Advanced Techniques for PWM Control in AC Motors
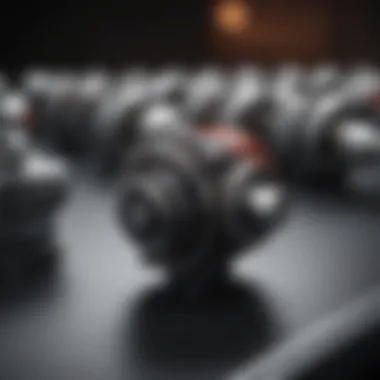
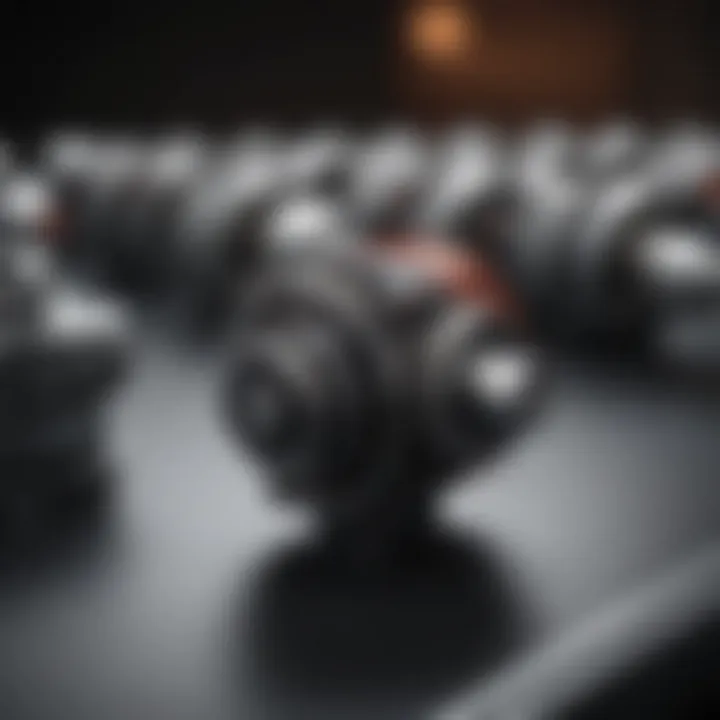
Research Context
Background Information
In an age where efficiency and precision in motor control are paramount, the dynamics of Pulse Width Modulation (PWM) technologies offer a fascinating guidelines for engineers and researchers alike. PWM is not just a technique; it's a leap in how we can control alternating current (AC) motors with unmatched accuracy. The history of PWM control techniques goes back several decades, but in recent years, innovations have made it a fundamental aspect of modern motor control systems. From household appliances to large industrial machines, PWM provides a responsive and energy-efficient means to regulate motor speed and torque.
As technology evolves, so does the complexity of AC motor control. Public discourse often highlights the structural aspects of PWM; however, it’s imperative to grasp the intricate relationship between PWM parameters—such as duty cycle, frequency, and waveform shape—and the operational efficiency of AC motors. Understanding these elements serves a dual purpose: enhancing the understanding of existing systems and laying a groundwork for future advancements.
Importance of the Study
The significance of studying advanced PWM techniques for AC motor control extends beyond academic interest. Industries are under growing pressure to reduce energy consumption while maximizing output. PWM demonstrates a clear advantage in this respect, allowing motors to run at optimal efficiency across various loads and speeds.
Examining these advanced techniques provides valuable insights into:
- Energy Efficiency: How PWM reduces power consumption in industrial applications.
- Performance Impact: Connection between advanced PWM strategies and motor responsiveness.
- Adaptability: Flexibility in motor applications, allowing for widespread use across different industries.
PWM not only plays a crucial role in enhancing operational efficiency; it also enables integration with modern technologies like IoT (Internet of Things) for smarter control systems. With such expansive applications, a nuanced understanding of PWM is vital for professionals aiming to stay ahead in a competitive marketplace.
Discussion
Interpretation of Results
Advanced PWM methods like Space Vector PWM and Sinusoidal PWM are reshaping the landscape of motor control. Each method carries its own implications for performance, thus it’s essential to parse out how these variables interact. For instance, Space Vector PWM is known for its ability to generate higher output voltage, leading to improved drive performance and decreased harmonics.
This section of the study seeks to elucidate how the choice of PWM technique impacts speed control, thermal performance, and energy savings. Engineers have observed that as these methods mature, they frequently yield diminishing returns when coupled with sub-optimal motor designs. The adaptation of PWM must be synchronized with motor specifications and intended application to achieve optimal results, ensuring motors do not just run, but run efficiently.
Comparison with Previous Research
Prior studies have largely focused on simple PWM methodologies and their basic implementation in motor control. While foundational, these insights can sometimes lack the granularity needed for real-world applications.
