressure levels, and applied angle.
- Energy Transfer: The energy from the propellant medium must be effectively transferred to the target surface. This transfer dictates how well the surface is prepared for subsequent processes, such as coating or welding.
- Impact Velocity: The speed at which the blasting medium strikes the surface is crucial. A higher impact velocity generally leads to effective cleaning and profiling, but factors must be balanced to prevent damage to the underlying substrate.
- Nozzle Design: Different nozzle designs can greatly influence the trajectory of the abrasive. A well-designed nozzle optimizes the distribution and velocity of particles, enhancing the efficiency of the blast process.
Blasting can vary significantly based on its intended outcome. Different applications may require different methodologies and equipment setups, showcasing the adaptable nature of blast techniques.
Materials Involved
The choice of materials used in blasting plays a pivotal role in determining the effectiveness of the process and the quality of the results. Here are some common materials:
- Abrasives: Common blasting materials include sand, steel shots, glass beads, and aluminum oxide. Each offers unique properties impacting the finish and characteristics of the blasted surface.
- Abrasive Size: The particle size directly affects the aggressiveness of the cleaning or finishing process. Larger particles can remove substantial amounts of material quickly, while smaller particles may provide a finer finish without significant substrate wear.
- Blasting Compound: The medium through which the abrasives are propelled, whether it’s air, water, or another fluid, can influence the efficiency and effectiveness of the blast. For instance, wet blasting uses water to dampen dust and can enhance surface finish.
"The optimal selection of materials is as paramount as the blasting technique itself; it's the combination that often leads to the desired outcome."
The synergy between the various materials and the mechanism of action exemplifies the complexity of steel blast techniques.
By paying close attention to these principles, industry professionals can not only ensure a high-quality surface but also optimize processes to enhance productivity and safety.
Types of Steel Blast Techniques
Understanding the various types of steel blast techniques is essential for anyone involved in the industrial sector. Each method has its unique characteristics, procedures, and advantages that cater to different applications. The choice of technique can significantly impact the quality of the surface, the efficiency of the operation, and even the cost-effectiveness of the process. Here’s a breakdown of the three main types utilized in industries today.
Sandblasting
Sandblasting, also known as abrasive blasting, is one of the most traditional and widely used techniques for surface preparation. It involves propelling a stream of sandy material against the surface of metal to remove impurities, rust, or old paint. The process is highly effective for achieving a clean substrate ready for subsequent treatments, such as painting or coating.
- Applications: Widely seen in automotive industries, shipbuilding, and restoration projects.
- Materials: Typically utilizes silica sand, although garnet, glass beads, and plastic media might be employed depending on the application.
- Benefits: The main advantage of sandblasting is its ability to reach recessed areas and intricate surfaces, making it ideal for both large and small components.
However, there are considerations. Sandblasting can produce harmful dust, leading to health hazards for operators if not performed with adequate safety measures. Therefore, protective equipment is paramount.
"Sandblasting is often a necessary step to ensure the longevity and quality of metal surfaces, but it comes with its own set of challenges that need careful management."
Shot Blasting
Shot blasting varies from sandblasting in that it employs a system of mechanical impellers to hurl metal shots at the surface of the part. This technique is mostly used for cleaning, deburring, and preparing surfaces where a more uniform finish is required.
- Applications: It’s commonly deployed in manufacturing plants, especially for automotive parts and other machinery components where precision is key.
- Materials: Steel shots or other metallic abrasives are predominantly used, chosen based on the desired finish and the material of the substrate being treated.
- Benefits: One notable advantage of shot blasting is that it maintains the mechanical properties of the metal, leading to an increased lifespan for treated parts. It is also less dusty than sandblasting, which contributes to a safer working environment.
This method is best suited for larger parts and those requiring a standardized surface treatment.
Wet Blasting
Wet blasting, an innovative alternative to traditional dry methods, involves mixing water with abrasive materials. This technique has gained traction due to its ability to minimize airborne dust and its enhanced cleaning properties.
- Applications: Often used in delicate machining processes, the aerospace industry, and situations where the integrity and cleanliness of the surface are paramount.
