Exploring Friction Welding Machines: Principles and Applications
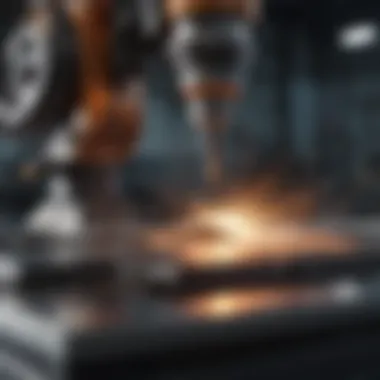
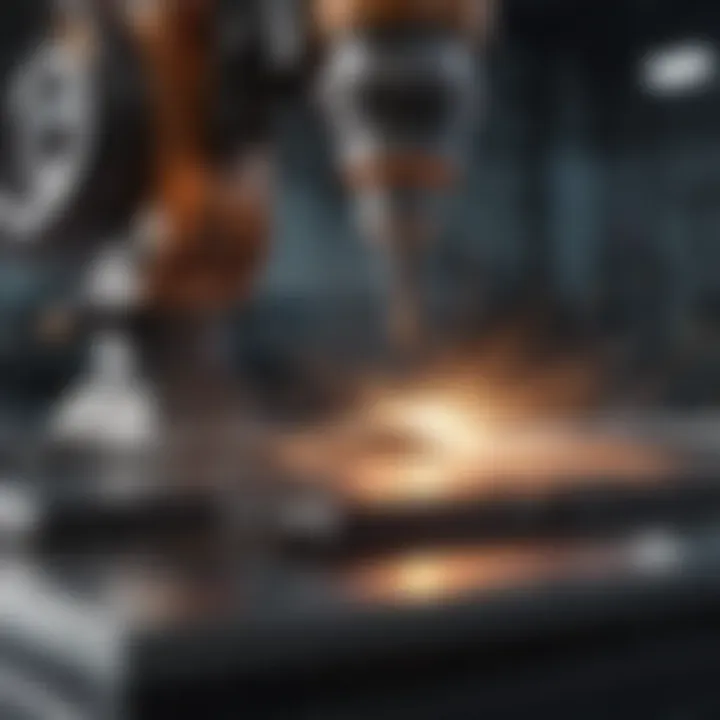
Intro
Friction welding is an evolving technology in the field of material joining. It is distinct due to its innovative process that utilizes frictional heat to bond materials without the need for additional filler materials or shielding gases. Understanding the principles and applications of friction welding machines is essential for engineers and manufacturers who aim to stay competitive in todayβs market.
The operation of these machines is based on the principle of generating heat through friction between two surfaces that are brought into contact while rotating. This method proves to be advantageous in various sectors, including automotive, aerospace, and construction, where the integrity of joints is crucial.
Industry experts show a growing interest in friction welding due to its efficiency and reduced environmental impact. As businesses aim to optimize processes and minimize waste, friction welding presents a viable option. The future of this technology looks promising, with ongoing research focusing on enhancing machine capabilities and material compatibility.
Prologue to Friction Welding
Friction welding is a critical technological process that has revolutionized the way materials are joined in various industries. This joining method is gaining increasing importance due to its efficiency and effectiveness in certain applications. Understanding the fundamentals of friction welding enables professionals and students alike to appreciate its role in modern manufacturing. With the ongoing need for robust, high-strength joints, friction welding stands as a leading alternative to traditional welding techniques.
Definition and Basics
Friction welding is defined as a solid-state welding process where the heat needed for joining is generated through the mechanical friction between the workpieces. The performance of this process largely depends on several factors, including material properties, contact pressure, and rotational speed. In friction welding, two workpieces are held together and one of them is rotated. The friction produced at the interface generates heat. As the temperature rises, materials soften, allowing them to bond under pressure.
The basic principle can be summarized as:
- Mechanical friction generates heat at the surface.
- Heat softens the materials at the interface.
- Pressure is applied to forge the softened materials together.
This method is particularly advantageous for joining similar or dissimilar materials, including metals and polymers. The process provides several benefits such as reduced distortion, lower energy consumption, and minimal environmental impact.
Historical Context
The origins of friction welding can be traced back to the 1950s when it was first used in the United States and Europe. It emerged from the need for more efficient and reliable joining methods in industries such as automotive and aerospace. Traditional welding techniques had limitations in terms of material compatibility and structural integrity, which fueled research into alternative methods.
By the 1960s, the introduction of rotary friction welding in various manufacturing settings marked a significant advancement. Over the decades, the technology has evolved with the integration of automated controls and advanced materials. Today, friction welding is utilized in numerous applications ranging from small components in medical devices to large structures in energy production sectors.
"Understanding the historical development of friction welding sheds light on its advantages over conventional welding methods and its adaptability in different industries."
This section lays the groundwork for discussing the mechanisms, types, and future trends within the friction welding domain, enhancing its relevance in a rapidly advancing technological landscape.
Mechanism of Friction Welding
The mechanism of friction welding is pivotal in understanding how this joining technology operates effectively. This section will elucidate the core elements of friction welding, focusing on friction generation, heat production and its management, and the material flow during the joining process. Each of these components plays a crucial role in determining the quality and strength of the weld. Moreover, grasping these mechanisms offers insights into the efficiencies and advantages that friction welding provides when compared to conventional welding techniques.
Friction Generation
Friction generation stands at the core of the welding process. It is the initial phase wherein two materials are pressed together and rotated or linearly moved against one another. This action creates resistance, which is the friction itself. The amount of friction generated depends on several factors, such as the materials' surface properties, the applied force, and the speed of movement.
The effectiveness of friction generation directly influences the subsequent stages of the welding process. More friction leads to higher temperatures and energy input, promoting the materialβs plastic deformation. The optimization of this phase is essential as it sets the groundwork for a strong bond between the materials. The focus on adequate friction generation is what makes this welding method distinct.
Heat Generation and Management
Heat generation occurs as a result of the friction created during the initial phase. This heat is vital because it softens the material, allowing it to flow and bind without melting. However, managing this heat is equally important. Excessive heat may weaken the material, leading to defects or even failure at the joint. Consequently, it is critical to control the parameters related to heat generation, such as rotational speed and duration of contact.
Several strategies can be employed to manage heat effectively. For example, varying the speed and pressure can help to maintain optimal temperatures. The materials used also play a role; materials with higher thermal conductivity may dissipate heat more effectively than others. Precise temperature monitoring during the process can prevent overheating, ensuring the integrity and strength of the joint.
Material Flow During Joining
Material flow is a key element in achieving a good weld. During the process, as the temperature rises due to friction, the material begins to flow and deform, allowing atoms from both joined surfaces to intermingle and ultimately bond together. The characteristics of the materialβits ductility, viscosity, and flow behaviorβare significant in this stage.
The flow dynamics are influenced by factors such as the welding speed and pressure. When the processes are aligned properly, the result is a homogenous weld with mechanical properties that are often superior to those of the base materials. Furthermore, the effectiveness of material flow can sometimes be enhanced through pre-welding treatments like surface roughening or cleaning.
Key Takeaway: The mechanisms of friction welding involve a combination of friction generation, heat management, and material flow, each of which is crucial to ensuring a strong and durable bond. Recognizing these aspects is essential for optimizing the process and achieving high-quality welds.
In summary, a thorough understanding of the mechanism of friction welding enhances the application of this technology across various industries, ensuring that the advantages can be fully realized while minimizing potential drawbacks.
Types of Friction Welding Machines
Understanding the different types of friction welding machines is critical for anyone looking to utilize this technology effectively. Each type of machine has its unique characteristics and applications. Their design can greatly influence the outcome of the welding process, impacting factors such as joint quality, efficiency, and cost.
The three main types of friction welding machines are Rotary Friction Welding, Linear Friction Welding, and Friction Stir Welding. Each type has specific advantages and considerations that make it suitable for certain applications. In this section, we will explore each type in detail, providing insight into their operational principles and typical uses.
Rotary Friction Welding Machines
Rotary friction welding machines utilize rotational motion to produce heat through friction. One part of the workpiece is spun while the other remains stationary. The heat generated from friction softens the materials, allowing for a solid-state weld once adequate pressure is applied.
Key features of rotary friction welding machines include:
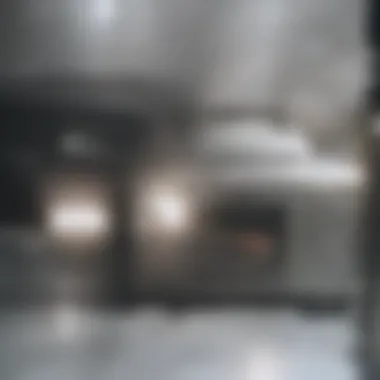
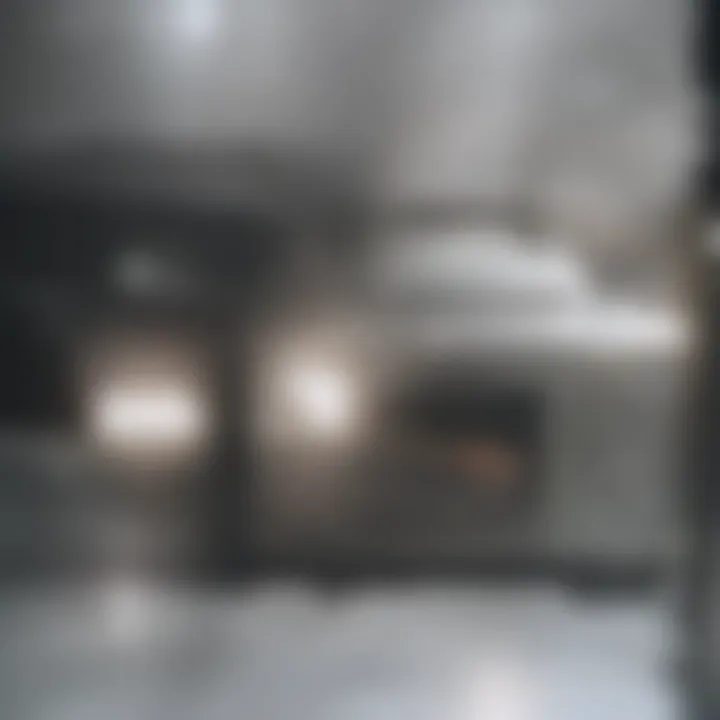
- High welding speed: These machines can quickly achieve the required temperature and pressure, leading to faster production cycles.
- Versatility in materials: Suitable for a wide range of materials, including metals and some plastics.
- Compact design: Many rotary machines are designed to occupy minimal floor space in manufacturing settings.
Applications often involve the automotive and aerospace industries, where components require strong, reliable joints. Additionally, this method is frequently used in the production of gears and shafts.
Linear Friction Welding Machines
Linear friction welding involves the linear movement of two workpieces against each other. Typically, one workpiece oscillates back and forth while the other is held static. The friction created through this relative motion generates heat, which causes material softening and allows for fusion under pressure.
Advantages of linear friction welding machines include:
- Control over joint quality: The ability to adjust parameters such as oscillation amplitude provides better control over the weld quality.
- Optimized for larger components: These machines are especially effective for welding large parts where gaps must be minimized.
- Reduced thermal distortion: Compared to traditional welding methods, linear friction welding leads to reduced thermal impact on the materials.
This technique is commonly seen in the aerospace sector for applications involving turbine components and airframe assemblies.
Friction Stir Welding Machines
Friction stir welding is slightly different from the other types. It uses a rotating tool that softens two workpieces while they are held in place. The tool moves along the joint line and creates a solid-state weld. This method is less common than the others but is gaining popularity due to its unique advantages.
Benefits of friction stir welding machines include:
- Quality of welds: The process typically results in welds with superior corrosion resistance and mechanical properties.
- No melting occurs: Since no melting takes place, the welds tend to maintain the original properties of the base materials.
- Versatility in application: Suitable for welding complex shapes and dissimilar materials presence.
Friction stir welding finds applications mostly in aerospace, marine, and automotive industries, particularly for aluminum alloys and other non-ferrous materials.
"Friction welding machines represent a vital component of modern manufacturing. Their efficiency and effectiveness pave the way for innovation across industries."
In summary, these three types of friction welding machines each offer distinct advantages. Recognizing their unique characteristics facilitates better decisions in selecting the right machine for specific applications. Understanding these nuances is essential for engineers and professionals in the manufacturing domain.
Applications of Friction Welding
Friction welding has gained traction in various industries due to its unique properties and benefits. Understanding its applications is crucial for professionals and researchers exploring modern manufacturing techniques. This method offers strong, durable joints and is suitable for a myriad of materials, making it versatile. The applications mentioned below highlight the significance of friction welding in advancing technology and improving production processes.
Automotive Industry
The automotive sector is one of the primary adopters of friction welding technology. It is widely used for producing components such as axle shafts, crankshafts, and gear assemblies. The benefits include:
- Material Savings: Friction welding enables the joining of dissimilar materials, such as steel to aluminum. This leads to a reduction in overall weight, contributing to fuel efficiency.
- Strength and Reliability: The joints created through friction welding exhibit high strength, crucial for automotive components subject to high stress and demands.
- Cost Efficiency: The process often reduces assembly time and material waste, enhancing production efficiency.
This application showcases friction welding's capacity to meet the rigorous standards of the automotive industry while fostering innovation and continuous improvement.
Aerospace Sector
In the aerospace industry, where safety and material integrity are paramount, friction welding is critical. It is extensively utilized in manufacturing aircraft components, such as:
- Wing Structures: Friction welding creates robust joints that offer the necessary strength-to-weight ratio for wings and fuselages.
- Engine Parts: Components like turbine blades and shafts benefit from the durability provided by friction-welded joints.
The capability to weld high-performance alloys without compromising their properties is essential in this sector. By reducing the number of parts, friction welding simplifies assembly tasks and minimizes potential failure points.
Energy Production
Energy production, particularly in renewable energy, has also embraced friction welding technology. This includes applications such as:
- Wind Turbines: Components such as tower sections and rotor blades can be joined efficiently using friction welding.
- Oil and Gas Equipment: Critical parts like pipelines and valve components benefit from the strength and reliability of friction welding.
Utilizing this method provides a pathway to create more efficient energy solutions. The reduction in weight and maintenance requirements directly impacts the sustainability of energy resources.
Other Industrial Applications
Friction welding is not limited to the automotive, aerospace, and energy industries. It has a diverse range of applications, including:
- Railway Systems: Used for joining rail sections and components, ensuring durability and safety.
- Heavy Machinery: Component assembly in construction and agricultural machinery benefits from strength and durability.
- Electronics: Small, intricate components can be welded with precision, enhancing electronic device reliability.
The adaptability of friction welding in various contexts speaks to its importance in modern manufacturing. It can effectively enhance performance while promoting cost savings and efficiency across multiple industries.
Advantages of Friction Welding
Friction welding has gained attention in recent years due to its unique advantages over traditional welding techniques. This section provides a detailed examination of these benefits, emphasizing the crucial aspects of material integrity, efficiency, cost-effectiveness, and environmental impact. Companies across various industries have identified friction welding as a solution that aligns with modern manufacturing demands.
Material Integrity and Strength
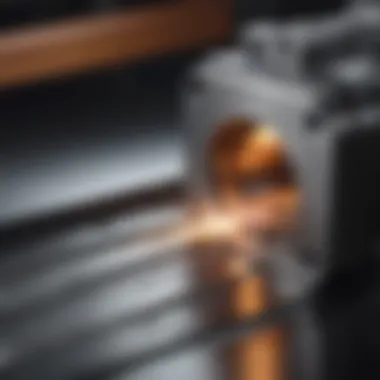
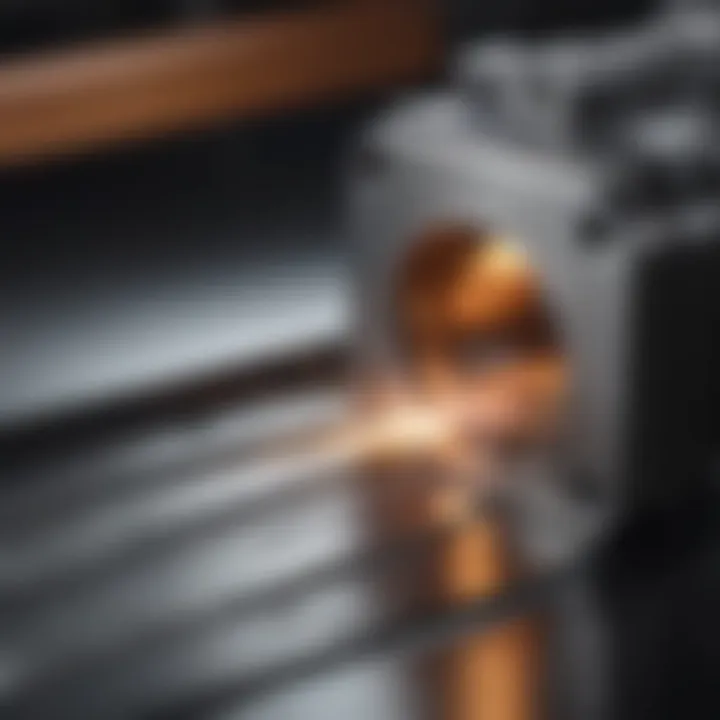
One of the primary advantages of friction welding is the exceptional material integrity it offers. This method produces joints that can maintain the original mechanical properties of the materials being joined. The solid-state nature of friction welding minimizes the risk of defects, such as porosity and inclusions, common in fusion welding methods. Research shows that joints created through friction welding can exhibit strength levels comparable to or surpassing that of the parent materials. This is particularly beneficial in critical applications where reliability and safety are paramount, such as the aerospace and automotive sectors.
Efficiency and Cost-Effectiveness
Friction welding stands out for its efficiency and cost-effectiveness. The process is relatively quick, taking only a few seconds for most joints. This rapid processing time not only increases productivity but also reduces labor costs. Furthermore, the need for additional filler materials is often eliminated, as the process typically joins the base materials directly. Maintaining and operating friction welding machines can also be less expensive than other welding systems due to their simplified design and lower energy requirements. As a result, businesses can see a notable return on investment when adopting this technology.
Reduction of Environmental Impact
The environmental considerations of manufacturing processes are becoming more critical. Friction welding offers a compelling advantage in this regard. First, it generates less waste since it does not require filler materials, which contributes to a more sustainable production practice. Additionally, the process consumes less energy compared to traditional melting welding methods, aligning it with growing sustainability initiatives in manufacturing. By minimizing resource consumption and waste production, friction welding presents a pathway for companies looking to reduce their environmental footprint while maintaining high-quality output.
"The sustainability potential of friction welding is an important consideration for industries aiming for greener manufacturing processes."
Considerations for Friction Welding Implementation
In the context of friction welding, successful implementation necessitates a close examination of several critical aspects. Understanding these considerations is essential not just for optimizing the welding process but also for maximizing the longevity and performance of the resultant joints. The following sections will delve into key elements that practitioners must consider for effective friction welding implementations.
Material Compatibility
Material compatibility stands as a fundamental consideration for friction welding. Not all materials are suitable for this welding process. The welding processes primarily depend on the thermal and mechanical properties of the materials being joined. Metals like steel, aluminum, and titanium are frequently used due to their favorable friction welding characteristics. However, it is imperative to assess material compatibility carefully, as differences in melting points, thermal expansion, and microstructure can adversely impact joint quality.
A few specific points to consider include:
- Thermal properties: Materials with vastly different thermal conductivities may lead to uneven heating, resulting in defective joints.
- Mechanical properties: Disparities in hardness, tensile strength, and ductility can produce unwanted stress concentrations, which may cause joint failure.
Finding compatible materials not only enhances joint integrity but also prevents unnecessary failures during applications in critical sectors such as aerospace or automotive.
Machine Configuration Requirements
The configuration of machines used for friction welding plays a crucial role in achieving desired outcomes. Factors such as machine type, skill of the operator, and tooling must align with the specific requirements of the material and joint design. Different kinds of friction welding processesβrotary, linear, or friction stirβrequire distinct machine configurations. Each type has its own operational parameters that influence the efficiency and quality of the weld.
Key considerations include:
- Tool design: The shape and material of the tool affect the effectiveness of heat generation and material flow during welding.
- Pressure settings: Insufficient or excessive pressure can lead to poor joint formation or damage to the workpieces.
- Speed control: Adjusting the rotational or linear speed is vital to managing heat input wisely, impacting the quality of the weld.
Ensuring the machine is properly configured will minimize risks throughout the welding process and contribute substantially to the durability of joints created.
Quality Control Measures
To ensure the longevity and effectiveness of friction welds, stringent quality control measures are indispensable. The complexity of the welding process necessitates continuous monitoring and assessment at various stages. Meeting these quality benchmarks is essential for minimizing defects and maintaining structural integrity.
Important quality control considerations include:
- Visual inspection: Regular checks for surface defects can help in early identification of potential issues.
- Non-destructive testing: Techniques such as ultrasonic testing or radiographic inspection can assess internal joint quality without compromising the integrity of the weld.
- Process parameters monitoring: Keeping an eye on factors such as temperature, speed, and pressure will alert the operator to variations that could lead to poor weld quality.
Implementing robust quality control measures ensures that the benefits of friction welding are fully realized, protecting investments made in both materials and technology.
"Effective friction welding processes hinge on a thorough understanding of material compatibility, machine requirements, and quality control protocols. Failing to address these elements can lead to significant operational setbacks."
Technological Advancements in Friction Welding
Technological advancements in friction welding are reshaping how manufacturers approach this joining technique. New technologies enhance performance, increase precision, and reduce production times. Each advancement helps manufacturers meet demands for high-quality welds while maintaining efficiency. The integration of innovative designs, automation, and sophisticated sensor technologies plays a pivotal role in these enhancements.
Innovations in Machine Design
Recent innovations in machine design have led to improved operational efficiency and weld quality. Manufacturers now focus on ergonomic layouts, modular components, and advanced control systems. These systems are designed for user-friendliness, allowing operators to fine-tune parameters to achieve optimal welding conditions.
Along with this, modern machines often feature higher power output and better heat management systems. Such improvements facilitate the use of materials with different thermal properties. Consequently, manufacturers can join materials such as aluminum to steel more effectively, expanding the range of applications.
Automation and Robotics Integration
The integration of automation and robotics into friction welding processes marks a significant trend. Automated systems enable consistent and repeatable welds, reducing the variability often present in manual operations. Robots equipped with advanced programming capabilities can work quickly while maintaining accuracy.
Furthermore, automation minimizes labor costs and increases production rates. This is particularly advantageous in high-volume manufacturing environments, such as the automotive sector. In addition, robots can be deployed in hazardous environments, improving workplace safety. Overall, automation enhances product quality while reducing risks associated with manual work.
Sensor Technology and Data Monitoring
The role of sensor technology and data monitoring in friction welding cannot be overstated. Smart sensors are being utilized to collect real-time data on welding parameters such as temperature, pressure, and material displacement. This data helps in monitoring the welding process for anomalies that could indicate potential failures or weaknesses in the joint.
Data monitoring also allows for predictive maintenance of welding machines. Early detection of wear and tear can prevent unexpected downtimes and costly repairs. Integration with Internet of Things (IoT) technology further allows for remote monitoring and control, making friction welding machines more adaptable and efficient.
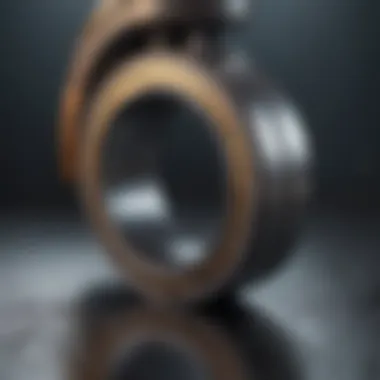
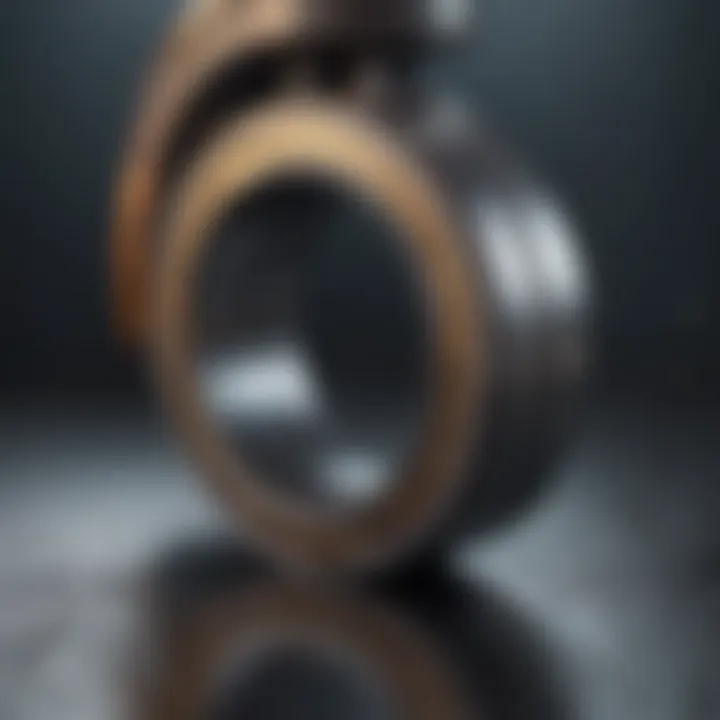
The evolution of technology in friction welding presents opportunities to optimize processes and enhance product reliability.
Challenges and Limitations of Friction Welding
Understanding the challenges and limitations of friction welding is essential for manufacturers and engineers. While these processes offer numerous advantages, they are not without their issues. Addressing these challenges is crucial for enhancing the technology's effectiveness and expanding its applications across industries. This section will examine specific limits of material joints, operational challenges, and cost-related concerns related to friction welding.
Limitations of Material Joints
In friction welding, the compatibility of materials is a significant factor. Not all material combinations can achieve effective joints. For example, joining dissimilar metals can be problematic. When two metals with different thermal and mechanical properties are welded, issues arise such as differing expansion rates and insufficient bond strength. Consequently, careful selection of materials is necessary to achieve reliable joints.
Friction welding tends to work best with similar metals. The material's microstructure can also play a role. Some alloys may become brittle during the process, leading to a weaker joint. Therefore, manufacturers must conduct thorough material evaluations to ensure successful welding outcomes and mitigate these limitations.
Operational Challenges
Operational challenges in friction welding can also hinder efficiency. These challenges can include the technical know-how required for machine operation. Users must understand the proper parameters, such as pressure, speed, and time. Incorrect settings may result in poor fusion or inadequate bonding.
Moreover, recruitment and training of skilled operators can be a hurdle for many firms. Unlike traditional welding methods, which are widely understood, friction welding requires specialized knowledge.
Cost-Related Concerns
Cost considerations can impact the adoption of friction welding. Although friction welding can save money in the long run due to its efficiency, the initial capital investment in machinery can be high. Purchasing advanced friction welding machines may deter some smaller or budget-conscious companies.
Moreover, maintenance costs for specialized equipment can add to the overall expense. Regular maintenance ensures machines function optimally and produce high-quality welds. However, firms must weigh these costs against the benefits of reduced production time and waste. Finding the balance between upfront costs and operational savings is crucial for companies considering friction welding.
In summary, while friction welding presents compelling advantages, its limitations must be acknowledged. Material compatibility, operational challenges, and cost factors play a crucial role in its application and adoption. Recognizing these challenges is the first step in improving the technology and maximizing its effectiveness in various fields.
Future Trends in Friction Welding
Friction welding is evolving rapidly, reflecting advancements in technology and growing industry needs. Understanding future trends in this welding technique is crucial for professionals aiming to adopt these innovations. This section looks at emerging markets, ongoing research developments, and sustainability considerations that are shaping the future of friction welding.
Emerging Markets and Applications
As industries seek efficient and reliable joining methods, friction welding is making inroads into various sectors beyond traditional applications. Key industries like aerospace, automotive, and renewable energy are increasingly turning to this technology. The aerospace sector, in particular, is valuing friction welding for its ability to achieve strong bonds while maintaining material integrity at high temperatures.
Emerging markets, such as electric vehicles (EVs), are also pressing for advanced manufacturing techniques. Lithium-ion battery manufacturing is a prime example where friction welding can facilitate the joining of different battery components. Moreover, medical device manufacturing is expected to adopt this technology for ensuring high precision and sterility in joins.
These emerging applications are driving further research and development in machine design, increasing the demand for specialized friction welding machines.
Research Developments
Research into friction welding is broadening its scope. Academic institutions and industrial researchers are investigating various aspects, from new materials to advanced machine capabilities. For instance, recent studies focus on optimizing parameters like friction speed and pressure to improve joint quality and reduce cycle times. There is also exploration of using artificial intelligence to enhance process control and predict welding properties based on material types and conditions.
Robust research programs are investigating the integration of hybrid welding techniques combining friction welding with other methods. The aim is to achieve the benefits of multiple joining processes, thereby broadening material compatibility and enhancing joint performance.
Ongoing developments indicate a focus on personalized solutions. Each industry may have specific needs that require tailored welding processes. This shift towards customization is a significant trend in friction welding research.
Sustainability Considerations
Sustainability is becoming a focal point in friction welding discussions. As industries face pressures to reduce their carbon footprint, friction welding offers several advantages. Its energy efficiency is considerable compared to traditional welding methods, primarily due to its minimal pre-heating requirements. This reduced energy consumption helps lower greenhouse gas emissions during manufacturing.
Furthermore, the process generates less waste, as it typically requires fewer filler materials. Enhanced joint strength also allows for thinner components, leading to lightweight structures. Such reductions in material usage contribute positively toward sustainability goals.
Additionally, the trend of reusing produced energy in friction welding machines is gaining attention. By capturing and reusing thermal energy generated during welding, manufacturers can improve operational efficiency. Companies that adopt these sustainable practices are likely to gain a competitive edge in the increasingly eco-conscious market.
"The future of friction welding is intertwined with sustainability; its efficient processes and reduced material waste make it an attractive option for environmentally-friendly manufacturing."
In summary, the future trends in friction welding point toward a blend of innovation, efficiency, and sustainability. Stakeholders in various industries must pay attention to these trends to remain relevant and competitive.
Epilogue
The conclusion serves as a pivotal element in this exploration of friction welding machines. It connects the foundational knowledge and insights gathered throughout the article, reinforcing the significance of friction welding in modern manufacturing contexts.
Summary of Findings
In this article, we examined the operational principles of friction welding, highlighting the mechanism of heat generation and material flow during the joining process. We identified various types of friction welding machines such as rotary, linear, and friction stir welding machines. Each type has distinct characteristics and applications in industries like automotive, aerospace, and energy production.
Friction welding offers several advantages over traditional welding methods. Notably, it preserves the integrity and strength of materials while being more efficient in energy and cost. The discussion emphasized technological advancements in machine design, automation integration, and sensor technologies that enhance performance and reliability.
Implications for the Future
Looking ahead, the relevance of friction welding will likely grow as industries seek innovative and sustainable solutions. The emergence of new markets and applications indicates that this joining technology will play a crucial role in meeting the demands of modern manufacturing.
Research developments are poised to address existing challenges, leading to improved methodologies and better material compatibility. Additionally, sustainability considerations are becoming increasingly critical. It is imperative that future trends in friction welding emphasize minimizing environmental impact while maximizing efficiency.
Friction welding presents a compelling alternative in a world striving for operational efficiency and material integrity.
The synthesized knowledge throughout this article has demonstrated that friction welding is not just a technological advancement but a significant shift in manufacturing paradigms. It is essential for professionals and researchers to stay abreast of developments in this field to leverage its benefits effectively.