Effective KPI Measurement Strategies in Manufacturing
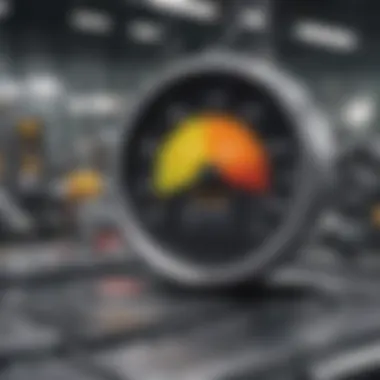
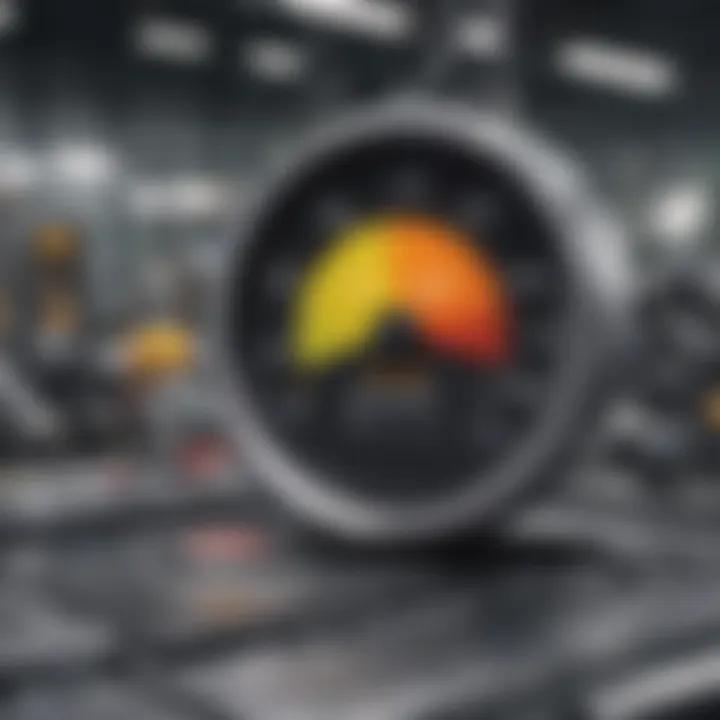
Intro
In the realm of manufacturing, where each component and process intertwines seamlessly like cogs in a machine, the measurement of Key Performance Indicators (KPIs) plays a pivotal role in ensuring operational success. Without effective KPIs, organizations might as well be flying blind, lacking the vital metrics needed to steer their operations towards efficiency and profitability.
Understanding how to measure these indicators is not just about crunching numbers; it’s about grasping the story behind those numbers. By honing in on the right metrics, manufacturers can pinpoint inefficiencies, adapt strategies, and ultimately drive growth. This narrative will take you through the various methodologies of KPI measurement in manufacturing, guide you on interpreting the results meaningfully, and underscore the strategic value these metrics hold for any manufacturing entity.
Research Context
Background Information
From the assembly line to the final product, the manufacturing sector is rife with complexities. Each element—from the materials sourced to the processes employed—can drastically affect the bottom line. Companies today are inundated with data, yet the challenge lies in distilling that data into actionable insights. This is where KPIs come into play. They serve as the compass in the storm of manufacturing data, guiding organizations toward improved performance.
Importance of the Study
The importance of studying KPI measurement in manufacturing cannot be overstated. As industries pivot towards more data-driven decision-making frameworks, having robust methods to measure performance becomes essential. This isn't merely about tracking outputs; it’s about aligning those outputs with strategic goals.
As the industry evolves, firms with a clear picture of their performance metrics are better equipped to adapt to market shifts, enhance productivity, and ultimately secure their place in a competitive landscape.
Discussion
Interpretation of Results
When analyzing KPI results, it’s crucial to look beyond surface figures. For instance, a decline in production efficiency might suggest machine overuse or inadequate training among workers. Therefore, diving deeper into the data can reveal underlying issues that need addressing. By interpreting results in context, organizations can formulate targeted improvements rather than just surface-level fixes.
Comparison with Previous Research
Historical data provides a valuable benchmark for evaluating current performance metrics. For example, if a company has historically maintained a 90% production efficiency and suddenly drops to 80%, it is essential to compare this with prior trends. Are there external factors at play, such as supply chain disruptions? Or do internal processes require reassessment? Comparative analysis with historical data aids in understanding fluctuations and guiding future strategies.