In contrast to earlier works, recent research has begun to highlight:
- Hybrid PWM Techniques: Combining multiple techniques for enhanced control and performance.
- Advanced Modulation Schemes: The emergence of more complex algorithms that adaptively learn from the motor's performance metrics.
- Control Algorithms: New algorithms that evaluate the load and adjust PWM signals accordingly, paving the way for more intelligent motor systems.
"As the industry shifts towards a more digital landscape, understanding the complexities of PWM could mean the difference between stagnation and innovation."
By integrating these advanced techniques into AC motor systems, researchers can push the boundaries of efficiency and performance far beyond what traditional studies suggested. This not only informs current motor control practices but also sets a trajectory for future engineering advancements.
By emphasizing these shifts, this study aims to serve as both a resource and a catalyst for further discourse and exploration in the field of PWM in AC motor control.
Preamble to PWM AC Motor Control
In the realm of electrical engineering, the ability to effectively manage AC motors is paramount. These motors are woven into the fabric of many industries, from manufacturing to automotive. However, controlling them with precision requires understanding advanced techniques, particularly Pulse Width Modulation (PWM). PWM acts not just as a tool for control, but as a vital technique that enhances performance, efficiency, and adaptability of these motors.
Definition and Relevance of PWM
Pulse Width Modulation is a method used to encode information in a pulsing signal. This technique varies the width of the pulses to regulate the amount of power delivered to a device, in this case, AC motors. It's highly relevant in today’s technology landscape, where energy efficiency and precision are increasingly crucial.
PWM essentially transforms a constant voltage into a variable one by switching the signal at different frequencies and pulse widths. This allows for smoother operations and reduced energy consumption.
The application of PWM in motor control is characterized by its flexibility. Engineers can precisely control speed, torque, and direction of the motor, thereby maximizing its overall efficiency. The rise of renewable energy sources, such as wind and solar, further amplifies the necessity for PWM as it helps integrate these variable sources more effectively into existing infrastructures.
Benefits of PWM in AC Motor Applications
Adopting PWM in AC motors offers numerous benefits:
- Improved energy efficiency: The ability to fine-tune the power delivered reduces waste, leading to significant energy savings, which benefits both the environment and operating costs.
- Enhanced control: PWM provides precise control over motor parameters, allowing for smoother operation and better responsiveness to operational demands.
- Flexibility in design: PWM techniques can be tailored to suit various motor types and applications, providing versatility that is often required in industrial settings.
- Reduction in heat generation: By modulating the power supply, PWM reduces thermal stress on the motor, prolonging its lifespan and improving reliability.
- Capability to integrate advanced control strategies: Incorporating PWM enables the use of sophisticated techniques like vector control or adaptive control, which can optimize performance dynamically based on real-time conditions.
Fundamentals of AC Motors
Understanding the fundamentals of AC motors is vital for anyone diving into Pulse Width Modulation (PWM) control techniques. These motors are the backbone of numerous industrial and commercial applications, from conveyor belts to HVAC systems. When engineers grasp the basic principles governing AC motors, they can better appreciate how PWM influences their efficiency and performance. This section will unpack the different types of AC motors and elucidate the principles underpinning their operation.
Types of AC Motors
Induction Motors
Induction motors are perhaps the most ubiquitous type of AC motor, often praised for their simplicity and rugged design. One noteworthy characteristic is their self-starting ability, which eliminates the need for external starting mechanisms. This makes them a popular choice for many industrial applications, as they can handle high loads with minimal maintenance.
A unique feature of induction motors is their efficiency when coupled with PWM techniques, which enhance control over speed and torque without compromising performance. However, they do have drawbacks, such as reduced efficiency under certain load conditions and a dependency on slip for operation. Overall, induction motors align well with the goals of PWM strategies, making them a staple in the industry.
Synchronous Motors
Synchronous motors present a stark contrast to induction motors in terms of operation. They are governed by the idea that the rotor turns in synchrony with the stator's magnetic field, achieving a constant speed regardless of load variations. A key characteristic of synchronous motors is their ability to operate at power factor correction, which improves energy consumption efficiency.
Their unique feature lies in their capability to run at leading, lagging, or unity power factors. While this can lead to significant energy savings and reduced electricity bills, synchronous motors can be more complex and expensive, requiring precise control mechanisms. For PWM applications, their ability to maintain a steady speed even under varying loads can be highly valuable.
Universal Motors
Universal motors are intriguing in their versatility, as they can run on either AC or DC power. Their high starting torque makes them particularly advantageous for applications that require quick acceleration, like power tools and household appliances. This flexibility contributes to their appeal in PWM system designs that involve variable speed applications.
Despite their benefits, the unique feature of universal motors comes at a price; they tend to be less efficient than their induction and synchronous counterparts. They also generate more noise and can wear out faster due to their brush design. In the context of PWM techniques, while they may offer rapid response times, engineers need to weigh these factors against performance longevity and energy consumption.
