Applications and Techniques of 3D Printing Wax Molds
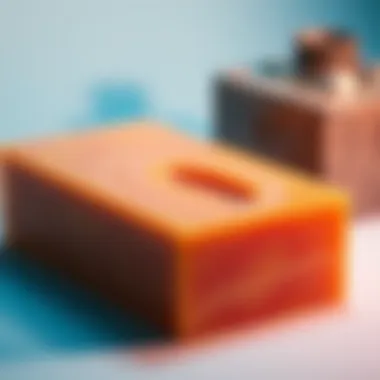
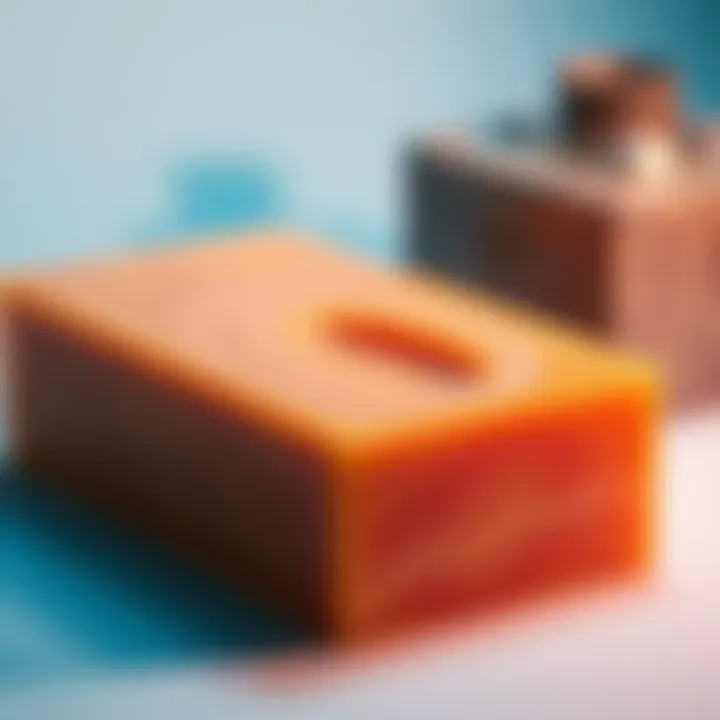
Intro
The dawning of 3D printing has ushered in a new age for multiple industries, redefining traditional practices through innovation. Among the various applications of this technology, 3D printing wax molds stands out for its versatility, particularly in fields like jewelry making, dentistry, and prototyping. The fusion of traditional methods with cutting-edge technology provides an avenue for enhanced precision, speed, and creativity, thus becoming a focal point of exploration.
Understanding the potential applications of wax molds crafted through 3D printing is crucial. This method not only streamlines production processes but also significantly reduces errors. As a result, artists and professionals are able to bring their visions to fruition more effectively.
In this article, we will delve into the various techniques employed in creating wax molds, analyzing their significance and the challenges that come with adopting such practices. Students, researchers, and industry professionals alike will find this exploration to be both informative and essential, considering the growing relevance of additive manufacturing in today’s world.
Prelude to 3D Printing Wax Molds
The advent of 3D printing has not just been a mere shift in technology, it has sparked a whole new realm of possibilities within various industries. Among the most compelling applications is the production of wax molds, which revolutionize traditional processes in art, dentistry, and manufacturing. The importance of understanding 3D printing wax molds lies in their efficiency, precision, and the unique characteristics they bring to the table.
Definition and Overview
3D printing wax molds refer to the technique of using specialized printers that fabricate objects in wax, typically meant for casting procedures. Unlike standard 3D printing, which often employs plastics or metals, the use of wax is integral here because it allows for more intricate designs without compromising on the usual strength required for casting. Wax molds serve as the prototype that can be easily melted away, enabling the final product to be formed from a variety of materials, usually metals like gold or silver, in jewelry, or other durable substances for industrial applications.
