Precision Metrology: Principles and Applications
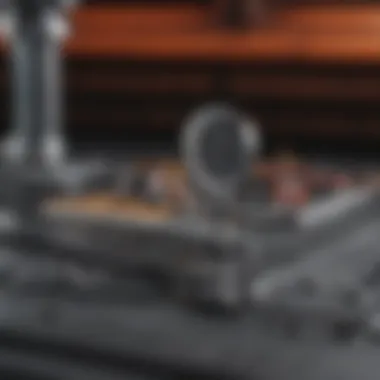
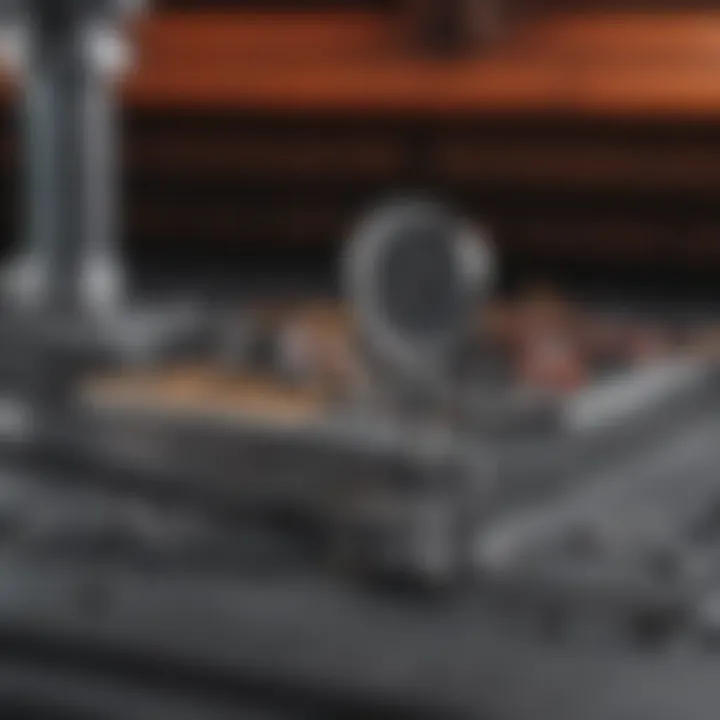
Research Context
Background Information
Precision metrology is not just a niche field; it underpins the foundations of various industries. From the bustling floors of manufacturing plants to laboratories where groundbreaking research takes place, the accuracy of measurements can dictate success or failure. The term metrology refers to the science of measurement, rooted deeply in both physical and mathematical principles. It involves the selection of suitable methodologies and instruments, ensuring that every measurement counts. With advancements in technology, we are now equipped with smarter tools that aid in achieving high precision. This field has evolved significantly over the decades, shaped by the need for more reliable data in everything from the production of microchips to aerospace engineering.
Importance of the Study
Understanding precision metrology unlocks insights into how quality is maintained across different sectors. The ongoing strive for higher standards often hinges on precise measurement. In engineering, for instance, the tolerances for components are extremely tight. A slight miscalculation can compromise safety and functionality. Moreover, in scientific research, accurate measurements provide the underpinning for theories and experimentation. Every data point is pivotal. As the demands for innovation increase, so does the importance of precise metrology. It not only facilitates consistency but drives the push towards more sophisticated technologies, ensuring that today’s breakthroughs translate to practical applications tomorrow.
“Accuracy paves the path to repeatability, and therein lies the power of precision.”
Discussion
Interpretation of Results
The results derived from precise measurements often exceed mere numbers; they provide actionable insights. For instance, in quality assurance processes, the use of precision instruments can significantly reduce product defects. When a factory implements a rigorous metrology process, the overall waste decreases, leading to cost savings. This practical implication demonstrates how precision instruments contribute to a company's bottom line.
Comparison with Previous Research
Historically, metrology faced challenges related to the limitations of technology—tools could only measure to a certain degree of accuracy. Recent advancements have seen technology leapfrog through rapid innovations. Today, instruments can measure dimensions at a microscopic level, far surpassing the capabilities of earlier devices. Studies show that the integration of techniques like laser interferometry has not only improved measurement accuracy but also expanded the applications of metrology in areas like nanotechnology and bioengineering. By comparing past methodologies with contemporary practices, it becomes clear that the evolution of precision metrology is a hallmark of progress in numerous scientific fields.
Prolusion to Precision Metrology
The field of precision metrology plays a vital role in a range of industries and scientific disciplines, where the accuracy of measurement can make the difference between success and failure. Understanding how precision metrology functions is essential for professionals and researchers alike, allowing them to recognize its significance in ensuring quality, efficacy, and reliability across various applications. At its core, precision metrology is focused on achieving the lowest measurement uncertainty possible, embodying both quantitative and qualitative understandings of measurements.