- Materials: Water mixed with abrasives like glass beads, silicon carbide, or aluminum oxide, adjusts the aggressiveness of the blast.
- Benefits: One significant advantage is its ability to achieve a smoother finish while minimizing wear on the substrate. Wet blasting also reduces the risk of oxidation and contamination of the treated surface, making it a preferred choice for sensitive applications.
Unlike other methods, it’s less abrasive, making it useful in scenarios where finishes must be immaculate.
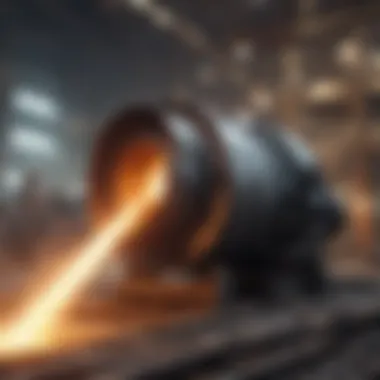
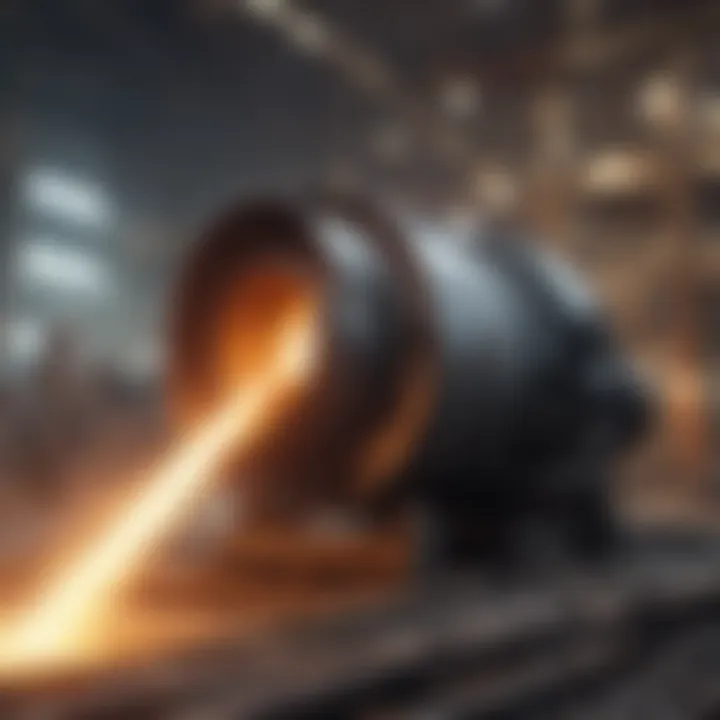
In summary, the choice between sandblasting, shot blasting, and wet blasting hinges on the requirements of the project at hand. Understanding the strengths and limitations of each technique is crucial for optimizing surface treatment processes and ensuring the desired results.
Applications of Steel Blast in Industry
Steel blast techniques play a crucial role in several industrial sectors, offering numerous benefits that enhance production efficiency and product quality. Their significance is underscored by their ability to prepare surfaces for subsequent treatments, improve the longevity of materials, and often reduce the environmental impact of industrial processes. The following sections detail the specific applications of these techniques in automotive manufacturing, construction, and aerospace engineering, showcasing how they contribute to industry standards.
Automotive Manufacturing
In the automotive sector, steel blast techniques are vital for ensuring both aesthetic quality and functional durability of automobile components. When car parts are blasted, they undergo a meticulous cleaning process that removes rust, old paint, and contaminants from the surface. This careful preparation is essential before applying coatings or paints, as it enhances adhesion and ensures a smoother finish.
Moreover, techniques such as shot blasting can provide parts with a uniform surface roughness, which not only improves the bonding of adhesives used in vehicle assembly but also contributes to a reduced coefficient of friction in moving parts.
- Key Benefits:
- Improved paint adhesion and finish quality
- Enhanced performance of mechanical parts
- Increased lifespan of automotive components
Ultimately, the use of steel blast techniques in automotive manufacturing can lead to significant cost savings and increased safety through improved component integrity.