Historical Context
Looking back, the use of wax for casting isn’t entirely recent. Historically, craftsmen relied on the lost-wax casting method—dating back to ancient civilizations such as the Egyptians and Greeks. This method involves creating a wax model and encasing it in a material that hardens. Once the mold is set, the wax is melted away, leaving a cavity for pouring molten metal. The integration of 3D printing into this process marks a significant evolution, streamlining what once could be a labor-intensive craft into a more automated and precise operation. This blend of age-old techniques with modern technology exemplifies a pivotal moment in manufacturing evolution, enhancing both speed and accuracy.
Importance of Wax in Mold Making
Wax plays a critical role in the mold-making process primarily due to its melting properties and ease of handling. This material can capture fine details—an essential feature in sectors like jewelry design, where even the slightest nuances matter. Furthermore, compared to other materials, wax can be relatively easy to work with. It can be melted down to create new molds, thus reducing waste and making the production process more sustainable. In healthcare, particularly in dentistry, wax molds are utilized for creating precise replicas of patient anatomy, which aids significantly in treatment planning and execution.
"The transition to 3D-printed wax molds isn’t just about speed, it’s about elevating the artistry and precision of the craft, bridging the gap between technology and tradition."
In summary, the deep-rooted significance of wax in mold making can’t be overstated. It blends tradition with modern capabilities, paving the way for innovations in various realms. By marrying historical context with contemporary applications, we lay the groundwork for a closer look into what 3D printing can achieve in the realm of wax molds.
Understanding 3D Printing Technology
The world of 3D printing has grown rapidly, finding practical applications in numerous industries, particularly with wax molds. Understanding this technology is essential as it serves as the backbone for creating accurate, intricate, and bespoke items—from jewelry to dental prosthetics. Knowing how various techniques operate allows professionals to select the most suitable method for their project, ensuring both quality and efficiency in the process.
Different Types of 3D Printing Methods
Every approach to 3D printing comes with its own strengths and weaknesses, particularly when it comes to creating wax molds. Here’s a closer look at three prevalent methods:
Fused Deposition Modeling (FDM)
Fused Deposition Modeling is a widely used technique in the realm of 3D printing. It works by extruding melted material—usually thermoplastics—through a nozzle, layer by layer, to form a solid object.
The advantageous aspect of FDM lies in its cost-effectiveness and accessibility. For individuals or businesses just getting started in 3D printing, this method provides a low entry price, enabling them to experiment without breaking the bank. However, the finish quality is often not as smooth compared to other methods, which can be a drawback, especially when fine detail is required in wax molds.
Stereolithography (SLA)
Stereolithography operates on a different principle: it uses a laser to cure liquid resin into hardened plastic. This technique excels in producing high-resolution prints with intricate details. Many jewelers and dentists prefer SLA for wax mold applications because it allows for a finer finish and better accuracy.
While SLA captures complex designs beautifully, the resin used can be more expensive, and the printing process often takes longer. Additionally, the need for post-processing, like cleaning and curing, can make this method a bit cumbersome for some users.
Selective Laser Sintering (SLS)
Selective Laser Sintering involves using a laser to fuse powdered material together, building up layers of a solid object. This method is known for its durability and ability to produce functional prototypes.
The beauty of SLS lies in its versatility with materials, including certain waxes, which allows it to create robust molds that can withstand high temperatures. However, the initial investment for SLS machines is quite steep, making it less accessible for small-scale users.
Material Compatibility and Selection
Selecting the correct material is crucial when working with 3D printing wax molds. The properties of wax materials can drastically influence the final product.
Properties of Wax Materials
Wax materials play an integral role in the quality of the final mold. Ideal waxes should possess a good balance between melting point, flow characteristics, and cooling time.
