Heat Formed Plastic Sheets: Properties and Innovations
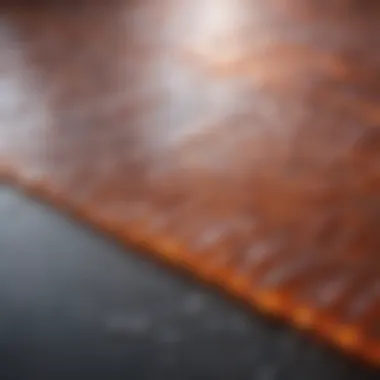
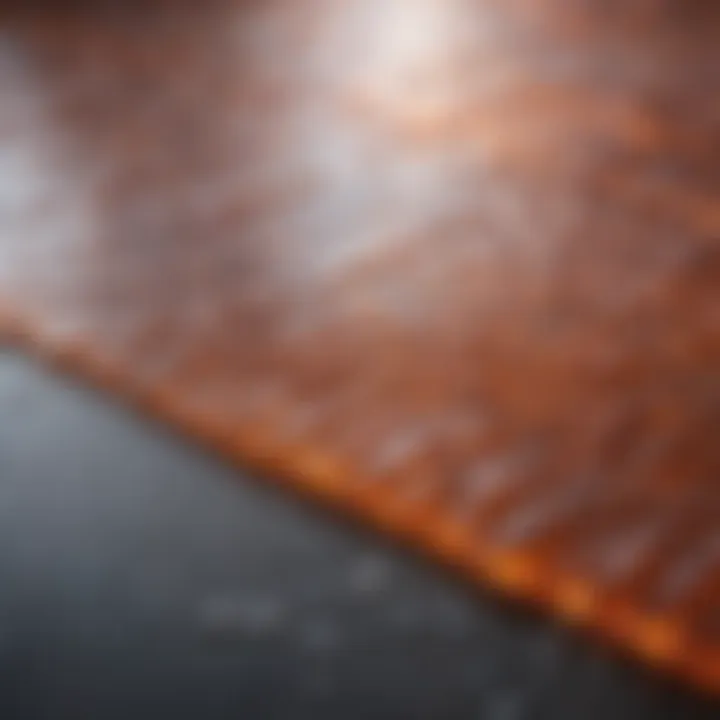
Intro
In an ever-evolving landscape of materials science, heat formed plastic sheets have emerged as a significant asset with versatile applications. These thermoplastics are not just mere plastic sheets, but structured solutions that enhance efficiency and effectiveness across various industries. Understanding their properties, applications, and the innovations in their production can seem daunting, but letβs unpack this fascinating subject step by step.
By delving into the characteristics of heat formed plastics, one can appreciate their importance in the contemporary manufacturing environment. With a wide variety of thermoplastics available, each presents unique thermal properties and molding capabilities. This exploration will not only provide insights into their practical uses but also address sustainability innovations that help mitigate environmental impacts.
Research Context
Background Information
Plastic sheets molded through heat processing offer a level of customization and durability that makes them attractive for multiple sectors. The process involves heating a thermoplastic material until it is soft enough to be formed into specific shapes, after which it is cooled to solidify. This versatile molding process allows designers and engineers to create products that meet specific needs while providing durability. Depending on the type of thermoplastic usedβsuch as polycarbonate or PETβeach material brings a set of distinct thermal and mechanical properties to the table.
Importance of the Study
The significance of studying heat formed plastic sheets stretches beyond mere academic interest. For industries including automotive, aerospace, and consumer goods, understanding these materials leads to better product performance and enhanced sustainability practices. In addition, as global attention shifts toward eco-friendly alternatives, innovations in the production and application of these plastics are becoming increasingly relevant. By disassembling the intricate dynamics of heat formed plastic sheets, we can reveal not just their present potential but also their future possibilities.
"In a world where sustainability is becoming non-negotiable, the evolution of heat formed plastics could redefine the manufacturing industry."
Discussion
Interpretation of Results
Examining the properties of heat formed plastic sheets shows their clear advantages over other materials. These plastics display remarkable impact resistance, elasticity, and clarity, especially in products like protective coverings and custom plastic enclosures. The results from various tests indicate that, compared to traditional materials, heat formed plastics have a lower weight, which translates into savings on materials and transportation costs. Moreover, using heat formed plastics can lead to shorter production times due to the efficiency of their molding processes.
Comparison with Previous Research
Previous research consistently indicates that heat formed plastics not only provide benefits in manufacturing but also show promise in reducing environmental footprints. Innovations, such as incorporating biodegradable additives in the plastic matrix or utilizing recycled materials, highlight the industry's shift toward sustainability. A contrast to studies published even a decade ago reveals substantial progress; it seems that what was once considered a rigid domain has now morphed into an arena ripe for innovation and responsible usage.