Construction and Infrastructure
Within the construction and infrastructure industries, steel blast techniques hold paramount importance for maintaining the durability and reliability of structures. For steel frameworks, bridges, and other critical infrastructure, proper surface treatment is non-negotiable. Blasting ensures that the surfaces are free of debris and pollutants, which is often essential for ensuring that protective coatings effectively shield materials from corrosion.
In addition to rust removal, specific blasting techniques allow for the profiling of steel surfaces. This profiling increases the surface area for bonding, enhancing the strength of welds and connections crucial for the stability of structures.
- Considerations Include:
- Maintaining the structural integrity of materials
- Compliance with industry standards for safety
- Reducing the lifetime costs associated with corrosion
A significant aspect of using these techniques in construction is also the timeline of projects, which can be positively affected when surface preparation is expedited.
Aerospace Engineering
Aerospace engineering demands exceptionally high standards concerning both safety and performance. In this field, steel blast techniques are utilized in a variety of applications, from the preparation of frameworks for aircraft to the maintenance of engine components. The unique aspect of aerospace is that even the smallest flaws or surface irregularities can lead to catastrophic failures. Therefore, the precision offered by blasting methods is invaluable.
The application of steel blast techniques also aids in weight reduction by allowing for the removal of excess material without compromising the structural integrity of components. These methods also enhance the fatigue resistance of parts, which is especially critical in aerospace, where components are repeatedly subjected to stress during flight.
- Benefits for Aerospace:
- Ensures compliance with stringent safety regulations
- Enhances fatigue resistance and performance
- Enables lighter and more efficient designs
"In aerospace, where precision is key, the surface preparation provided by steel blasting techniques is a game changer that can determine the success of a mission."
As demonstrated in these key industries, steel blast techniques not only facilitate improved material properties but also create numerous performance efficiencies that are critical for modern manufacturing and construction.
Advantages of Steel Blast Techniques
The advantages of steel blast techniques cannot be overstated. In an era where industries strive for efficiency and quality, understanding the immense benefits derived from these techniques is essential for professionals in fields like manufacturing, construction, and engineering. By optimizing surface treatment processes, steel blast techniques present numerous advantages that not only assist in material preparation but also enhance overall performance and durability. Let’s delve deeper into some of these significant benefits.
Surface Preparation
One of the standout advantages of steel blast techniques lies in their profound impact on surface preparation. When steel surfaces are treated meticulously, they are rid of impurities such as rust, scale, and old paint. This is crucial for ensuring any subsequent coatings, whether paint or a protective layer, adhere properly. A clean surface significantly increases the longevity and effectiveness of these materials. During this process, tiny particles are propelled towards the surface at high velocity, rapidly stripping away unwanted elements.
The meticulous nature of this technique enables:
- Enhanced Adhesion: Proper surface preparation promotes better coating adhesion, reducing the risk of delamination or peeling.
- Uniform Surface Texture: A consistently prepared surface contributes to improved aesthetic and functional properties.
- Efficiency in Follow-Up Procedures: When surfaces are prepared correctly, it streamlines subsequent processes like painting or galvanization, ultimately saving time and resources.
In practical terms, various industries can see immediate benefits—automotive components experiencing longer-lasting paints, for example, or construction projects that require robust protection against the elements.
"Proper preparation is half the battle," as the saying goes. In steel blasting, it sets the stage for success.
Material Integrity and Longevity
Another fundamental advantage that warrants attention is the enhancement of material integrity and longevity. Steel blasting techniques not only serve as surface treatments but also play a crucial role in fortifying the material itself. By improving the surface characteristics, these techniques help in reducing the onset of corrosion and wear, extending the useful life of the steel components.
The ways in which steel blast techniques contribute to improved material integrity include:
- Stress Relief: High-energy impacts during blasting operations can relieve internal stresses in the metal, thus reducing the risk of failures during service.
- Improved Fatigue Resistance: Properly treated surfaces exhibit superior resistance to fatigue, making them ideal for high-stress applications such as aerospace or heavy machinery.
- Increased Resistance to Environmental Factors: Steel surfaces that have undergone blasting are often more resistant to moisture, chemicals, and extreme temperatures due to their refined surface profile and enhanced coatings.