Defining Precision Metrology
So what exactly is precision metrology? In simple terms, it is the science of measurement, specifically dealing with the precision and accuracy of these measurements. It involves using specialized techniques to ensure that every parameter—from length to mass—is measured as accurately as possible. This precision is crucial not just for industry but also for scientific inquiry, where even minor errors can lead to substantial misinterpretations of data.
Precision metrology deals with three main components: the definition of measurement standards, the methods used to obtain those measurements, and the instruments employed therein. Essentially, these elements create a framework within which the quality of measurements can be consistently maintained.
Historical Context of Measurement Science
The journey of measurement science is a fascinating one, tracing back to ancient civilizations that relied on rudimentary forms of measurement, such as body parts or the lengths of ropes. As societies evolved, so did the methods of measurement, with the advent of standardized units—think of the meter that French scientists introduced during the French Revolution.
The history of precision metrology is marked by significant milestones. For instance, the introduction of the metric system in the late 18th century revolutionized the way measurements were standardized across Europe and later the world. It laid the groundwork for future advancements by establishing a universal language of measurement. Furthermore, the development of the international yard and pound system made measurements more consistent and reproducible.
As we delve into the past, it is also noteworthy to mention the influence of renowned scientists such as Galileo and Newton, who laid foundational principles that would guide measurements in various disciplines. Their findings not only shaped physics but also opened doors for more precise measurement in fields like astronomy and engineering.
With ongoing advancements in technology, precision metrology continues to evolve, embracing new methodologies and tools. However, these modern advancements build on the rich legacy of historical measurement practices, reminding us that while technology may change, the core objective of precision remains timeless.
"Precision metrology is not just about tools; it's about understanding the scientific principles that govern measurement itself."
Now that we've set the stage with a clear definition and explored its historical roots, we can further investigate the importance of accurate measurement and its profound impact on various fields.
The Importance of Accurate Measurement
Accurate measurement constitutes the bedrock of precision metrology and is fundamental in diverse fields, including engineering, manufacturing, and scientific research. Its importance cannot be overstated, as inaccuracies can lead to significant errors, financial losses, and safety risks. When it comes to crafting high-performance products or conducting thorough scientific investigations, every minute measurement counts. There are several specific elements that underline the significance of accuracy in measurement, and understanding these can shed light on its broader implications.
Impact on Engineering and Manufacturing
In the arena of engineering and manufacturing, precision is the name of the game. Whether designing a sleek aircraft or a small electronic device, engineers rely heavily on precise measurements. A misstep in gauging tolerances can result in parts that don’t fit together, leading to inefficient production or, worse, catastrophic failures.
To provide a clearer picture, consider the following aspects that showcase this impact:
- Component Integration: In multi-part assemblies, each component’s dimensions must be accurate to ensure a proper fit. A discrepancy as small as a few micrometers can generate assembly issues down the line.
- Quality Control: Manufacturing processes involve strict guidelines to maintain quality. Measurements ensure that products meet required specifications and perform reliably under varied conditions.
- Cost Efficiency: Precision reduces waste and rework. For instance, if a part is measured inaccurately, it may need to be scrapped or re-manufactured, incurring additional costs.
In summary, accurate measurement in engineering and manufacturing ensures that products are not only built correctly but also function as intended across their lifespan.
Role in Scientific Research
In scientific research, accuracy in measurement is equally pivotal. Researchers operate within a realm that demands both precision and repeatability. The efficacy of experimental results hinges on how well measurements can be trusted; inaccurate data can lead to erroneous conclusions that skew understanding.
Key considerations include:
- Data Integrity: High stakes are involved when collecting data for experimental analysis. Errant measurements can lead to a domino effect, misguiding future research or applications based on flawed findings.
- Replication of Results: The scientific method relies on others being able to replicate experiments. If measurements lack precision, replication might yield conflicting results, undermining the credibility of the original study.
- Technological Innovation: As technology becomes more complex, the precision needed in measurements increases. Groundbreaking fields such as genomics and nanotechnology are examples where measurement precision plays a central role in advancing knowledge and applications.
“In science, the precision of our tools determines the boundaries of our understanding.”
Fundamental Principles of Metrology
In precision metrology, understanding the fundamental principles is crucial. This foundational knowledge ensures that measurements are not just numbers on a screen but reflect reality with great accuracy. As we delve into these principles, we discover that precision metrology goes beyond mere measurement; it shapes industries, drives innovation, and ensures quality across various domains.
