Nutsche Filtration: Principles and Industrial Applications
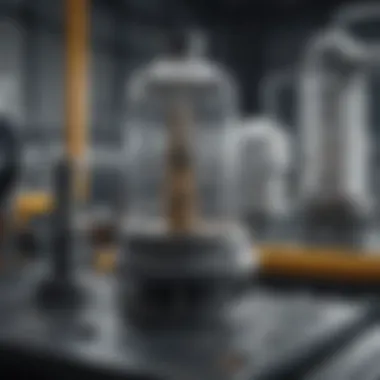
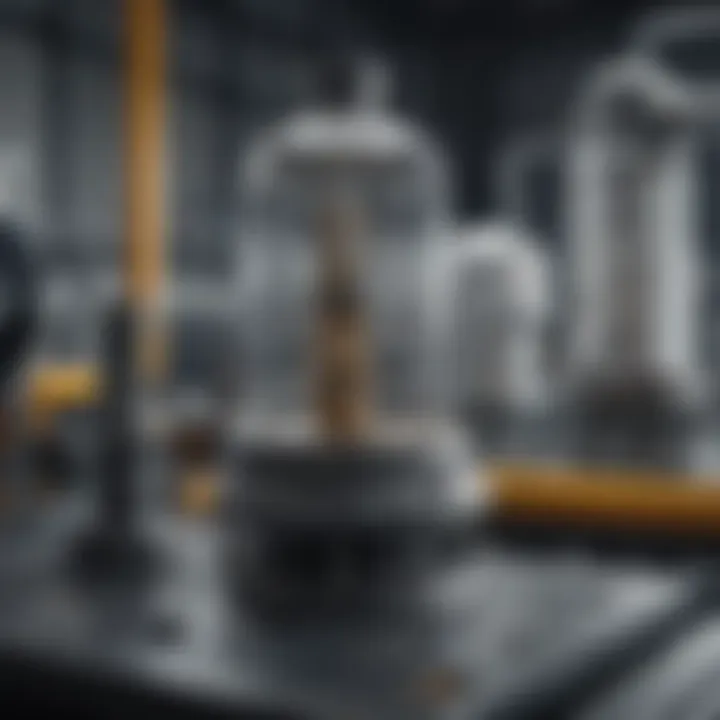
Intro
Nutsche filtration stands as a significant method in the realm of industrial separation processes, distinguished for its effectiveness in solid-liquid separation. Though one may encounter various filtration techniques, nutsche filtration garners attention for its suitability across a host of industriesβfrom pharmaceuticals to food processing. Leveraging the advantages of controlled filtration, it provides a refined approach to managing the complexities of separating solid particulates from liquids.
This article aims to unfold the foundational concepts surrounding nutsche filtrationβits operational principles, specific applications, and optimization strategies. Engaging with these elements offers readers not just the theoretical underpinnings, but also the practical insights necessary for applying nutsche filtration in real-world scenarios.
The narrative seeks to bridge knowledge gaps and stimulate intellectual curiosity for both seasoned professionals and those venturing into this area of study. By delving into the details, from equipment design to the advancements in technology, one can appreciate the multifaceted nature of nutsche filtration and envisage its evolution within the broader industrial filtration landscape.
Foreword to Nutsche Filtration
Nutsche filtration is a vital process widely utilized in numerous industries for separating solids from liquids. It stands out for its ability to handle batch filtration operations efficiently. Understanding this method is crucial for students, researchers, educators, and professionals who are keen on enhancing their knowledge of industrial filtration techniques. This section outlines its historical significance and contemporary relevance.
Historical Background
The origins of nutsche filtration can be traced back to the early 20th century when advancements in chemical engineering began to require more effective separation techniques. Initially employed in the context of the chemical industry, the nutsche filter has evolved significantly, adapting to meet the demands of various applications. Historical data show that this technology has been a reliable choice for decades, paving the way for innovations in equipment designs and filtration methodology.
In those early days, pans or trays were used for simple gravity filtration. As industries grew and processes became more complex, the design of nutsche filters was refined. The introduction of mechanical aids allowed for improved filtration rates, which was a game changer. Now, it's not unusual to find sophisticated versions utilizing automation and real-time monitoring.
Definition and Importance
Nutsche filtration refers specifically to a process employing a filtration vessel wherein a mixture is spread over a filter medium. The liquid passes through, leaving behind the solid particles. This is essential in establishing a clean separation between liquids and solids, which is vital across various industries like chemicals, pharmaceuticals, and food production.
Its importance cannot be overstated; it ensures the quality of final products by effectively removing contaminants. The significance of nutsche filtration lies not only in its versatility but also in its adaptability to different operational conditions. In a study, it was noted that nearly 70% of companies in the chemical sector utilize nutsche filters for solid-liquid separation.
Basic Principle of Operation
The operating principle of nutsche filtration is straightforward yet effective. The basic process involves placing a slurry consisting of solids and liquids into the filtration vessel. When the filtration begins, several phases come into play:
- Gravity or pressure-driven flow allows the liquid to seep through the filter medium, leaving solids behind.
- Flow control mechanisms are employed to regulate the operational conditions, such as temperature and pressure, greatly impacting efficiency.
- After initial separation, the cake formed on the filter media might undergo washing and drying to enhance the purity of the solid product.