This journey through the unique properties, alignments with sustainability, and practical applications of heat formed plastic sheets is just the beginning. As we continue to explore, the implications and advancements in this field become ever clearer, mapping a future where material science meets environmentally conscious solutions.
Prelude to Heat Formed Plastic Sheets
In recent years, heat formed plastic sheets have emerged as a crucial component across a vast array of industries. Their flexibility, resilience, and adaptability make them a preferred choice for applications ranging from industrial machinery to everyday consumer products. Understanding the unique properties and applications of these sheets opens avenues for innovation and efficiency, making it imperative to delve into their significance.
Definition and Overview
Heat formed plastic sheets are materials that have been molded into desired shapes through the application of heat and forming techniques. This process allows for a variety of plastic types to be transformed into sheets that exhibit distinct characteristics based on the thermoplastic selected. Essentially, the heat does not permanently change the chemical structure of the plastic; instead, it enables it to become malleable enough for shaping.
Here are some key properties of heat formed plastic sheets:
- Durability: These sheets resist impact and are capable of enduring harsh conditions.
- Lightweight: Their reduced weight compared to metals allows for easier handling and installation.
- Versatility: With a range of types available, they can fulfill diverse engineering and aesthetic requirements.
The importance of these sheets becomes evident when considering their ubiquitous presence in todayβs market. Any dairy aisles in supermarkets or even the housing of electronic devices may hide components created from heat formed plastics.
Historical Context
The journey of heat formed plastic sheets dates back to the mid-20th century, when the development of synthetic polymers began to revolutionize material sciences. Early pioneers such as John Wesley Hyatt paved the way by inventing celuloid, a material used in billiard balls and photographic film. As manufacturers began to explore the capabilities of plastics, innovations in processing techniques followed suit.
By the 1960s, advancements in polymer chemistry led to a more significant understanding of thermoplastics and their applications. Companies like Royalite and Mitsubishi Chemical pushed boundaries further by refining thermoforming methods, paving the way for mass production.
Fast forward to today, and you see a landscape where heat formed plastic sheets are not merely an industrial byproduct but a vital part of product design and usability across sectors. The adaptability of these materials has made it possible for creators to push the envelope in design and functionality, revolutionizing how products are conceptualized and executed.
"The evolution of heat formed plastics is a testament to human ingenuity, reflecting our continuous quest for better materials and efficient processes."
In summary, the exploration of heat formed plastic sheets encompasses their broad definition, the historical progress in their manufacture, and their enduring relevance in modern manufacturing and design. No matter the industry, the heat formed plastic sheets stand as pillars of innovation and utility.
Understanding Thermoplastics
Thermoplastics are a crucial component in the realm of heat formed plastic sheets. Understanding their unique characteristics not only sheds light on the practical applications but also emphasizes how they impact the production and functionality of various products. Itβs essential to know that thermoplastics can be repeatedly heated and reshaped without losing their inherent properties. This makes them incredibly versatile in manufacturing processes. In this section, we will look closer at the different types of thermoplastics and their thermal properties, which are vital in determining their suitability for specific applications.
Types of Thermoplastics
Polypropylene
Polypropylene is one of the most widely used thermoplastics due to its low density and high chemical resistance. Its contribution to the creation of rigid packaging materials, automotive parts, and consumer goods cannot be overstated. One of the key characteristics of polypropylene is its excellent fatigue resistance, which allows products such as hinges and living hinges to operate without failure. This feature makes it a beneficial choice in applications requiring durability and flexibility, particularly in products like food containers and automotive components.
However, while polypropylene boasts many advantages, it does have some disadvantages in terms of UV stability, making it less ideal for outdoor applications unless treated or combined with other materials.
Polyethylene
Polyethylene stands as one of the most common thermoplastics in the world. It is well-regarded for its lightweight properties and chemical resistance. The primary contribution of polyethylene within this article lies in its versatility in applications ranging from packaging to construction. The key characteristic of this thermoplastic is its ability to be produced in various densitiesβhigh-density polyethylene (HDPE) and low-density polyethylene (LDPE)βallowing it to cater to different needs.
The unique feature of polyethylene is its non-toxic nature and recyclability, which offers solid advantages for companies seeking to reduce their environmental footprint. Yet, it does come with its weaknesses, as its tensile strength is generally lower than other plastics, limiting its use in high-stress applications.
Polystyrene
Polystyrene is another significant thermoplastic, known for its rigidity and clarity. Often used in foam products and packaging materials, its contribution to safety and insulation is important in sensitive applications like protective packaging. A key characteristic of polystyrene is its excellent molding capability, making it easy to produce intricate shapes and designs in products such as disposable cutlery and plastic models.