"With the right KPIs, you can transform raw data into powerful stories that drive decisions and foster growth."
In summary, measuring KPIs in manufacturing is not simply about gathering data; it’s the synthesis of insights that form the backbone of strategic decision-making. The alignment of KPIs with corporate objectives ensures that organizations not only remain on track but are also poised for continual improvement and innovation in an ever-evolving industry landscape.
Intro to KPIs in Manufacturing
Measuring Key Performance Indicators (KPIs) in manufacturing is not just a process; it's a roadmap to operational excellence. In an industry that thrives on efficiency, precision, and value creation, KPIs provide the essential touchpoints that organizations need to navigate towards their goals. The weight of KPIs extends far beyond mere numbers; they encapsulate the heartbeat of manufacturing operations, offering insights that can propel a company to new heights.
To understand how KPIs function effectively within a manufacturing context, we have to first get a grip on what makes them tick. These indicators are more than just statistical outcomes; they are carefully crafted metrics aligned with an organization’s strategic objectives. That means they must reflect the particular nuances of the industry, the company at large, and the specific goals of a production cycle.
What’s the real value in having robust KPIs? For starters, they help in evaluating business performance, offering a snapshot of how well a company is performing against its benchmarks. Moreover, they foster accountability at every level of the organization. Everyone from the floor worker to the top management can see how their roles contribute to the bigger picture. KPIs give clarity, driving teams to focus on what truly matters.
Another significant aspect of KPIs in manufacturing revolves around continuous improvement. These indicators are not just set in stone; they adapt with changing circumstances, pressures, and market demands. They act as a feedback loop, allowing organizations to assess, analyze, and refine their processes over time.
In summary, the introduction of KPIs in the manufacturing sector serves as a strategic compass guiding companies through the intricacies of production metrics while ensuring alignment with overarching business goals. This insightful approach helps to bolster performance culture, making it imperative for any serious manufacturing entity to understand and engage with KPIs.
Types of KPIs Relevant to Manufacturing
Key Performance Indicators (KPIs) are the backbone of any robust manufacturing framework. They serve as quantifiable measurements that allow organizations to assess their performance in critical areas. Knowing what metrics to focus on can be the difference between a thriving operation and a floundering one. This section dives into the types of KPIs relevant to manufacturing and their significance in driving efficiency, quality, and profitability.
Production Efficiency Metrics
In the world of manufacturing, efficiency can make or break a project. Production efficiency metrics are foundational KPIs that measure how effectively a company turns raw materials into finished products. Examples of these metrics include:
- Overall Equipment Effectiveness (OEE): OEE offers a snapshot of how well a manufacturing operation performs compared to its full potential. It considers availability, performance, and quality rates.
- Cycle Time: This metric tells you how long it takes to complete one cycle of production, from start to finish. Shorter cycle times generally indicate greater efficiency.
- First Pass Yield (FPY): FPY measures the percentage of products manufactured correctly the first time without requiring rework. High FPY indicates excellent efficiency in production processes.
Optimizing these metrics not only reduces waste but also promotes the effective use of resources, resulting in improved profitability.
Quality Control KPIs
Quality matters enormously in manufacturing. Defect rates and returns not only eat into profit margins, but they can also damage a brand’s reputation. Quality control KPIs help organizations monitor their products and processes to ensure they meet established standards. Key quality metrics include:
- Defect Rate: This is the number of defective products expressed as a percentage of total output. A lower defect rate shows high quality and customer satisfaction.
- Customer Complaints: Tracking complaints can provide insights into quality issues. Frequent complaints might pinpoint flaws in production processes that need addressing.
- Scrap Rate: This indicates the percentage of materials wasted during production. Lower scrap rates signal efficient use of resources and quality control.