Through these benefits, steel blast techniques prove invaluable across various sectors, notably in maintaining the quality and performance of critical components, which translates to cost savings over time. Understanding these advantages helps professionals in making informed decisions regarding material treatment options, leading to optimized project outcomes.
Challenges and Limitations
Understanding the challenges and limitations inherent in steel blast techniques is crucial for professionals and researchers. These facets not only highlight the complexities involved but also guide improvements and innovations in the industry. While steel blasting offers numerous benefits such as effective surface preparation and enhanced durability, it also carries risks and constraints that cannot be overlooked.
Health Hazards
Health hazards associated with steel blasting are significant and warrant careful attention. Workers involved in this process often face exposure to dust, noise, and even chemical agents used in some blasting materials. Silicosis, a respiratory condition caused by inhaling silica dust, often rears its head in situations where adequate ventilation and respiratory protection are not utilized. Furthermore, metal dust can present long-term health risks if proper safety protocols are not enforced.
Protective measures such as:

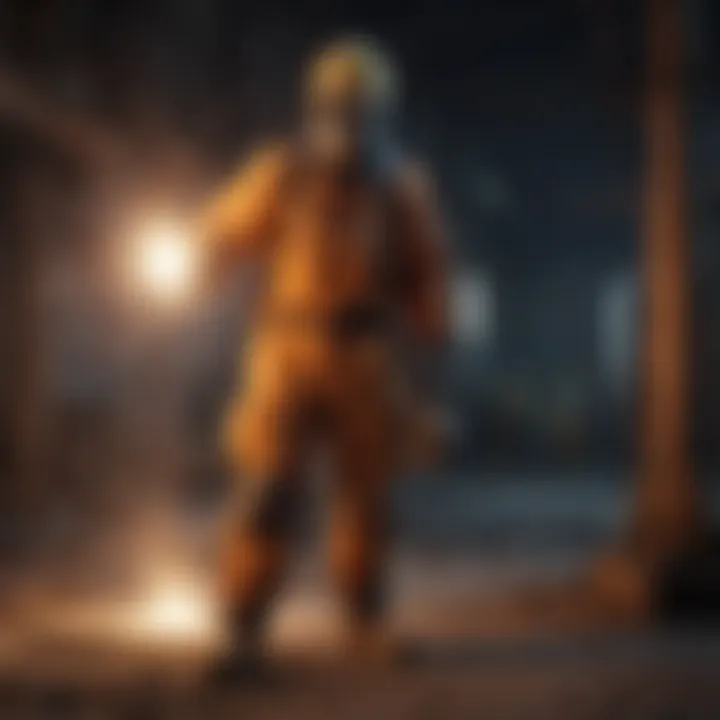
- Use of Personal Protective Equipment (PPE): Items like respirators, goggles, and protective clothing are essential in minimizing exposure.
- Implementing Ventilation Systems: Properly designed exhaust systems can help reduce airborne dust levels, creating a safer working environment.
- Regular Health Monitoring: Routine checks for workers can help catch any early signs of health issues, ensuring timely intervention.
"Safeguarding the workforce not only prevents health issues but also enhances productivity in the long run. It’s a win-win situation."
Equipment Limitations
While the equipment used in steel blasting has advanced over time, limitations still exist. Modern machines are often powerful, yet they can be susceptible to breakdowns and require significant upkeep, which can disrupt operations. For instance, older shot blast machines might not effectively maintain the required pressure and flow rates, leading to inefficient blasting.
Moreover, some equipment may not be suitable for all types of blasting materials. This is especially relevant in cases where industries require specific surface finishes or treatment levels. By understanding these constraints, companies can make informed decisions about equipment purchases and maintenance, which can save time and resources in the long run.
- High Initial Costs: The initial investment for advanced equipment often deters smaller companies from using highly effective blasting technologies.
- Training Needs: Employees need training not only to operate complex machinery but to maintain safety standards, which can increase operational overhead.
- Limited Versatility: Some blast equipment performs optimally under specific conditions, limiting its use to particular types of jobs or materials.
Realizing the challenges and limitations of steel blast techniques enables organizations to address these issues head-on, fostering a more safe and efficient work environment. In doing so, they can continue to leverage the advantages offered by steel blasting while calling attention to necessary improvements.
