Exploring the Complexities of Mechanical Systems
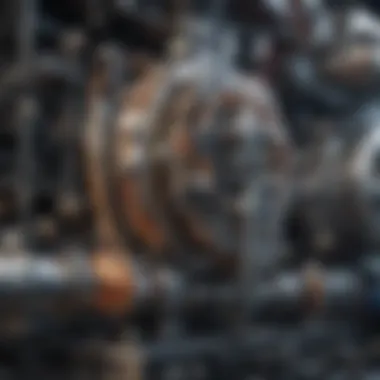
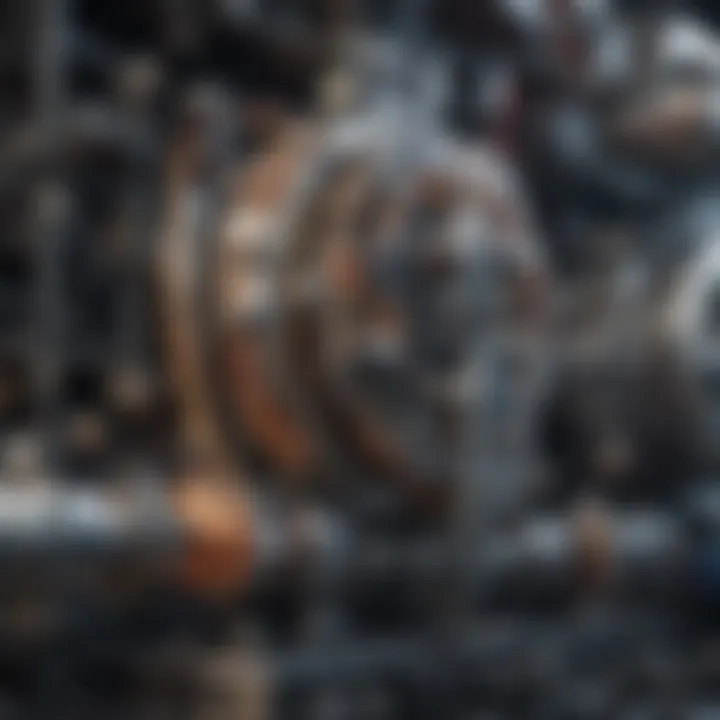
Intro
Mechanical systems play a vital role in our daily lives as they are involved in numerous applications across various industries. Whether in household items, transportation, or advanced machinery, mechanical systems are the backbone of functionality and efficiency. This article intends to explore the underlying principles governing these systems, their materials, design, and the technological advancements that have significantly transformed their development.
By examining these facets, we can gain better insight into how mechanical systems affect different sectors, such as automotive, aerospace, and manufacturing. Concepts like dynamics, kinematics, and thermodynamics will serve as the foundation for understanding how these systems operate. Beyond the scientific background, itβs important to understand the material choices that impact performance and durability, as well as the collaborative approaches that drive innovation in mechanical engineering.
Prologue to Mechanical Systems
Mechanical systems are fundamental structures that govern the operation of machines and devices in both everyday life and advanced industrial applications. Understanding these systems is critical as they form the backbone of a vast array of technologies, from simple tools to complex machinery. Their importance lies not only in their functionality but also in their capacity to be informed by various scientific principles, especially physics.
Benefits of Understanding Mechanical Systems
Familiarity with mechanical systems offers multiple benefits. It enhances problem-solving skills by allowing individuals to identify faults and inefficiencies in systems. Moreover, a solid grasp of these concepts aids in the design and optimization of machinery, often leading to improved productivity and efficiency. By appreciating the underlying mechanics, one can better innovate and contribute to advancements in technology.
Considerations in Mechanical Systems
When discussing mechanical systems, it is essential to consider the implications of design choices, material selection, and the operational environment. Each decision can significantly impact performance and longevity. Newer methodologies and technologies, including automation and robotics, also play a pivotal role in shaping modern mechanical systems.
"Understanding the intricacies of mechanical systems equips professionals with the insights necessary to innovate and address contemporary challenges in engineering."