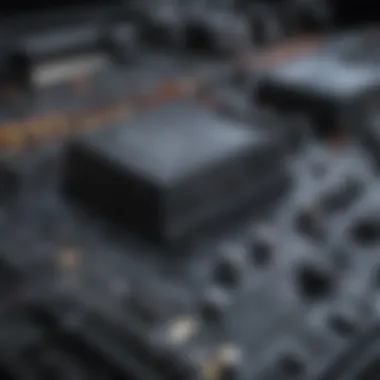
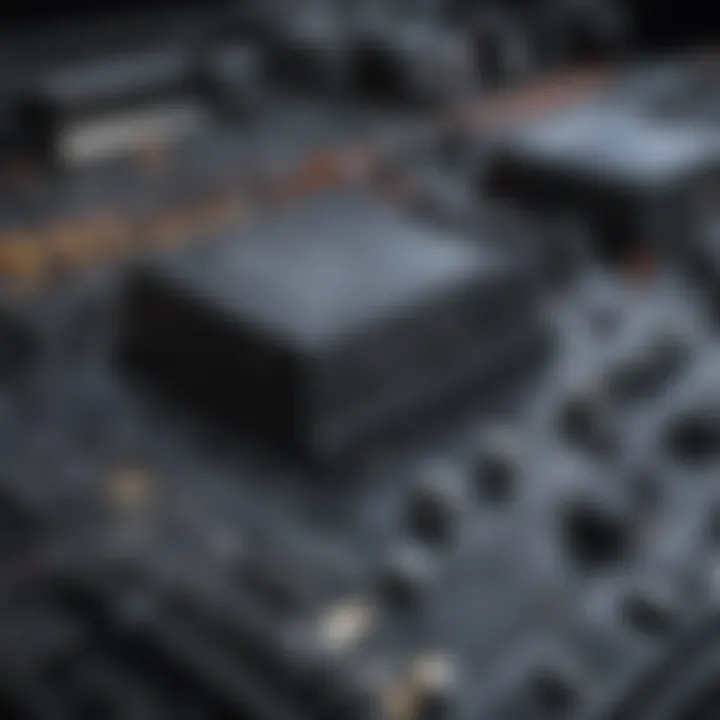
Basic Operation Principles
The basic operation principles of AC motors revolve around the interaction of magnetic fields and electrical currents. In its essence, an alternating current establishes a rotating magnetic field that interacts with the rotor, giving rise to motion. There are two fundamental aspects to highlight:
- Electromagnetic Induction - The principle that underlies induction motors. When an electric current flows through the stator, it generates a magnetic field that induces current in the rotor, causing it to turn. This is the foundation of how most AC motors operate.
- Synchronous Operation - For synchronous motors, the magnetic field rotates at the same rate as the rotor, which is crucial for maintaining a constant speed. The design of the rotor—involving permanent magnets or electromagnets—enables this unique behavior.
Understanding these principles is critical for advancing in PWM control strategies, as it sets the stage for further exploration in modulation techniques and their implications on motor functionality.
Pulses and Modulation Techniques
Understanding the nuances of pulses and modulation techniques is essential for optimizing PWM control in AC motors. This section addresses the significance of these elements in enhancing motor performance, efficiency, and adaptability. The modulation strategies serve not just to control the motor speed and torque, but also play a vital role in reducing energy consumption and improving the overall operational lifespan of the systems involved.
Understanding Pulse Width Modulation
Pulse Width Modulation (PWM) is fundamentally about controlling the average power delivered to an electrical load, in this case, AC motors. The core idea revolves around varying the width of the pulses in the signal without changing its frequency. Each pulse's width directly influences how much power the motor receives, allowing precise control over speed and torque.
PWM is crucial for several reasons:
- Efficiency: By modulating the power supply effectively, PWM minimizes energy loss, turning excess energy which would cause heating into useful work instead.
- Motor Longevity: This meticulous control helps reduce wear and tear on motor components, extending their operational life.
- Versatility: PWM can adapt to different types of AC motors, making it a versatile choice in various applications including industrial automation and HVAC systems.
Moreover, incorporating PWM allows for smoother control of motor speeds. Unlike traditional methods that might produce jerky movements, PWM provides seamless transitions, contributing positively to process reliability.
Sinusoidal PWM vs. Space Vector PWM
When discussing modulation techniques, two prominent methods emerge: Sinusoidal PWM and Space Vector PWM. Both have distinct characteristics and advantages, making them suitable for specific applications.
Sinusoidal PWM
Sinusoidal PWM uses a sinusoidal signal to generate the fundamental frequency. The modulation is achieved by comparing the reference sine wave with a high-frequency triangular or sawtooth wave. The result is a continuous modulation that creates smoother output voltage waveforms, which ultimately leads to reduced harmonics that could otherwise interfere with motor operation.