Overall, nutsche filtration operates efficiently under relatively simple principles, but its effectiveness relies on carefully designed equipment and optimized operational parameters.
"The application of nutsche filtration in industry not only enhances production quality but also showcases the simplicity of design in complex separation processes."
Components of Nutsche Filters
In order to fully grasp the significance of Nutsche filtration, itβs crucial to understand its core components. Each component plays an integral role in ensuring the process is effective, efficient, and meets the specific requirements of different industries. The design and integration of these elements not only impact the filtration performance but also determine its suitability for particular applications. By examining the components closely, users can optimize their filtration processes, ensuring that the intended outcome is achieved with minimal complications.
Filtration Vessel Design
The filtration vessel is more than just a container; it is the heart of the Nutsche filtration system. Constructed from materials resistant to corrosion and wear, such as stainless steel, the vessel must accommodate high pressures without compromising integrity. Its design features a bottom drainage outlet to allow for smooth removal of filtrate while retaining the solid phase.
Key considerations in vessel design include uniform flow distribution. If the distribution is uneven, you can expect localized clogging, a definite no-go in industrial settings. Companies often opt for a cylindrical shape as it encourages better flow dynamics. Additionally, the option for jacketed designs allows for temperature control, an essential factor when dealing with heat-sensitive materials. Think of the filtration vessel not just as a mere apparatus; itβs a well-engineered solution catering to the nuances of your specific filtration needs.
Filter Media Selection
When diving into Nutsche filtration, the choice of filter media is pivotal. It's the barrier that permits liquid to pass while retaining particles. Selecting the appropriate filter media can drastically improve the overall effectiveness of the filtration process.
Media can range from various materials like paper, synthetic fibers, to metals. Not all filter media are created equal; some are most effective for specific types of solids. For instance, in the chemical industry, you might prefer woven wire cloth due to its strength under pressure, while in pharmaceuticals, non-fibrous alternatives that minimize contamination risks might be essential.
Factors such as pore size, thickness, and flow rate should weigh into your decision-making. After all, the right filter media can lead to higher throughput and reduce the frequency of maintenanceβresulting in a smoother operation overall.
Pneumatic and Mechanical Systems
The operational aspect of Nutsche filtration heavily relies on its pneumatic and mechanical systems. These systems are responsible for the movement of the slurries and the exertion of force needed to maximize filtration efficiency.
A pneumatic system can introduce air pressure for assisting in discharge of solids. This technique becomes particularly handy for viscous suspensions where gravity alone wonβt do the trick. Mechanical systems, often equipped with agitators, can enhance the homogeneity of the feed, ensuring that the solid-liquid mixture is even, which leads to consistent filtration results.
The reliability of pneumatic and mechanical systems dictates the success rate of Nutsche filtration, making their proper integration into the overall design a priority.
In some instances, automation features might be introduced to monitor pressure and flow rates in real-time, enhancing both safety and efficiency. Thus, integrating these systems thoughtfully is essential for achieving optimal results across different applications.
Understanding the components of Nutsche filters deepens insights into their functionality. Each element from the vessel design to filter media and supporting systems plays its part, not just in the physical process but as a strategic advantage within various industrial landscapes.
Nutsche Filtration Process
The Nutsche filtration process is central to understanding how this methodology operates across various industries. It serves not only as a method for separating solid and liquid components but also emphasizes the importance of efficiency and precision in industrial applications. By breaking down this process and its associated phases, we gain insight into the meticulous nature of Nutsche filtration, which impacts factors such as cost-effectiveness, product quality, and operational downtime. All these elements are critical in a competitive industrial landscape.
Preparation of the Feed
Before the filtration begins, there's a crucial step called the preparation of the feed. This involves ensuring that the material to be filtered is consistent in size and composition. Any discrepancies in this stage can lead to varying flow rates and filtration efficiency down the line.
In practice, this means screening the feed to remove larger particles that could clog the filter media. A uniform feed enhances the overall performance of the Nutsche filter and establishes the foundation for a successful filtration cycle. When the feed is prepared correctly, it sets the stage for more predictable processes in subsequent phases.
Filtration Cycle Phases
Understanding the filtration cycle phases gives valuable insights into how Nutsche filtration works. Each phase has unique tasks and contributions that together drive the overall effectiveness of the process.
Clarification Phase
The clarification phase stands out as the initial stage in the filtration cycle where the bulk of solids begins settling out. What characterizes this phase is the relatively low pressure applied, which allows finer solids to slowly ascend to the surface, creating a layer known as a filter cake. This aspect is beneficial because it minimizes shear forces that could damage sensitive materials, particularly in pharmaceutical applications. However, the unique feature here is that the quality of the clarified liquid can be significantly improved through controlled sedimentation, ensuring that only the desired liquid proceeds to the next stage.
Advantages include less wear on machinery, but the downside is that the efficiency may fluctuate depending on the initial quality of the feedstock.
Retention Phase
Next comes the retention phase, which plays an essential role in holding back the solid materials from passing through the filter media. Here, a key characteristic is the use of pressure to ensure that the filter cake remains intact while achieving effective separation. This phase is often favored due to its capacity to deal with varying particle sizes and ensure that the majority of solids remain behind. A unique feature of this phase is the possibility of periodic backwashing to maintain filter integrity.
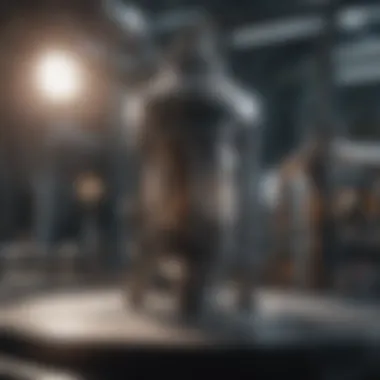
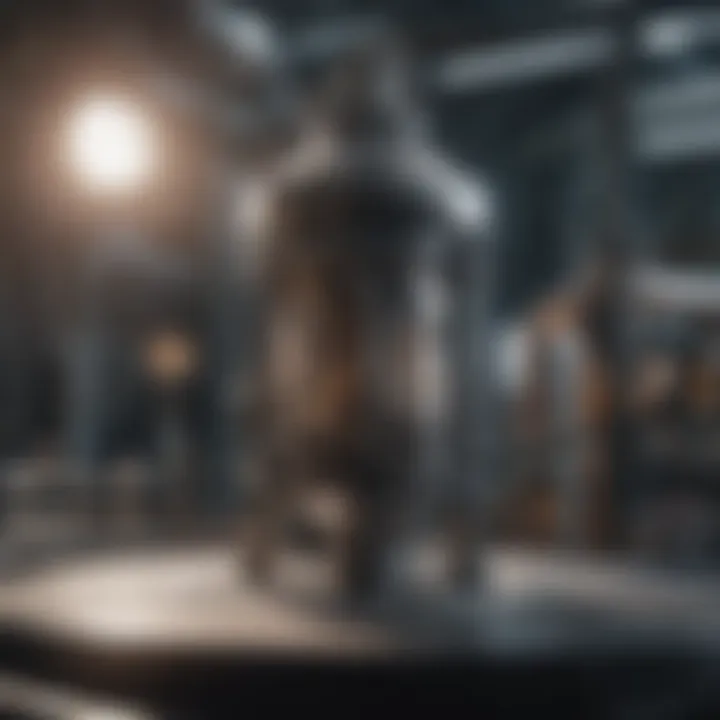
Its advantage lies in improved yield; however, should clogging occur, the entire filtration efficiency may drop.
Washing Phase
In the washing phase, solvents or cleaning agents flow through the filter cake to further cleanse the solids from residual contaminants. The essential aspect of this phase is to recycle or improve the quality of the solids. A distinct feature is that the washing process can be adjusted to optimize resource usage and minimize waste. This is why it's a favored phase, especially within pharmaceutical and chemical industries where product purity is paramount.
However, a potential downside is that excessive washing can lead to throughput delays and increased costs.
Drying Phase
Finally, during the drying phase, the remaining moisture in the filtered solids is reduced, preparing them for downstream processes or final storage. A key characteristic is often the application of vacuum assistance or extensive heating to expedite moisture removal. This phase is vital, particularly in applications where adhering to moisture specifications can influence product quality. The unique aspect is the ability to adjust drying conditions based on the specific material characteristics.
Advantages include enhanced storage stability and reduced risk of microbial growth, while a drawback can be energy consumption with high-temperature applications.
Post-Filtration Handling
Once the filtration process is complete, objects of careful consideration include transporting the filtered solids and managing the clarified liquid. The post-filtration handling stage is crucial for maintaining product integrity and preparing materials for their next application. Any mishandling at this point can negate the precision that was achieved during the filtration process.
Aspects like the design of the discharge systems, potential residual moisture levels, and storage environment should be accounted for to maximize efficiency and minimize loss. A solid understanding of post-filtration procedures can greatly influence operational success across industries.
Applications of Nutsche Filtration
Nutsche filtration has cemented its place as a pivotal process in various industrial sectors. Understanding its applications is crucial as it reveals how this process not only enhances productivity but also ensures quality in numerous end products. Here we delve into the applications, focusing on sectors where nutsche filtration plays a critical role, highlighting benefits, implications, and some potential concerns that come into play.
Chemical Industry
In the chemical industry, the application of nutsche filtration is paramount for separating solids from liquids. Here, the demand for high purity and consistent quality is non-negotiable. Using nutsche filters, manufacturers can tackle thick sludges and cumbersome slurries that are often found in this field.
Key benefits include:
- Efficiency: The process can handle large volumes, catering to production demands.
- Quality Control: Continuous operation helps maintain uniform product standards.
- Versatility: Apart from separation, filtration works effectively during crystallization and drying stages.
However, companies should be cautious about clogging, which can hinder throughput and operational efficiency.
Pharmaceutical Manufacturing
When it comes to pharmaceutical applications, purity is a top priority. Nutsche filtration is widely employed to separate active pharmaceutical ingredients (APIs) from reaction by-products or solvents. The filtration system's design allows for precise control of the filtration process, which is crucial given the regulatory landscape of the pharmaceutical industry.
Some crucial points to consider are:
- Sterility: Proper design minimizes contamination risk.
- Scalability: Nutsche filters can be scaled up effectively for large-scale production.
- Cost-effective: Offers a reliable means to process expensive materials efficiently.
The downside remains the initial capital outlay and the need for expert operational oversight to meet stringent regulatory standards.
Food and Beverage Processing
The food and beverage industry also benefits significantly from employing nutsche filtrations, particularly in processes like juice clarification, sugar refining, and the filtration of beer. Here, the emphasis is on ensuring product safety and taste while maintaining efficiency.
Benefits in this sector include:
- Safety: High-quality filtration ensures the removal of harmful microbes and contaminants.
- Taste Preservation: Gentle filtration techniques maintain the flavor profile of beverages.
- Waste Reduction: Efficient processes lead to lesser waste and better resource management.
However, manufacturers face challenges during cleaning and maintenance, especially ensuring that all residues are adequately removed to avoid flavor contamination.
Wastewater Treatment
Finally, in wastewater treatment, nutsche filtration has emerged as an effective solution for removing solids and other contaminants from industrial effluents. The application here is vital for meeting environmental regulations while recycling water for reuse.
"> Nutsche filtration helps industries not only in managing waste but also promoting sustainable practices."
The key points to note are:
- Environmental Compliance: It helps facilities meet governmental standards.
- Resource Recovery: Allows for reclaiming valuable components from wastewater.
- Operational Flexibility: Adaptable to various types of wastewater.
Nonetheless, the costs associated with initial installation and ongoing upkeep can be a concern for some facilities.
Advantages of Nutsche Filtration
Nutsche filtration stands out in the field of industrial filtering due to several inherent advantages it possesses. Understanding these benefits is essential for educators, researchers, and professionals who are engaged in optimizing filtration processes across various sectors. This section will delve into the different aspects of the advantages of nutsche filtration, highlighting specific elements that contribute to its relevance and effectiveness.
Efficiency and Effectiveness
Nutsche filters are widely appreciated for their efficiency in separation processes. They offer a streamlined approach when it comes to filtering liquids from solids. This method typically leads to a higher yield of the desired product.
- High throughputs: One of the primary benefits is the capacity to handle large volumes, thus enabling industries to maintain productivity levels. Once the feed is prepared, the filtration process operates rapidly, cutting down production time significantly.
- Solid product quality: The end product, usually a solid cake, exhibits a high purity level due to the improved design of filter media. Not only does this enhance the quality of the product, but it also aligns with stringent compliance regulations across industries such as pharmaceuticals.
- Minimal loss of product: Efficiency does not merely relate to speed but also to material loss. In nutsche filtration, the enclosed system minimizes exposure of materials to contaminants, which helps in retaining maximum product quality while reducing waste.
Nutsche filtration systems can often achieve separation efficiencies above 90%, making them a cornerstone in many industrial settings.
Ease of Operation
One of the attractive features of nutsche filtration is its straightforward operation, especially when compared to alternatives like centrifuges or other complex systems. The design inherently supports a user-friendly process:
- Simple controls: Operators require minimal training to run these systems effectively. Most nutsche filters come with easily accessible controls that can be monitored and adjusted as needed.
- Automated systems: Many modern iterations of nutsche filters incorporate automation, making it even easier to manage operations with reduced human intervention. With advanced sensors and monitoring technologies, operational parameters can be maintained without constant oversight, allowing operators to focus on more strategic decisions.
- Reduced manual labor: The operational workflow minimizes the need for physical labor, which is beneficial in heavily regulated environments like pharmaceuticals. This reduction in manual tasks not only enhances safety by preventing exposure to hazardous materials but also cuts costs related to labor management.
Scalability
The scalability of nutsche filtration systems is another notable advantage, particularly for industries facing fluctuations in production demands. They offer flexibility that can accommodate varying scales of production:
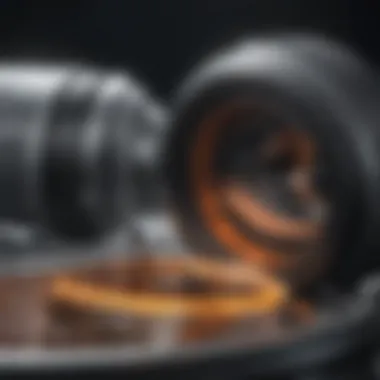
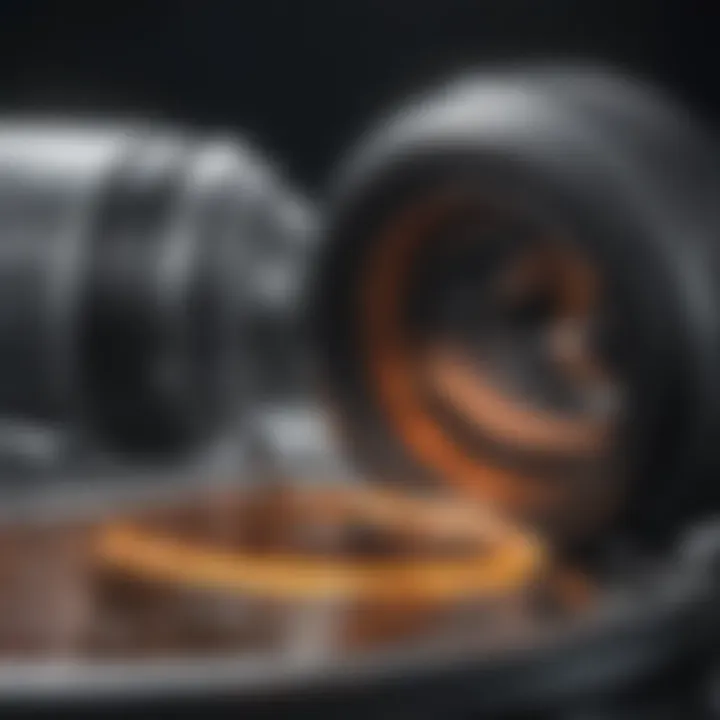
- Adaptable design: Nutsche filtration systems come in a range of sizes and configurations. Smaller models can cater to lab-scale processes, while larger systems can serve high-volume industrial needs. This adaptability ensures that organizations can grow without the necessity of overhauling their existing equipment.
- Incremental upgrading: Existing systems can be upgraded as production increases. New components can often be integrated seamlessly into the existing setup, which prevents interruptions to ongoing operations, maintaining productivity.
- Cost-effective: Investing in a single adaptable system rather than multiple specialized systems can be more cost-effective over time. As production needs grow, companies can scale their nutsche filtration setup with minimal interruption to regular operations, ultimately yielding greater returns on their investments.
Limitations of Nutsche Filtration
Understanding the limitations of nutsche filtration is vital for industries relying on this process for liquid-solid separation. While itβs a robust method, several constraints can hinder its overall effectiveness, making it imperative for professionals to recognize and navigate these issues. Identifying these limitations allows for better optimization strategies, ensuring that the filtration process is both efficient and cost-effective.
Clogging Issues
One of the most significant challenges in nutsche filtration is clogging. This can occur due to the build-up of particulate matter on the filter media. When the feed solution contains high concentrations of fine particles, the filter might become restricted. In situations where clogging occurs, the flow rate diminishes, leading to longer filtration times and reduced throughput. It's akin to trying to get water through a heavily soiled sponge; the more muck there is, the harder it becomes to achieve the desired flow.
To mitigate clogging, operators can implement several strategies:
- Choosing Appropriate Filter Media: Using media with the right pore size and material can drastically reduce clogging.
- Regular Maintenance: Cleaning or replacing filter elements when starting to notice performance drops keeps the system running efficiently.
- Control Feed Concentration: Keeping an eye on the concentration of suspended solids in the feed can help avoid overwhelming the filter system.
Equipment Complexity
Operating a nutsche filter isnβt as straightforward as it may seem. The necessary equipment, ranging from valves to the filtration vessel itself, can be complex. This complexity often results in increased maintenance needs and requires skilled personnel for operation. Adding to this, troubleshooting becomes more daunting due to the intricate nature of these systems. Everyone loves a straightforward approach, but with nutsche filtration, complexity is often the name of the game.
Moreover, interfacing with other equipment in a production line may present additional challenges. Compatibility issues can arise, especially when integrating legacy systems with new technology. Designers must pay close attention to the equipment layout and flow dynamics to prevent potential bottlenecks.
Initial Investment Costs
While nutsche filtration can offer significant operational efficiencies, the initial investment costs can be a barrier for some organizations. The high upfront costs associated with purchasing specialized nutsche filter equipment and necessary peripherals can make companies hesitant to adopt this technology. Like investing in a good pair of shoes, you know it pays off in comfort, but the ticket price can be a shock.
Beyond the equipment itself, one must also factor in installation expenses, which often add up. Training personnel in troubleshooting and operation increases costs further. In the long haul, however, the efficient separation capabilities of nutsche filtration can lead to savings. But thatβs an easier sell when youβre already deep into the business.
In summary: Recognizing the limitations of nutsche filtrationβclogging, equipment complexity, and high initial costsβis crucial for optimizing its use. By being aware of these hurdles, businesses can better prepare to tackle them, ultimately enhancing efficiency and performance in their processes.
Advancements in Nutsche Filtration
The world of nutsche filtration is subtilely evolving, shaped by technological prowess and environmental awareness. Advancements in this field are pivotal, not just for enhancing the operational yield but also for streamlining processes, curbing costs, and ensuring compliance with environmental standards. As industries continuously seek to enhance efficiency, the role of innovation in nutsche filtration assumes greater significance. Key advancements focus on automation, monitoring technologies, and research, all integral in keeping pace with the demands of modern industry.
Technological Innovations
Automation in Filtration
Automation in filtration has become a cornerstone of modern nutsche filtration systems. This shift towards automated processes minimizes the need for manual intervention, thus enhancing overall efficiency. One major characteristic of automated filtration is its ability to maintain consistent operating conditions. By using advanced control systems, businesses can ensure that parameters like pressure and flow rate are kept within optimal limits. This consistency not only improves product quality but also reduces material waste.
A unique feature of automation is its reliance on advanced algorithms that can adapt filtration processes in real-time based on varying feed characteristics. This adaptability is not merely advantageous; it's crucial for industries where the composition of the feed can fluctuate widely. However, one must consider that the initial setup for such systems could be costly, and the learning curve might require some degree of expertise. On the flip side, the long-term gains in efficiency and reduction in labor costs often off-set these initial hurdles.
Real-time Monitoring Systems
Real-time monitoring systems offer another layer of enhancement to nutsche filtration processes. These systems track various parameters, ensuring that conditions remain stable throughout the filtration cycle. Their main advantage is the immediacy with which they provide data. They give operators the ability to respond promptly to any deviations from expected performance. This characteristic makes them a popular and necessary addition to high-stakes filtration environments like pharmaceuticals and food processing.
A striking feature of these monitoring systems is their integration with data analytics tools, allowing for predictive maintenance and optimization based on historical performance metrics. While installation can be intricate, potentially leading to initial downtime, the eventual benefits include not only enhanced operational efficiency but also improved safety and product integrity. Hence, investing in these systems proves their worth in advancing the productivity and reliability of nutsche filtration.
Research and Development Trends
The field of nutsche filtration is witnessing noteworthy research and development trends. Scholars and industry experts are increasingly focused on enhancing filtration media and exploring alternative materials. Such endeavors aim not only to boost filtration efficiency but also to create eco-friendly options that align with contemporary sustainability efforts. Innovations in materials science, particularly the development of high-performance filter media, are garnering interest, transforming traditional methods into more effective solutions. Furthermore, ongoing studies in separator design aim to reduce the environmental footprint without compromising productivity.
Environmental Considerations
In an era where environmental sustainability is paramount, nutsche filtration technologies are making strides to align with green practices. Modern advancements emphasize reducing waste and energy consumption, thus supporting stricter environmental regulations across various industries. By optimizing operational parameters through innovative approaches, firms can mitigate their ecological impacts while enhancing filtration efficiency. This is particularly significant in industries such as wastewater treatment, where the implementation of greener practices can lead to substantial ecological benefits.
Advancements in nutsche filtration signify more than just improvements in efficiency; they reflect a broader commitment to sustainable practices, innovation, and an awareness of industry needs. By embracing these changes, companies can not only thrive in competitive markets but also contribute positively to their sectors and the environment.
Optimization Techniques
Optimization techniques play a crucial role in enhancing the Nutsche filtration process, significantly impacting efficiency, product quality, and operational costs. In a world where precision is key, understanding how to fine-tune parameters during filtration can make all the difference. This section focuses on specific elements such as pressure optimization, temperature control, quality control measures, and data analysis, exploring their contributions and advantages in the application of Nutsche filtration.
Parameter Adjustments
Pressure Optimization
Optimizing pressure is essential in the Nutsche filtration process. The filtration performance can be greatly influenced by the applied pressure, which affects flow rates and the overall efficiency of solid-liquid separation. Higher pressures typically promote faster filtering, reducing cycle times. However, the downside of increasing pressure is the potential for filter medium damage or even system leaks. Achieving the balance of pressure is critical; too much can lead to increased wear on equipment and higher maintenance costs.
A unique aspect of pressure optimization is that it varies depending on the characteristics of the material being filtered. For instance, thicker slurries may require different pressure settings than thinner ones. In addition, utilizing variable pressure systems can allow processors to adapt quickly to changes in feed material conditions, ensuring optimal performance at all times.
One of the biggest advantages here is the increased throughput. More material can be processed effectively, which often translates to better overall productivity in the long run. Still, it necessitates careful monitoring and adjustments to avoid compromising the filtration integrity.
Temperature Control
Temperature control also plays a vital role in Nutsche filtration. The solubility and viscosity of the slurry can shift dramatically based on temperature variations. Maintaining the right temperature ensures that solid-liquid separations are effective and efficient, especially when handling temperature-sensitive materials typical in the pharmaceutical and food industries.
The key characteristic of temperature control is its ability to affect the viscosity of fluids. Warmer temperatures often result in lower viscosity, promoting quicker flow rates through the filter medium. However, like pressure optimization, excessive heating can lead to thermal degradation of certain materials.
A unique feature of incorporating temperature control in Nutsche filtration is the potential for enhancing the washing phase. Warm washing solutions can more effectively remove residual impurities from solids, leading to a higher quality product. The challenge lies in the initial setup costs and energy requirements for maintaining certain temperature settings.
Quality Control Measures
Quality control measures specifically tailored to Nutsche filtration processes ensure consistent output quality. Regular monitoring of filtration efficiency and product purity forms an essential part of maintaining standards. Techniques such as visual inspections, microscopy, and on-site analytical measurements can provide feedback on filter performance and product quality. High-quality controls not only prevent costly discrepancies in product specifications but also boost customer confidence in the end product, establishing a reputation for quality.
Data Analysis and Performance Tracking
Data analysis serves as a backbone for optimizing Nutsche filtration. Utilizing software tools for performance tracking allows operators to gather critical data β flow rates, filtration time, pressure differentials, and product quality metrics β in real-time. By employing statistical process control techniques, engineers can identify trends and anomalies in filtration performance, leading to informed decisions.
Such analytics can help in predictive maintenance strategies, thus reducing downtime and extending equipment life. Furthermore, compiled performance data makes it easier to compare against historical benchmarks, driving continuous improvements. This supports a proactive approach toward operational efficiency, ensuring facilities remain at the forefront of technology and best practices.
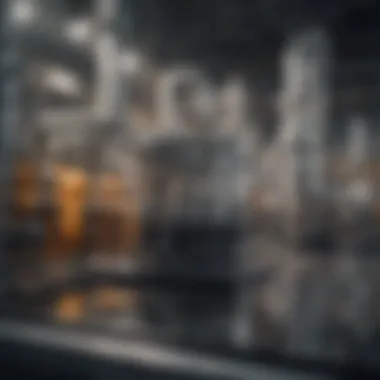
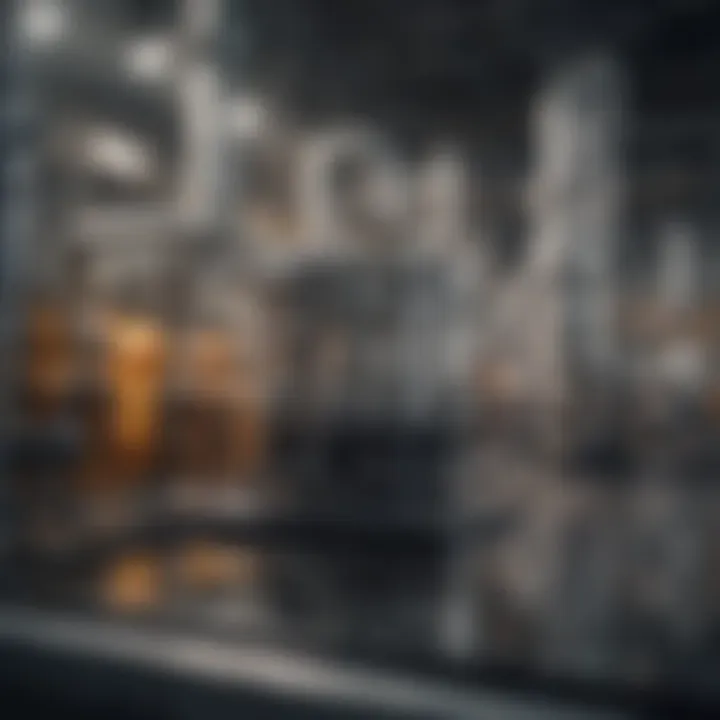
Continuous monitoring and data analysis are not merely optional; they're essential for maintaining a competitive edge in the industry.
Case Studies
Case studies are an integral part of understanding the practical applications and efficacy of nutsche filtration. By examining real-world scenarios, we gain insights into how this specific filtration technology operates across different industries. The focus on case studies helps highlight not only the effectiveness of nutsche filtration but also the challenges faced in implementation and operation. Additionally, these studies illuminate the decision-making processes that led companies to choose nutsche filtration over other methods while providing a framework for others looking to adopt similar systems.
Benchmarking in the Chemical Sector
In the chemical industry, benchmarking nutsche filtration offers a clear view of its advantages in separating liquid from solids. For instance, a company producing fine chemicals recently integrated a nutsche filter in their purification process. This shift was based on extensive evidence gathered from various case studies indicating higher yields and quicker cycle times compared to traditional filtration methods.
Benchmarking not only involves measuring performance indicators like filtration speed and throughput but also assessing aspects such as maintenance costs and operational downtime. Companies commonly analyze metrics against industry standards and competitors to identify best practices. The real-world benefit here is akin to finding a shortcut on a long road; efficiency rises significantly while resource use drops.
Some common metrics examined include:
- Filtration speed: Time taken to complete a filtration cycle.
- Filtrate clarity: Purity level achieved post-filtration.
- Operational costs: Overall expenditure related to power and labor.
Nutsche Filtration in Pharmaceuticals
In the pharmaceutical industry, the stakes are incredibly high when it comes to purity and compliance with regulations. Nutsche filters have found extensive application in this sector, particularly for the production of active pharmaceutical ingredients (APIs). A notable case study involved a pharmaceutical manufacturer that switched to nutsche filtration for its antibiotic production line.
Here, the flexibility of nutsche systems allowed for ease of process scale-up while maintaining stringent quality requirements. This was particularly critical in the washing phase which necessitates a high wash efficiency to ensure that any residual solvent or reactant was thoroughly removed. The result? A significant reduction in product contamination incidents during quality testing, thereby improving both the compliance rate and marketability of their products.
Application in Food Industry
Nutsche filtration is also making its mark within the food industry. One fascinating case involved a company producing edible oils. The oils were initially filtered using conventional methods, but they faced challenges in removing fine particulates, leading to sedimentation in the final product.
Switching to nutsche filtration allowed for finer filtration, resulting in higher product clarity and consistency. The company observed a remarkable improvement in shelf-life of their products due to the reduction of solids, which often promotes rancidity.
"With nutsche filtration, we not only retained quality but also increased our production capacity without the need for significantly more resources."
The key lessons from this case revolved around the adaptability of nutsche systems in existing production lines and how these filters can contribute to meeting both quality and efficiency objectives.
The exploration of these practical examples underscores the vital role of case studies in illuminating the effectiveness and practicality of nutsche filtration systems across various sectors.
Future of Nutsche Filtration
As industries evolve, the need for advanced and efficient filtration technologies continues to grow. Nutsche filtration, with its solid reputation, isn't left out of this transformative wave. The future of nutsche filtration hinges on several key factors, including technological integration and emergent trends in both manufacturing and environmental stewardship. It holds promise not just for enhancing filtration performance, but also for establishing a more sustainable solution to industrial challenges.
Emerging Trends
The landscape of nutsche filtration is seeing shifts that reflect broader industry changes. A notable trend is the increasing emphasis on automation. With digital technologies being woven into the fabric of industrial processes, the role of machine learning and artificial intelligence in optimizing filtration parameters is becoming clear. Companies are looking to streamline operations and minimize human error, making filtration processes faster and more reliable.
Another trend is the focus on sustainability. As environmental regulations tighten, industries are prompted to adopt greener practices. Nutsche filtration offers a path forward, chiefly due to its capabilities in reducing waste generation. For instance, the ability to tailor filtration to specific processes means less byproduct and more efficient use of chemicals.
- Increased automation: Streamlining operations through digitalization.
- Sustainability focus: More efficient processes lead to reduced waste.
- Cost-effective solutions: Innovations typically result in lowered operational expenses.
Integration with Other Technologies
Cross-Flow Filtration
Cross-flow filtration represents a significant leap in how filtration can be effectively carried out. Its core characteristic is maintaining a constant flow of the feed solution across the filter. This approach minimizes the likelihood of filter cake formation, which often clogs traditional filters. The continuous flow allows for better permeate quality and operational efficiency, making it a favored choice in various applications.
The unique feature of cross-flow filtration is its ability to keep the filtration medium clean while working. This means less downtime for maintenance and cleaning, ultimately translating into cost savings for companies. It makes cross-flow filtration a popular and beneficial addition to the nutsche filtration landscape.
- Key characteristic: Constant flow reduces clogging.
- Advantages: Lower maintenance, improved permeate quality.
- Disadvantages: Initial setup costs may be higher compared to standard methods.
Membrane Technologies
Membrane technologies are reshaping traditional filtration approaches with their innovative processes. These technologies provide precise separation capabilities, which is essential when dealing with complex mixtures. When integrated with nutsche filtration, membrane technologies can dramatically enhance throughput and the quality of the final product.
What sets membrane technologies apart is their ability to operate at lower pressure compared to other methods. This feature not only conserves energy but also extends the life of the equipment. As industries look for energy-efficient solutions, these technologies are quickly gaining traction as a complementary method within the realm of nutsche filtration.
- Key characteristic: High precision in separation processes.
- Advantages: Energy efficiency, extended equipment lifespan.
- Disadvantages: Can be sensitive to fouling, necessitating regular monitoring.
The future of nutsche filtration is not just about refining existing processes but also about embracing new technologies that promise efficiency, sustainability, and scalability.
The End
The conclusion serves as a critical reflection on the entire discourse surrounding nutsche filtration. The importance of understanding its principles extends beyond mere interest; it has practical implications in various industrial applications. From pharmaceuticals to wastewater treatment, the nuances of nutsche filtration shape how solids and liquids are separated efficiently. This art of filtration is not just a matter of separating particulates; it's fundamentally about optimizing resources, maintaining product quality, and ensuring environmental compliance.
In this article, we highlighted several key components that underscore its relevance. Key considerations include:
- Efficiency: Nutsche filtration is recognized for effectively handling different viscosity and composition of slurries, making it a standout choice in industry.
- Scalability: It can be adjusted from small-scale laboratory settings to large-scale production, thus catering to various operational needs.
- Versatility: Its applications span across multiple sectors, showing its ability to adapt to different processing requirements.
While there are limitations such as equipment complexity and potential clogging, these challenges often present opportunities for innovative solutions. Addressing these challenges through advancements in technology, as discussed, not only improves the filtration process but also brings continued relevance to nutsche filtration in modernization and efficiency.
Ultimately, concluding this exploration, it's clear that the implications of nutsche filtration touch on economic factors, production standards, and regulatory compliance. Understanding these facets promises greater efficiency in industrial operations, which is a benefit for businesses aiming for excellence.
Summary of Key Points
In summation, the article provided a thorough examination of nutsche filtration, covering its principles, advantages, and limitations. The highlights of the sections include:
- The operational framework of nutsche filtration, including its capacity for solid-liquid separation.
- Applications that range across different industries, reinforcing nutsche filtration's relevance in both traditional and contemporary contexts.
- Discussions on optimization strategies, reflecting on how small tweaks can lead to significant improvements in performance and cost-effectiveness.
Each point tied back to the overarching theme of efficiency and adaptability, showcasing why nutsche filtration remains a pivotal practice in the industrial filtration landscape.
Final Thoughts
Wrapping up this exploration into nutsche filtration, itβs worth reflecting on its evolving role in industrial settings. As industries push for innovations, the importance of integrating advanced technologies with traditional methodologies cannot be overstated. Automation and real-time monitoring represent the future's willingness to enhance procedural efficiencies while minimizing human error. With research and development continuously paving the way for new insights, the future is bright for nutsche filtration.
The goal remains clear: to push the boundaries of what's possible and to solidify the efficacy of filtration processes. As industries strive for sustainability and increased productivity, a deeper understanding of nutsche filtration principles will undoubtedly lead to innovative solutions and optimized practices all around.
"In a constantly changing industrial landscape, staying informed about technologies such as nutsche filtration is not just beneficial; it's essential for any organization aiming to stay ahead."
This conclusion role models the art of reflection with depth, ensuring every student, researcher, educator, and professional is equipped with a comprehensive understanding of nutsche filtration's current and future impact.