In essence, an in-depth exploration of mechanical systems not only serves educational purposes but also fosters a practical approach to engineering disciplines, guide research initiatives, and bolster technological progress. This article aims to provide a comprehensive overview, setting the stage for a deeper analysis of the core principles, materials, design concepts, and future trends in the field.
Core Principles of Mechanical Systems
The core principles of mechanical systems serve as the foundation for understanding how these systems operate and interact with the forces and materials around them. They provide a framework that is essential for designing efficient machines and structures. Mechanical systems rely on reliable principles to ensure functionality, safety, and durability. Moreover, they are pivotal in predicting the behavior of systems under various conditions. Knowledge of these principles allows engineers to optimize designs and foresee potential issues.
Newton's Laws of Motion
Newton's Laws of Motion form the cornerstone of classical mechanics. These three laws help to explain how objects move, interact, and respond to forces.
- First Law: An object at rest remains at rest and an object in motion continues in motion unless acted upon by an external force. This law underscores the concept of inertia, which is critical in evaluating how forces will affect a mechanical system.
- Second Law: The acceleration of an object depends on the mass of the object and the amount of force applied. This law is often summarized by the equation F = ma. Understanding this relationship is vital for calculating how much force is needed to move objects within mechanical systems effectively.
- Third Law: For every action, there is an equal and opposite reaction. This principle is crucial when designing mechanisms that involve movement, such as engines or robotic joints, as it helps predict how forces will influence systems.
Grasping these laws is not merely academic; they have direct implications in fields ranging from automotive engineering to aerospace. Engineers often refer to these laws to refine their calculations and improve safety measures in their designs.
Energy Conservation in Mechanical Systems
The concept of energy conservation in mechanical systems asserts that energy cannot be created or destroyed, only transformed from one form to another. This principle is fundamental to both the design and analysis of mechanical systems.
- Types of Energy: Mechanical systems often deal with kinetic energy (the energy of motion) and potential energy (stored energy based on position). For example, a spring stores potential energy that can be converted to kinetic energy when released.
- Practical Implications: Understanding energy conversion efficiency is crucial for engineers tasked with reducing energy waste in mechanical systems. Maximizing efficiency helps improve performance and sustainability.
- Applications: This principle finds applications in a multitude of fields. From optimizing the efficiency of engines to analyzing the behavior of structures under load, energy conservation is a unifying thread in mechanical design.
The effective application of these core principles not only enhances the functionality of mechanical systems but also meets contemporary challenges in efficiency and sustainability. Engineers rely on these principles to innovate and improve technology across various industries.
Materials in Mechanical Engineering
Materials play a fundamental role in the design and functionality of mechanical systems. The selection of appropriate materials not only affects the performance and durability of components but also influences manufacturing processes and cost-effectiveness. A deep understanding of materials helps engineers to innovate and improve mechanical systems with efficiency and sustainability in mind.
Selecting Appropriate Materials
Choosing the right material is crucial for successful mechanical design. Different materials have distinct characteristics, and each choice carries advantages and disadvantages tailored to specific applications.
Metals and Alloys
Metals and alloys are widely used in mechanical engineering due to their strength and durability. They can withstand high stress and offer excellent fatigue resistance. This makes them a favorable option for load-bearing components such as gears and shafts. The unique feature of metals is their malleability, which allows them to be formed into various shapes without breaking.
However, the disadvantage of metals includes susceptibility to corrosion, which can reduce their lifespan in harsh environments. This requires the use of coatings or treatments to enhance their resistance. Despite this drawback, the benefits of using metals often outweigh these challenges, making them essential in many mechanical systems.
Plastics and Composites
Plastics and composites provide a different set of benefits in mechanical systems. Their lightweight nature is one of the most significant advantages. This property reduces the overall weight of devices, leading to improved fuel efficiency in automotive applications. Additionally, plastics can exhibit good chemical resistance, making them suitable for use in various environments.