Safety Measures in Steel Blasting
Safety in steel blasting is a cornerstone of the industry, paramount to safeguarding the well-being of workers and ensuring consistent operational integrity. The task of blasting, while effective for surface preparation and cleaning, can pose various hazards. Therefore, the implementation of stringent safety measures is not just beneficial; it is essential. These measures encompass a range of protocols and equipment, highlighting the significant implications they have in both everyday operations and long-term health outcomes.
Protective Equipment
In the realm of steel blasting, personal protective equipment (PPE) acts as the first line of defense. This equipment is designed to shield workers from the multifaceted dangers that arise during blasting operations. Standard PPE items include:
- Respirators: To filter out harmful dust and contaminants generated during blasting.
- Safety goggles and face shields: Protecting eyes from projectiles and fine particles.
- Hearing protection: Since blasting can create high decibel levels, earmuffs or plugs are crucial.
- Heavy-duty gloves: To safeguard hands from abrasives and mechanical injuries.
- Steel-toed boots: Minimizing the risk of foot injuries caused by falling materials.
These measures go a long way in minimizing risks associated with steel blasting. Each piece of equipment must meet high safety standards to effectively protect workers. Additionally, proper training in the correct use of PPE enhances its effectiveness, making worker compliance an integral part of the safety equation.
"Failure to wear appropriate protective gear not only jeopardizes the individual but also compromises the overall safety culture of the workplace."
Regulatory Compliance
Regulatory compliance is another layer of safety in steel blasting operations that cannot be overlooked. Various agencies outline specific regulations that govern how blasting should be conducted. In the United States, for instance, the Occupational Safety and Health Administration (OSHA) and the Environmental Protection Agency (EPA) provide guidelines that companies must strictly follow. Key considerations include:
- Training and Certification: Workers need proper education about the hazards they face and how to mitigate them.
- Safe Storage of Materials: Hazards associated with the storage and handling of blasting materials must be managed effectively to prevent accidents.
- Environmental Protection: Blasting operations should comply with environmental regulations to safeguard air and water quality.
Non-compliance with these regulations can result in severe penalties and increased risk of accidents. Therefore, investment in compliance not only protects workers but also serves as a measure of corporate responsibility.
In summary, the combination of effective protective equipment and strict adherence to regulatory requirements forms the backbone of a safe steel blasting operation. Together, they ensure that the blasting practices industry remains as efficient as it is secure, paving the way for continued advancements in the field.
Environmental Impact of Steel Blast Techniques
The environmental footprint of steel blasting techniques is a growing area of concern, not just for regulatory agencies but also for industry players keen on sustainability. Understanding this impact is essential for anyone involved in materials science and engineering. As the world pivots towards more eco-friendly practices, the significance of addressing environmental considerations cannot be overstated. Here, we’ll dissect the nuances of waste management and pollution reduction strategies in steel blast methods, aiming for a more balanced approach to industrial processes.
Waste Management
Waste management within steel blasting involves the collection, treatment, and disposal of materials produced during the blasting process. Being mindful about how waste is handled can significantly mitigate its impact on the environment.
- Types of Waste: Steel blasting generates various wastes, including spent abrasives, hazardous dust, and chemical residues. Spent abrasives, such as steel grit, can often be recycled or repurposed.
- Recycling Opportunities: The recycling of materials not only reduces landfill waste but also supports the circular economy. For instance, reclaimed abrasives can be reused in subsequent blasting processes, diminishing the need for new raw materials. This not only saves costs but also lessens the extraction pressure on natural resources.
- Waste Treatment Technologies: Implementing advanced waste treatment systems is crucial. Technologies such as filtration and dust extraction systems can contain harmful particles, thereby ensuring they don't escape into the atmosphere. Effective filtration systems can capture up to 99% of particulate matter, making a significant difference.
By adopting meticulous waste management practices, companies can uphold their commitment to corporate social responsibility while aligning with global sustainability goals.
Pollution Reduction Strategies
The strategy to reduce pollution from steel blasting is multifaceted, integrating technological advancements and operational shifts.