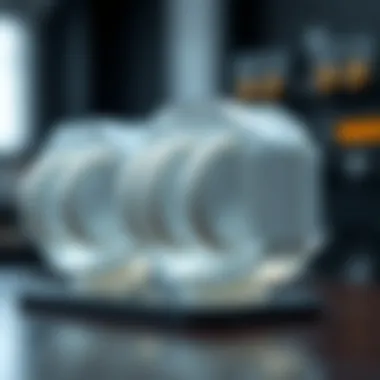
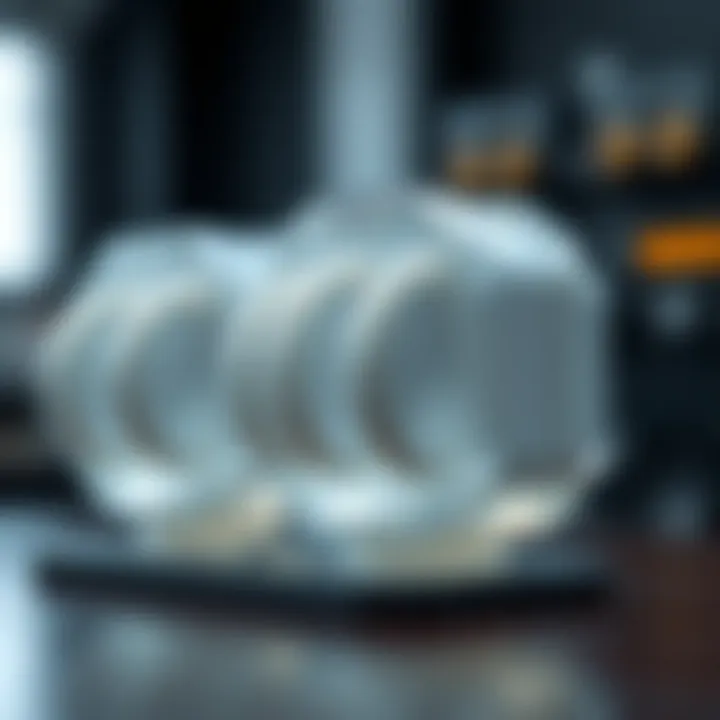
These properties determine how well the wax holds detail during printing and whether the finished mold can endure the casting process without warping or cracking. The paramount reason for using wax is its excellent ability to melt away cleanly, leaving behind a precise cavity for casting metals or other materials. However, wax can also be sensitive to extremes in temperature, which could pose storage and handling issues.
Considerations for Choosing Wax Types
When selecting wax for 3D printing molds, various factors come into play. Each type of wax is designed for specific applications; some are formulated for durability, while others are optimized for detail.
For instance, harder waxes might be more suitable when making mold impressions that are going to undergo heavy usage. On the other hand, softer waxes may allow for finer detailed work, crucial for intricate jewelry designs.
The decision rests not just on the desired outcome but also on the capabilities of the printer being used. Choosing the wrong type can lead to complications in the printing process, such as inadequate layer adhesion or even complete failure of the mold.
"The right wax can spell the difference between a successful mold and a disappointing failure. It’s not just about the end product, but the process as a whole."
In summary, comprehending the methodology and material choices in 3D printing wax molds equips manufacturers, designers, and artisans with essential insights that directly influence production outcomes. This knowledge is vital for those aspiring to harness the full potential of 3D printing technology.
Applications of 3D Printing Wax Molds
The applications of 3D printing wax molds span a wide range of industries, showcasing the versatility and efficacy of this technology. Understanding these applications is crucial, as they provide insight into how such techniques can revolutionize processes in fields as varied as jewelry making, dentistry, and industrial prototyping. The specific elements highlighted in this section not only illustrate the flexibility of wax molds but also emphasize the increasingly crucial role they play in accelerating production, enhancing design fidelity, and minimizing waste.
Jewelry Design and Production
Rapid Prototyping Techniques
Rapid prototyping serves as a linchpin in modern jewelry design. This approach allows designers to translate their ideas into tangible objects much quicker than traditional methods. The characteristic speed of rapid prototyping means that designers can iterate their concepts rapidly, reducing the time between conception and realization. This is particularly beneficial in a market where trends shift faster than you can blink.
One unique feature of rapid prototyping is the ability to create complex designs that would be next to impossible using conventional techniques. The detail captured when creating wax molds allows jewelers to experiment freely, pushing the boundaries of creativity. The advantage here is clear; designers reduce the risk and cost associated with making changes after initial casting. However, it’s essential to note that while the technique is good at detailing, the strength of the mold can sometimes be an issue, particularly for very intricate designs.