A unique characteristic of composites is their ability to combine different materials to achieve superior properties. For example, carbon fiber composites can offer high strength-to-weight ratios that metals cannot match. Nonetheless, while they are advantageous in many cases, routines for recycling these materials remain a challenge, which can impact sustainability efforts.
Advanced Materials
Advanced materials, such as smart materials and nanomaterials, are at the forefront of evolution in mechanical engineering. These materials can respond to external stimuli, such as temperature or pressure. The innovative characteristic of advanced materials is their ability to adapt to changing conditions, enhancing the functionality of mechanical systems significantly.
Their advantages include improved performance under specific conditions and the potential for miniaturization of components. On the flip side, the higher cost of advanced materials can be a barrier to widespread adoption. Despite these challenges, their unique properties make them increasingly popular in sensitive applications such as aerospace and medical devices.
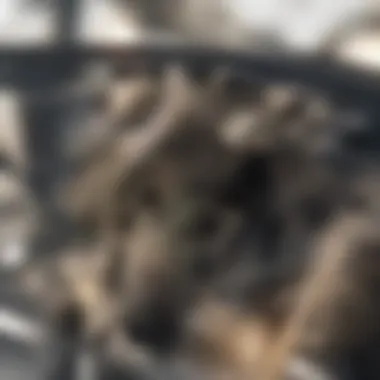

Properties of Materials
Understanding the properties of materials is essential for engineers. Each material behaves differently under various conditions, which affects its suitability for specific applications.
Mechanical Properties
The mechanical properties of a material define its behavior under external forces. These include tensile strength, yield strength, and elasticity. These properties are critical when assessing how materials will perform in mechanical systems. A high tensile strength is beneficial for components that experience tension forces, whereas materials with good elasticity can return to their original shape after deformation.
Knowing these properties helps engineers select materials that can withstand the specific stresses encountered in different mechanical systems. This knowledge optimizes performance and contributes to the reliable operation of mechanical assemblies.
Thermal Properties
Thermal properties refer to how materials react to heat. Given the nature of many mechanical systems, understanding thermal expansion and heat conduction is imperative. Materials that have low thermal expansion are essential for precision applications where dimensional stability is key.
Additionally, materials with high thermal conductivity improve heat dissipation in systems that generate substantial heat. However, choosing materials that manage thermal properties effectively can be limiting if the operating environment features extreme temperatures. This necessitates thorough evaluation during the design stage.
Electrical Properties
Electrical properties are important when a mechanical system needs to conduct electricity. Materials such as copper and aluminum are common for electrical conduction due to their excellent conductivity. On the other hand, insulating materials are essential to prevent unintended electrical flow.
The choice of materials can significantly impact efficiency and safety in electrical circuits. Selecting appropriate conductors and insulators is crucial to ensure effective performance and longevity of the mechanical system.
Design Concepts in Mechanical Systems
In the realm of mechanical systems, design concepts play a pivotal role that transcends mere aesthetics. They inform the functional integrity, efficiency, and longevity of machines and structures. A well-thought-out design can lead to innovative solutions that enhance performance and reduce costs over time. The process involves careful consideration of materials, forces, and the intended use of the system. Every aspect, from the initial sketches to the final prototype, is integral in creating effective mechanical solutions.
Adopting these design concepts also paves the way for enhanced collaboration across disciplines. Engineers, designers, and manufacturers must work together to ensure that all aspects of a mechanical system operate cohesively. This multidisciplinary approach promotes knowledge sharing and results in products that are not only functional but also optimized for sustainability and efficiency.
Computer-Aided Design (CAD)
Computer-Aided Design, commonly referred as CAD, revolutionizes the way engineers and designers approach the design process. Traditionally, designs were created through manual methods, which often resulted in time-consuming iterations. CAD software, such as AutoCAD and SolidWorks, streamlines this process. It allows designers to create accurate and detailed 2D and 3D models efficiently.
One of the significant advantages of CAD is its ability to visualize concepts in a digital format. This allows for better analysis and modifications before any physical prototyping takes place. Moreover, CAD systems often include simulation features that allow for stress testing and analysis of materials under various conditions. Design changes can be made quickly, ultimately saving time and resources.