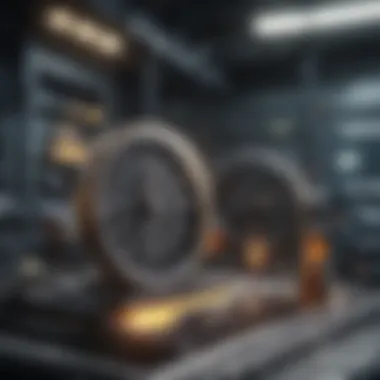
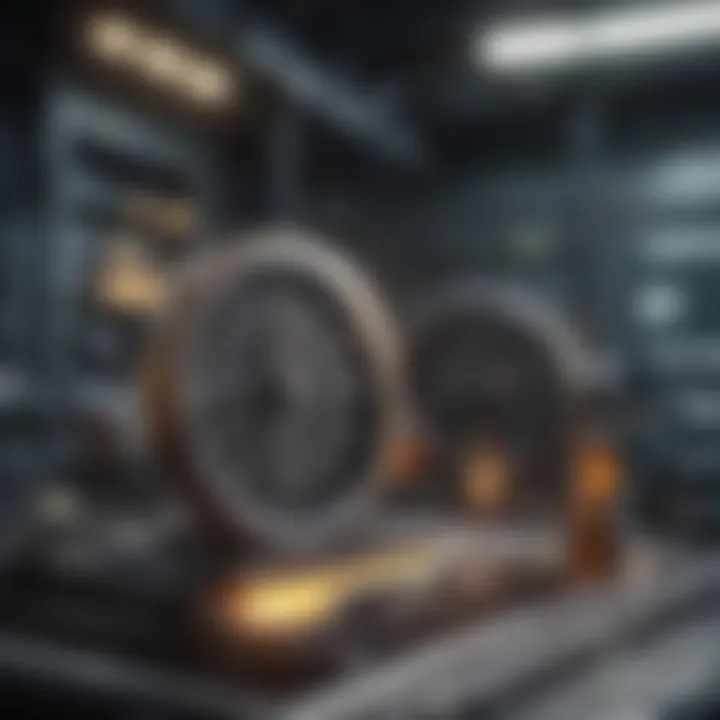
Regularly tracking these quality KPIs fosters continual improvement and can significantly minimize operational risks.
Supply Chain and Inventory Metrics
Supply chain management is another crucial area for manufacturing. Efficient inventory management ensures that production runs smoothly without interruption. Relevant supply chain and inventory KPIs include:
- Inventory Turnover Ratio: This measures how many times inventory is sold or used over a period. A higher turnover indicates better sales or effective stock management.
- Lead Time: Understanding the time from order placement to delivery is essential. Shorter lead times often enhance customer satisfaction and provide a competitive edge.
- Stockout Rate: This metric indicates how often inventory is unavailable when needed. Keeping this number low is crucial for maintaining production workflows.
These metrics are essential as they help organizations fine-tune their supply processes, reducing costs while maximizing efficiency.
Sales and Revenue KPIs
Ultimately, the goal of manufacturing is to drive sales and increase revenue. Monitoring sales and revenue KPIs offers insights into the financial health of a manufacturing entity. Key indicators include:
- Sales Growth Rate: This metric tracks the percentage increase in sales over a set period. A positive growth rate indicates effective market strategies and demand for products.
- Gross Margin: This measures the difference between sales and the cost of goods sold, expressed as a percentage of sales. Higher margins indicate greater profitability.
- Average Order Value (AOV): Knowing the average revenue generated per order helps inform pricing strategies and marketing efforts.
Keeping a close eye on these KPIs helps organizations make informed decisions that can lead to sustainable growth.
"Effective KPI management is not about tracking numbers for the sake of numbers; it’s about using those figures to create tangible improvements in the manufacturing process."
In summary, honing in on the relevant types of KPIs is crucial for manufacturing success. Each category brings unique insights that drive decision-making and operational improvement, elevating a business's capacity to respond to market demands.
Establishing KPIs Based on Business Objectives
Defining Key Performance Indicators (KPIs) that resonate with your specific business objectives is like mapping the route on a treasure hunt. Cutting through the ambiguity, a targeted approach enables companies to zero in on their desired outcomes efficiently. Establishing KPIs based on objectives not only lays a firm foundation for operational effectiveness but also infuses a strategic perspective into daily manufacturing activities. Without this alignment, KPIs can become just numbers on a report rather than meaningful measures of success.
Aligning KPIs with Strategic Goals
Aligning KPIs with strategic goals starts by identifying what truly matters for your business. This means digging deep into the company’s mission, vision, and long-term objectives. One must ask questions such as: What is the core intention behind our manufacturing efforts? Are we focusing on maximizing profit, enhancing quality, or perhaps driving innovation?