Measurement Uncertainty
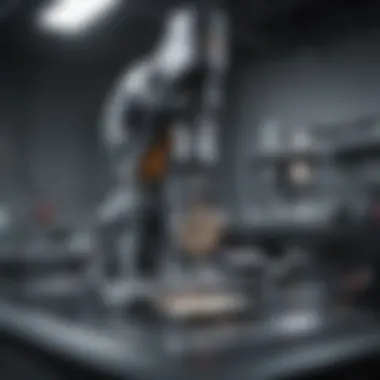
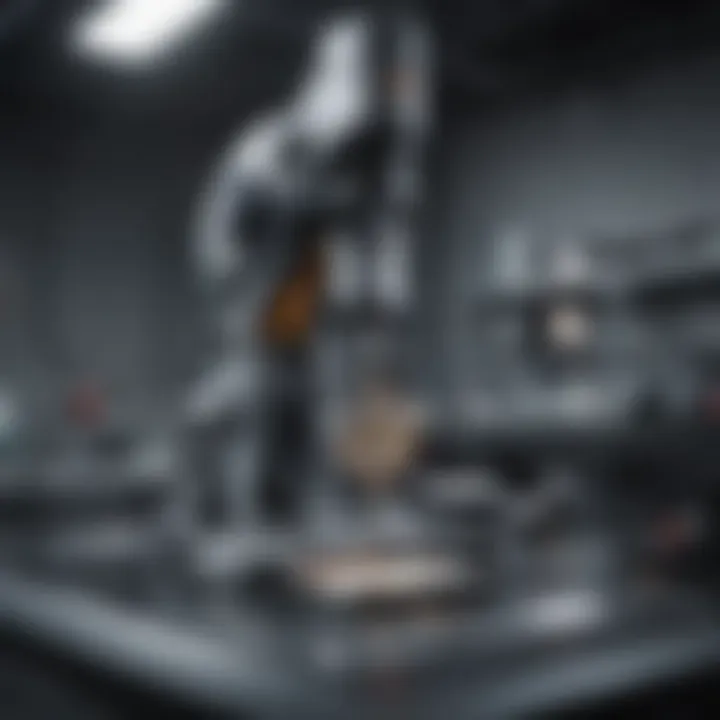
At the heart of metrology is measurement uncertainty, which essentially quantifies the doubt about the result of a measurement. It’s not just about getting a number; it’s about understanding how reliable that number is. Factors contributing to uncertainty are numerous—ranging from environmental conditions, instrument calibration, and even the skill of the operator.
One significant aspect of measurement uncertainty is its impact on decision making. For instance, in a manufacturing setting, if the uncertainty in the measurements is not well understood, it can lead to defective products, resulting in costly recalls and reputational damage. Thus, recognizing the uncertainty can help in setting quality benchmarks and in the implementation of effective quality control measures. Additionally, industries often employ statistical methods to analyze and manage uncertainty, ensuring that the confidence in results is maintained. It’s this careful balancing act that makes metrology a disciplined science rather than just a practical application.
Calibration Standards
Another pillar of precision metrology is calibration standards, which serve as the yardsticks against which measurements are made. Calibration is essentially the process of comparing a measurement instrument’s output with a standard of known accuracy. This process is pivotal across various fields, such as aerospace or health care, where even the minutest deviation could have dire consequences.
Calibration standards ensure that measurements are consistent over time and across different instruments. They also help standardize measurements globally, paving the way for international trade and communication. For example, consider a company manufacturing precision components that need to meet specific safety regulations. Without calibration, there can be discrepancies between the measurements of different machines or even different laboratories, leading to catastrophic failure in real-world applications.
In essence, a robust calibration system minimizes errors and reinforces trust in measurement results. Adopting proper procedures for calibration and understanding the implications of these standards is not only beneficial but necessary for producing high-quality outcomes in precision metrology.
"Inaccurate measurement is a recipe for failure. Standards and procedures can forge success from uncertainty."
The interaction between measurement uncertainty and calibration standards forms the cornerstone of precision metrology. By addressing these principles, professionals, researchers, and students not only deepen their comprehension of metrology but also develop a critical lens to evaluate and improve measurement practices in their respective fields. Understanding these principles allows for a more rigorous approach to measurement, ensuring that every count matters and that precision is not just a goal but a guarantee.
Measurement Techniques in Precision Metrology
In the realm of precision metrology, the choice of measurement technique can significantly shape the accuracy and reliability of the data gathered. Understanding these techniques is essential for researchers, engineers, and students alike, as they lay the groundwork for ensuring precision in a variety of applications. The efficacy of any measurement system can hinge upon how well these techniques are implemented.
Precision metrology is often regarded as the backbone of various industries. The reason for this can be boiled down to two critical factors: accuracy and repeatability. When a technique is properly employed, it produces measurements that consistently reflect reality, driving quality improvements and fostering innovations. Thus, the techniques used not only impact immediate results but can also influence long-term processes and product developments, highlighting their importance in metrology’s broader context.