However, this material does have downsides. Polystyrene is not as impact-resistant as other thermoplastics, which can make it prone to cracking. Furthermore, its environmental impact, due to difficulties in recycling, poses a serious concern in the long term.
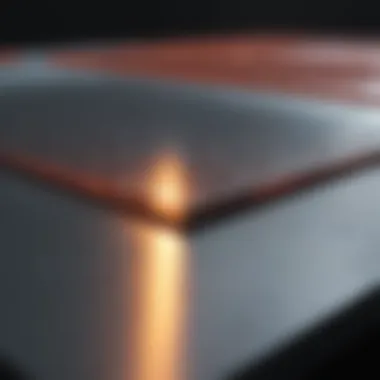
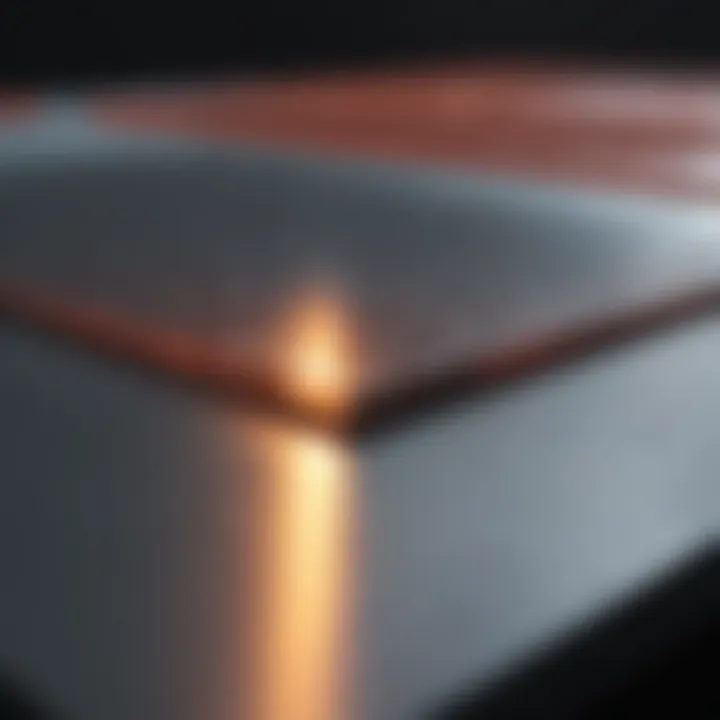
Polyvinyl Chloride
Polyvinyl chloride, commonly known as PVC, is a thermoplastic with a significant market presence. Its durability and versatility make it a popular choice in construction, plumbing, electrical cable insulation, and even toys. The notable characteristic of PVC is its strong resistance to environmental degradation, which contributes to its long lifespan in applications where durability is paramount.
A unique feature of PVC is that it can be made flexible when combined with plasticizers, allowing for the creation of various products like flexible tubing and flooring materials. However, the disadvantages include potential health hazards associated with its production and disposal, which have led to increased scrutiny and calls for more sustainable alternatives.
Thermal Properties
Melting Point
The melting point is a critical factor affecting the performance of thermoplastics and, consequently, the effectiveness of heat formed plastic sheets. It defines the temperature range within which a plastic can be processed and reformed. For example, having a well-defined melting point allows manufacturers to design products that can withstand specific heat conditions without deforming. This is particularly beneficial in applications where materials are subjected to varying temperatures, such as automotive parts and appliance housings.
Understanding the melting point of different thermoplastics helps to select the appropriate material for specific applications, saving costs and reducing waste in production processes.
Thermal Conductivity
Thermal conductivity is another essential property that significantly impacts the use of heat formed plastic sheets. It measures how well a material can conduct heat. In applications where heat retention or dissipation is crucial, selecting a thermoplastic with the right thermal conductivity can enhance overall product performance. For instance, in electronic devices, materials with low thermal conductivity are preferred to protect sensitive components from overheating.
Understanding this property allows industries to make informed decisions when sourcing materials, leading to products that are not only safer but more efficient in their intended use.
Heat Resistance
Heat resistance is vital for thermoplastics, determining their ability to maintain structural integrity at elevated temperatures. For industries such as aerospace and automotive, this property is non-negotiable. The key characteristic of heat resistance is that it enhances the longevity of products, especially in high-heat environments. By recognizing the heat resistance capabilities of various thermoplastics, developers can optimize their designs accordingly.
Advancements in material sciences continually push the boundaries of heat resistance, leading to innovations that can potentially redefine how these materials are used. Consequently, this property is indispensable for ensuring that products can endure for extended periods without losing performance.