Here are some essential elements to consider:
- Clarity of Purpose: Every KPI should stem from an overarching goal. For instance, if a company aims to reduce costs, metrics like production costs per unit or downtime can serve as effective KPIs.
- Measurable Outcomes: Establishing KPIs that can be quantified is critical. Choose metrics that can be tracked over time, providing clear insights into progress.
- Balance: Avoid leaning too heavily on one aspect. A combination of KPIs covering productivity, quality, and customer satisfaction ensures a well-rounded perspective.
By ensuring a coherent link between KPIs and strategic business goals, organizations not only bolster performance monitoring but also aid in better decision-making processes. Regularly revisiting and refining these KPIs ensures they remain relevant as business objectives evolve.
Involving Stakeholders in KPI Development
Involving stakeholders in the KPI development process is akin to having a chorus rather than a solo. When multiple voices come together to share their insights, it fosters a comprehensive viewpoint that can lead to more effective metrics. Stakeholders, ranging from floor workers to upper management, each have unique experiences and insights. This means their input is invaluable.
Consider the following benefits:
- Enhanced Buy-In: When stakeholders are part of the KPI creation process, they are more likely to be committed to achieving these targets.
- Diverse Perspectives: Without input from those who execute tasks daily, KPIs might lack practicality. For instance, involving machine operators might reveal that a potential KPI on machine downtime needs tweaking based on real-world usage patterns.
- Improved Relevance: Stakeholders can help ensure that the KPIs selected are truly relevant to their functional areas and reflect their capabilities and responsibilities.
Involving stakeholders isn't just a nice-to-have; it leads to a more solidified understanding of the KPIs and the tasks they govern. This inclusive approach not only strengthens relationships across the board but also creates a culture rooted in collaboration, enhancing overall performance.
Ultimately, establishing KPIs based on business objectives requires a delicate balance of alignment and involvement. As organizations embark on this journey, taking the time to ensure that every piece of the puzzle is in its right place will pave the way for insightful data that genuinely reflects operational performance and strategic success.
Data Collection Methods for KPI Measurement
Data collection methods for Key Performance Indicators (KPIs) are essential for accurately gauging manufacturing efficiency and effectiveness. Without reliable data, the entire framework of KPI measurement crumbles. This section delves into two primary methods: automated data collection systems and manual data entry. Each method has its benefits and considerations, which are critical for professionals involved in KPI measurement.
Automated Data Collection Systems
Automated data collection systems serve as the backbone of a well-oiled manufacturing operation. They enable companies to gather data seamlessly and consistently, leading to a treasure trove of information on various metrics. These systems use various technologies such as sensors, barcode scanners, and IoT devices to capture data in real time.
Benefits of Automated Systems:
- Efficiency: By removing the human element from data recording, these systems can operate continuously, gathering more data than manual processes. This leads to quicker decision-making based on up-to-date information.
- Accuracy: Automated methods minimize the risk of human error, a common pitfall in manual data entry. This leads to greater reliability of the KPIs established.
- Real-time Insights: They facilitate immediate data access, allowing manufacturers to respond to issues as they arise rather than waiting for periodic reports.
Despite the clear advantages, organizations must also consider their initial investment for these systems. There’s need for training and maintenance, which tends to be overlooked. Specifying goals before implementation is vital to ensure these systems meet business needs effectively.