Contact Measurement Methods
Contact measurement methods are perhaps the most traditional approach in the sphere of precision metrology. Here, measuring instruments physically interact with the object being measured. This can involve tools like calipers and micrometers, which apply direct pressure to the object to ascertain its dimensions. Such methods provide a direct and tangible touchpoint that can be extremely beneficial in specific scenarios.
The advantage of contact methods lies in their simplicity and effectiveness. For instance, they are often more cost-effective compared to advanced non-contact technologies, making them more accessible for smaller enterprises or research institutions. Calipers can accurately measure thickness and depth, while micrometers excel in measuring small gaps and diameters.
However, there are considerations to keep in mind. Pressure applied through contact might induce deformations in delicate materials, leading to inaccuracies. Also, these methods may not be suitable for intricate processing tasks or in situations requiring high-speed measurements, particularly in automated settings.
"While contact methods have their merits, they are not always the holy grail of precision. Their limitations can sometimes outweigh the advantages, depending on the context of use."
Non-Contact Measurement Methods
As technology progresses, non-contact measurement methods are gaining traction in precision metrology. These techniques are characterized by their capability to acquire data without physical interaction with the object. Technologies like laser scanning and optical measurement systems fall under this umbrella.
One of the standout features of non-contact techniques is their capability to measure a wide array of surfaces and shapes without compromising the integrity of the material. Laser scanners, for example, allow for high-speed measurements of complex geometries, making them ideal in industries such as aerospace and automotive where precision is non-negotiable.
Moreover, non-contact methods present a considerable advantage in terms of versatility. They can adaptively measure at various distances and can easily accommodate branching measurements without needing to reposition the object.
Yet, these methods also have their challenges. Calibration procedures can be more complex and costly, particularly for high-end optical systems. Moreover, environmental factors can influence measurements, such as ambient light levels and surface reflectivity, thus introducing potential errors.
In summary, understanding these measurement techniques is pivotal for anyone involved in precision metrology. Balancing the benefits and considerations of both contact and non-contact methods equips professionals to choose the most suitable approach based on specific needs and contexts. Accurate choices pave the way for innovation while ensuring that quality standards remain high.
Tools and Equipment in Precision Metrology
In the realm of precision metrology, the tools and equipment utilized serve as the backbone for accurate measurement processes. The integrity of measurement results relies heavily on the quality of these instruments. They not only enhance the precision of measurements but also streamline workflows across various industries. Understanding the specifics, benefits, and unique considerations of these tools is imperative for anyone involved in metrology, whether in engineering, manufacturing, or scientific research.
Calipers and Micrometers
Calipers and micrometers are among the most ubiquitous tools in precision metrology. They provide the means to measure dimensions such as thickness, diameter, and depth with remarkable accuracy.
- Calipers typically come in two main types: vernier and digital. The vernier caliper, with its sliding scale, allows users to read measurements between the metric and imperial scales. On the other hand, digital calipers offer easy readability and can switch between metric and imperial units at the touch of a button.
- Micrometers, though resembling calipers, are designed for even finer measurements. They generally measure dimensions down to a thousandth of a millimeter, making them essential in fields where precision is paramount.
The versatility of these tools makes them suitable for a wide array of applications, from crafting intricate components in aerospace design to quality control in automotive parts production. Proper calibration remains critical for both calipers and micrometers to ensure consistent and reliable results.
Coordinate Measuring Machines ()
Coordinate Measuring Machines stand at the forefront of modern metrology. Equipped with probes and software, CMMs can capture the exact dimensions of physical objects in three-dimensional space.
- Types of CMMs include mechanical, optical, laser, and white light machines. Each type employs a different method for measurement, thus offering flexibility depending on the specific needs of the measurement task.
- A significant advantage of CMMs is their ability to automate measurements. This reduces the risk of human error and enhances efficiency, particularly in repetitive tasks common in manufacturing.
Furthermore, the CMM’s capability for combining measurement data with CAD systems has transformed how industries approach design and quality assurance. Data obtained can be readily analyzed and compared against predetermined specifications, making these machines indispensable in modern quality control practices.
Optical Measurement Systems
Optical measurement systems utilize light to gather dimensional information without direct contact with the object, which can be a game-changer in certain scenarios. These systems are particularly useful for fragile components or those that require high-speed measurement processes.
- Common types of optical systems include laser scanners and vision-based measurement systems. Laser scanning technology can produce detailed 3D models, while vision systems typically work with cameras and advanced software to extract measurements from images.
- One of the primary benefits of optical measurement systems is their speed of operation. Numerous measurements can be taken in a short span, making them ideal for high-volume production contexts.
However, it’s essential to understand the limitations, such as the surface finish of the material being measured, which can affect accuracy. Care must be taken when selecting an optical system depending on the specific measurement requirements.
"Precision metrology equips industries not merely with numbers but with the means to innovate and maintain quality. Every tool plays its unique role toward an end goal of accuracy and reliability."