Precision Casting Advantages
Precision casting offers remarkable benefits that enhance the overall quality of jewelry production. This technique relies on the high intricacy achievable through wax molds, resulting in pieces that have fine surface details and smooth finishes. This means that the final cast items exhibit greater accuracy compared to items produced through traditional methods. This characteristic makes precision casting highly desirable for jewelers aiming to deliver high-quality products.
A unique advantage of this method is that it minimizes material waste, which is especially important in jewelry production where gold and other materials can be costly. However, one thing to keep in mind is that the initial investment for equipment and materials can be higher than simpler techniques. Still, the long-term gains in the quality of production and customer satisfaction often outweigh these initial costs.
Dentistry and Medical Applications
Crown and Bridge Work
In the realm of dentistry, the production of crowns and bridges has seen significant improvements through 3D printing wax molds. These molds allow for an exceptional level of customization to fit each patient’s specific needs, which is a key characteristic of modern dental practice. A prominent aspect of this application is time savings; processes that once took days or even weeks can now often be completed within hours.
The unique feature here is the high degree of accuracy in fit; these wax molds ensure a snug, comfortable, and precise attachment, strongly influencing patient satisfaction. However, the initial learning curve and the requirement for skilled technicians to operate the machinery may represent challenges in clinics that are more traditional in their approaches.
Custom Implant Solutions
Custom implant solutions are another crucial application in the medical field made possible through wax molds. By utilizing this technology, healthcare providers are able to develop implants tailored for individual anatomy. The distinct advantage here is that these custom models can lead to better post-operative outcomes for patients, paving the way for improved recovery times and comfort.
What sets custom implant solutions apart is their ability to streamline patient-specific treatment plans, ensuring that every aspect, from shape to fit, is optimized for the individual. However, it's important to highlight the potential drawbacks, like the costs involved in design and fabrication that may deter some practices from fully integrating these advanced solutions.
Architectural and Industrial Prototyping
Complex Geometry Creation
The ability to create complex geometrical shapes is one of the standout benefits of using 3D printing wax molds in architectural and industrial contexts. These molds offer designers the freedom to explore avant-garde architectural ideas that challenge traditional forms. This capability allows for innovative structures that are both aesthetic and functional, making it a favored choice among architects looking to make a statement.
The flexibility in design is one distinct feature; adjustments can be made with ease, enabling architects to quickly adapt to design feedback without incurring high costs. On the downside, the intricacy may lead to production issues if the equipment isn’t correctly calibrated for delicate designs, necessitating a highly trained workforce to mitigate risks.
Testing and Iteration Processes
Testing and iterating designs is essential in both architectural and industrial settings. 3D printing wax molds allows for rapid testing of these designs, facilitating a swift cycle of creation and feedback. This process is essential in determining site viability and feasibility. Quick iterations help reduce expensive redesign phases that can delay projects significantly.
The unique aspect of this process is the chance to refine every detail before the final production, leading to better-informed decisions. However, one must also contend with the potential for dependency on technology; if the software or machinery goes down, it can stall the entire project.