Here are some key points about Sinusoidal PWM:
- Produces lower harmonic distortion, enhancing motor performance.
- Commonly used in low-power applications due to its relative simplicity.
- Enables efficient control over various load conditions.
Space Vector PWM
Space Vector PWM takes a more geometric approach. It treats the multilevel action of the inverter as a vector, effectively allowing it to utilize the entire DC bus voltage more efficiently. This strategy helps in maximizing the output voltage applied to the AC motor while maintaining a low harmonic distortion.
The characteristics of Space Vector PWM include:
- Higher efficiency compared to traditional methods, especially in high-power applications.
- Improved voltage utilization which is particularly beneficial for large motors driving high loads.
- Greater complexity in implementation, requiring advanced control strategies and algorithms.
"Every modulation technique has its place, and understanding their intricacies allows engineers to choose the right tool for the right job."
Control Methods Overview
The realm of PWM AC motor control has multiple dimensions, among which control methods stand as crucial pillars. Understanding these control techniques helps engineers and researchers pinpoint the most suitable approach for a specific application. Control methods not only govern the performance of the motor but also enhance efficiency and reliability across various operational settings. By carefully selecting a control method, professionals can tailor the motor's functionality to meet precise performance standards while minimizing energy consumption.
With a host of considerations at play, delving deeper into scalar and vector control techniques reveals their respective strengths and nuances. These methods play a significant role in maximizing output, preventing unnecessary wear and tear on components, and facilitating ingenuity in motion control. The remaining sections will dissect scalar and vector techniques, emphasizing their application and relevance in the context of PWM AC motor control.
Scalar Control Techniques
Scalar control techniques are often regarded as the foundational methods in controlling AC motors, particularly in applications where simplicity and cost-effectiveness are paramount. This approach primarily manipulates the voltage and frequency supplied to the motor, enabling control over speed and torque.
Key features of scalar control include the following:
- Speed Control: By adjusting the frequency of the power supply, one can control the speed of the motor efficiently.
- Ease of Implementation: Scalar methods require fewer sophisticated components, making them straightforward and affordable for many industrial settings.
- Robustness: This technique shows a reliable performance across a vast range of operating conditions, often outshining more complicated methods in basic applications.
However, it's worthwhile to note that scalar control has its drawbacks. One of the primary limitations lies in its inability to deliver precise torque control, which can limit its effectiveness in applications demanding high dynamics or quick responses.
Vector Control Techniques
In contrast to scalar control, vector control techniques offer a more advanced approach, enabling better performance characteristics, particularly in high-performance applications. The essence of vector control is to decouple the torque and flux components of the motor, allowing independent control.
Several aspects of vector control include:
- Dynamic Performance: Vector control allows for superior acceleration and deceleration responses, making it suitable for applications requiring rapid transitions.
- Torque Control: By separating the control of torque from speed, vector control achieves seamless responses under varying loads, ideal for machinery with fluctuating demands.
- Efficiency Optimization: Often, motors under vector control operate closer to their optimal efficiency, leading to reduced energy consumption.
While vector control presents significant advantages, its complexity can pose challenges. The need for advanced sensors and algorithms can escalate costs and require skilled personnel for effective implementation.
In summary, both scalar and vector control techniques bear distinctive advantages and limitations. Scalar control may present a viable solution for less demanding applications, whereas vector control serves as the go-to option for high-performance needs. As the field of PWM AC motor control evolves, understanding and mastering these methods will be paramount for professionals and researchers alike.
PWM Implementation Strategies
In the realm of AC motor control, PWM Implementation Strategies stand as a cornerstone for achieving precision and efficiency. Various techniques can significantly influence how AC motors operate under different conditions. Understanding these strategies allows engineers to tailor solutions that meet specific performance criteria while maximizing energy use. This section touches upon the hardware and software aspects necessary for effective PWM implementation, delving into considerations that ensure optimal motor functionality, stability, and adaptability for various industrial applications.
Hardware Considerations
When it comes to hardware considerations, the architecture and components used in PWM systems can not be overstated. The choice of microcontrollers, power electronics, and sensors directly impacts the efficiency and responsiveness of the control system. Here are a few key elements to keep in mind:
- Microcontroller Selection: The microcontroller's capabilities define how well it will handle PWM signals. Look for units that can generate high-resolution PWM outputs and support multiple output channels.
- Power Conversion Components: Elements like MOSFETs, IGBTs, and diodes must be chosen based on switching frequency and load conditions. A reliable power inverter is crucial for correctly translating PWM signals into usable AC outputs.
- Feedback Mechanisms: Effective PWM control relies on real-time feedback from sensors. Pressure sensors, temperature sensors, and encoders provide vital data that impacts the control algorithms.