Applications of Precision Metrology
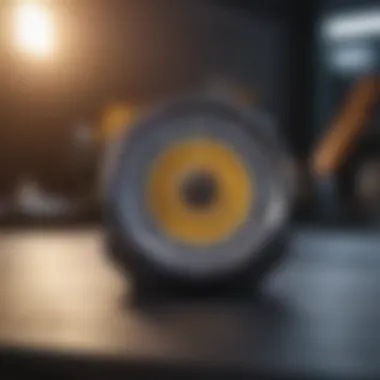
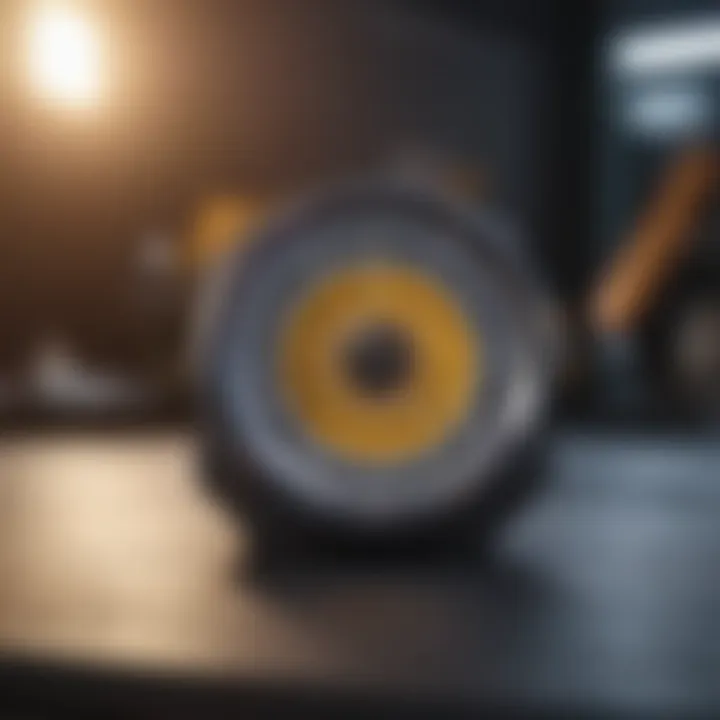
Precision metrology plays a pivotal role across various industry sectors, ensuring that measurements are not just a matter of convenience but are instead critical for functionality and compliance. By accurately gauging parameters, an organization can significantly enhance product quality, guarantee safety, and streamline operations. Whether it’s the fine-tuning of aerospace components or the minute measurements vital in electronics, precision metrology is integral to modern engineering.
Metrology in Aerospace
In the aerospace sector, precision is not just desirable – it is non-negotiable. The safety of flights hinges on the meticulous measurements of parts and systems. Aircraft components undergo stringent testing; even the tiniest error could have catastrophic outcomes. For example, turbine blades, which operate under intense conditions, are measured with utmost precision using tools like Coordinate Measuring Machines (CMM) and laser-based systems. Such technology allows engineers to monitor dimensions down to micrometers.
Benefits of Precision Metrology in Aerospace:
- Enhanced Safety: Accurate measurements ensure that all components perform as designed, minimizing risks during operation.
- Regulatory Compliance: Aerospace products must adhere to rigorous standards, making precise metrology a necessity in meeting certifications.
- Cost Efficiency: By reducing errors, companies cut costs associated with rework and non-conformance.
"In aerospace, even the smallest margin of error can mean the difference between safety and disaster."
Metrology in Automotive Industries
The automotive industry also leans heavily on precision metrology, as it underlies quality control processes from design to production. As vehicles increasingly incorporate complex electronic systems alongside traditional mechanical components, the stakes of precise measurement have risen. For example, during the assembly of vehicles, elements such as chassis alignment and engine fitment require detailed measurements to ensure optimal performance.
Key Applications:
- Assembly Line Verification: Ensuring that every part fits perfectly without gaps or malfunctions.
- Performance Testing: Measurements taken during prototype testing help refine specifications and improve vehicle performance.
- Quality Assurance: Creating a consistent output quality by maintaining standards across mass production.
Metrology in Electronics Manufacturing
The electronics sector thrives on precision metrology for both production and testing phases. As devices become smaller and more intricate, the requirement for superior measurement techniques has escalated. Semiconductor fabrication is one area where metrology is critical; here, the dimensions of waveguides can be smaller than the width of a human hair. Advanced systems like optical measurement technologies are utilized to gauge these minuscule features with exquisite accuracy.
Advantages of Precision Metrology in Electronics Manufacturing:
- Yield Improvement: Higher precision measurements lead to greater manufacturing efficiency and lesser product waste.
- Innovative Design Capability: Precision in measurement supports the development of novel designs that push the boundaries of what technology can achieve.