Production Process of 3D Printing Wax Molds
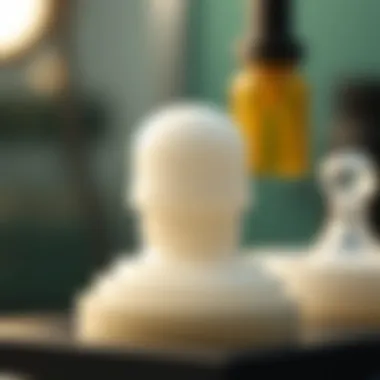
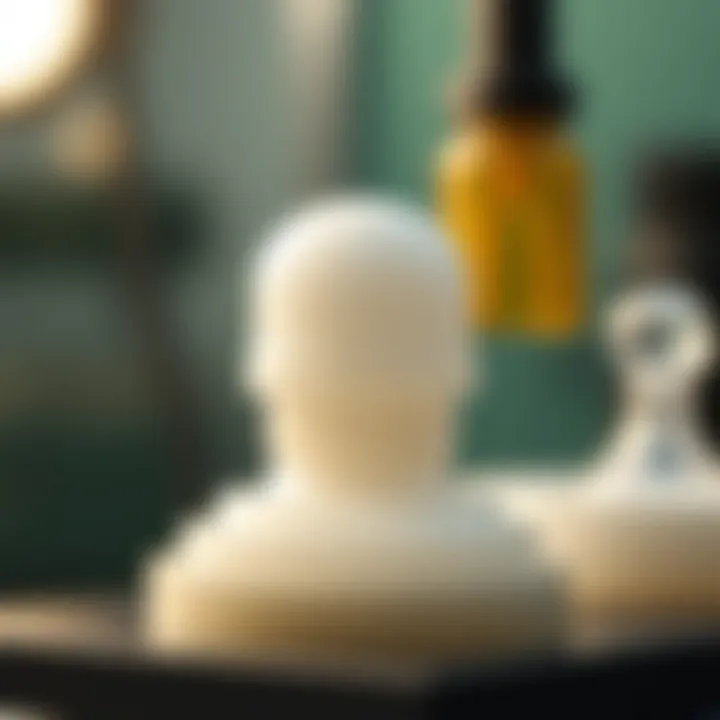
The production process of 3D printing wax molds is a cornerstone of the entire operation, influencing both the quality of the final product and the efficiency of the fabrication process. Understanding the nuances present in each step can help users navigate challenges and optimize their workflows. The production process involves three main phases: designing the mold, applying printing techniques, and post-processing the wax molds. Each of these phases plays a critical role in determining the success of the entire 3D printing endeavor.
Designing the Mold
Utilizing CAD Software
Utilizing CAD (Computer-Aided Design) software is a game changer in the design phase of 3D printing wax molds. This software allows designers to create highly detailed models, which can be transformed into accurate 3D representations. One key characteristic of CAD software is its ability to facilitate complex geometric designs. Designers appreciate that they can tweak and adjust any aspect of the mold at a moment's notice, catering to precise requirements of various industries, like jewelry and medical applications.
A unique feature of CAD software is the range of modifications that can be applied seamlessly throughout the design process. For example, one can simulate different configurations to check how a mold will hold up under casting conditions. The advantage of using CAD is that it provides a clear visualization of the end product, potentially saving time and resources in the production stage. However, it also requires a certain level of expertise that might not be accessible to everyone entering the field.
Considerations in Design for Printing
When it comes to design for printing, considerations become paramount. Effective mold designs should account for the properties of wax, from its melting point to how it reacts under pressure during the casting process. One key characteristic of this design consideration is ensuring a balanced wall thickness throughout the mold. Having consistent thickness minimizes warping and potential distortions in the final cast.
A notable unique feature in design for printing is the understanding of flow dynamics. The design has to allow for the smooth flow of molten materials into the mold, which means features like vents and gates should be strategical placed. This supports optimal filling of the mold and avoids air entrapment. Balancing all these considerations can be challenging, but doing so ultimately results in more successful castings and less waste.
Printing Techniques
Layering Strategies
Layering strategies are vital in the production process, as these dictate how the printing will take place. The ability to lay down wax in successive layers leads to the creation of complex shapes and designs that would be difficult to achieve through traditional mold-making methods. A key characteristic of layering strategies is that they allow for precision control over the resolution of the mold. Higher resolutions mean betterquality final products, even though they can result in longer print times.
One unique feature of layering strategies is their adaptability to various designs. If a model has intricate detailing, adopting a finer layering strategy may be necessary, whereas larger, more robust designs can be printed with thicker layers. The advantage here is the flexibility to choose how fine or coarse the print should be depends solely on the requirements of the mold rather than restricting the designer's vision.
Support Structures in Printing
Support structures in printing are another crucial topic and play a major role in achieving successful mold outcomes. These structures hold up parts of the mold that might otherwise sag or collapse during the printing process. A key characteristic of support structures is that they can be customized based on the specific needs of each individual print. This means flexibility and the ability to adapt to diverse designs.