- Air Quality Control: Steel blasting can release dust and particulate matter, thus directly impacting air quality. Utilizing wet blasting techniques can mitigate airborne pollutants by binding dust with water droplets, effectively reducing air emissions.
- Dust Suppression Systems: Installing automated dust suppression systems can help contain fugitive dust. These systems typically use water or chemical suppressants that capture dust particles before they can disperse into the environment. Regular maintenance of these systems is paramount to ensure their effectiveness.
- Monitoring Systems: Implementing real-time environmental monitoring systems can provide valuable data regarding emissions and pollutants. Continuous monitoring allows industries to remain compliant with environmental regulations, along with providing insights to improve their practices.
"Doing away with pollution caused by blasting not only preserves the environment but also enhances the overall quality of life for communities nearby."
In essence, to transform the environmental impact of steel blast techniques, a proactive approach toward both waste management and pollution reduction should be at the forefront. The aim should always be to sustain our environment while still achieving industrial goals.
Technological Innovations in Steel Blasting
In the domain of industrial steel treatment, the importance of technological innovations cannot be underestimated. As industries continue to seek ways to improve efficiency, reduce costs, and comply with environmental regulations, advancements in steel blasting techniques play a pivotal role. These innovations not only transform traditional approaches but also pave the way for more sustainable practices, ultimately benefiting both companies and the environment.
Automation of Processes
Automating processes in steel blasting has revolutionized the way operations function. Automation minimizes the need for manual intervention, allowing for consistency and precision that is hard to achieve through human efforts alone. With technology like robotics and advanced programming, it’s now feasible to implement automated systems that handle blasting tasks with remarkable accuracy. These systems can operate at increased speeds, maintaining high quality without compromising safety standards.
However, it's not just about speed; automation leads to significant cost reductions. By reducing labor requirements and minimizing human error, companies can save money while improving output. Some examples of automated blasting systems include the robot-operated shot blasters used in automotive manufacturing.
"Automation does not only follow industry trends; it leads them, ensuring that operations are kept at the cutting edge of efficiency and safety."
Enhancements in Efficiency
Efficiency remains a cornerstone of successful steel blasting operations. Technological enhancements have led to improved combinations of blasting media and techniques, ultimately allowing for quicker cycle times and reduced resource consumption. One noteworthy development is the use of advanced software that models blasting processes to optimize parameters such as pressure, media type, and angle of application. This software enables operators to predict outcomes and make adjustments in real-time, leading to optimal results.
Several enhancements have emerged in recent years:
- Eco-friendly Blast Media: Shifting toward biodegradable or recyclable media has made blasting not only more efficient but also significantly more environmentally friendly.
- Improved Dust Collection Systems: These systems allow for better air quality by capturing harmful particles, ensuring compliance with regulations while enhancing the work area atmosphere.
- Real-time Monitoring: Employing sensors for monitoring critical aspects of the blasting process leads to proactive adjustments and optimizations that enhance overall efficiency.
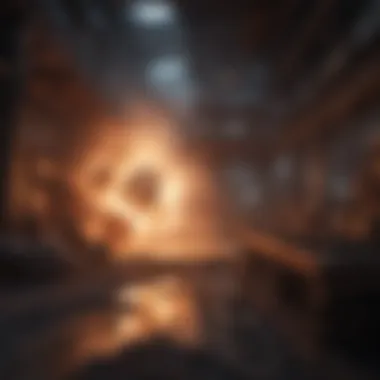
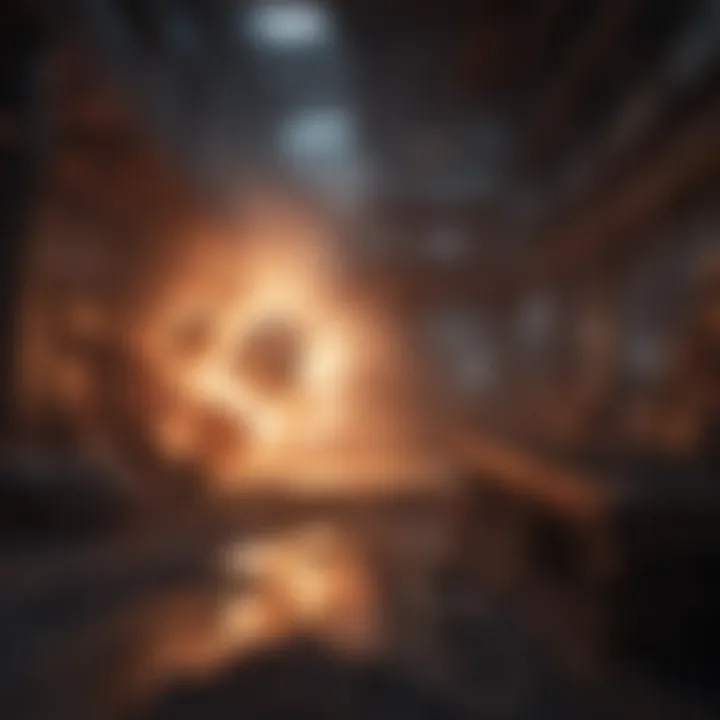
In summary, technological innovations in steel blasting are an essential part of modern industrial practices. Both automation of processes and enhancements in efficiency herald a new era that benefits manufacturers looking for cutting-edge solutions to stay competitive.