Manual Data Entry and Its Challenges
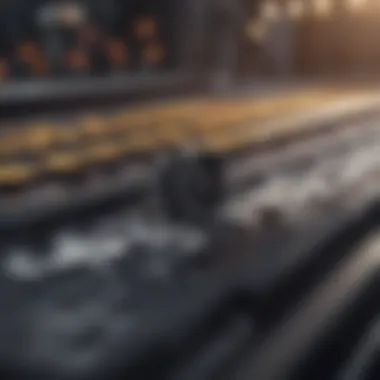
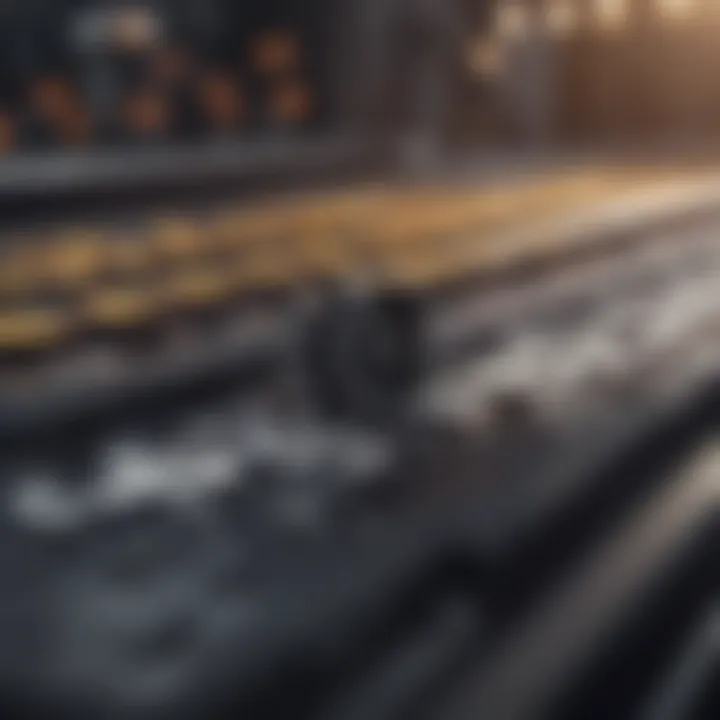
Manual data entry, while increasingly being overshadowed by its automated counterpart, remains prevalent in many manufacturing environments, especially smaller ones or those with limited budgets for tech solutions. In this method, operators or clerks collect data from various sources and input it into designated systems.
Challenges Faced with Manual Data Entry:
- Error Rates: This method is prone to human error, which can lead to inaccurate KPI measurements. A simple typo can throw the whole analysis off-kilter.
- Time Consuming: Recording data manually is labor-intensive and often leads to delays in processing. This can hinder timely decision-making.
- Lack of Real-Time Data: Unlike automated systems, manual entries are typically made at specific intervals, which means missed opportunities for immediate insights.
To counter these challenges, organizations can implement routine audits of data quality and provide thorough training for staff involved in data entry. It’s also beneficial to integrate some level of automation into the manual process when possible, enabling a smoother transition toward more efficient data gathering practices.
In the world of manufacturing, accurate data collection isn’t just a box to check; it’s a cornerstone of strategic development and operational excellence.
Analyzing KPI Data for Insight Generation
Certain facets are critical when it comes to analyzing KPI data in manufacturing. First and foremost, the ability to sift through vast arrays of data helps firms pinpoint exactly what’s influencing their operations. This is not just about numbers; it's about understanding the story those numbers tell. Developing a keen sense of observation toward this data fosters better decision-making. When you align your analysis strategy with specific business goals, it amplifies not only efficiency but also engagement across your organization.
One of the vital reasons to focus on KPI analysis is to turn raw numbers into actionable insights. Unpacking this concept is essential. Imagine a factory that produces wooden furniture. The KPIs might indicate a high defect rate. Analyzing this data can reveal problems such as machinery malfunction, insufficient training, or raw material quality. Once identified, necessary adjustments can lead to significant improvements. Without analysis, these issues remain concealed, often leading to wasted resources and inflated costs.
"Data only tells you what happened; it takes analysis to understand why it happened."
In the modern landscape, where technology reigns supreme, leveraging data analytics tools has never been more straightforward. Many solutions come pre-packaged with user-friendly interfaces and extensive support, allowing teams to get insights without needing advanced data science skills. However, there's a caveat: reliance on these tools must be balanced with human expertise. While software excels in crunching numbers, human intuition and experience are paramount in interpreting those results accurately.
Using Data Analytics Tools
Deployment of appropriate data analytics tools is crucial for deriving comprehensive understandings from KPI data. Think of these tools as Swiss Army knives. They can dissect information in myriad ways, giving you the breathing room to focus on the core issues rather than getting lost in spreadsheets. Tools like Tableau or Power BI are commonly employed to visualize data, letting users see trends and patterns at a glance.
Moreover, real-time dashboards are invaluable as they offer instant access to KPIs. This immediacy means that any alterations in performance can be identified almost on the go. Understanding the metric’s visual presentation makes it easier for teams to collaborate around the insights gained, encouraging communication across departments.
However, when utilizing these tools, professionals should consider these aspects:
- Data Integration: Ensure that all relevant data sources are connected. If not, your conclusions might be skewed.