- Global Competitiveness: Companies that utilize precision metrology can better compete in a market that demands high-quality electronics.
The importance of precision metrology cannot be overlooked; it provides the backbone for quality, safety, and innovation across multiple industries. Each application showcases its critical need, reinforcing the essential skills necessary in the fields of engineering and manufacturing.
Technological Advancements in Metrology
In the fast-paced world of metrology, technological advancements are not just trends; they’re fundamental shifts shaping how measurements are conducted today. These innovations not only enhance the precision of measurements but also streamline processes, making them more efficient and accessible. The role of these advancements cannot be overstated, as they impact various sectors significantly, including manufacturing, aerospace, and electronics.
Evolution of Sensor Technologies
The heart of modern metrology lies in sensor technology. These devices, capable of detecting and measuring physical phenomena, have progressed leaps and bounds over the years. Initially, sensors were relatively simple and often limited in application. However, with developments in materials science and engineering, we now have sensors that are small, robust, and highly sensitive.
For example, consider the rise of microelectromechanical systems (MEMS). These miniaturized devices allow for incredibly precise measurements, often within nanometer ranges. The applications are vast, from monitoring environmental conditions to integrated circuits in electronics. Moreover, they come equipped with the capability to collect real-time data, which is crucial for industries that rely on immediate response mechanisms.
The benefits of advanced sensor technologies include:
- Increased Precision: Higher accuracy ensures that errors are minimized.
- Real-time Monitoring: Continuous data collection enables immediate intervention when anomalies arise, enhancing system reliability.
- Miniaturization: Compact designs make them easier to integrate into various systems without compromising performance.
Integration of Artificial Intelligence
Artificial Intelligence (AI) is increasingly making its mark within precision metrology, transforming how data is handled and analyzed. The synergy between AI and metrology leads to powerful insights that were previously difficult to obtain. By employing machine learning algorithms, metrology systems can now learn from past measurements and improve their predictive capabilities.
AI assists in:
- Data Analysis: It can process vast amounts of measurement data quickly, identifying patterns and anomalies with remarkable speed.
- Predictive Maintenance: AI can forecast when equipment is likely to malfunction based on previous performance data, helping to evade costly downtimes.
- Enhanced Measurement Techniques: With AI, even complex measurement challenges can be tackled more efficiently, enhancing the scope of what can be accurately measured.
The integration of AI into precision metrology is not without its challenges. However, the potential gains from this technology push many industries to explore how they can incorporate AI effectively into their measurement processes.
"The marriage of sensor technology and artificial intelligence revolutionizes our understanding and application of precision metrology, laying the groundwork for future innovations."
As the landscape continues to evolve, it’s clear that understanding these technological advancements provides critical insight into the future of metrology, paving the way for continued precision and efficiency in various fields.
Quality Assurance and Metrology
In the discipline of precision metrology, quality assurance stands as a pillar of effectiveness and reliability. It ensures that products meet stringent specifications and standards, ultimately securing customer satisfaction and safety. Accurate measurements, after all, are the building blocks of successful engineering, manufacturing, and research. This section will outline the significance of quality assurance in metrology, providing insights into the underlying protocols and guidelines that govern this critical field.
Standards and Protocols in Quality Control
Quality control in metrology is not merely a procedural formality; it is a necessary practice that dictates the reliability of measurements and instruments utilized throughout various industries. The backbone of any quality control system resides in its standards and protocols. These guidelines, often determined by national and international bodies such as the International Organization for Standardization (ISO) or the American National Standards Institute (ANSI), lay the foundation for consistent and uniform practices.
To maintain these standards, numerous methods are employed, including:
- Calibration: Regularly ensuring that measuring equipment provides accurate readings.
- Procedures: Established standards dictate the steps necessary for testing, measuring, and documenting results.
- Documentation: Keeping records of measurements and equipment performance which help in auditing and traceability.
Each of these elements contributes to a transparent quality assurance process that reinforces trust in both the findings and the products derived from precision metrology. In essence, the application of these protocols mitigates risk and bolsters quality against the backdrop of increasing global manufacturing competition.
Metrology’s Role in Product Certification
Product certification relies heavily on the principles of metrology. In many industries, particularly those heavily regulated such as aerospace and healthcare, certification signifies that products comply with legal and performance standards. This process involves thorough examination and testing, where metrology provides the tools necessary to validate claims about a product’s quality and efficacy.