Future Trends in Steel Blast Technologies
In the world of steel blast techniques, staying ahead of the curve is paramount. Understanding the future trends in this domain not only informs current practices but also lays the groundwork for innovation and evolution within the industry. These emerging trends depict not just a direction, but a necessity for sustainability, efficiency, and adaptation to market demands.
Sustainability Practices
As the industries evolve, so too do the expectations surrounding environmental responsibility. Sustainability practices in steel blasting are no longer optional; they are a fundamental expectation. Directives like reducing waste, minimizing energy consumption, and employing eco-friendly materials should now dominate the conversation. For instance, using recycled abrasives can dramatically cut costs and reduce environmental footprints. Additionally, implementing water reclamation systems can preserve invaluable resources while ensuring operations remain compliant with regulatory demands.
It’s crucial to embrace technological advancements that facilitate these sustainable practices. Recycling systems, for example, have made it much easier to collect steel and other materials for reuse, effectively reducing the demand for new source materials.
"Sustainability is not just a buzzword; it is the future of all industrial applications."
Individuals and companies that prioritize sustainable practices find themselves reaping both environmental and economic benefits. Increased public consciousness about ecological issues can sometimes sway consumer choices, making sustainable options more appealing. This shift not only fosters goodwill amongst clients but often leads to long-term loyalty as well.
Emerging Market Dynamics
Simultaneously, the marketplace for steel blast technologies is undergoing a transformation influenced by new material needs, global competition, and advancements in automation. As industries such as automotive and aerospace face increasing pressure to innovate, the demand for more efficient, effective blasting techniques is paramount.
The emergence of new players in developing countries alters the competitive landscape, resulting in an increased focus on cost-effective solutions without compromising quality. With global supply chains becoming more intricate, understanding and adapting to these dynamics can be the differentiating factor between success and failure.
Furthermore, the rise of smart technologies cannot be ignored. Industries are beginning to implement Internet of Things (IoT) features in their blasting operations, allowing for real-time data tracking, performance monitoring, and predictive maintenance. This not only saves time and costs but empowers workers to manage operations with utmost effectiveness.
Finale
The conclusion of this article emphasizes the critical role that steel blast techniques play in modern industrial applications. These methods not only enhance the quality and longevity of metal surfaces but also streamline production processes across various sectors. As industries continue to evolve, understanding the intricacies of steel blasting becomes increasingly significant.
From automotive manufacturing to aerospace engineering, the applications of these techniques are vast. Properly implemented, these methods can significantly improve efficiency, reduce costs, and enhance sustainability. Companies that prioritize these processes often find themselves a step ahead in the competitive marketplace.
Moreover, advancements in technology, such as automation and pollution reduction strategies, show great promise for the future. Industries must keep pace with these innovations to maintain safety standards, meet regulatory compliance, and address environmental concerns. As the world shifts towards more sustainable practices, steel blast techniques must also adapt to ensure they align with these new priorities.
Summary of Insights
Through the examination of steel blast techniques, several key insights emerge:
- Efficiency Gains: The application of automated steel blasting can significantly reduce labor costs and time.