- User Training: Invest time in educating your staff on how to maximize the functionality of these tools.
- Customization: Tailor reports and dashboards to the specific needs of your business units for better clarity.
Interpreting Results and Identifying Trends
Now that the data is neatly arranged and visuals are ready, the next step requires a discerning eye. Interpreting results isn’t merely about looking at numbers; it involves digging beneath the surface. For instance, a rise in production efficiency may seem beneficial at face value, but a closer examination might show that it's resulting from overworking employees or neglecting equipment maintenance.
Identifying trends over time helps in understanding how various factors interplay within the manufacturing process. Spotting these patterns does more than just highlight success or failure; it provides insights into operational temperaments. Perhaps, every July, there's a noticeable dip in production quality—a pattern often tied to seasonal employee turnover. Identifying this trend allows companies to prepare and plan ahead, minimizing disruptions.
To add layers to your interpretation process, consider using layered metrics. For instance, combine information from production quality KPIs with employee engagement scores. This merge can showcase correlations that would be unseen when looking at metrics individually.
In summary, proper analysis of KPI data is a dynamic process that can fuel insightful improvements in manufacturing practices. It challenges manufacturers to not just rely on what the numbers are, but to explore deeper meanings and connections behind those figures. This level of scrutiny sets the stage for ongoing assessment and fosters an environment ripe for innovation.
Challenges in Measuring KPIs
Measuring Key Performance Indicators (KPIs) in manufacturing is not a walk in the park. It’s often fraught with obstacles that can hinder accurate evaluation and lead to misguided strategies. Understanding these challenges is critical for professionals aiming to enhance operational efficiency and informed decision-making. Recognizing these barrier can pave the way for more effective KPI implementation and ensure that metrics accurately reflect the manufacturing operations they’re intended to monitor.
Data Accuracy and Reliability Issues
One of the most pressing challenges in measuring KPIs is ensuring that the data collected is both accurate and reliable. In manufacturing, decisions are sometimes made based on data that can be flawed or misrepresented. Issues such as manual data entry errors, outdated information, or even system malfunctions can lead to discrepancies. Therefore, businesses must adopt stringent data governance practices.
Consider using automated data collection systems as they often reduce human error and enhance the reliability of the metrics being produced. Moreover, establishing a regular audit trail can help in identifying any inconsistencies.
It’s also useful to invest in training staff about the importance of data integrity. This can foster a culture where employees understand how vital their role is in maintaining accuracy, ensuring that data isn’t just numbers on a page, but insights that drive the organization forward.
"Accurate data is like solid gold; you need it to build anything worthwhile in manufacturing."
Resistance to Change in Organizational Culture
Another noteworthy hurdle in measuring KPIs in manufacturing lies in the organization’s readiness to adapt to new systems or processes. It’s not uncommon for employees to resist changes due to a fear of the unknown or a belief that current methods are adequate. This resistance can manifest in a variety of ways—from open defiance to passive non-compliance.
To tackle this, leadership must actively engage employees throughout the KPI development and implementation process. Involving staff in discussions about why KPIs are essential, what benefits they stand to gain, and how these metrics will be monitored can help lessen anxiety related to change. Additionally, fostering a culture that celebrates innovation and flexibility can ease the transition to a more data-driven approach.
Providing incentives for employees who embrace and effectively utilize KPIs can also enhance acceptance. The endgame is not just about measuring performance but creating an environment that values continuous improvement, where every individual feels they have a stake in the outcome.
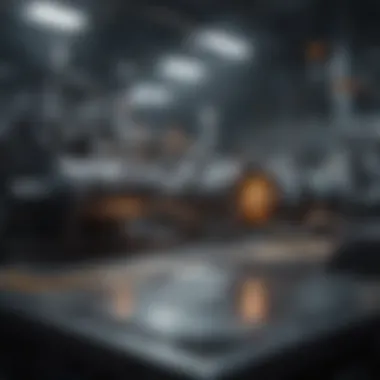
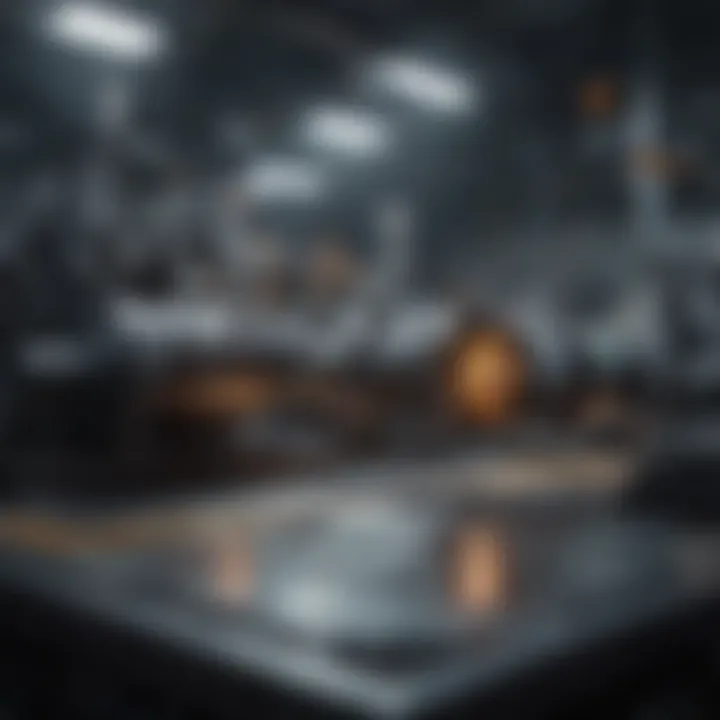
Best Practices for Implementing KPIs
Understanding how to effectively implement Key Performance Indicators (KPIs) is crucial for any manufacturing entity. Effective KPI implementation enhances focused performance and drives the organization towards its strategic objectives. Well-defined practices help bridge the gap between lofty goals and practical action. It’s not merely about identifying what to measure but rather about making sure the measurement helps the business in the way it intends.
Setting Realistic Targets and Benchmarks
When it comes to KPIs, setting targets is akin to having a roadmap for a journey. It directs the course and ensures that everyone involved knows the destination. However, these targets must be realistic. Setting the bar too high can lead to frustration, while targets that are too easy can induce complacency.
To achieve realistic target-setting:
- Understand Historical Performance: Reviewing past data provides baseline metrics. Use previous performance trends to inform future targets.
- Engage Team Members: Collaboration often brings insights that upper management might overlook. Involving the workforce in target-setting not only garners buy-in but also helps to create more achievable goals.
- Incremental Adjustments: Begin with achievable targets that can gradually align with longer-term goals. This gradual progression encourages a sense of accomplishment.
An example: If a factory produced 800 units a day last quarter, expecting to leap to 1,200 units might be ambitious, but setting a target of 900 can inspire improvement without overwhelming the team.
Regularly Reviewing and Adjusting KPIs
The business landscape is not static, and neither should be the KPIs. Regular reviews are paramount to ensure that these indicators remain relevant. A KPI that once suited the business context may no longer apply due to various factors like market shifts, technological advancements, or internal process changes.
Steps for effective reviewing and adjusting:
- Schedule Reviews: Establish a regular cadence for reviewing KPIs. Monthly or quarterly check-ins can help assess if the indicators still align with current operations and strategic goals.
- Solicit Feedback: Engage with personnel at all levels to understand how the KPIs are perceived. Does the data reflect the reality on the ground?
- Adapt to Insights: If KPI data indicates a significant shift in operations or productivity, adjust targets accordingly. Flexibility can often lead to better alignment with business objectives.
For instance, if a company notices a decline in production efficiency due to supply chain issues, adjusting the efficiency KPI to reflect achievable production levels while still addressing the underlying issues can help maintain morale and drive.
The key to successful KPI implementation lies in recognizing that these indicators are not cast in stone. They should evolve with the business, providing a dynamic framework for continuous improvement.
The Role of Continuous Improvement in KPI Measurement
In the dynamic world of manufacturing, measuring KPIs is not a one-time affair. It’s a journey, akin to a never-ending road trip where every mile adds to the experience. This is where the concept of continuous improvement comes into play. By integrating a mindset of ongoing enhancement into KPI measurement, manufacturers can adapt, refine, and optimize their operations with greater precision.
Integrating KPIs into Lean Manufacturing Practices
Lean manufacturing emphasizes waste reduction while maximizing productivity. It’s like carving away the excess from a block of marble to reveal a masterpiece. When KPIs are woven into lean practices, they serve as vital indicators that guide teams to identify inefficiencies and streamline processes. Specifically, KPIs can track metrics such as cycle times, lead times, and overall equipment effectiveness (OEE).
By focusing on these metrics, organizations can:
- Spot inefficiencies: Direct observation of KPIs can highlight areas where processes slow down, guiding interventions that eliminate waste.
- Encourage a team mentality: Lean practices thrive on teamwork. Using KPIs collaboratively can empower everyone from floor workers to team leaders to work together towards common objectives.
- Foster agility: Since manufacturing is subject to various disruptions – be it supply chain issues or shifting demand – having KPIs tied to lean methods allows for swift adaptations without losing sight of overall goals.
Imagine a factory floor where every worker understands the metrics that define success. That’s the power of integrating KPIs into lean practices.
Using KPIs to Foster a Culture of Innovation
Creating an innovative environment isn’t just about encouraging creativity but also about leveraging data-driven insights. KPIs can significantly contribute to this cultural shift. When teams observe performance data regularly, they can identify opportunities for product improvements, new processes, or even groundbreaking technologies.
- Encourage experimentation: With clear KPIs in place, teams are more likely to take calculated risks, knowing they can measure the outcomes effectively. This transforms a highly regulated environment into one that values experimentation.
- Celebrate successes and learn from failures: KPI measurement doesn't just spotlight failures, it celebrates achievements too. Recognizing when a KPI has improved boosts morale and encourages continued innovation.
- Continuous feedback loop: KPIs create a feedback mechanism that informs all levels of decision-making. By utilizing this data, managers can adjust their strategies, foster creative solutions, and drive innovation throughout the organization.
"Innovation and improvement are not just goals; they’re an ongoing journey fueled by informed decisions."
In essence, the role of continuous improvement in KPI measurement enables manufacturers to sustain high levels of efficiency and creativity. By embedding KPIs into lean methodologies and using them to nurture innovation, organizations can truly position themselves as leaders in the manufacturing sector.
Finale
The measurement of Key Performance Indicators (KPIs) in manufacturing stands as a linchpin for operational success. In a rapidly evolving industry landscape, harnessing the full potential of KPIs can drive productivity, enhance quality, and ultimately bolster profit margins. Understanding each facet of KPI measurement ensures that organizations can adapt to fluctuating market demands while maintaining solid performance metrics.
Summary of the Importance of KPIs in Manufacturing
KPIs serve as the compass guiding manufacturers towards their strategic objectives. By clearly defining what success looks like, they provide measurable goals that can be tracked over time. Consider the following key points about KPIs in manufacturing:
- Benchmarking Performance: KPIs allow for comparisons against industry standards or historical data, making it easier to spot trends or patterns in performance.
- Identifying Improvement Areas: By analyzing KPI data, manufacturers can identify where operations might be lagging—be it in production efficiency or quality control.
- Facilitating Decision Making: With reliable data, decision-makers can make informed choices that align with overall business strategy, thus minimizing risks.
- Improving Employee Engagement: When employees understand the KPIs that matter, they are more likely to engage positively with their work.
In essence, KPIs create a structured approach to managing performance and pushing for continuous improvement across all levels of manufacturing.
Future Trends in KPI Measurement
As technology continues to advance, the future of KPI measurement in manufacturing is looking brighter with a few notable trends. Organizations are increasingly leveraging big data, IoT devices, and machine learning to hone their KPI frameworks. Here are a few expected trends:
- Real-Time Data Visualization: With the integration of advanced analytics tools, manufacturers can track KPI performance in real time, making adjustments much faster.
- Predictive Analytics: Future KPI frameworks are expected to incorporate predictive capabilities, enabling businesses to forecast outcomes and drive proactive decisions.
- Customization of KPIs: There is a growing trend towards customizing KPIs to tailor them closely to specific operational needs rather than relying on one-size-fits-all metrics.
- Holistic Performance Indicators: As companies push towards sustainability, environmental and social performance indicators are expected to become increasingly relevant in KPI measurement, reflecting a broader view of success.
These evolving trends emphasize the need for manufacturers to remain agile and responsive. Adopting innovative approaches to KPI measurement ensures that organizations don’t just keep pace with changes but thrive amid them, ensuring long-term profitability and sustainability.