The Process of Heat Forming Plastic Sheets
Understanding the process of heat forming plastic sheets is crucial in the world of manufacturing and product design. This process not only allows for the transformation of raw thermoplastic material into usable products but also plays a pivotal role in the efficiency and economics of production. The significance of mastering heat forming techniques cannot be overstated, especially when it comes to enhancing product performance, reducing waste, and optimizing design flexibility.
The application of various heat forming methods varies significantly, influencing the end quality and usability of the products created. As such, recognizing the distinct techniques and the corresponding equipment is essential for professionals seeking to leverage these technologies in their projects.
Heat Forming Techniques
Thermoforming
Thermoforming is a fundamental technique where a sheet of thermoplastic is heated until it becomes pliable. Once in this softened state, the material is shaped into a mold to create a specific product. One of the key characteristics of thermoforming is its ability to produce complex shapes with pronounced detail, making it a favored technique in industries ranging from packaging to automotive parts.
What sets thermoforming apart is its versatility. This method is often seen as a go-to choice because it can accommodate various materials and thicknesses, allowing for a wide range of applications. However, one particular feature that highlights its utility is the ease of production runs. While it can be cost-effective for short runs, it may not be the best option for high-volume scenarios compared to other methods.
Advantages of thermoforming include:
- Design Flexibility: Ideal for intricate shapes and custom designs.
- Material Efficiency: Can often reuse excess materials left after the forming process.
Disadvantages may include:
- Limitations on Material Choices: Not all thermoplastics are suitable for this technique.
- Higher Setup Time: Molds need to be created specifically for each product.
Vacuum Forming
Vacuum forming is a specialized subtype of thermoforming where the heated thermoplastic sheet is drawn onto a mold by creating a vacuum. This technique is widely recognized for its simplicity and effectiveness in producing shape-well products with minimal material wastage. Key to vacuum forming is the combination of pressure and heat, which ensures that the material snugly fits the design of the mold it is placed over.
One reason vacuum forming remains popular is its accessibility for smaller production runs. It's often chosen for its cost-effectiveness, especially for prototypes and small-batch productions. A unique feature is the ability to create lightweight parts, which is particularly advantageous in automotive sectors where reducing weight can contribute to improved fuel efficiency.
Benefits of vacuum forming include:
- Cost-Effective Prototypes: Ideal for initial designs and testing phases.
- Fairly Rapid Production: Shortened lead times compared to other methods.
On the downside, it does have limitations:
- Thickness Constraints: Generally, it works best with thinner sheets.
- Surface Detail: May not capture minute details as well as some competing processes.
Pressure Forming
Pressure forming elevates the vacuum forming technique by introducing an additional positive pressure to enhance material flow into the mold. This method is characterized by its capacity to produce parts that have far superior detail and surface finish compared to its vacuum-forming counterpart. It's particularly effective when high-quality aesthetic finishes are required.
A key characteristic of pressure forming is the speed at which it can produce high-quality products, making it a beneficial technique particularly in the fast-paced production environments of the consumer goods sector. This method is often seen as favorable for industries that need both quality and quantity; the unique feature here is the enhanced capabilities to create thicker or sturdier parts without compromising on detail.
The advantages of pressure forming include:
- Superior Quality: Capable of producing intricate designs and smooth finishes.
- Versatile Material Application: Works well with various types of thermoplastic materials.
However, one must also consider its disadvantages:
- Higher Costs: More expensive due to the need for more sophisticated equipment.
- Longer Setup Time: Requires more time and precision to prepare molds properly.
Equipment and Technology
Forming Machines
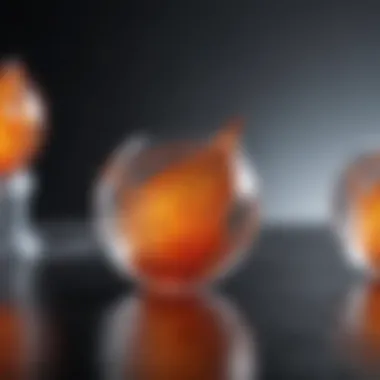
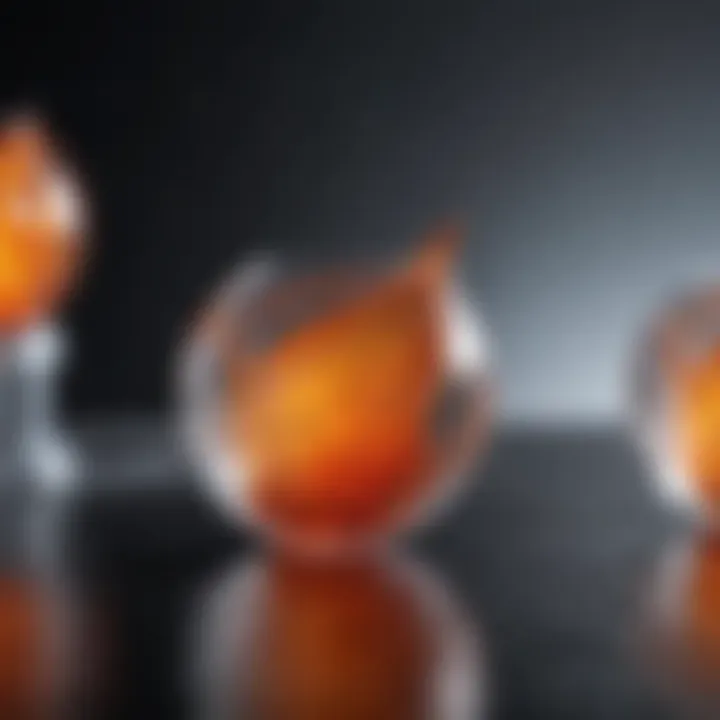
Forming machines are the backbone of any heat forming operation. The technology employed in these machines is continuously evolving, allowing for greater efficiency and precision. A primary characteristic of forming machines is their ability to handle diverse materials and create parts in various shapes and sizes, which is crucial in a rapidly changing market.
Choosing to invest in advanced forming machines can lead to substantial improvements in production capacity and product yield. These machines often come equipped with both manual and automated settings, catering to a range of operational scales. A notable benefit is how they can drastically reduce production time through automation features.
However, disadvantages also exist:
- Initial Investment: The cost of high-tech forming machines can be significant.
- Operator Skill Requirement: Staff needs training to operate advanced machines effectively.
Temperature Control Systems
Temperature control systems play an integral role in heat forming processes, ensuring that the plastic sheets reach the optimum temperature for forming. The critical aspect here is maintaining consistent heat levels to achieve uniform product quality. Fluctuations in temperature can lead to defects, highlighting the necessity for reliable temperature control.
These systems are indispensable for ensuring the best performance of the heat forming operation, enhancing both the quality of the end product and the efficiency of the process overall. They offer features such as real-time monitoring, allowing for rapid response to any variations.
Advantages include:
- Consistency: Maintains optimal temperature throughout the forming process.
- Reduced Scrap Rates: Minimizes the occurrences of material wastage due to temperature errors.
On the flip side, the drawbacks include:
- Complexity: The technology can be intricate and require extensive understanding.
- Maintenance Needs: Regular check-ups and calibrations may add time and costs to production schedules.
"The process of heat forming plastic sheets is not merely about molding materials; it embodies the essence of innovation and adaptability in modern manufacturing."
As we've seen, the process of heat forming plastic sheets integrates various techniques and technologies that are essential for producing quality products across industries. The careful selection of methods and equipment can have profound implications on product quality, production efficiency, and overall operational costs.
Applications of Heat Formed Plastic Sheets
Heat formed plastic sheets have found their way into numerous sectors, making them integral to modern production and design. These materials offer versatility and efficiency, which are core to various applications. Their lightweight characteristics, ease of fabrication, and ability to conform to specific shapes allow for innovative designs across industries. As more organizations seek to enhance their product lines while simultaneously pursuing sustainability, heat formed plastic sheets become increasingly relevant. They provide optimal solutions to balance cost, performance, and environmental impact.
Industrial Uses
Aerospace
In the aerospace industry, heat formed plastic sheets play a foundational role. These materials need to adhere to strict weight and performance standards, and heat formed options such as polycarbonate and acrylic stand out due to their high strength-to-weight ratio. This not only contributes to fuel efficiency but also enhances safety without compromising structural integrity. Aerospace companies consistently rely on these sheets for applications ranging from cockpit displays to cabin interiors, making them critical in manufacturing lightweight components.
One unique aspect of using heat formed plastics in aerospace is their resistance to the harsh environmental conditions experienced at high altitudes. This characteristic makes such materials popular, though one should also consider their temperature susceptibility during extreme conditions. Nonetheless, the benefits they provide in terms of performance and weight savings make them a prime choice.
Automotive
The automotive sector is another significant arena for heat formed plastic sheets. This industry depends heavily on materials that are not only lightweight but also sturdy enough to endure various stresses. Heat formed plastics such as ABS (Acrylonitrile Butadiene Styrene) are embraced for many interior and exterior applications, ranging from dashboards to bumpers. Their ability to retain shape while bearing impact is vital for vehicle safety and aesthetics.
Moreover, a unique feature of heat formed sheets in this context is the ability to be molded into intricate designs that appeal to consumers. This flexibility enables manufacturers to differentiate their products without incurring hefty costs. However, it should be noted that while these materials may offer impressive durability, they can sometimes lack the same temperature resilience as metals, necessitating careful consideration during design.
Packaging
When it comes to packaging, heat formed plastic sheets are revolutionizing storage and transportation. Their transparency and sealability enhance product visibility while ensuring freshness and protection. For instance, vacuum-formed trays for food products are a common application that highlights the benefits of using these materials. Not only are they lightweight, but they also often provide a barrier against moisture and contaminants, which is critical in this domain.
Their characteristic of being easily customizable means that packaging can be designed to fit specific product shapes, optimizing space and reducing waste. However, challenges remain in ensuring that these plastics are recycled properly post-use, as contamination can lead to issues in the recycling stream. On the whole, the efficiency and practicality of heat formed plastic sheets in packaging give businesses a competitive edge.
Consumer Products
Kitchenware
Heat formed plastics are a popular choice for kitchenware, providing safe, durable, and aesthetically pleasing options for consumers. Products like containers, utensils, and serving dishes are often crafted from materials such as polypropylene. The advantage of using these materials lies in their ability to withstand thermal extremesβallowing for microwave use and dishwasher safety, which are paramount for modern cooking.
In addition to durability, a unique feature of heat formed kitchenware is its lightweight nature, making them easy to handle. With an increasing focus on sustainable products, many manufacturers are exploring biodegradable alternatives, positioning heat formed plastics as a leading choice in this sector.
Toys
The toy industry benefits greatly from heat formed plastic sheets, which allow for the creation of vibrant and intricate designs that appeal to children of all ages. Many toys are made from high-quality thermoplastics, narrowing the gap between functionality and creativity. An important aspect here is safety; heat formed plastics can be engineered to be non-toxic and robust, ensuring they withstand rough handling.
Additionally, the adaptability of these materials means they can easily be molded into various shapes and styles, increasing their market appeal. However, there's a growing need for manufacturers to balance creativity with environmental mindfulness, pushing the industry towards more sustainable practices.
"The role of heat formed plastic sheets in bridging functionality with design across numerous industries cannot be understated. Their lightness, durability, and adaptability present opportunities for innovation that are continually evolving."
Sustainability and Environmental Impact
As our world faces growing concerns about climate change and waste management, the topic of sustainability in materials science has become increasingly vital. The manufacture and disposal of plastic products have significant implications for the environment, particularly when it comes to heat formed plastic sheets.
These sheets are known for their versatility and wide-ranging applications across industries. However, the sustainability of such materials is critical for addressing environmental challenges. The principles of sustainability dictate that any material used should minimize waste and maximize efficiency. This leads to responsible production, reduced carbon footprints, and sustainable practices. Let's peel back the layers to understand how heat formed plastic sheets contribute to or detract from these goals.
Recycling Practices
Closed-Loop Systems
A closed-loop system refers to a process where waste materials are recycled back into the production process. This keeps materials in circulation, reducing the need for new raw materials and minimizing waste. In the context of heat formed plastic sheets, implementing closed-loop systems can significantly impact the industry.
Key characteristic: These systems often involve using recycled plastic sheets to create new products, which is an economically viable choice. The benefit of this method is twofold: it conserves resources and lessens the environmental burden associated with traditional plastic manufacturing.
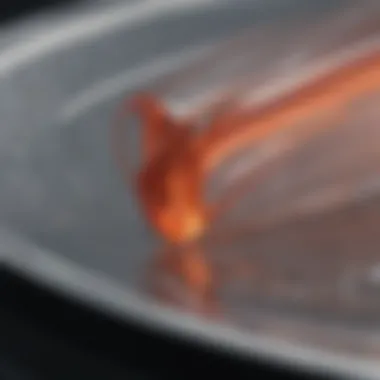
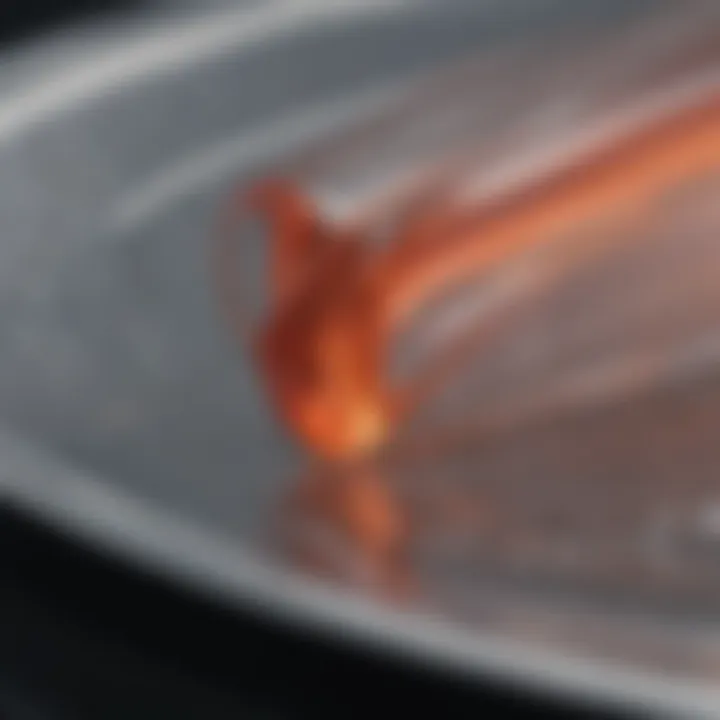
One unique feature of closed-loop systems is their ability to maintain material quality. Unlike linear systems, where materials might degrade over time, closed-loop systems can preserve the integrity of the plastic through multiple processing cycles. However, the initial setup costs can be high, and not all facilities are equipped for such systems. This can present hurdles for smaller manufacturers.
Material Recovery
Material recovery refers to the processes involved in retrieving valuable materials from waste. In the realm of heat formed plastic sheets, this can mean processes that extract usable plastic from discarded products or production scraps. This practice is essential to the overall goal of reducing waste and promoting sustainability.
Key characteristic: The significant aspect here is the potential for recovering materials that otherwise might end up in landfills. Itβs a practical approach, not just beneficial but vital for encouraging a circular economy in the plastic industry.
What sets material recovery apart is its unique capacity to contribute to environmental sustainability while also being often cost-effective. Companies can save on raw material expenses while being eco-friendly. Still, challenges exist, such as contamination in materials which can affect efficiency. When not done properly, it can lead to higher costs and less desirable quality in new products.
Biodegradable Alternatives
The emergence of biodegradable alternatives represents a significant shift in addressing environmental concerns related to traditional plastic. These materials, designed to break down under natural environmental conditions, could be the silver lining in the search for more sustainable solutions to plastic waste.
Unlike conventional plastics which can take hundreds of years to decompose, biodegradable plastics have the potential to alleviate some of the waste management challenges we face today. They can seamlessly integrate into existing waste streams, particularly those already geared toward organic materials.
The use of biodegradable alternatives in heat formed plastic sheets could drastically cut down pollution and landfill impact, serving various industries effectively. However, the current market for biodegradable materials often comes with a higher price tag, and compatibility with existing applications needs careful consideration.
Innovations in Heat Formed Plastic Sheets
The realm of heat formed plastic sheets has seen significant metamorphosis over the years, largely driven by innovations that enhance their properties and versatility. As industries evolve, so do the materials that cater to them, and heat formed plastic sheets are no exception. By refining production techniques and introducing novel materials, the field has opened doors to increased efficiency, functionality, and sustainability. Understanding these innovations is crucial for professionals striving to keep pace with industry developments and to harness these advances in their work.
Emerging Technologies
3D Printing Techniques
One of the most radical contributions to the production of heat formed plastic sheets is the advent of 3D printing techniques. This technology enables the fabrication of complex structures that were nearly impossible with traditional methods. The key characteristic is its capability to create customized components on-demand, effectively reducing waste and promoting sustainability in production.
The beauty of 3D printing lies in its precision. For instance, components can be produced layer by layer, allowing for intricate designs that optimize the use of materials. This is not only beneficial in creating unique items based on specific requirements but also paves the way for innovation in prototype development.
However, this technology does come with some challenges. One notable disadvantage is that 3D printing can often be slower than conventional manufacturing, especially for larger volumes. Additionally, the range of materials compatible with 3D printing can be limited compared to those used in traditional heat forming methods, which may restrict designs based on material properties.
Smart Materials
Following suit, smart materials have begun making waves in the heat formed plastics scene. These are materials designed to respond dynamically to external stimuli β be it temperature, light, or moisture. The standout feature of smart materials is their ability to adapt, which offers several advantages for applications spanning various industries.
For example, smart polymers used in plastic sheets can change shape or properties in response to temperature changes, making them ideal for applications in aerospace where optimizing weight and material use can significantly impact performance. This adaptability makes smart materials a popular choice for innovative product design, providing designers with flexibility that traditional materials lack.
On the downside, the complexity and cost of smart materials can be a double-edged sword. While they bring advanced functionality, their prices can pose a barrier, particularly for smaller manufacturers. Moreover, the integration of such materials into existing production processes might require substantial adjustments, which can be a deterrent.
Future Trends
Looking ahead, the innovations surrounding heat formed plastic sheets are poised to continue evolving. Trends suggest a growing inclination toward sustainability in production, with manufacturers increasingly prioritizing eco-friendly materials and processes. Additionally, as industries move towards automation, we may well see automation technologies that can seamlessly integrate with heat forming processes, leading to enhanced efficiency and reduced production times.
In summary, innovations like 3D printing and smart materials not only enhance the capabilities of heat formed plastic sheets but also drive the industry forward. As development marches on, professionals in the field must remain vigilant, adapting their practices to leverage these advancements effectively, ensuring that they remain at the forefront of change.
Challenges in the Industry
The production and use of heat formed plastic sheets come with a unique set of challenges. Understanding these hurdles is not just about identifying problems; it's about recognizing opportunities for improvement and innovation. The industry faces increasing pressure in terms of quality control and economic sustainability. Addressing these challenges effectively can lead to significant advancements in the field, making it essential to explore these facets thoroughly.
Quality Control Issues
Quality control in the manufacturing process of heat formed plastic sheets is crucial. The integrity of the final product is directly influenced by how well each step of the production is managed. Small deviations during the heat forming process can lead to significant flaws. For instance, inconsistencies in temperature can cause warping or incomplete molding. Keeping a close eye on the process helps ensure that products meet industry standards and consumer expectations.
One effective method for maintaining quality is implementing rigorous testing protocols. This could include:
- Visual Inspection: Examining the finished products for any visible defects.
- Dimensional Checks: Ensuring that the dimensions of molded sheets are within the specified tolerances.
- Material Testing: Conducting tests to assess material properties such as tensile strength and flexural modulus.
Quality assurance not only reduces waste but can also enhance the overall reputation of manufacturers. Adopting advanced technologies like real-time monitoring systems can help catch problems early, saving both time and money in the long run.
Economic Factors
Economic considerations are paramount in the plastics industry, particularly for heat formed sheets. The industry grapples with fluctuating raw material costs, which can impact the pricing and profitability of products. As oil prices fluctuate, so do the costs associated with thermoplastics, often leaving manufacturers in a tight spot.
Moreover, the pressure to keep prices competitive while maintaining quality can lead to difficult decisions on sourcing materials. This situation is further complicated by global supply chain challenges, exacerbated by geopolitical tensions or natural disasters. Companies need to remain agile and plan for contingencies.
- Cost-Effective Alternatives: Exploring different materials that are more economically viable without compromising quality.
- Investing in Efficiency: Upgrading manufacturing equipment can reduce long-term costs through improved energy efficiency and reduced waste.
- Market Trends: Keeping an ear to the ground on consumer preferences, particularly those shifting toward sustainability, can provide insights for new product development.
Ending
The discussion regarding heat formed plastic sheets culminates in an essential synthesis of insights that highlight the profound relevance of this topic. As we peel back the layers, it becomes clear that these materials are not merely utilitarian; they are pivotal in answering modern design and manufacturing challenges across various sectors.
Summary of Key Insights
Throughout the article, we've navigated the multifaceted world of heat formed plastic sheets, uncovering unique properties that contribute to their widespread application. The notable characteristics, such as:
- Versatility: Heat formed plastic sheets can be molded into diverse shapes which makes them suitable for many industries, from aerospace to consumer goods.
- Thermal Efficiency: The ability to withstand significant temperature variations without losing integrity ensures they serve well in varying applications.
- Sustainability Efforts: The emerging trends in recycling practices and biodegradable alternatives point to a future where such materials could yield less waste while still delivering functionality.
By diving into the thermoplastic categories and their distinctive qualities, we underscored their significant roles in product development. Additionally, the equipment and technology behind heat forming techniques suggest a rapidly evolving landscape that embraces innovation in manufacturing processes.
"Understanding the specific properties of different thermoplastics can significantly streamline product development, ensuring optimal performance in real-world conditions."
Looking Ahead
Looking to the horizon, it is evident that the heat formed plastic sector is poised for exciting developments. Advancements in 3D printing and smart materials are revolutionizing the way these materials are produced and utilized. This evolving trend signifies a shift toward customization and increased functionality, maximizing the potential of heat formed plastic sheets across a myriad of applications.
Moreover, as environmental concerns intensify, there's a growing impetus to innovate sustainable options. Organizations are likely to invest in research aimed at improving recycling systems while incorporating eco-friendly materials. The interplay between technology and sustainability will likely sculpt new opportunities, making heat formed plastic sheets not just a stopgap measure, but a cornerstone of future manufacturing practices.