Exploring the Zygo Profilometer for Precision Measurement
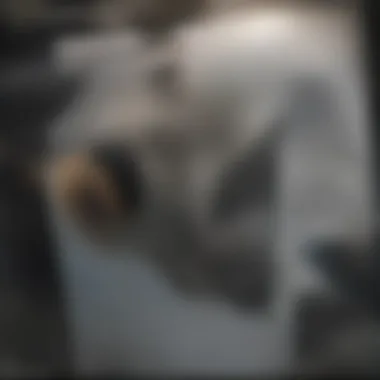

Intro
In the realm of precision measurement, the Zygo profilometer stands out as an indispensable tool. This specialized instrument plays a central role in accurately assessing surface profiles across various industries. The significance of optical measurement cannot be overstated, especially in fields such as semiconductor manufacturing and material science, where any deviation from precise measurements can lead to significant failures or inefficiencies. This article will elaborate on the functionalities and applications of the Zygo profilometer while offering insights that enhance understanding of this vital technology.
Research Context
Background Information
The Zygo profilometer operates on principles of interferometry, which allows for the measurement of surface variations at an incredibly small scale. Interferometry exploits the wave nature of light, using the interference patterns created by combining multiple beams of light. At the heart of the profiling process is the comparison of the light that is reflected from the sample surface with a reference beam. This technique enables the detection of minute surface imperfections and the quantification of topographical features.
Importance of the Study
Understanding the functions and applications of the Zygo profilometer is essential for professionals in fields requiring high-precision measurements. For instance, in semiconductor manufacturing, the quality of wafer surfaces can determine the operational efficiency of integrated circuits. Similarly, in optics, the performance of lenses and mirrors directly relies on accurate surface measurements.
The discussion surrounding profilometers also encapsulates a variety of technological advancements, improving both accuracy and efficiency. By delving into the nuances of its operability, users can make informed choices about which instruments best fit their specific measurement needs.
"Precision in surface measurement is not merely a luxury; it's a necessity in advancing technology and ensuring quality in production."
Discussion
Interpretation of Results
Data obtained from a Zygo profilometer not only informs about surface characteristics but also assists researchers and engineers in troubleshooting production issues and enhancing design processes. Notably, results can indicate surface roughness, flatness, and texture, which are critical metrics in evaluating material performance.
Comparison with Previous Research
Historically, surface measurement has evolved from analog methods to sophisticated digital measuring techniques. Comparatively, earlier methods were limited in precision and reliability. The advent of the Zygo profilometer reflects a significant shift towards more reliable optical measurement methods. Literature indicates that responses from the Zygo instrument have outperformed traditional profilometers in various benchmarks such as resolution and speed.
Enhancements in the design and functionality of profiling instruments also open new avenues for innovative applications and cross-disciplinary collaborations, further underscoring the importance of this study for ongoing advancements in optical measurement.
Prelims to Zygo Profilometer
The Zygo profilometer represents a pivotal tool in the domain of optical measurement. This sophisticated instrument is vital for precision surface measurements, widely utilized across various industries, especially those demanding high accuracy. Understanding the structure and functionalities of the Zygo profilometer is crucial for students, researchers, educators, and professionals who rely on surface profiling in their work. This section elucidates the importance of the Zygo profilometer by examining its definition and historical context.
Definition and Purpose
The Zygo profilometer is an advanced optical device designed specifically for measuring the surface topography of materials. Its primary purpose is to provide accurate three-dimensional representations of surface profiles. This capability is essential across numerous fields such as semiconductor manufacturing, where the flatness and features of surfaces determine device performance.
The principal working mechanism involves using interferometry, which allows the detection of minute variations in surface height. These measurements are crucial for quality control and research applications. By employing the Zygo profilometer, professionals can achieve precise metrics that guide critical decisions in product development and manufacturing.
Historical Context
The development of the Zygo profilometer can be traced back to advances in optical metrology during the late 20th century. Originally, surface measurement was primarily reliant on contact methods, which could introduce errors and damage to the surface under observation. However, the introduction of optical techniques marked a significant shift in measurement accuracy.
Zygo Corporation, founded in 1970, was instrumental in pioneering these optical measurement techniques, establishing a reputation for producing high-performance profilometers. The evolution of the Zygo profilometer reflected the broader advancements in technology and materials science, allowing for increasingly sensitive and precise measurements.
Over the years, various models have emerged, adapting to the growing needs of industries. As demands for accurate surface measurements increased due to miniaturization and complex geometries in modern manufacturing, Zygo profilometers continued to evolve, integrating cutting-edge technology that enhances their capabilities.
In summary, the introduction to the Zygo profilometer encompasses not just the definition and purpose of this valuable device but also highlights its significant historical progress. Understanding its development enriches the appreciation for its role in contemporary applications, thereby underscoring the importance of continual innovation in the field of optical measurement.
Operating Principles
Understanding the operating principles of the Zygo profilometer is crucial for grasping how this device achieves high precision in surface measurement. These principles lay the foundation for the various techniques utilized in profilometry, ensuring accurate readings of surface topographies. In this section, we explore three primary methodologies: interferometric techniques, phase shifting methods, and scanning methods. Each method has its own unique characteristics, benefits, and applications.
Interferometric Techniques
Interferometric techniques form the core of how Zygo profilometers operate. This method relies on the interference of light waves. When two coherent light waves combine, they create a pattern of bright and dark fringes that can be analyzed to determine surface variations. The measurement is based on the optical path difference between the reflected light from the surface being measured and a reference light beam. This enables detection of very small height differences, often in the nanometer range.
Benefits of interferometry in profilometry include:
- High Resolution: Capable of measuring minute variations on a surface.
- Non-contact Measurement: It does not physically touch the surface, making it ideal for delicate components.
- Fast Data Acquisition: Provides rapid measurements, which is essential in manufacturing environments.
Phase Shifting Methods
Phase shifting methods enhance the accuracy of interferometric measurements by analyzing the shift in phase of the light waves rather than relying on fringe patterns alone. By introducing a controlled phase shift, these methods allow for the extraction of height information with improved precision. This technique is particularly valuable for surfaces that may not produce clear fringe patterns due to roughness or other irregularities.
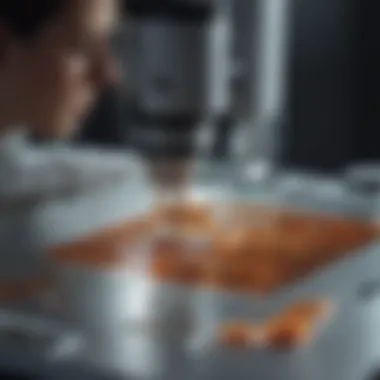

Key aspects of phase shifting methods include:
- Increased Accuracy: Reduces measurement errors linked to environmental fluctuations.
- Simplified Data Collection: Only a few individual measurements are necessary to generate detailed surface profiles.
- Versatility: Applicable to a broad range of materials and surface conditions.
Scanning Methods
Scanning methods involve moving the profilometer across the surface to gather data point by point. This approach is often paired with either the interferometric or phase shifting techniques to achieve a comprehensive understanding of the surface topology over a larger area. Scanning provides a means to create detailed 3D maps of the surface, offering insights that are invaluable for quality control and research purposes.
The advantages of scanning methods comprise:
- Extensive Coverage: Allows measurement over large areas, which is crucial in applications such as semiconductor manufacturing.
- 3D Mapping: Facilitates the creation of detailed models of surface topography, enabling deeper analysis.
- Adaptability: Can be combined with various measurement techniques to suit different materials and designs.
"The choice of measurement technique can greatly influence the data quality and interpretation of results in profilometry."
By comprehensively understanding these operating principles, users can better appreciate how Zygo profilometers function and select the appropriate methodology for their specific measurement needs.
Types of Zygo Profilometers
Understanding the types of Zygo profilometers is essential for comprehending their unique applications and benefits across various fields. Each type is specialized for specific measurement requirements. Knowing the distinctions helps researchers and professionals select the best tool for their needs, leading to more accurate and reliable surface measurements.
Optical Profilometers
Optical profilometers utilize light for surface measurement. They are noteworthy for their ability to achieve high resolution while remaining non-contact. This eliminates risks of damage, especially crucial in sensitive applications like semiconductor manufacturing.
Key advantages of optical profilometers include:
- High precision: These devices can capture minute surface features, crucial for applications in microelectronics.
- Versatility: They can measure a variety of materials, making them useful in different industries, including optics and pharmaceuticals.
- Speed: Rapid scanning capabilities allow for quick assessments, aiding processes where time is critical.
However, environmental conditions can affect measurements, necessitating controlled settings for accurate results. Overall, optical profilometers serve as indispensable tools in fields that demand unparalleled precision.
Mechanical Profilometers
Mechanical profilometers operate differently. They rely on a physical probe that contacts the surface being measured. This method suits rougher surfaces where optical methods may struggle.
In terms of benefits, mechanical profilometers offer:
- Robustness: They can measure a wider variety of textures and surface conditions, making them applicable in harsh environments.
- Cost-effectiveness: Typically more affordable than their optical counterparts, they provide a practical solution for various measurement needs.
- Simplicity: Their operation can be straightforward, which appeals to a range of users, from novice researchers to skilled professionals.
However, they may not match the resolution of optical devices and can alter the surface being measured. Therefore, understanding the specific use case is vital before choosing this method.
Non-contact Profilometers
Non-contact profilometers represent a third category, distinguishing themselves through advanced techniques that avoid physical contact with the surface. These devices, often utilizing lasers or white light, are excellent for delicate surfaces where contact could lead to damage.
The benefits of non-contact profilometers include:
- Safety: They preserve the integrity of sensitive materials, making them ideal for fragile optics.
- Speed and efficiency: Like optical profilometers, they often provide rapid data acquisition, enhancing productivity.
- Comprehensive analysis: These instruments can generate detailed three-dimensional maps of surfaces, crucial for complex data analysis in research and industry.
Despite their advantages, non-contact methods can be sensitive to environmental factors such as dust or vibration, which may lead to noise in the data.
Applications of Zygo Profilometers
Zygo profilometers are critical instruments in various advanced fields, providing precise measurements of surface profiles with unparalleled accuracy. These instruments help ensure quality control, enhance product design, and enable research and development. Understanding the primary applications of Zygo profilometers allows professionals and researchers to grasp their significance in industries like semiconductor manufacturing, optics, and material science. This section focuses on three main applications, detailing their unique contributions and benefits.
Semiconductor Manufacturing
In semiconductor manufacturing, the pursuit of precision is paramount. Zygo profilometers play a crucial role in this field. They help in monitoring and controlling surface properties of silicon wafers and other materials essential for fabricating chips.
- Process Control: Accurate measurements of surface finish and flatness are essential for optimal yield in production. Zygo profilometers ensure that any anomalies are detected early, reducing waste and maximizing efficiency.
- Thin Film Characterization: The technology enables precise measurement of thin films, which are vital in semiconductor devices. Understanding the thickness and uniformity of these films guarantees performance and reliability.
- Quality Assurance: By providing detailed metrics on surface topology, Zygo profilometers help in meeting stringent industry standards, ensuring that end products perform as intended.
Optical Component Measurement
The realm of optics relies heavily on precision for both development and application. Zygo profilometers serve an invaluable role in optical component measurement. They can assess various optical elements, including lenses and mirrors, ensuring that they meet specific design criteria.
- Surface Flatness: With high-resolution measurements, Zygo profilometers can determine surface deviations from the ideal shape in optics. This guarantees enhanced performance in beam steering and focusing applications.
- Wavefront Analysis: Emerging technologies in optical systems utilize Zygo's capabilities to evaluate wavefronts, leading to improved imaging and detection systems.
- Research and Development: In laboratories, these devices facilitate the development of new optical designs by measuring and refining component surfaces, crucial for advancing optical technology.
Material Science and Testing
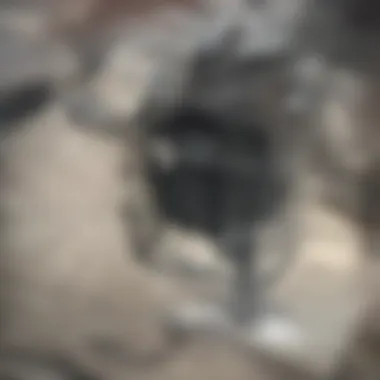

Zygo profilometers are also essential tools in the field of material science and testing. They assist in understanding material properties through detailed surface analysis.
- Characterization of Surface Roughness: By assessing the roughness of surfaces, researchers can establish correlations between surface characteristics and material performance. This analysis is vital in many applications, from coatings to composites.
- Failure Analysis: Zygo profilometers contribute to investigating the causes of material failure. Understanding surface defects or wear patterns can lead to improvements in material design and selection.
- Nano-Materials: As the field of nano-materials grows, the need for precise measurement becomes more pressing. Zygo profilometers provide the necessary precision to study and develop new materials at the nanoscale level.
Zygo profilometers are indispensable in semiconductor, optics, and material science fields. Their precise measurements ensure quality, enhance performance, and enable groundbreaking research and development.
Calibration of Profilometers
Calibration of profilometers is a critical aspect of ensuring accuracy and reliability in surface measurement. In the context of the Zygo profilometer, calibration establishes the precision of the device, allowing for valid comparisons and consistent results across various applications. Profilometers are employed in many fields, including semiconductor manufacturing and optical component measurement, where even minor deviations in measurements can lead to significant issues. Thus, proper calibration can enhance quality control and operational efficiency, making it essential for various industry applications.
Calibration Standards
Calibration standards serve as benchmarks for the verification and adjustment of measurement tools like the Zygo profilometer. These standards are generally established by authoritative organizations and define the expectations for accuracy in measurements. Utilizing recognized standards ensures that the measurements obtained are traceable to national or international reference standards. This traceability adds credibility to the results obtained from the Zygo profilometer, reinforcing trust in the measurement process among stakeholders. Key aspects of calibration standards include:
- Traceability: Connecting measurement results to a national or international standard.
- Accuracy: Ensuring that measurements are within acceptable ranges defined by standards.
- Consistency: Providing reliable measurement outcomes across different devices and over time.
Proper use of calibration standards increases measurement confidence and reduces variability in data analysis.
Routine Calibration Procedures
Routine calibration procedures are essential in maintaining the performance of the Zygo profilometer. These procedures involve systematic checks and adjustments to ensure the instrument remains within the specified accuracy limits. Regular calibration minimizes measurement drift that can occur due to environmental factors or wear over time. Essential steps in conducting routine calibration include:
- Pre-calibration Check: Inspect the system for any visible damage and check for proper functioning.
- Use of Calibration Standards: Implement established standards to compare and adjust measurements accordingly.
- Documenting Results: Maintain detailed records of calibration data to track trends and assist in troubleshooting.
- Frequency of Calibration: Often determined by usage patterns, ensuring the device is calibrated at appropriate intervals.
By adhering to these procedures, facilities can optimize the performance of Zygo profilometers, ensuring that they provide accurate and reliable data necessary for various measurement applications.
Interpreting Profilometry Data
In the realm of optical measurement, the skill of interpreting profilometry data is substantial. It not only determines the quality of a surface but also influences manufacturing processes across multiple industries. A profound understanding of this data empowers professionals to make educated decisions on production quality and performance improvements.
Surface Roughness Parameters
Surface roughness is a critical metric in profilometry. It provides insight into how a surface interacts with its environment, including friction, adhesion, and wear. Key parameters in surface roughness include Ra, Rq, and Rz, each offering unique perspectives on the surface texture:
- Ra (Average Roughness): It measures the average deviation of the surface profile from the mean line. This metric is widely used in quality control.
- Rq (Root Mean Square Roughness): It quantifies the square root of the average of the squares of the profile deviations. It is more sensitive to peaks and valleys than Ra.
- Rz (Average Maximum Height of the Profile): This parameter calculates the average distance between the highest peak and the lowest valley over a sampling length.
Interpreting these parameters involves assessing the intended application of the surface. For example, a semiconductor's smoothness can directly affect its performance. Accurate interpretation leads to necessary adjustments in processing techniques, optimizing overall results.
3D Surface Mapping
3D surface mapping represents another crucial way of interpreting data generated by a Zygo profilometer. This technique visually depicts the surface topography, allowing for an in-depth analysis of intricate features. Using various software tools, professionals can convert raw data into detailed 3D models.
These models reveal patterns and anomalies that might not be visible in traditional 2D representations. Benefits of 3D surface mapping include:
- Comprehensive Analysis: It allows for a holistic view of the surface, facilitating better understanding.
- Identification of Flaws: Issues such as scratches or unevenness can be detected with greater ease.
- Data Comparison: Mapping enables comparison with previous measurements. This helps in tracking changes over time, essential for quality assurance.
In summary, interpreting profilometry dataโthrough surface roughness parameters and 3D surface mappingโis culmination of essential skills in the field. These insights guide decision-making processes and foster improvements in product quality.
Technological Innovations
Technological innovations in the field of profilometry are pivotal, reshaping the way surface measurements are conducted and interpreted. In an era where precision is paramount, advancements in sensor technology and software development have significantly enhanced the capabilities of Zygo profilometers. These innovations not only improve measurement accuracy but also expand the range of applications across various industries.
Advancements in Sensors
Advancements in sensors have played a crucial role in the evolution of the Zygo profilometer. Modern sensors incorporate improved optical designs which increase their sensitivity and resolution. The introduction of high-speed cameras helps to capture high-quality images at a much faster rate. This acceleration is vital in environments that require immediate feedback, such as semiconductor manufacturing.
Moreover, innovative sensors are increasingly designed to handle diverse materials. For instance, the development of multi-wavelength sensors allows for better measurement of complex surfaces by compensating for different optical properties. This flexibility makes it possible to accurately measure a broader spectrum of surfaces, from smooth to rough, in a single setup.
These sensor advancements lead to better data quality and faster processing times, rendering the measurements more reliable and efficient.
Software Developments
Alongside sensor innovations, software developments have transformed how data is processed and analyzed in Zygo profilometers. Modern software solutions utilize advanced algorithms and machine learning techniques that enhance data analysis and interpretation. The transition from basic data visualization to comprehensive analysis tools has fundamentally changed the usability of profilometry.
These software advancements enable operators to handle large datasets with ease, provide more intuitive user interfaces, and assure a streamlined workflow. Features such as real-time data processing and automated reporting significantly minimize human error and improve repeatability in measurements.
Furthermore, customizability in software settings allows users to adapt the profilometerโs capabilities to specific industry needs. This adaptability is essential for fields such as materials science, where different analysis demands require unique approaches.
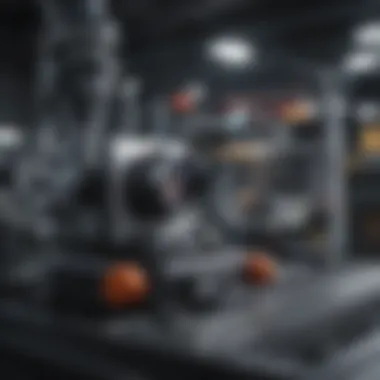

"Technological innovations are reshaping profilometry, enhancing both efficiency and capacity across various sectors."
Challenges in Measurement
Measurement in optical profilometry presents a complex landscape of challenges, critical to ensure reliability in the results. Factors affecting measurements can undermine the precision of the Zygo profilometer, crucial in critical industries like semiconductor manufacturing and material science. Understanding these challenges is paramount for professionals working with these tools.
Environmental Influences
Environmental conditions significantly impact the accuracy of measurements taken by a Zygo profilometer. Fluctuations in temperature and humidity can introduce noise and errors in the data. For example, temperature variations may cause thermal expansion of the materials being measured, resulting in distorted readings. Similarly, humidity can affect the refractive index of air, which may lead to errors in optical measurements.
Maintaining a controlled environment is essential. Using climate-controlled rooms when operating these devices minimizes external influences that may compromise the integrity of the measurements. Additionally, vibration from nearby equipment or activities may affect readings. Therefore, isolating the profilometer from high-vibration areas is often necessary.
Some practical strategies include:
- Utilizing vibration isolation tables to stabilize the equipment.
- Conducting measurements during off-peak hours to avoid disturbances.
- Monitoring environmental parameters regularly and adjusting protocols accordingly.
Material Properties
The properties of the materials being measured are another layer of complexity. Different materials respond uniquely to light, which could affect the results obtained from a profilometer. Variations in surface roughness, reflectivity, or texture can skew results, particularly if not accounted for in the measurement process.
For instance, a highly reflective surface might create misleading interference patterns, complicating the analysis. On the other hand, materials with intricate structures could pose challenges in interpreting the 3D maps generated by the measurements.
To address these challenges, awareness of material properties is crucial. Before measurement, knowing the surface characteristics can assist in selecting the right profiling methods. Moreover, pre-scanning tests can provide baseline data to compare against the final results.
In summary, challenges in environmental conditions and material properties necessitate careful consideration. Professionals must adopt rigorous protocols to mitigate these issues and ensure that the data gathered is reliable and actionable.
Future Trends in Profilometry
The realm of profilometry is witnessing rapid evolution, driven by advancements in technology and the increasing complexity of measurement requirements. The future trends in profilometry are crucial for understanding how optical measurement techniques will progress. They offer valuable insights into the integration of emerging technologies, enhancing measurement precision, efficiency, and overall analytical capabilities.
As industries continue to demand more sophisticated and reliable measurement solutions, the importance of these trends becomes more pronounced. Incorporating artificial intelligence and machine learning into profilometry can revolutionize the way data is analyzed, leading to smarter and more adaptive measurement systems.
Integration with AI and Machine Learning
Artificial intelligence and machine learning are reshaping various fields. Their integration into profilometry presents notable advantages. Through intelligent algorithms, systems can learn from historical data, identify patterns, and optimize measurement processes in real time. This adaptability could minimize human error and reduce the time needed for data processing.
Key benefits include:
- Enhanced Accuracy: AI can analyze complex datasets with greater consistency and precision.
- Predictive Maintenance: Machine learning can predict when equipment may require maintenance, prolonging its lifespan.
- Automated Diagnostics: With AI, systems may detect anomalies swiftly, reducing downtime in critical applications.
By using these technologies, profilometry can enhance its relevance in rapidly evolving fields like semiconductor manufacturing and advanced optics.
Increased Data Analysis Capabilities
The ability to analyze increasing volumes of data is another significant trend in profilometry. Modern profilometers are equipped with superior data collection capabilities, generating vast datasets that require sophisticated techniques to interpret effectively. Improved software tools can facilitate comprehensive data analysis, revealing deeper insights about surface characteristics and defects.
Benefits of enhanced data analysis capabilities include:
- Real-time Feedback: Immediate insights allow for rapid adjustments during the measurement process.
- Greater Resolution: Enhanced algorithms enable the extraction of more detailed information from measurements.
- Robust Statistical Analysis: Advanced analytical tools allow for thorough evaluation of measurement uncertainty and trends over time.
This increased analytical capacity will expand the range of applications for profilometers, solidifying their role in both research and industrial settings.
"The integration of AI and enhanced data capabilities marks a critical shift toward smarter, more efficient profilometry solutions that can adapt to future challenges."
Understanding these trends prepares users and researchers alike to leverage new technologies, ensuring that they remain at the forefront of measurement science.
The End
In the exploration of the Zygo profilometer, it is crucial to underscore the integral role this instrument plays in the realm of optical measurement. The Zygo profilometer serves as a cornerstone for precision in various fields ranging from semiconductor manufacturing to material science. Understanding this technology offers profound insights into surface characterization, impacting product quality and innovation.
Summary of Key Points
This article outlined several critical aspects of the Zygo profilometer. Here are the key points:
- Definition and Purpose: The Zygo profilometer is created for precise measurement of surface profiles, essential in numerous industries.
- Operating Principles: The article explained different techniques, such as interferometric and phase-shifting methods, used by the device to obtain accurate measurements.
- Types of Profilometers: Various forms were discussed, including optical and non-contact models, each suited for specific applications.
- Applications: Practical applications highlighted how the Zygo profilometer significantly contributes to quality assurance in semiconductor and optical component manufacturing.
- Calibration Procedures: Regular calibration ensures the accuracy and reliability of measurements, which is vital for maintaining industry standards.
- Challenges in Measurement: Factors such as environmental influences and material properties can affect measurement results.
- Future Trends: Innovations including AI integration are poised to enhance the capabilities and efficiency of profilometry.
Final Thoughts on Zygo Profilometry
The insights gained from understanding the Zygo profilometer present a comprehensive look at its importance in precision measurement and quality control. As industries evolve, this device's adaptability and technological innovations ensure it remains relevant. The continuing advancements in data analysis capabilities will play a pivotal role in shaping the future of optical measurement.
"Understanding the Zygo profilometer is not just about measurement; it is about advancing industries through precision and reliability."
The exploration of this technology continues to be essential for educating future engineers and scientists. Overall, the Zygo profilometer not only exemplifies precision measurement but also embodies the relationship between technology and innovation.