One unique feature of support structures is their ability to minimize material waste while providing necessary reinforcement. Many modern printing software solutions offer options to adjust the density and shape of support material. While they do add extra steps during both the printing and post-processing phases, the advantage they bring in achieving high-quality molds often outweighs the disadvantages.
Post-Processing of Wax Molds
Removing Support Materials
Removing support materials is a practical yet crucial aspect of post-processing wax molds. The method chosen for this task directly impacts the quality of the final product. One key characteristic of support removal is that it must be done carefully to avoid damaging the mold itself. Depending on the type of supports used, this could range from simple breakaway supports to more complex methods which may involve solvents or heat.
A unique feature of this stage is the variety of techniques available for removal. Some practitioners might employ precision tools, while others might rely on thermal means to melt away material. The advantages of proper support removal not only come in the form of improvements in mold appearance but also in the precision and ease of the subsequent casting process.
Smoothing and Finishing Techniques
Smoothing and finishing techniques are essential in achieving the desired surface quality of 3D printed wax molds. One principle aspect here is that a well-finished mold ensures a more elegant final cast. Key characteristics of smoothing techniques include methods such as sanding, polishing, or even using chemical treatments to achieve a finer surface finish.
A unique feature in this area is that different molds may require different finishing techniques depending on their complexity and intended use. For instance, jewelry molds often need a finer polish compared to industrial molds. Balancing the time and resources spent on finishing against the end quality of the casting is something that should be carefully considered. The proper approach can enhance the mold's effectiveness and lead to more successful casting outcomes.
Challenges in 3D Printing Wax Molds
The journey into the realm of 3D printing wax molds does not come without its hurdles. Understanding the challenges is crucial for those looking to harness this technology, be it for jewelry creation, dental applications, or any other purpose. Each problem brings with it certain considerations that could shape the effectiveness and efficiency of using these molds. Recognizing these difficulties can guide practitioners in their practices and ignite conversations on potential solutions.
Material Limitations
Durability Concerns
Durability is a prime concern when dealing with wax materials in 3D printing. Wax is inherently softer and more fragile than traditional mold materials, making it prone to deformation under pressure. This characteristic poses a challenge during the casting process. When molds are subjected to heat or mechanical stress, they may not maintain their intended shape.
This limitation can lead to inaccuracies in the final product, making it less reliable for industries that require precision. However, the very softness of wax makes it excellent for creating intricate details that are often required in specialties like jewelry design. It’s a trade-off situation. The unique feature of wax's softness can be advantageous in some cases, yet detrimental in others when durability is paramount.
Thermal Properties of Wax
The thermal properties of wax are another area that warrants attention. Wax has a relatively low melting point, which might appeal to those who require ease in mold removal. Nevertheless, this low melting point can become a double-edged sword. The material can deform under heat exposure, which may cause problems during casting or when subjected to high-temperature environments.
The melting point varies slightly between different types of wax, which adds additional layers of complexity in selection. This property makes wax optimal for applications that do not necessitate high thermal resistance, yet its vulnerability needs to be accounted for in scenarios where temperature fluctuations are frequent. Thus, weighing these pros and cons determines how and where wax molds are applied effectively.