Prototyping and Testing
Prototyping is the transitional stage between design and production. It involves creating a physical model of the intended system, which can be tested and evaluated. This stage is critical for detecting flaws and assessing performance before mass production begins. A prototype offers valuable insights that are difficult to obtain through CAD simulations alone.
Testing prototypes leads to a more refined final product. Engineers gather data on functionality, durability, and efficiency. The feedback captured during tests is essential in understanding the limits of materials and designs, enabling designers to make informed decisions.
- Benefits of Prototyping:
- Identifies design flaws early in the process.
- Provides a basis for further refinement and optimization.
- Engages stakeholders in the development process.
Dynamics and Kinematics
The study of dynamics and kinematics is crucial for understanding how mechanical systems behave under various conditions. These fields provide foundational knowledge that informs everything from the design of simple machines to complex robotic systems. Understanding motions, trajectories, and the forces that act upon objects allows engineers to predict how systems will perform in real-world applications. This predictability ensures that mechanical systems are both effective and safe.
Analysis of Motion
Kinematics focuses on the description of motion, ignoring the forces that cause it. In practical terms, this means examining position, velocity, and acceleration. Engineers utilize equations of motion to map out how components move relative to one another. The analysis encompasses not only linear motion but also rotational movement, which is equally significant in mechanical designs.
When performing kinematic analysis, engineers often use various tools such as diagrams and simulations. These methods simplify complex systems into manageable models, making it easier to visualize relationships between components. For instance, using tools like MATLAB or CAD software helps to simulate various scenarios, leading to optimal design strategies.
"Understanding motion is the cornerstone of effective mechanical design. Only by analyzing motion can we create systems that function as intended."
Forces Acting on Mechanical Components
In contrast to kinematics, dynamics examines the forces that cause motion. This includes gravity, friction, tension, and normal forces, among others. To design successful mechanical systems, it is essential to account for these forces as they significantly impact performance and durability.
Key considerations in dynamics include:
- Newton's Laws: Applying these fundamental principles helps understand how forces influence motion, ensuring that systems are not only functional but also efficient.
- Force Distribution: Knowing how forces distribute across components assists in selecting materials and designing structures, which directly affects the lifetime and reliability of a product.
- Dynamic Simulation: Advanced simulations can predict performance outcomes under various force conditions, which aids in precautionary design changes before implementation.
Successfully integrating the principles of dynamics into mechanical systems can greatly enhance their functionality and reliability in real-world applications. Engaging with these concepts allows engineers to innovate and solve complex problems within their designs.
Thermal Dynamics in Mechanical Systems
Thermal dynamics plays a crucial role in the field of mechanical systems. Understanding how heat interacts with materials and influences system behavior is fundamental for a range of applications. Mechanical systems often operate under varying thermal conditions, making it essential to comprehend thermal dynamics for effective design and operation. One key element of thermal dynamics is heat transfer, which involves the movement of thermal energy from one body to another. This process is essential for maintaining desired operating conditions in machines and can significantly affect overall performance and efficiency.