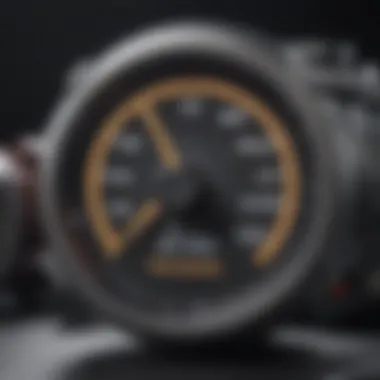
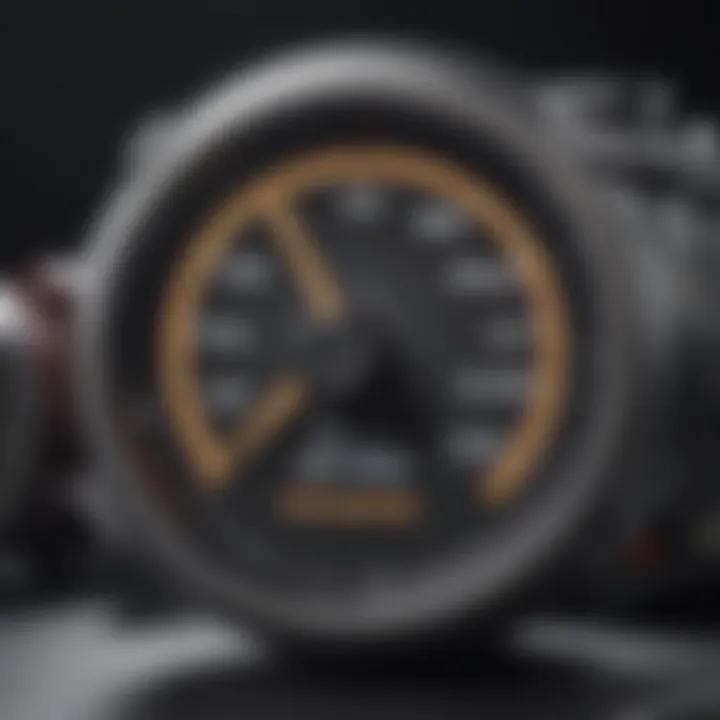
"A proper understanding of hardware capabilities can unlock potential improvements in system performance that may seem unattainable at first glance."
Furthermore, thermal management cannot be brushed under the carpet. Power devices can run hot under high loads, and ensuring adequate cooling solutions helps to sustain component longevity.
Software Control Algorithms
On the software side, the algorithms dictate how PWM signals are modulated and controlled. Several control methods can be implemented, ranging from traditional PID controllers to more sophisticated AI-based algorithms. Here’s what should be considered:
- Control Algorithms: Algorithms that can adapt to varying conditions in real time tend to perform better. Adaptive control strategies allow for changes in load or supply, ensuring the motor delivers consistent performance.
- Simulation and Modeling Tools: Software such as MATLAB/Simulink can aid in visualizing PWM strategies, allowing for exhaustive testing and refinement before hardware deployment. It’s like rehearsing a play before the opening night.
- Integration with IoT: Incorporating real-time data via the Internet of Things (IoT) can enhance decision-making processes, leading to predictive maintenance and improved operational efficiency. The connection between software and hardware should be seamless and intuitive.
As we put these strategies into practice, one must also consider the implications of specific configurations on system stability and responsiveness. Choosing an optimal control algorithm can mitigate issues like overshooting or oscillations, which could lead to premature equipment failure.
In summary, PWM Implementation Strategies encompass both hardware and software insights crucial in enhancing AC motor control's performance and efficiency. Whether it's selecting the appropriate microcontroller or utilizing cutting-edge software algorithms, the choices made during this phase are pivotal in defining the overall effectiveness of PWM systems.
Simulation and Modeling Techniques
Simulation and modeling in PWM AC motor control are crucial for several reasons. First off, they allow engineers to visualize complex systems and their behaviors before any physical prototypes are built. It saves both time and resources, ensuring that potential issues can be addressed in the early stages of development. Furthermore, modeling helps in analyzing the performance of different PWM strategies under varying conditions, which is essential for optimization.
Utilizing simulation tools can also provide insights into how changes in parameters influence the motor's performance, thus facilitating more informed design choices. These simulations can predict outcomes that would be difficult to ascertain through experimental setups. Overall, this section will explore two vital aspects of simulation: the utilization of MATLAB/Simulink for PWM analysis and the importance of real-time simulation approaches in refining control strategies.
Using MATLAB/Simulink for PWM Analysis
MATLAB and Simulink have become go-to tools for engineers needing to simulate PWM control in AC motors. The simplicity and flexibility of Simulink allow for the rapid prototyping of complex control systems. Users can drag and drop blocks to create the system’s model visually, making it straightforward even for those not deeply familiar with coding.
One of the standout features is the rich library of pre-built blocks specifically designed for PWM techniques. This includes modules for defining various PWM schemes like Sinusoidal PWM or Space Vector PWM. Moreover, the tool can easily illustrate the effects of changes, enabling modifications to be made on-the-fly. Engineers can run simulations to visualize waveform generation, observe transient responses, and analyze frequency components, providing a comprehensive view of system behavior.