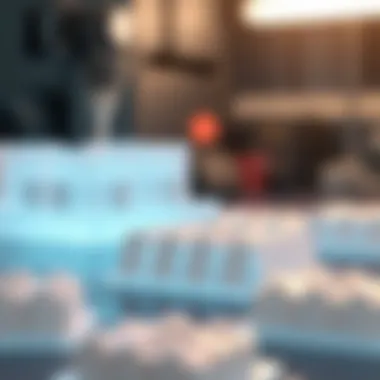
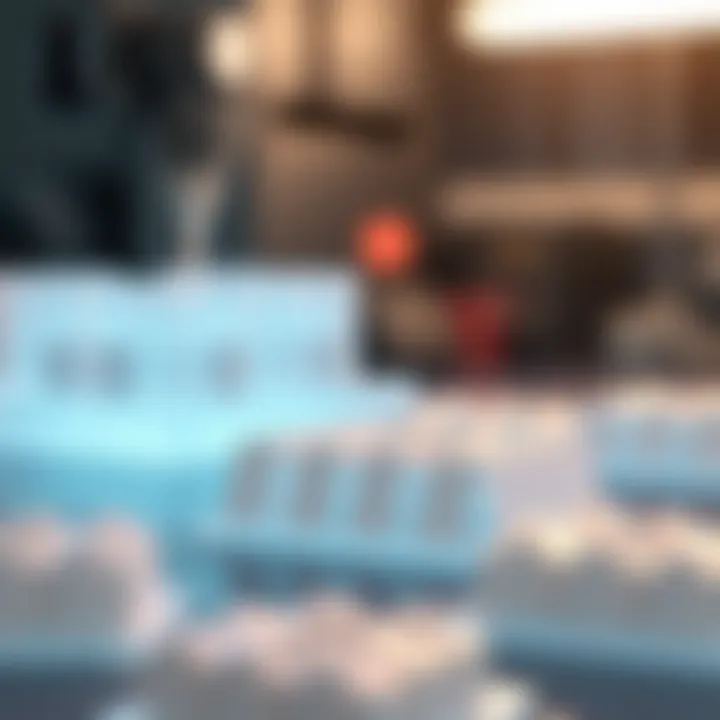
Cost and Accessibility
Cost-effectiveness is another big issue facing those interested in 3D printing wax molds. While 3D printing technology has become more accessible over time, the costs linked with high-quality wax and printing machines remain significant hurdles. This financial barrier can deter small businesses and independent artists, restricting opportunities. Factors like the quality of wax used, the printer’s capabilities, and ongoing maintenance expenses can add up quickly. The challenge here lies in balancing affordability with quality, which can be a tightrope walk.
Technical Expertise Requirements
Training and Skill Development
The complexity of 3D printing wax molds requires a decent level of technical expertise. Training and skill development are vital not just for operating the printers, but also for designing molds that are effective. Knowing CAD software is almost a prerequisite. However, the skills needed may not be readily available, creating a gap that can be frustrating for beginners.
Providing adequate training programs can help bridge this gap, but there may still be limitations in knowledge dissemination. Focused education can empower individuals to overcome technology barriers, but frustrations can arise from varying access to such programs. Technical skill isn’t just a nice-to-have; it’s a must for anyone wanting to excel in this field.
Industry Standards and Practices
Working in alignment with industry standards and practices is crucial in the realm of 3D printing wax molds. These standards dictate not only how products should be made and tested but also how to ensure safety in production. Adhering to industry norms helps maintain a level of consistency and quality which is paramount in applications like medical and dental fields.
Missing the mark on established practices can lead to faulty products and negative consequences that range from minimally problematic to catastrophic. Understanding these protocols is beneficial for maintaining high levels of quality and safety throughout the production process. Yet, the complexity of regulations and standards can be overwhelming, creating a steep learning curve for newcomers in the industry.
In summary, the challenges associated with 3D printing wax molds are multifaceted, revolving around material limitations, cost considerations, technical skills, and industry adherence. Recognizing and addressing these issues is paramount for anyone looking to navigate this intricate landscape.
Future Trends in 3D Printing Wax Molds
The field of 3D printing wax molds is rapidly evolving, with numerous trends shaping its future. It's crucial to understand how these developments will enhance traditional practices, making them not just relevant but a viable option across various industries. Staying ahead of these trends can unlock opportunities for innovation, efficiency, and sustainability.
Innovations in Wax Materials
As technology continues to march forward, the development of new wax materials is poised to make a permanent impact on the industry. Companies are now concocting materials that combine the inherent benefits of wax with enhanced durability and thermal stability. This makes them suitable for more demanding applications without sacrificing the quality of the final product. For example, hybrid wax formulations are being created to resist deformation during high temperatures, expanding their utility in both artistic and industrial processes.