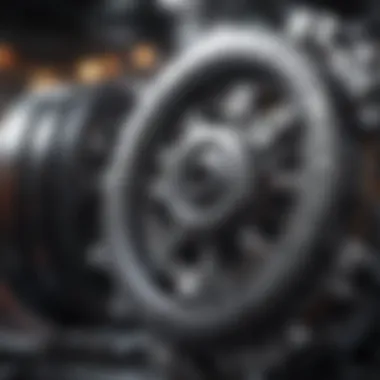
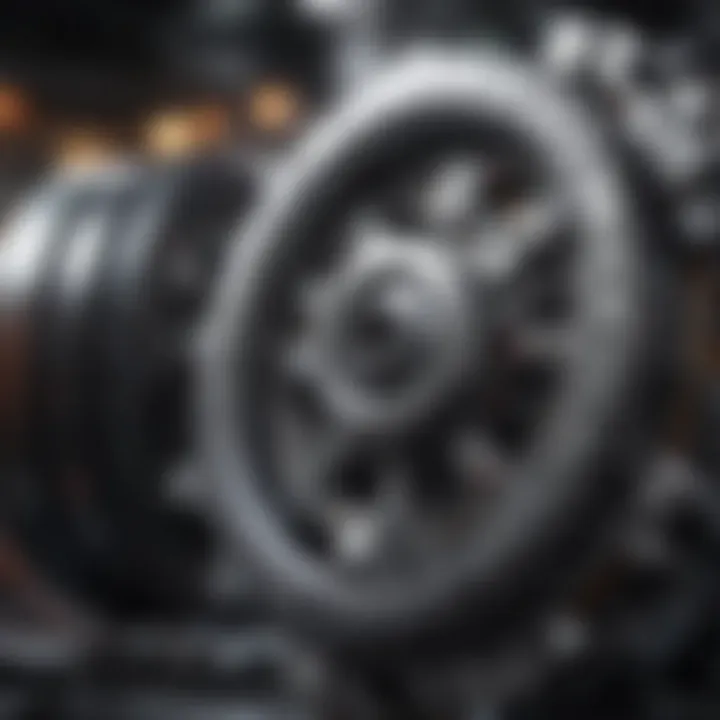
Another benefit of studying thermal dynamics is improved energy efficiency. By analyzing how heat is dissipated or retained in a system, engineers can optimize performance and reduce energy consumption. In an era where sustainability is increasingly prioritized, understanding thermal management solutions becomes essential in reducing the environmental impact of mechanical systems.
Factors such as material choice and system design have direct implications on heat transfer and thermal efficiency. Selection of suitable materials that can withstand specific temperature ranges is vital. Furthermore, designing components to facilitate effective heat exchange leads to enhanced reliability and longevity of mechanical systems.
Heat Transfer Mechanisms
Heat transfer mechanisms are categorized into three primary methods: conduction, convection, and radiation. Each mechanism plays a vital role in how heat moves within and between materials in mechanical systems.
- Conduction involves the transfer of heat through a solid material as kinetic energy is passed between neighboring particles. This mechanism is significant in components like engine blocks or heat sinks, where the material must dissipate heat efficiently.
- Convection is the process of heat transfer through fluid motion, which can be natural or forced. In mechanical systems, fans or pumps often enhance convection by moving air or liquid to improve heat dissipation.
- Radiation refers to the emission of energy as electromagnetic waves. This mechanism is less common in most mechanical systems, but it is still important in specific applications, such as high-temperature processes where heat radiated from hot surfaces can affect performance.
An effective understanding of these mechanisms allows engineers to design systems that manage heat efficiently, contributing to increased functionality and reliability.
Thermodynamics and Machine Efficiency
Thermodynamics is essential to understanding energy transformations within mechanical systems. It governs the principles of energy flow and transformation, which are vital for machine efficiency. The Second Law of Thermodynamics, for example, provides insight into the limits of efficiency for heat engines and other systems that convert energy.
To maximize machine efficiency, engineers often focus on minimizing losses due to heat. For instance, thermal insulation can be used to reduce unwanted heat loss. Additionally, the careful design of thermal systems can help ensure that machines operate within ideal temperature ranges, thus prolonging lifespan and enhancing performance.
Another key concept is the Carnot efficiency, which sets a theoretical maximum efficiency for any heat engine operating between two temperatures. This concept pushes researchers and engineers to innovate new designs or processes that approach this ideal to optimize energy usage in mechanical systems.
In summary, thermal dynamics is not just about managing heat; it's about maximizing performance, ensuring sustainability, and driving innovations in the field of mechanical engineering. Understanding these dynamics provides a framework for addressing contemporary engineering challenges.
Control Systems and Automation
Control systems and automation play a critical role in mechanical engineering, enhancing efficiency and precision across a multitude of applications. These systems enable machines to operate autonomously, thereby reducing the need for constant human intervention. This reduces errors and improves productivity in various sectors, including manufacturing, transportation, and robotics. Effective control systems can monitor and adjust the performance of mechanical components in real-time. Therefore, they directly contribute to the optimization of processes and the enhancement of system performance.
Feedback Control Systems
Feedback control systems form the backbone of automation in mechanical systems. They work by continuously measuring the output of a system and comparing it to the desired input or set point. When there is a deviation from the set point, the system automatically adjusts to correct this. This mechanism is vital for maintaining stability and reliability in operations.
Some key benefits include:
- Precision: Feedback systems improve the accuracy of mechanical operations by ensuring real-time corrections.
- Stability: These systems can stabilize responses in dynamic environments.
- Flexibility: Feedback control allows for the adaptation to changing conditions without the need for human intervention.
Understanding the principles of this technology is essential for engineers who design complex mechanical systems that require autonomy and reliability.
Applications of Robotics in Mechanical Systems
The integration of robotics in mechanical systems has transformed industries by employing advanced automation techniques. Robotics combines mechanical engineering with electronic and computer control systems, enabling machines to perform tasks that are often dangerous or complex for humans.
Robots are used in a variety of fields, such as:
- Manufacturing: Automating repetitive tasks, increasing production speed, and enhancing safety.
- Medical Applications: Performing delicate surgeries or delivering medications with precision.
- Exploration: Vehicles used in space exploration conduct missions far beyond human reach.
The importance of robotics lies not only in efficiency but also in innovation. Robotics improves operational capabilities and can lead to new solutions for existing challenges. As technology advances rapidly, understanding robotics becomes vital for future mechanical engineering practices.
"Automation is not just a goal; it is a journey towards higher efficiency and capability in engineering."
In summary, control systems and automation, particularly through feedback control systems and robotics, are essential components in modern mechanical engineering. They enable increased efficiency, precision, and adaptability in an ever-evolving technological landscape.
Challenges and Innovations in Mechanical Engineering
The field of mechanical engineering is constantly evolving, driven by both challenges and innovations. Understanding these elements is crucial as they shape the future of design and functionality in mechanical systems. Every mechanical engineer must navigate a landscape filled with obstacles such as resource constraints, environmental regulations, and the need for enhanced performance and durability in products. Yet, these challenges also give rise to innovations that enable engineers to solve complex problems and create efficient systems. This section examines sustainability and emerging technologies as key driving forces in overcoming the current obstacles in mechanical engineering.
Sustainability in Mechanical Design
Sustainability in mechanical design is becoming increasingly important as industries face pressure to reduce their environmental footprint. This involves not only using eco-friendly materials but also emphasizing energy efficiency in the design process. For example, mechanical designs that prioritize recyclability ensure materials are not wasted. Such practices are supported by frameworks like Life Cycle Assessment, which evaluates the environmental aspects associated with all stages of a product's life.
Key characteristics of sustainable mechanical design include:
- Energy Efficiency: Optimizing designs to minimize energy consumption.
- Minimal Material Use: Focusing on designs that use fewer resources without compromising quality.
- Reusability and Recycling: Ensuring products can be repurposed at the end of their life cycle.
Implementing sustainable practices can lead to significant cost savings and increase a company's reputation. However, there are challenges such as higher initial costs and potential limitations in material selection that engineers must navigate.
Emerging Technologies
Emerging technologies continue to play a pivotal role in solving traditional challenges in mechanical engineering. Noteworthy developments include 3D printing and smart materials and structures. These innovations not only improve manufacturing processes but also expand possibilities within product design, leading to greater efficiency and functionality.
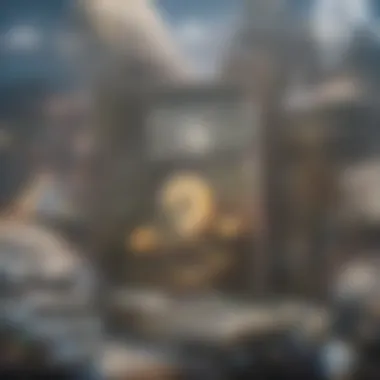
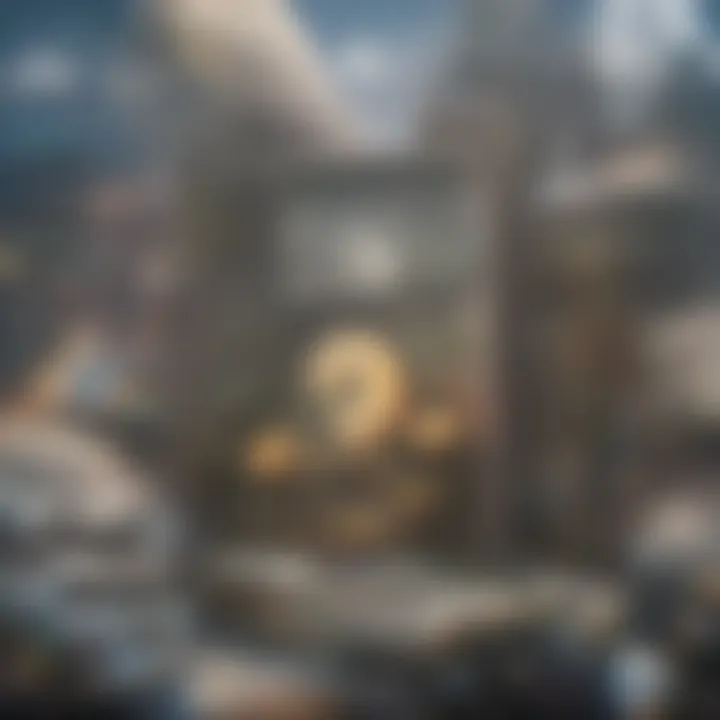
3D Printing in Mechanical Engineering
3D printing, or additive manufacturing, revolutionizes how components are made. It allows engineers to create complex geometries that were previously unfeasible using traditional manufacturing techniques. Key characteristics of 3D printing include:
- Customization: Products can be tailored precisely to meet specific requirements.
- Reduced Waste: Materials are added layer by layer, minimizing surplus material.
Many engineers favor 3D printing due to its flexibility and efficiency. This process significantly cuts down production time and costs associated with tools and molds. However, some challenges persist, such as material constraints and slower production speeds for larger projects.
"3D printing unlocks opportunities for innovation, enabling the creation of parts that meet demanding specifications with unprecedented efficiency."
Smart Materials and Structures
Smart materials and structures are designed to respond dynamically to external stimuli. Their ability to change properties in response to environmental conditions provides extensive benefits in mechanical systems. Key characteristics include:
- Responsiveness: Ability to adapt to changes in temperature, pressure, or other conditions.
- Enhanced Functionality: Smart materials can serve multiple purposes, such as structural integrity and functionality, all-in-one.
The introduction of smart materials can lead to increased efficiency and reduced maintenance costs. However, challenges include the higher cost of these advanced materials and the need for new design approaches to fully integrate their capabilities into existing systems.
As mechanical engineering continues to advance, balancing sustainability with emerging technologies will be essential for the industry's progress and responsibility towards environmental stewardship.
Interdisciplinary Approaches in Mechanical Engineering
The field of mechanical engineering is becoming increasingly complex due to rapid advancements in technology and global interconnections. Interdisciplinary approaches in mechanical engineering play a critical role in addressing contemporary engineering challenges. This approach fosters innovation, facilitates problem-solving, and enhances the capability to design intricate mechanical systems that meet diverse needs.
The integration of various disciplines encourages engineers to look beyond traditional boundaries. Areas like physics, materials science, aerospace, and even psychology can significantly influence mechanical design. By incorporating insights from these fields, engineers are able to create more efficient, sustainable, and user-friendly solutions.
Collaborations Across Disciplines
Collaborative efforts between mechanical engineers and specialists from other fields, such as electrical engineers and environmental scientists, can yield remarkable outcomes. For example, in developing renewable energy systems, a joint effort can combine mechanical engineering principles with environmental science to enhance overall system efficiency.
Some benefits of collaboration include:
- Innovation: New ideas emerge when different perspectives meet.
- Enhanced Problem-Solving: Diverse skill sets lead to comprehensive solutions.
- Resource Sharing: Collaborative projects often utilize shared resources, reducing costs and maximizing efficiency.
Organizations and institutions that promote interdisciplinary teamwork often excel in tackling complex projects. By breaking down silos between disciplines, they foster a culture of learning and adaptability.
Integration of Computer Science and Mechanical Engineering
The fusion of computer science with mechanical engineering represents one of the most transformative trends in the industry. This integration facilitates the development of smart systems that not only perform mechanical tasks but also adapt based on data input.
Examples of integrated technologies include:
- Robotics: Computer algorithms enable robots to learn from their environments, improving operational success.
- Machine Learning in Design: Advanced algorithms support design optimization by predicting performance and identifying potential failures.
- Simulation Software: Computational fluid dynamics and finite element analysis tools are essential for testing mechanical components without the need for costly prototypes.
"The intersection of computer science and mechanical engineering redefines what is possible, leading to systems that are more intelligent and efficient than ever before."
The collaboration between these two fields can lead to significant advancements in industrial automation, material processing, and product lifecycle management. As technology continues to evolve, the synergy between mechanical engineering and computer science will likely dictate the future landscape of engineering design and implementation.
Future Directions in Mechanical Systems
The future of mechanical systems is essential to the ongoing evolution of technology. With advancements in fields such as materials science and artificial intelligence, the implications for mechanical engineering are profound. Understanding future directions can help stakeholders in aligning their projects with emerging trends. This is critical for maintaining competitive advantage and fostering innovation.
Factors such as increased demand for energy efficiency and sustainability play key roles in shaping future mechanical systems. Engineers must consider these demands when designing new solutions. Moreover, interdisciplinary approaches that integrate insights from biology, physics, and computer science are becoming increasingly important. These considerations are crucial for addressing the multifaceted challenges faced by modern engineering landscapes.
The benefits of focusing on future directions in mechanical engineering include enhanced performance, lower environmental impact, and improved user experience. Students and professionals alike can benefit from being proactive in anticipating these changes. Consideration of future trends not only prepares engineers for the next step in their careers but also ensures that industry-wide advancements can be successfully implemented.
"Engineering is not just about building; itβs about building a future that we can all benefit from."
Anticipating Future Trends
Anticipating future trends is vital for engineering fields, specifically in mechanical systems. These trends often emerge from intersection of technology and social demands. Some notable trends include the rise of automation, increasing use of sustainable materials, and the shift toward smart systems.
- Automation: Modern mechanical systems are increasingly utilizing automation through robotics. This accelerates production processes and reduces human error.
- Sustainable Materials: Focus on sustainability impels engineers to innovate in material selection, leading to the use of recycled and biodegradable options.
- Smart Systems: Internet of Things (IoT) has enabled the development of smart mechanical systems. These systems can communicate data to optimize performance dynamically.
The convergence of these trends indicates that engineering practices must evolve to meet emerging demands. Adapting to such shifts requires skill development and openness to new technologies.
The Role of Artificial Intelligence in Mechanical Systems
Artificial intelligence (AI) is revolutionizing mechanical systems by introducing new levels of efficiency and capability. Traditional mechanical systems are now infused with intelligent algorithms that enhance their performance and decision-making. AI can analyze vast datasets and predict outcomes, facilitating improvements in design and methodology.
Key areas where AI plays a significant role include:
- Predictive Maintenance: AI algorithms can monitor equipment health and predict failures before they occur, allowing for timely interventions.
- Design Optimization: AI assists in optimizing designs by analyzing various parameters. This leads to innovations that were not possible with traditional methods.
- Automation: AI enhances robotic capabilities, allowing for more complex tasks and improving operational efficiency in manufacturing environments.
By leveraging AI, mechanical systems can become more adaptive and responsive to real-world conditions. This shift represents not just a technological advancement but a fundamental change in how engineering problems are approached, emphasizing the need for a multidisciplinary perspective, integrating computer science with traditional engineering.