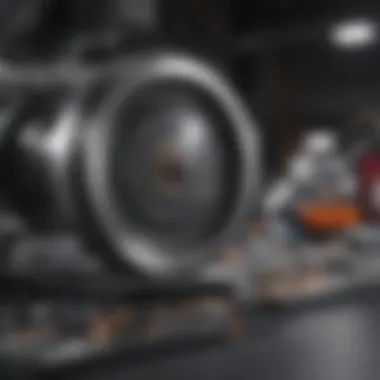
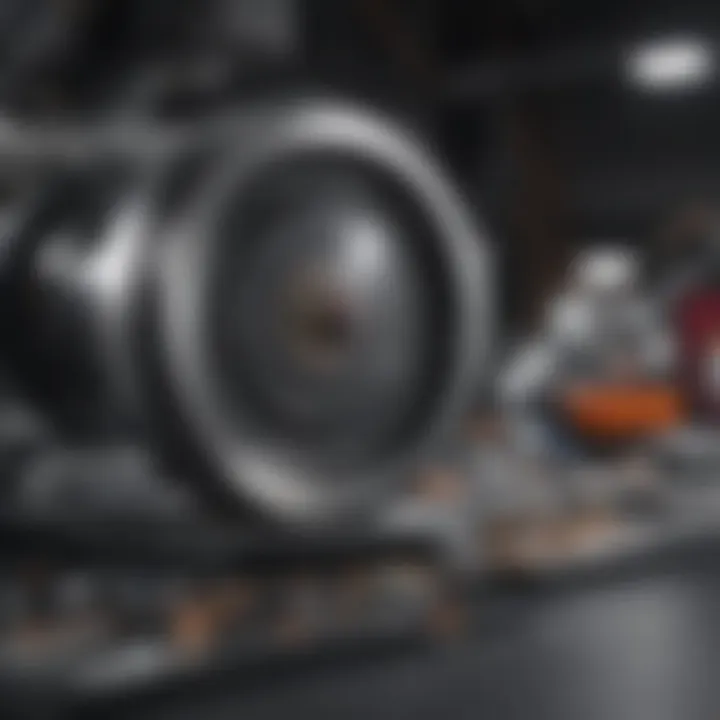
The role of metrology in product certification can be summarized in several key areas:
- Verification of Compliance: Metrology ensures products meet specified dimensional and operational requirements before entering the market.
- Safety Assurance: By assessing attributes like sizes, weights, and tolerances, metrology plays a vital role in ensuring that products are safe for consumer use.
- Market Confidence: Through proper certification processes, stakeholders can have confidence that products are reliable and of high quality.
"Without metrology, product certification would be akin to sailing without a compass—unpredictable and fraught with unexpected outcomes."
Challenges in Precision Metrology
Precision metrology is not without its hurdles. As technologies accelerate and fields of application broaden, practitioners find themselves navigating a complex landscape. The significance of addressing these issues cannot be overstated, as they play a crucial role in ensuring accuracy and reliability in measurements, which are foundational to various sectors including engineering, manufacturing, and scientific research.
Addressing Measurement Uncertainties
One of the most pressing challenges in precision metrology is measurement uncertainty. This phenomenon refers to the doubt that exists regarding the result of a measurement. Any measurement can be viewed as a dance between reality and the tools we use to capture it. Since no measurement can be perfectly accurate, understanding this uncertainty is vital.
"In measurement science, knowing the limits of our tools can be as important as the measurements themselves."
There are several factors that can influence measurement uncertainty, such as:
- Environmental conditions, like temperature and humidity
- Instrumentation errors
- Calibration discrepancies
- Human factors, including operator bias
Addressing these uncertainties entails rigorous calibration and continuous monitoring of measurement processes. Metrologists often utilize statistical methods to characterize and quantify uncertainty. Techniques such as the Monte Carlo simulation allow for better estimation of how uncertainties propagate through measurements—a must for achieving reliable results.
Continual training and education of personnel involved in measurement processes is essential. By fostering a culture of awareness and accountabiity regarding measurement uncertainties, organizations can better assure quality and precision in their output.
Keeping Up with Technological Changes
The rapid evolution of technology introduces both new opportunities and challenges in precision metrology. Staying current with the latest tools and techniques is indispensable for metrology professionals. For example, the rise of advanced sensors and automation has streamlined many aspects of measurement, yet also amplifies the complexity of understanding and applying these technologies.
Key considerations in staying updated with technological advances include:
- Regular training and workshops aimed at knowledge enhancement
- Collaboration with tech developers to tailor solutions for specific needs
- Adopting a mindset of agility and adaptability to rapidly changing landscapes
In addition, integrative technologies, such as artificial intelligence and machine learning, illustrate the need for metrologists to rethink traditional approaches. These technologies can provide sophisticated analytics, enhancing not just measurement accuracy but also process efficiency. However, this also means that professionals must acclimate to new forms of data interpretation and machine functioning.
By proactively addressing the challenges posed by measurement uncertainties and technological advancements, professionals in precision metrology can ensure they remain at the forefront of this critical field.