"Simulation provides a sandbox where ideas can be tested rigorously without the cost of physical hardware."
Another significant advantage of using MATLAB/Simulink is the ability to seamlessly integrate hardware-in-the-loop testing. This means you can connect actual motors and controllers to the simulation environment to test how the real-world system reacts under the designed PWM control. It narrows down the gap between simulation and real-world performance, making it easier to fine-tune and validate models before full-scale implementations.
Real-Time Simulation Approaches
Real-time simulation is yet another critical aspect of PWM control for AC motors. Unlike traditional simulation, which allows for non-time critical computations, real-time simulation requires computations to occur within a strict timeframe. This necessity ensures that control algorithms function effectively and reliably.
Implementing real-time simulations can use various platforms and tools like dSPACE or National Instruments, giving engineers a chance to instantly assess how changes in parameters affect motor performance.
Benefits of real-time simulation include:
- Enhanced Validation: Engineers can test their control strategies against real-world conditions to validate performance before deployment.
- Immediate Feedback: Real-time data is invaluable. Adjustments to control algorithms can be made during the simulation, yielding immediate results and insights.
- Reduced Development Cycle: By catching issues early in the design phase, engineers can significantly decrease the time spent on debugging during later stages of the project.
Real-time simulations also foster collaboration among teams, as the instant feedback loop encourages immediate discussions and brainstorming on strategy adjustments. Overall, implementing these approaches can lead to more robust motor control solutions that are well adapted to fulfill the demands of modern applications.
Challenges and Limitations
In the realm of PWM AC motor control, understanding the challenges and limitations is paramount. Just as a coin has two sides, the benefits of Pulse Width Modulation come paired with certain obstacles that engineers and researchers must navigate. These challenges not only affect the performance of the motors but also influence the overall effectiveness of the control systems.
Addressing these difficulties equips practitioners with the know-how to optimize performance, ensuring that PWM techniques can continue to evolve. Identifying the specific limitations can lead to innovative solutions, pushing the boundaries of what's achievable in motor control applications.
Harmonics in PWM Control
Harmonics arise as unintended frequency components within PWM signals. They can distort the current and voltage waveform, leading to a myriad of potential problems, such as overheating, increased losses in magnetic components, and noise pollution in electrical systems. The introduction of harmonics into AC motor control is like throwing a wrench in the works – it interrupts smooth operation.
When harmonic content increases, it can lead to several detrimental effects:
- Inefficiency: Motors often experience reduced efficiency due to strain caused by harmonic distortion.
- Overheating: Excessive harmonic content can heat the windings more than usual, possibly leading to insulation failure.
- Decreased lifespan: Prolonged exposure to harmonics may result in equipment failure, reducing the expected operational lifespan of the motor.
Addressing harmonics involves strategies like using filters, redesigning winding layouts, or employing advanced modulation schemes that aim to minimize their impact. Techniques such as active filters have become essential tools in mitigating the effects of harmonics and improving overall system performance, allowing for more reliable PWM control in AC motors.
Thermal Effects on Motor Performance
The thermal behavior of motors under PWM control is another crucial factor. As a motor operates, especially under varying loads and duty cycles, it generates heat. The stability and efficiency of PWM control can be severely affected by the motor's thermal status.
Heat affects performance in several ways:
- Thermal Runaway: If not managed properly, a rise in temperature can cause rotor or stator winding insulation to degrade, leading to performance loss or failure.
- Control Accuracy: Thermal expansion can change mechanical tolerances, influencing the precision of feedback systems that rely on consistent physical relationships.
- Speed Regulation: Increased temperatures may lead to reduced torque generation, affecting the control over speed, and complicating the operation further.
To counteract thermal effects, engineers might incorporate thermal management systems that utilize heat sinks, cooling fans, or even liquid cooling systems in extreme cases. Additionally, smart thermal sensors can provide real-time data to control algorithms, allowing for adaptive responses based on temperature variations.
"Engaging with PWM technology is not just about controlling power; it involves a nuanced understanding of the underlying challenges that can arise in operations."
Thus, grappling with the complexities of harmonics and thermal effects in PWM systems helps users appreciate the delicate balance required to optimize AC motor performance. Recognizing these limitations allows for enhanced approaches in various applications, ensuring that the continued advance of PWM technology not only addresses current hurdles but also prepares the path for future innovations.
Advanced PWM Techniques
In the realm of AC motor control, advanced PWM techniques have become not just an add-on but a necessity. Working with pulse-width modulation allows for innovative approaches that directly impact the functionality and efficiency of motors. These techniques enable finer control over speed and torque, significantly enhancing the adaptability of motors in diverse applications. By leveraging such capabilities, engineers can tailor solutions to meet specific demands without compromising performance.
Adaptive PWM Strategies
Within the landscape of PWM control, adaptive strategies stand out as a dynamic solution. Adaptive PWM strategies adjust the modulation parameters in real-time based on feedback from the motor's performance. This adaptability is crucial in applications where load conditions fluctuate, providing a significant advantage over traditional methods that maintain a static approach.
One of the critical benefits of adopting adaptive PWM strategies is the improved efficiency, especially under varying loads. By continuously monitoring the motor's operational state and optimizing the pulse width accordingly, energy losses can be minimized. The intricacies of these methods involve sophisticated algorithms and real-time data processing, ensuring that the control remains responsive to changes.
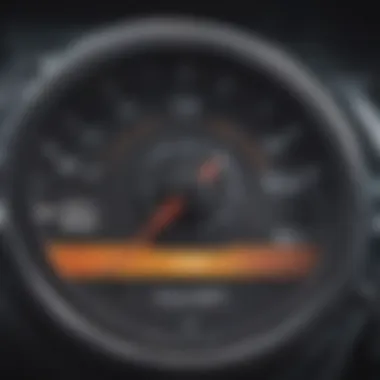

For example, consider a conveyor system with variable load due to different products being transported. An adaptive PWM strategy can automatically adjust the power supplied to the motor, maintaining optimal speed without overshoot or power wastage. This level of control not only enhances system efficiency but also prolongs the life of the motor by reducing thermal stress.
Additionally, the implementation of adaptive strategies often involves the integration of sensors and controllers. These components work synergistically to create an intelligent control loop that enhances the robustness of the overall system.
"Efficient control is about not just the basics but how to maximize each component's performance under varying conditions."
Predictive Control in PWM Systems
Predictive control emerges as a forward-thinking approach in the PWM toolkit. This technique revolves around using mathematical models that forecast the future behavior of the controlled system. In a PWM environment, this means anticipating the needs of the AC motor before they arise, allowing for preemptive adjustments to the modulated signal.
One of the most significant advantages of predictive control is its ability to enhance stability and reduce system oscillations. Unlike traditional control methods that react to changes, predictive control formulates a strategy based on expected trends. For instance, if a motor is known to experience increased load during peak hours, predictive algorithms can adjust the PWM signals preemptively, allocating the necessary resources in advance.
Moreover, these algorithms can learn from past performance data, refining their accuracy over time. This data-driven approach creates a self-improving system that benefits from historical insights, optimizing operational efficiency. It’s akin to having a wise mentor—experience teaches what works and what doesn’t.
In terms of implementation, predictive control integrates seamlessly with existing PWM frameworks. It requires a solid understanding of system dynamics and the factors influencing motor performance. Engineers looking to utilize predictive control must be prepared to invest time in model development and testing to ensure reliability.
Applications of PWM AC Motor Control
The use of Pulse Width Modulation (PWM) in AC motor control is becoming increasingly pivotal in a variety of sectors. From enhancing operational efficiency to improving control precision, PWM techniques present numerous advantages that are valuable across multiple applications. In this section, we'll explore how PWM helps in industrial automation and HVAC systems, underscoring its role in fostering adaptation and optimizing performance.
Industrial Automation
In the realm of industrial automation, PWM AC motor control plays a crucial role. Factories rely heavily on precise motor control to ensure streamlined production processes and minimize waste. The ability to adjust the output voltage and frequency through PWM allows for significant flexibility in how motors respond to varying operational demands. For example, in robotic assembly lines, motors can run at different speeds based on task requirements, leading to energy savings.
Key Benefits in Industrial Automation:
- Energy Efficiency: PWM reduces energy consumption by providing only the necessary power to motors at any given time. This often translates to lower operational costs.
- Improved Control: Enhanced control contributes to better product quality, particularly in processes that rely on consistent speed and position accuracy.
- Longevity of Equipment: Gradual power adjustments reduce wear and tear on mechanical components, prolonging the service life of motors.
Moreover, the diverse range of applications within industrial automation—from conveyor belts to packaging machinery—necessitates versatile control systems. Implementing advanced PWM techniques allows manufacturers to optimize motor operation and maintain high levels of productivity.
"Utilizing PWM in industrial automation results not only in substantial cost savings but also in improved process reliability."
HVAC Systems
Another significant application of PWM AC motor control can be seen in Heating, Ventilation, and Air Conditioning (HVAC) systems. In these systems, motors are needed to power fans, pumps, and compressors, all of which benefit from efficient motor control. PWM enables HVAC systems to adjust airflow, heating, or cooling output according to real-time demands, which is particularly valuable in dynamic environments where conditions frequently change.
Advantages in HVAC Applications:
- Reduced Energy Consumption: With PWM providing the ability to fine-tune motor speed and torque, HVAC systems consume only as much energy as needed.