- Safety Protocols: Strict adherence to safety measures protects workers and minimizes health risks associated with blasting.
- Environmental Concerns: Managing waste and reducing emissions is crucial in today’s environmentally-conscious landscape.
- Technological Integration: Leveraging modern technologies can augment the effectiveness of traditional steel blast methods, ensuring higher quality outcomes.
These insights not only enrich our understanding of the topic but also serve as a guide for the practical application of these techniques in various industrial contexts.
Implications for Research and Industry
The implications of our findings extend beyond just immediate applications.
- Researchers are encouraged to explore further innovations tied to steel blast techniques, particularly in areas like nano-coatings and sustainable materials.
- Industries need to consider the long-term impacts of their blasting techniques on both product quality and the environment.
- Collaboration between academic institutions and industrial partners can foster innovative developments and solutions to current challenges.
- Continuous education and training for professionals in the field will be necessary to navigate the ever-changing landscape of steel blast technology.
In summary, while steel blast techniques are entrenched in industry, they are far from static. The framework laid out in this article serves as a stepping stone for further exploration and adaptation, paving the way for future advancements that are both efficient and responsible.
References and Further Reading
An insightful exploration of steel blast techniques benefits significantly from a solid foundation of references and further reading. Diving into the existing body of work allows readers to gauge the depth of knowledge in the field and discover valuable resources that can sharpen their understanding. The significance of this section cannot be overstated— it serves not only as a pathway for deeper exploration but also as a validation of the details presented throughout the article.
In the fast-evolving world of industrial applications, staying abreast of the latest findings is vital. Each new study or publication adds a layer of comprehension, whether it's refining procedures, enhancing safety protocols, or identifying novel materials. These resources often present firsthand accounts of experiments and case studies that shed light on real-world applications.
When approaching references, it’s essential to consider:
- Breadth and Scope: Comprehensive texts can offer diverse perspectives, from foundational principles to advanced methodologies.
- Recent Findings: Up-to-date studies keep practitioners aligned with industry innovations and regulatory changes.
- Critical Reviews: Articles that synthesize multiple research outcomes provide clarity on prevailing trends and intersections of knowledge.
Notably, one key benefit of diving into references is the opportunity to link empirical knowledge with theoretical frameworks, fostering a deeper appreciation for the mechanics at play within steel blast techniques. Readers can expect to discover not only what works best but also why those techniques have evolved to their current stature.
"Knowledge is not simply what you know; it’s how you apply that knowledge to new challenges."
Key Texts in Steel Blast Techniques
To further understand the dynamics of steel blast techniques, engaging with foundational texts is paramount. Influential works often serve as bedrock upon which subsequent studies build. Some key texts include:
- "Principles of Blast Cleaning" by J.D. Smith: This book outlines basic and advanced blasting principles, ensuring a holistic understanding of various techniques.
- "Industrial Applications of Steel Blast Techniques" by L. Wang: A useful reference for connecting theoretical knowledge with practical applications in various industries, from automotive to aerospace.
- "Sustainable Practices in Material Treatment" by R. Patel: This text illustrates the critical intersection of steel blasting and environmental considerations.
These books not only present methodologies but also discuss industry standards, safety measures, and emerging technologies relevant to steel blasting.
Recent Studies and Publications
Recent studies significantly contribute to the continual development of best practices in steel blast techniques. Current articles and publications highlight key advancements, such as improved material formulations for blasting agents and novel equipment designs that enhance efficiency and safety.
Some notable sources of recent studies include:
- Journal of Materials Science: Regularly publishes articles about new materials and techniques in steel surface treatment.
- International Journal of Abrasive Technology: Focuses on technical papers that provide insights into recent advancements in blasting technology.
- Conferences on Steel Processing: These events often yield proceedings that discuss cutting-edge research and applications, allowing those in the field to exchange knowledge.
By diving into these recent publications, professionals can keep pace with innovations and make informed decisions regarding techniques and equipment in steel blast applications.
In summary, references and further reading are instrumental to mastering steel blast techniques. They equip students, researchers, educators, and professionals with a comprehensive toolkit to navigate the complexities and advancements in this evolving field.
For more information, you can check out: