The Impact of Control Integrators in Modern Systems
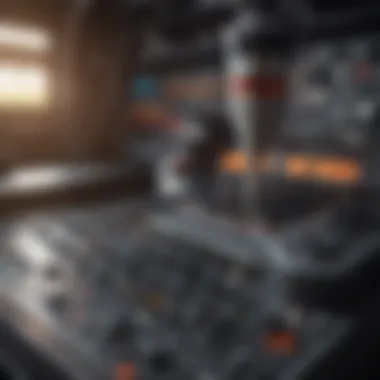
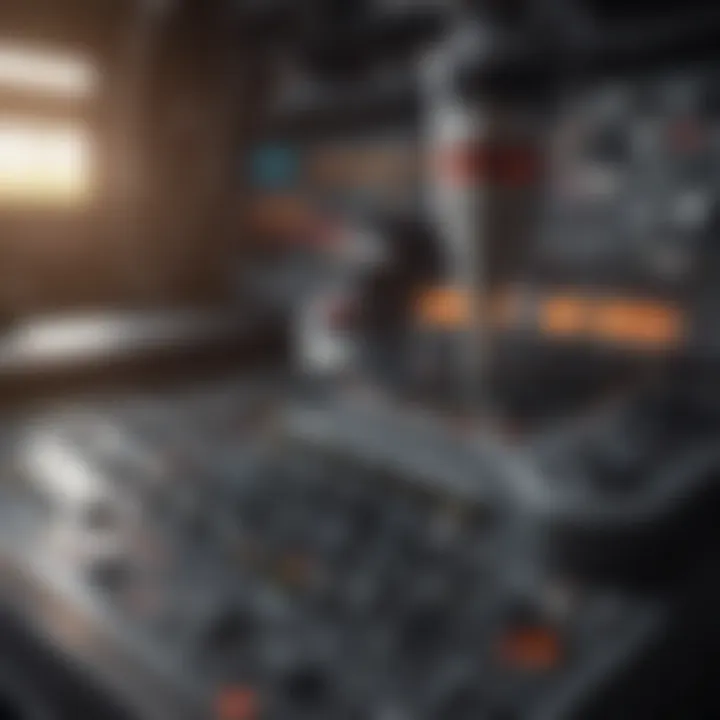
Intro
The complexities of modern systems demand tools and frameworks that can adapt and respond dynamically to changing conditions. At the forefront of this evolution are control integrators, which serve as the backbone for an array of industrial applications. Their role encompasses not just the management of system commands but also ensuring efficiency, reliability, and adaptability within various operational contexts.
Understanding how control integrators fit into this bigger picture is crucial for stakeholders in manufacturing, automation, and environmental management. They enable seamless interactions between components, ensuring that systems run smoother than a greased wheel. The foundational principles blend technology with operational needs, creating a landscape ripe for exploration and advancement, especially as new technologies continually emerge in our fast-paced digital age.
Foreword to Control Integrators
In a world where systems operate with increasing complexity, the role of control integrators has never been more crucial. Control integrators are the unsung heroes behind the curtain, ensuring that variances in operational parameters are kept in check and that systems run smoothly and efficiently. Their importance spans across various industries—from manufacturing to environmental management—shaping the way modern systems address challenges and optimize processes. This section aims to shed light on the principles that govern control integrators, their necessity in the digital age, and what informs their design and implementation.
Definition and Overview
Control integrators are tools or systems that manage and optimize the performance of control systems. They utilize various algorithms to ensure that a system maintains a desired output, despite disturbances or changes in input. A good way to think about them is like a conductor for an orchestra; they ensure each component performs harmoniously, thereby achieving a cohesive output.
Integrators work by taking the input from a sensor, processing it through a controller, and finally outputting commands to an actuator. Each piece is vital; without integration, you’d end up with a cacophony of disjointed signals that result in inefficiency, errors, or failures. The beauty of control integration lies in its ability to translate complex data into actionable directives, fundamentally impacting system efficiency and performance metrics.
Historical Context
The evolution of control integrators has deep roots in engineering and technology. The history traces back to the industrial revolution. In those early days, control techniques were rudimentary at best, relying heavily on human intervention. For instance, consider the steam engine: systems needed manual adjustments based on steam pressure and load conditions. However, this was neither efficient nor reliable. Fast forward to the 20th century, when automation began to take center stage with analog control systems making their way into various industries.
One significant leap was the development of the Proportional-Integral-Derivative (PID) controllers in the mid-20th century, which introduced a standardized method to enhance control precision. These developments paved the way for sophisticated control integrators that are commonplace today. The integration of digital technologies and advancements in algorithmic approaches have continually reshaped how control integrators function.
Today, control integrators position themselves at the intersection of hardware and software, merging sensor technologies, predictive analysis, and internet-connected devices to create systems that do not merely respond to changes but anticipate them.
"Control integration is not just about regulation; it’s about foresight and adaptability to future conditions."
By understanding the definition and historical background of control integrators, this article sets the stage for deeper exploration into their specific components, types, and application domains. This holistic view will enable stakeholders—from engineers to business leaders—to grasp their indispensable role in shaping modern systems.
Fundamentals of Control Systems
Control systems act as the backbone of countless modern technologies, from simple home appliances to intricate industrial processes. Understanding the fundamentals of these systems is pivotal to grasping the nuances of how control integrators operate within them. Control systems enable individuals and organizations to monitor and manage different processes efficiently, leading to enhanced performance and safety.
A deep dive into the components and types of control systems highlights their significance while also providing important context for the role control integrators play.
Components of Control Systems
Sensor Technologies
Sensor technologies serve as the eyes and ears of control systems. These devices collect data about the physical environment, translating changes—such as temperature, pressure, or humidity—into signals that can be processed. An essential aspect of sensor technology is its ability to provide real-time feedback, which is crucial for maintaining system stability and performance.
One key characteristic of sensor technologies is accuracy. Accurate data allows control systems to react swiftly and effectively, which is a beneficial aspect for industries requiring high precision. For instance, in manufacturing, the right sensor can ensure that machinery functions within defined parameters, preventing costly errors.
However, sensor technologies also present some challenges. Environmental factors may affect their performance, leading to maintenance needs that can slow down processes if not addressed promptly. Nonetheless, their ability to offer immediate, actionable insights makes them an indispensable part of control systems.
Actuators
Actuators are the muscles of control systems, converting control signals into physical actions. These devices respond to commands from controllers to execute tasks, like moving components or adjusting valves. The key characteristic of actuators is their capability to provide mechanical output, which is vital in achieving desired process control outcomes.
The unique feature of actuators lies in their wide range of operations—be it hydraulic, pneumatic, or electric—and their integration into varying control structures. This versatility contributes to their popularity across diverse sectors, including robotics and automotive systems, where adaptability is crucial.
Despite their advantages, actuators can encounter issues concerning speed and efficiency. If not calibrated correctly, they may operate slower than necessary, which could hinder overall system performance. Yet, the significance of actuators in translating control decisions into actions cannot be understated.
Controllers
Controllers take on the role of the decision-makers in control systems. They analyze input data from sensors and determine the appropriate output actions for actuators. The central function of a controller is maintaining system stability by continuously adjusting commands based on the feedback received.
Hosting a wealth of algorithms, controllers come in many forms. For instance, PID controllers are widely utilized due to their simplicity and robustness in various applications. Their unique feature—combining proportional, integral, and derivative actions—enables fine-tuning of the control process.
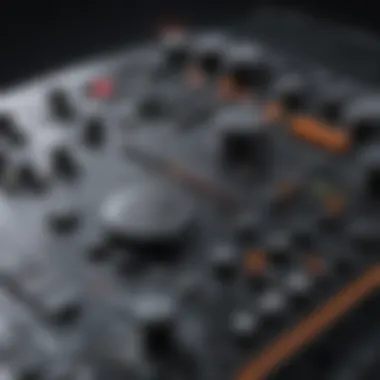
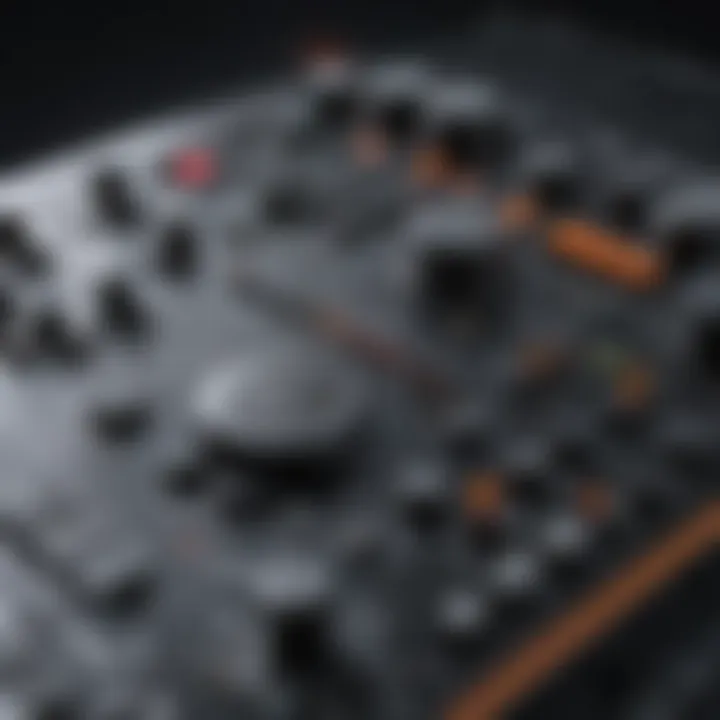
Nevertheless, controllers can sometimes struggle with complex processes. Especially in environments where rapid changes occur, the challenge of tuning parameters to adapt to performance demands can emerge. Yet, the critical role of controllers in bridging the gap between systems and physical actions exemplifies their importance in effective control integration.
Types of Control Systems
Open Loop vs Closed Loop
The distinction between open-loop and closed-loop control systems is fundamental for understanding operational strategies within system environments. Open-loop systems, like a simple washing machine, operate on predefined settings without feedback, making them easy to implement but limited in adaptability. Their simplicity translates to low costs and easy maintenance.
In contrast, closed-loop systems are more dynamic. They incorporate feedback mechanisms that allow them to adjust actions based on outcomes. This adaptability can lead to improved precision and efficiency, proving especially beneficial in scenarios like climate control, where maintaining specific temperatures is crucial.
However, closed-loop systems can be more complex and costly to implement, often requiring more sophisticated components and tuning efforts. The balance between ease of setup and responsiveness underscores the preferences for different types of control systems based on specific application needs.
Linear vs Non-Linear
Understanding linear versus non-linear control systems further enriches the discussion about design and functionality. Linear control systems operate under principles of proportionality, meaning that input changes directly correlate with output changes. Their predictability makes them valuable for applications requiring straightforward control, such as traditional industrial processes.
On the other hand, non-linear control systems handle complexities where relationships between inputs and outputs aren't directly proportional. They are crucial in applications that require advanced responses, particularly in robotics and aerospace where varying conditions frequently arise. While non-linear systems offer the advantage of higher performance in complex scenarios, they come with increased design challenges and computational requirements.
Both types of control systems play a pivotal role in defining the parameters of control integrators, ensuring that the systems can operate effectively under varied conditions.
In summary, the fundamentals of control systems set the stage for understanding how control integrators enhance functionality across various applications, ultimately impacting efficiency and performance in modern systems.
Types of Control Integrators
Control integrators are pivotal in shaping the efficacy and reliability of modern control systems. Each type has its own set of principles and benefits catering to diverse applications and operational demands. Understanding the nuances among Proportional-Integral-Derivative (PID) Integrators, Model Predictive Control (MPC), and Digital Control Integrators is essential for optimizing system performance. By evaluating these types, we can grasp their unique contributions and the contexts in which they shine.
Proportional-Integral-Derivative (PID) Integrators
PID Integrators are the bread and butter of control systems, widely appreciated for their relative simplicity and robustness. This integration technique is based on three fundamental components: proportional, integral, and derivative control. The proportional element adjusts the output proportionally to the error, while the integral aspect computes the cumulative error over time, allowing for corrections that eliminate steady-state error. The derivative component predicts future error based on its rate of change, providing a predictive element that helps stabilize the system.
The benefits of PID Integrators are manifold:
- Simplicity: Easy to understand and implement, making them a go-to choice for many control engineers.
- Versatility: Applicable across various industries, from automotive to aerospace.
- Effectiveness in Disturbance Rejection: Good at maintaining performance in the presence of disturbances, ensuring smoother operations.
However, it's not without challenges. Tuning PID parameters can be a bit of a head-scratcher, often requiring trial and error, and in more complex systems, they can struggle with issues like overshoot and oscillation. Achieving that delicate balance is the art and science of control systems design.
Model Predictive Control (MPC)
Moving beyond traditional methods, Model Predictive Control offers a sophisticated approach by leveraging a dynamic model of the system. Instead of merely reacting to changes or errors, MPC uses an optimization algorithm that looks into the future, predicting possible future states and taking pre-emptive actions. This characteristic allows it to handle multi-variable control problems efficiently, a feat often beyond the capacity of PID controllers.
Key features of MPC include:
- Optimization: Continuously optimizes control moves based on predicted future outcomes, which enhances performance.
- Constraint Handling: Effectively enforces constraints on inputs and outputs, making it suitable for applications that require strict adherence to operational limits.
- Versatile Applications: Widely used in chemical processing, energy management, and robotics, where the ability to forecast and optimize is crucial.
Nonetheless, MPC also comes with its own set of hurdles, chiefly its computational intensity. The need for a robust model and real-time processing can present challenges in systems with limited computational resources.
Digital Control Integrators
In an age where digital technologies dominate, Digital Control Integrators represent the natural evolution in control system integration. These systems utilize digital signals and systems, enabling the automation and optimization of processes through advanced software algorithms. They excel in their ability to integrate with modern sensors and IoT devices, paving the way for smart systems that can learn and adapt over time.
Some striking advantages of Digital Control Integrators are:
- Precision and Flexibility: They offer precise control with the adaptability to change parameters as needed.
- Integration with Modern Interfaces: Interfaces well with databases and software platforms, facilitating data-driven decision-making.
- Real-Time Analytics: Ability to monitor and analyze large data streams, contributing to predictive maintenance and efficiency improvements.
Of course, as with any innovation, they come with challenges, including the complexity of implementation and the potential for cybersecurity risks. Organizations need to be mindful of these elements when deploying digital systems.
Control integrators, whether PID, MPC, or digital, are fundamental to steering complex systems towards efficient operation. Their unique characteristics cater to specific challenges across industries, ensuring that systems remain responsive, reliable, and robust.
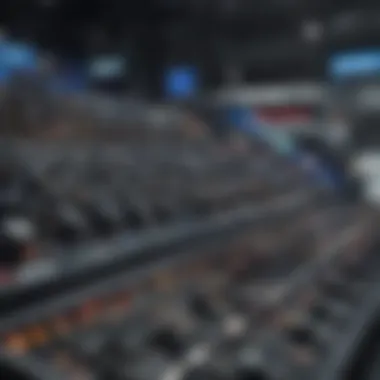
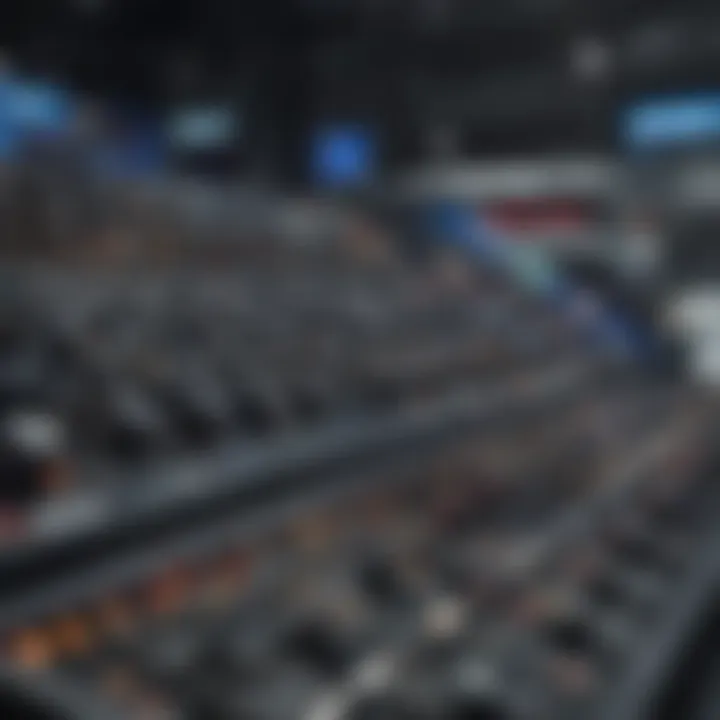
Application Domains of Control Integrators
In the realm of modern systems, control integrators hold pivotal positions across various industries. It's essential to appreciate the practical applications of these systems because they are not just theoretical constructs; they are foundational elements that drive efficiency, safety, and responsiveness in diverse domains. The significance of control integrators extends beyond mere automation—they enhance productivity, enable intricate process control, and support sustainable practices. Each industry benefits distinctly, making it critical to explore how control integrators are integrated into different applications.
Manufacturing and Automation
Manufacturing stands as a primary domain where control integrators demonstrate outstanding capability. These systems streamline production processes, ensuring that operations run as smoothly as a well-oiled machine. For example, using Proportional-Integral-Derivative (PID) controllers in automated machinery helps maintain consistent output quality by adjusting variables like speed and temperature in real-time. This adaptability significantly reduces downtime, while also increasing throughput.
Moreover, integrating these systems with advanced robotics amplifies their effectiveness. The interchange between control integrators and robotic arms in assembly lines creates a synchronized effort that not only improves precision but also optimizes labor efficiencies. The implementation of Industry 4.0 concepts further enhances this by incorporating data analytics, allowing manufacturers to predict failures before they occur, thus saving costs and resources.
Environmental Control Systems
When it comes to managing our environment, control integrators are indispensable. They play an integral role in environmental control systems, regulating various factors such as air quality, waste management, and resource consumption. For instance, smart thermostats adjust heating and cooling in buildings based on occupancy and external weather conditions. This can lead to substantial savings in energy use and a reduced carbon footprint.
Environmental impact is increasingly critical, and control integrators furnish solutions that help mitigate adverse effects. Systems that monitor emissions from industrial sites apply feedback loops to ensure compliance with environmental standards. By harnessing data in real time, these controls facilitate swift adjustments that protect both public health and the environment. A sophisticated approach, such as Model Predictive Control (MPC), leverages predictive algorithms to understand potential environmental impacts and take proactive measures, fostering sustainability.
Transportation Systems
Transportation is another prime area where control integrators enhance efficiency and safety. The rise of smart transportation systems incorporates advanced algorithms and real-time data to optimize traffic flow and reduce congestion. For example, traffic lights equipped with integrated controls can adjust their cycles based on current traffic conditions, leading to smoother commutes.
Additionally, autonomous vehicles rely heavily on integrators for navigation and safety. They utilize a combination of sensors and controllers to maintain optimal performance—calculating routes, avoiding obstacles, and ensuring passenger safety. The implications of these technologies are profound in reducing accidents and enhancing reliability in public transit systems, showcasing how integral control systems are in modern transportation scenarios.
Building Management Systems
In building management, control integrators synchronize various systems for improved occupant comfort and energy efficiency. Lighting, heating, ventilation, and air conditioning systems can all be seamlessly managed through a centralized control system. For example, an intelligent building management strategy may adjust lighting in response to natural daylight, compressing energy use without sacrificing comfort.
Moreover, integrating IoT devices allows for real-time monitoring and managing of building conditions. Sensors can identify disturbances in air quality or temperature and adjust settings automatically, ensuring a pleasant environment. Such proactive approaches not only enhance the occupant experience but also extend the longevity of building systems and lower operational costs. As we embrace smart buildings, the role of control integrators in achieving these efficiencies is becoming even more critical.
Control integrators are not merely supporting actors; they are the backbone of modern systems across key industries.
As we consider these application domains, it's evident that the incorporation of control integrators influences efficiency, sustainability, and overall effectiveness in operations. Whether it's optimizing manufacturing lines or ensuring environmental compliance, the role of these systems cannot be overstated.
Design Considerations for Control Integrators
Designing control integrators involves a myriad of factors that can make or break the effectiveness of these systems. This particular segment focuses on the critical design considerations that should be taken into account to optimize the functionality and reliability of control systems within various industries.
Stability and Performance Metrics
Stability is at the heart of control systems; it ensures that the system responds predictably. When designing a control integrator, it's vital to include stability analysis. This involves understanding how the system reacts to different inputs and perturbations. Utilitarian metrics like overshoot, settling time, and steady-state error help evaluate how well the system meets desired performance levels.
For instance, consider a temperature control system in a manufacturing plant. If the control integrator isn't stable, even a small change in temperature could lead to significant swings, causing equipment to malfunction or produce poor-quality products. Thus, establishing appropriate performance metrics is essential—even a precise temperature reading may not be beneficial if the control doesn't stabilize quickly.
Implementation Challenges
There are numerous hurdles encountered during the implementation of control integrators. Recognizing these challenges early on can save time and resources.
System Complexity
One characteristic that defines system complexity in control integrators is the multitude of components and interactions involved. Modern control systems might incorporate a blend of hardware and software that manages several operational facets. This intricate web can become an uphill battle if clarity and organization aren't maintained.
For example, integrating a PID controller into an existing automation system can be straight forward, but when you have various sensors, actuators, and data inputs flowing through multiple pathways, things can go awry swiftly. The complexity might not only lead to design delays, but can also cause unforeseen operational issues if not managed well. That said, complexity does provide opportunities for enhanced functionality if appropriately navigated.
Scalability Issues
As system demands increase, scalability becomes a significant concern. When designing control integrators, it's necessary to ensure that the system can grow seamlessly without major overhauls. Scalability relates to how well a system can adapt to increased loads or changes in operational needs without sacrificing performance.
A unique feature of scalability issues in control systems is that they often require additional resources, such as more processing power or memory, to handle greater loads. If developers overlook this aspect during design, their control integrator can end up becoming a bottleneck rather than a solution. In practice, this means a scalable design allows for quicker response times and greater flexibility, but getting there may require more investment upfront.
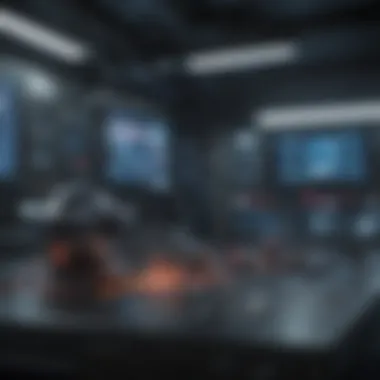
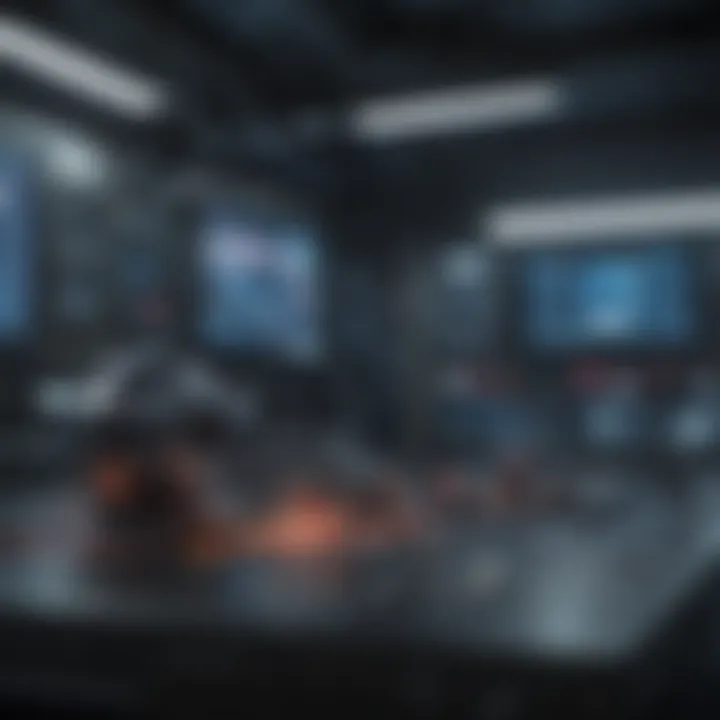
"The key is striking a balance between immediate operational effectiveness and long-term adaptability."
Recent Advancements in Control Integration Techniques
The realm of control integration techniques has seen significant evolution in recent years, influenced by the broader digital transformation occurring across various sectors. These advancements not only enhance operational efficiencies but also open the door to innovative ways to tackle complex systems challenges. The integration of cutting-edge technologies, particularly artificial intelligence and the Internet of Things, has reshaped how control systems function and interact with their environments. Let's delve into these two pivotal areas that are propelling the field forward.
Artificial Intelligence in Control Systems
Artificial intelligence (AI) is often regarded as a game changer in control systems. The integration of AI allows for real-time decision-making based on massive datasets and patterns that are typically beyond human comprehensibility. This is particularly beneficial because control systems, by their nature, require rapid adjustments to maintain optimum performance.
- Adaptive Learning: AI algorithms can learn from previous operating conditions, allowing systems to adapt without the need for constant reprogramming. This adaptability is crucial in environments where operating conditions change frequently, such as manufacturing plants or smart grids.
- Predictive Maintenance: By analyzing historical data, AI can predict potential failures before they occur, minimizing downtime and repair costs. For instance, AI can process sensor data from machinery to forecast when a machine is about to fail and trigger maintenance before the problem escalates.
- Enhanced Control Algorithms: AI can enhance traditional control strategies like PID by optimizing the control parameters dynamically. This results in improved stability and performance over classical methods, particularly in nonlinear systems.
"The incorporation of AI in control systems marks a significant shift, transforming systems into intelligent entities capable of self-optimization."
IoT and Remote Control Integration
The Internet of Things (IoT) underscores a fundamental change in how control systems are implemented and managed. With IoT, control systems are interconnected, allowing remote access and control over various devices and sensors via the Internet. This integration has several remarkable implications.
- Data Collection: IoT devices collect vast quantities of data that can be aggregated and analyzed to refine control strategies further. In agriculture, for example, IoT sensors can monitor soil moisture levels and automatically adjust irrigation systems accordingly. This situation illustrates how the seamless flow of information can enhance efficiency and resource usage.
- Remote Monitoring and Management: With IoT, professionals can monitor and control systems from virtually anywhere. For instance, energy management systems can adjust energy consumption based on real-time usage data, even allowing users to manage their electricity from their smartphones. This flexibility is particularly important for industries where time is of the essence and rapid responses are critical.
- Scalability: IoT technology facilitates the easy scaling of systems. Connecting additional sensors or devices can be done without overhauling existing control systems, providing an avenue for growth and adaptation to new operational demands. Industries can expand their control capabilities as needed without extensive reengineering.
In summary, the recent advancements in control integration techniques, especially through the lens of artificial intelligence and IoT, mark a significant breakthrough. These developments allow systems to be more adaptive, efficient, and responsive, thus enhancing performance across various applications and industries.
Future Trends in Control Integration
The realm of control integration is fast evolving, and anticipatin’ those changes is crucial in navigating the complexities of modern systems. Understanding future trends not only marks the journey of technological advancements but also helps industries adapt to shifting paradigms in efficiency and operational performance. As automation and connectivity grow in prominence, control integrators are positioned at the heart of these developments, providing the backbone for smarter, more responsive systems.
Evolution of Control Algorithms
Control algorithms are like the brains inside a control system, guiding how it reacts to varying inputs. The past few years have seen a significant leap in the sophistication and capabilities of these algorithms. Traditional control methods, while reliable, have often struggled to adapt dynamically to the challenges presented by modern systems.
- Adaptive Algorithms: The development of adaptive algorithms marks a significant turning point, as these allow systems to self-tune based on real-time data. For example, in a manufacturing setting, an adaptive algorithm can modify the operation parameters of machinery based on feedback from production rates or quality assessments. This means less downtime and more product consistency.
- Machine Learning: The integration of machine learning techniques into control algorithms is another breakthrough. Consider how a smart thermostat learns a household's temperature preferences over time. Similarly, in industrial applications, algorithms can predict and mitigate potential failures by analyzing historical operational data. This ability to foresee issues before they escalate into major problems can save both time and substantial costs.
The influence of these evolving control algorithms cannot be overstated. They enhance responsiveness, improve accuracy, and have the potential to revolutionize the efficiency of control systems across various industries.
Impact of Quantum Computing
As we peer into the future of control integration, the impact of quantum computing looms large on the horizon. While still in its nascent stages, quantum computing holds the promise of performing computations that are currently deemed impossible within a feasible timeframe using classical computers. This potential transformation in how we process information could lead to groundbreaking advancements in control systems.
With quantum computers, tasks such as optimization and simulation—crucial for intricate control systems—could become significantly more manageable. Imagine a logistics company utilizing a quantum computer to optimize delivery routes in real-time based on fluctuating traffic conditions and fuel consumption. Harnessing the power of quantum systems could lead to unprecedented efficiency and reduced operational costs.
Moreover, the ability to analyze vast datasets instantly could result in more sophisticated predictive control. This means that systems may not only respond to real-time data but also anticipate future states, leading to a more proactive approach in control integration.
"Quantum computing could revolutionize traditional control integration, offering solutions that were thought too complex for real-time processing."
In summary, the future trends in control integration are set to redefine how we engineer and interact with control systems. From the evolution of algorithms that learn and adapt in real-time to the stunning possibilities introduced by quantum computing, the landscape will continue to change, requiring professionals in the field to remain vigilant and open to innovation. As these trends unfold, staying ahead will be essential for maximizing the impact and utility of control integrators in modern systems.
Epilogue
In a world where efficiency and precision dictate operational success, the role of control integrators stands pivotal. Their influence permeates various sectors, enhancing productivity and enabling systems to adapt swiftly to changes. This article has illuminated the intricate interplay between control integrators and modern systems, underscoring their necessity in achieving seamless operations.
Summary of Key Points
- Significance of Control Integrators: Control integrators play a crucial role across industries by automating processes and optimizing performance. They allow systems to respond effectively to disturbances or changes in environmental conditions.
- Types and Applications: Various control integration methodologies, ranging from PID integrators to model predictive control, are tailored for different applications—whether it's in manufacturing automation or transportation systems.
- Recent Technological Advances: Innovations such as AI integration and IoT have revolutionized how these systems operate, pushing the boundaries of efficiency further.
- Future Directions: The evolving landscape of control technology promises to unveil new strategies, particularly with the advent of quantum computing, enhancing predictive capabilities and operational effectiveness.
"Control integrators not only streamline processes but also empower industries to flourish in an increasingly complex digital age."
Call to Action for Future Research
The exploration of control integrators is far from complete, and future research should delve deeper into several important aspects:
- Interdisciplinary Approaches: Encouraging collaboration among engineers, data scientists, and domain experts can lead to innovative control strategies and more effective systems.
- Integration of Emerging Technologies: Researching how evolving technologies like machine learning and quantum computing can be synergistically applied to improve control systems will be vital.
- Environmental Impacts: As sustainability becomes paramount, studying how control integrators can contribute to greener operations should be prioritized.
- Customization and Scalability: Investigating user-specific customization in control integration could improve efficacy in diverse applications, making systems more adaptable than ever before.
As we step further into the realm of advanced control systems, your contributions in these areas could illuminate the path ahead.