- Enhanced Comfort: Variable speed operations translate to a more consistent temperature and humidity level within the controlled environments.
- Noise Reduction: PWM allows motors to operate at lower speeds when full capacity is not required, reducing noise levels and improving the overall comfort of spaces.
These benefits illustrate why PWM is increasingly being integrated into modern HVAC technologies. As energy efficiency regulations become more stringent, utilizing advanced PWM techniques in these systems is likely to remain a top priority for designers and engineers.
Future Trends in AC Motor Control
The landscape of AC motor control is undergoing significant shifts owing to technological advances and economic pressures. This section tackles the progressive trends reshaping the industry, focusing particularly on the pivotal integration with renewable energy sources and the emergence of smart motors. Having a grip on these trends not only empowers professionals with cutting-edge knowledge but also enables them to implement solutions that truly make a difference. A forward-looking perspective helps ensure that businesses remain competitive and that innovation in motor control systems continues to thrive.
Integration with Renewable Energy Sources
The merging of AC motor control techniques with renewable energy frameworks has never been more crucial. With environmental considerations at the forefront, integrating renewable energy sources like solar and wind is becoming a standard practice. This integration helps stabilize energy supply, mainly because these energy sources can be erratic. Coupling PWM techniques can enhance this stability by allowing AC motors to adapt based on energy availability.
Benefits of integration include:
- Efficiency: AC motors can adjust their performance based on the energy input, maximizing efficiency.
- Resilience: Systems can maintain functionality despite fluctuations in power supply.
- Cost-Effectiveness: Utilizing free sources of energy reduces operational costs.
Emerging technologies such as energy storage systems will support this integration, allowing excess energy to be stored for later use. The adaptability of PWM control methods plays a critical role here, facilitating these interactions while maintaining motor performance.
"The future belongs to those who prepare for it today." – Malcolm X
The Rise of Smart Motors
Smart motors represent another fascinating avenue in the evolution of AC motor control techniques. These motors incorporate advanced sensors, microcontrollers, and communication systems to gather and analyze performance data. The result is an unprecedented level of control and fine-tuning that allows for maximum efficiency and lifespan.
Key highlights of smart motors include:
- Real-Time Monitoring: Continuous data collection enables timely analysis of performance metrics, ensuring motors operate under optimal conditions.
- Predictive Maintenance: Through data analytics, predictive maintenance reduces downtime by notifying technicians of potential failures before they occur.
- Flexible Communication: Smart motors can communicate with other systems, ensuring synergy within larger networked environments.
The adoption of Industry 4.0 principles is accelerating the implementation of smart motor technology. When combined with advanced PWM techniques, these motors can achieve a new level of performance. The synergy not only enhances operational efficiency but also aligns with ongoing efforts towards sustainability.
Epilogue
As we close the loop on our exploration of PWM AC motor control, it’s clear that this field represents a convergence of innovation and practicality. Understanding advanced PWM techniques provides a roadmap to enhancing motor performance across varied applications. Engineers and researchers, whether fresh to the field or seasoned veterans, benefit immensely from grasping the nuances involved in these methodologies. Collaboratively, they address not just efficiency but adaptability in a marketplace that increasingly demands responsive and intelligent systems.
Summary of Key Insights
The sine qua non of PWM in AC motor control encompasses multiple insights:
- Efficiency and Performance: PWM controls enable motors to operate at higher efficiency levels by optimizing the input voltage and current. This ultimately leads to reduced energy consumption and operational costs for industries that rely heavily on consistent motor performance.
- Flexibility in Applications: Whether it’s in robotics, HVAC systems, or industrial machinery, the versatile implementation of PWM techniques allows for customization to specific needs, fostering innovation.
- Real-Time Variability: With the advent of adaptive PWM strategies, motors can adjust their output dynamically in response to load changes, a significant leap from traditional methods that lacked this level of responsiveness.
"Adopting advanced PWM control methods not only enhances motor operation but also contributes to sustainable industrial practices."
Implications for Future Research
The future of PWM AC motor control is ripe for research and development. Here are several avenues worth pursuing:
- Integration with IoT Technologies: As the Internet of Things continues to proliferate, exploring how PWM can interact with smart devices might unveil efficiencies that traditional systems lack.
- Enhanced Algorithms for Predictive Control: Developing more precise algorithms could further enhance predictive capabilities, allowing motors to behave optimally even in varying environmental conditions or application demands.
- Investigation into Alternative Materials: Research into materials that reduce thermal effects or enhance harmonic performance could yield breakthroughs in motor longevity and efficiency.
- Combining Renewable Inputs: Examining how PWM can integrate smoothly with renewable energy sources could pave the way toward greener, more sustainable industrial practices.
In summary, the journey into advanced PWM control for AC motors is only just beginning, and maintaining momentum in research is paramount. Bridging theory and implementation will undoubtedly lead to innovative solutions that reshape the industry, making it more intelligent and efficient.