Integration with Advanced Technologies
Artificial Intelligence in Design
Artificial Intelligence (AI) is not just a buzzword; it’s quickly becoming a cornerstone in the design landscape of 3D printing. The incorporation of AI in design aids artists and engineers alike in creating highly complex shapes that are often impractical through traditional methods. One of the key characteristics of AI in this context is its predictive capability. By analyzing user input and past designs, AI can provide suggestions for optimizing the shape or materials used in the mold. This not only saves time but also ensures more reliable results. However, some may argue that reliance on AI can diminish the creative aspect of mold design, as artists might find themselves following algorithm-generated ideas instead of relying on their instincts.
Automation in Production
Automation is changing the game when it comes to the production of wax molds. With automative systems in place, the speed of production can significantly increase. This is particularly advantageous for mass-production scenarios where consistency and quick turnaround times are essential. One critical aspect of automation is its potential to minimize human error, ensuring that every mold is top-notch. Yet, there are downsides too, such as the initial setup costs for automation technologies, which can be steep for smaller operations.
Sustainability Considerations
Biodegradable Wax Options
Environmental consciousness is becoming more important, even in industries that traditionally relied on materials with significant ecological footprints. The development of biodegradable wax options represents a stepping stone toward a more sustainable approach to mold making. These new materials break down naturally without leaving toxic residues, making them a strong contender for application across various industries. One appealing feature is the ability to create designs that are not only functional but also environmentally friendly, merging utility with ethical responsibility. Still, some may find that the performance of biodegradable wax doesn't always match that of traditional wax, leading to debates on quality versus sustainability.
Energy Efficiency in Printing
Lastly, energy consumption in the production process is always a hot topic. The future of 3D printing wax molds also hinges upon innovations aimed at improving energy efficiency. New technologies are being developed that can cut down power usage significantly—making the entire production process more economical and less taxing on the environment. A key characteristic here is the decrease in operational costs, allowing businesses to allocate resources elsewhere. However, while these technologies promise to be effective, the upfront investment might be a hurdle for some smaller firms looking to transition.
As the trend leans toward sustainability and efficiency, those who adapt to these innovations will likely find themselves at the forefront of the industry.
The End
The significance of 3D printing wax molds can't be overstated. As highlighted throughout our exploration, this technology is reshaping industries and practices previously restricted by traditional methods. The capability to produce intricate designs quickly and accurately has sparked innovations in jewelry, dentistry, and industrial prototyping, leading to more efficient workflows and reduced timeframes for product development.
Recap of Key Points
In summary, key points covered in this article include:
- Applications in Various Industries: From jewelry design to medical uses in dentistry, the applications of 3D printing wax molds are extensive and varied. Each sector benefits from improved precision and customization, allowing for tailored solutions to meet specific needs.
- Production Process: We detailed the steps necessary for creating wax molds through 3D printing, including design considerations, printing techniques, and the importance of post-processing. Each step plays a critical role in ensuring the quality and functionality of the final product.
- Challenges and Solutions: Challenges such as material limitations and the need for technical skills were discussed. Addressing these hurdles is vital for maximizing the technology's potential, leading to ongoing advances in training and material development.
- Future Trends: The potential for innovation in wax materials, automation in production, and sustainability efforts suggest a promising landscape for the future of 3D printing wax molds. Companies are increasingly looking to integrate advanced technologies, ensuring they remain at the cutting edge.
Final Thoughts on the Future of 3D Printing Wax Molds
Looking forward, it's clear that the future of 3D printing wax molds is bright but also laden with questions and opportunities. As material science evolves, we can expect to see more sustainable and versatile wax materials emerging, responding to the growing demand for eco-conscious manufacturing. Furthermore, the use of artificial intelligence for streamlining design processes will likely enhance efficiency and creativity.
"The ability to adapt and innovate will be the cornerstone of growth in the realm of 3D printing wax molds."
In closing, both established industries and emerging players must embrace these changes to fully harness the advantages that come with this technology. Continuous research, stakeholder collaboration, and education will pave the way for a future where 3D printing wax molds are not only standard practice but also a critical driver of innovation. This technology, once seen as niche, is now becoming a fundamental aspect of production across various fields, providing a competitive edge in a rapidly transforming market.