Future Directions in Precision Metrology
In the ever-evolving landscape of technology, precision metrology stands at the forefront of innovation. This section focuses on the potential future paths this field may take, highlighting vital elements and considerations that shape its trajectory. As industries continue to demand higher standards of accuracy, precision metrology must adapt and grow. Failure to do so not only hampers progress but may also result in significant repercussions across various sectors. By examining emerging trends and the crucial role of big data, we can gain insight into how precision metrology will influence the coming generations of technology and engineering practices.
Emerging Trends in Measurement Technologies
Recent years have brought about a slew of groundbreaking technologies that promise to redefine how measurements are taken in precision metrology. Notable trends include:
- Advancements in Sensor Technology: As our understanding of materials and techniques grows, new sensor technologies are being developed. These sensors are becoming increasingly sensitive and capable of detecting minute changes in measurement conditions.
- Integration of IoT Devices: The Internet of Things (IoT) is paving the way for smart manufacturing and metrology. Devices that communicate with each other in real-time can significantly enhance measurement processes, allowing for immediate adjustments and better quality management.
- Increased Automation and Robotics: Automated measurement systems are reducing human error, improving efficiency and consistency. Automation technologies like collaborative robotics are being used alongside traditional metrology tools, bringing precision to the next level.
- 3D Printing and Additive Manufacturing: The rise of 3D printing necessitates precise measurements for effective design and production. New metrology solutions are emerging that specifically cater to the unique challenges presented by additive manufacturing processes.
These trends highlight a shift towards more integrated, automated, and connected measurement solutions, pointing to a future where precision metrology is not just a standalone discipline but a key player in the manufacturing ecosystem.
The Role of Big Data in Metrology
Big data plays a transformative role in precision metrology by enabling the collection, analysis, and utilization of vast amounts of data from various sources. Here’s how it impacts the field:
- Data-Driven Decision Making: With big data analytics, metrology professionals can make informed choices based on trends and predictive algorithms. This helps them anticipate measurement needs and align resources accordingly.
- Enhanced Calibration Processes: Large datasets allow for more precise calibration of instruments, ensuring they perform optimally under different conditions. The use of historical data for calibration settings can significantly reduce errors.
- Real-Time Monitoring and Feedback: Utilizing big data in conjunction with IoT enables real-time monitoring of measurement systems. Immediate feedback can alert operators to deviations, minimizing the risk of errors in production processes.
- Improvement of Quality Control: By analyzing patterns in measurement data, organizations can better understand variations in their processes. This leads to more effective quality control measures and a proactive approach to addressing issues before they escalate.
"Embracing big data in precision metrology is not just an option anymore; it’s a necessity for any organization that aims to stay competitive."
In summary, the future of precision metrology looks bright, filled with opportunities propelled by advances in technology and data analytics. The evolution of measurement techniques combined with the power of big data will undoubtedly reshape how industries view and implement precision in their operations.
Epilogue
In the field of precision metrology, the conclusion serves as a pivotal element that brings coherence and clarity to the insights previously discussed. It offers a moment to reflect on the nuances of measurement accuracy, the tools employed, and the implications of precision metrology across various industries.
Summarizing the Key Insights
The importance of summarizing insights in precision metrology cannot be overstated. Here are some key takeaways that arise from our exploration:
- Measurement Accuracy: At the heart of metrology lies the quest for accurate measurements. This ensures all operations in sectors like manufacturing and aerospace run smoothly, avoiding any costly errors.
- Diverse Applications: Precision metrology isn't just for engineers or scientists; it finds its utility in everyday life, from the calibration of medical devices to the manufacturing of microelectronic components.
- On-going Advancements: With the rapid pace of technological development, the landscape of metrology is constantly evolving. This encourages professionals to stay informed and adapt to new methodologies and tools.
Ultimately, precision metrology encompasses an intricate interplay of theory and practice, underpinning advancements in technology and quality assurance.
The Ongoing Importance of Precision Metrology
As we look ahead, the significance of precision metrology continues to grow. In a world driven by data and sophistication, the need for accurate measurements is paramount. Industries rely on established standards to ensure that their products meet rigorous requirements.
- Global Competitiveness: Businesses are increasingly at the mercy of global markets. Maintaining high standards in measurement helps companies stand out.
- Innovation: In sectors like aerospace and electronics, where performance can be a matter of life or death, measurement precision is not just important; it’s essential.
- Sustainability: Metrology plays a role in environmental conservation by ensuring that resource consumption is systematically measured and minimized.
"The ongoing importance of precision metrology lies in its ability to shape the future of innovation and quality across all sectors."
As such, precise measurements are the bedrock of trust in technology and safety in quality assurance. Understanding and embracing this field undoubtedly fosters not only individual growth but also bolsters entire industries in their quest for excellence.
With the complexities of our world looming large, precision metrology will undoubtedly continue to carve a path towards a future where measurements profoundly shape our daily lives.